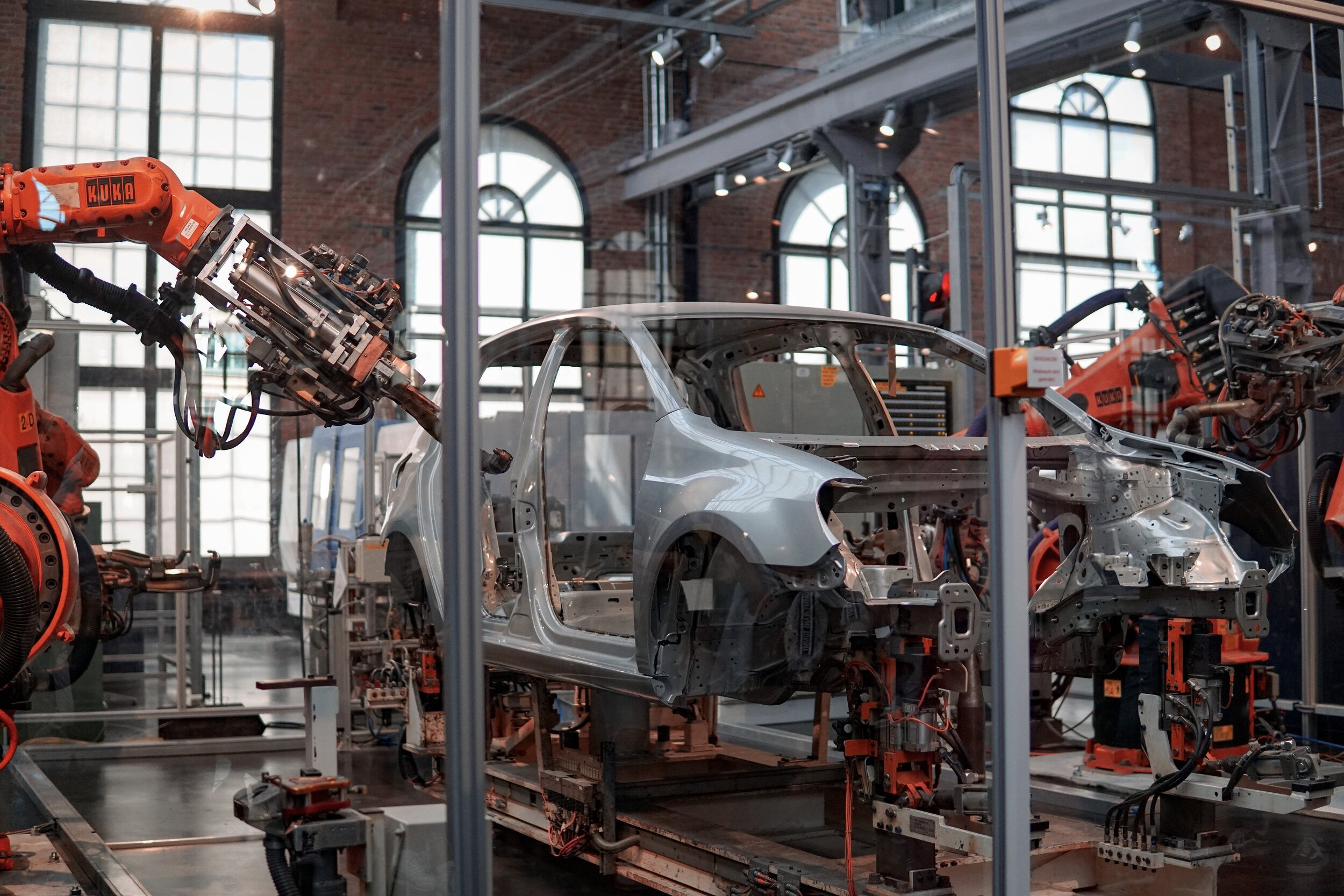
LANGUAGE OF LEAN
Order and Cleanliness
Order and cleanliness are two critical components of a successful and efficient work environment.
Order and cleanliness are two critical components of a successful and efficient work environment. By creating an organized and tidy workspace, employees are able to work more effectively, reduce waste, and increase productivity. One proven method for achieving order and cleanliness is through the use of the 5S Method.
The 5S Method is a system that originated in Japan and focuses on five key principles: Sort, Simplify, Sweep, Standardize, and Sustain. By following these five principles, organizations are able to create a work environment that is efficient, safe, and conducive to high performance.
The first step of the 5S Method is "Sort." This principle involves eliminating items that are no longer necessary or used. This could include outdated equipment, supplies that have been discontinued, or items that have simply outlived their usefulness. By sorting through items and getting rid of what is not needed, organizations are able to free up valuable space and resources.
The second principle of the 5S Method is "Simplify." This step involves organizing the items that remain after the sorting process and finding ways to make the workplace more efficient. This could mean moving items to more accessible locations, labeling items clearly, or rearranging the workspace to make it more user-friendly.
The third step is "Sweep." This principle involves cleaning the workspace and ensuring that it is free of debris and clutter. This not only helps to create a cleaner and more inviting work environment, but it also helps to prevent accidents and injuries.
The fourth step of the 5S Method is "Standardize." This principle involves establishing procedures and processes that ensure the workplace remains organized and clean. This could include regular cleaning schedules, procedures for storing items, and guidelines for maintaining a tidy workspace. By establishing these standards, organizations are able to ensure that the benefits of the 5S Method are sustained over time.
The final step of the 5S Method is "Sustain." This principle involves continuously monitoring and improving the work environment. This could involve regular audits, updating procedures, or incorporating feedback from employees. By continuously improving, organizations are able to maintain the benefits of the 5S Method and ensure that they remain at the forefront of efficiency and productivity.
In a nutshell order and cleanliness are critical components of a successful and efficient work environment. By following the 5S Method, organizations are able to create a work environment that is safe, efficient, and conducive to high performance. Whether you are an office worker or a factory worker, the 5S Method can help you achieve a more productive and effective work environment.
Point Of Use
Point of Use (POU) is a key component of Lean initiatives aimed at reducing waste, increasing efficiency, and improving overall production processes.
Point of Use (POU) is a key component of Lean initiatives aimed at reducing waste, increasing efficiency, and improving overall production processes. It is a philosophy that focuses on delivering materials, tools, and equipment directly to the worker at the moment they need them. The goal of POU is to minimize unnecessary movement, handling, and storage of materials, which not only streamlines production but also reduces the risk of damage, loss, and obsolescence.
In traditional manufacturing processes, raw materials and supplies are often stored in central locations, such as inventory rooms, and are retrieved and moved to the production line as needed. This can result in excess inventory, increased lead times, and the need for multiple trips to retrieve materials. Additionally, workers may spend significant amounts of time searching for the tools or materials they need, which reduces productivity and increases the risk of mistakes.
Point of Use aims to eliminate these inefficiencies by bringing materials and supplies directly to the worker at the point of need. This reduces the need for workers to search for materials and increases the speed and accuracy of the production process. POU also reduces the amount of inventory that needs to be stored and managed, which helps to reduce the risk of damage, loss, and obsolescence.
There are several different approaches to implementing POU, each with its own set of benefits and challenges. One approach is to use kanban systems, which are visual signals that tell workers when it’s time to replenish materials or supplies. Another approach is to use automated systems, such as conveyors or robots, which move materials and supplies directly to the production line as needed.
Regardless of the approach used, POU requires careful planning and coordination between all departments involved in the production process. It also requires regular monitoring and adjustments to ensure that the system is working as intended. This can include tracking key performance indicators (KPIs) such as inventory levels, production lead times, and worker productivity.
One of the benefits of POU is that it helps to improve worker morale and job satisfaction. When workers have access to the materials and supplies they need exactly when they need them, they are able to focus on their work without worrying about finding the right tools or supplies. Additionally, POU helps to eliminate the frustration that workers may feel when they are unable to find the materials they need, which can lead to decreased job satisfaction and even burnout.
Another benefit of POU is that it helps to reduce the risk of mistakes and increase quality. When workers have everything they need at their fingertips, they are able to focus on their work without worrying about searching for materials or supplies. This reduces the risk of errors, which in turn helps to improve overall quality and reduce the need for rework.
In a nutshell, Point of Use is an important concept in Lean Manufacturing that aims to reduce waste, increase efficiency, and improve overall production processes. By bringing materials and supplies directly to the worker at the point of need, POU streamlines production, reduces the risk of damage, loss, and obsolescence, and improves worker morale and job satisfaction. To be successful, POU requires careful planning, coordination, and monitoring, as well as a focus on continuous improvement. By implementing POU and other Lean principles, manufacturers can reduce costs, increase efficiency, and improve overall production outcomes.
Rapid Improvement Event
Rapid Improvement Events, also known as Kaizen events, are a powerful tool for improving production processes in every industry.
Rapid Improvement Events, also known as Kaizen events, are a powerful tool for improving production processes in the manufacturing industry. They are focused, short-term initiatives aimed at solving specific problems and improving processes in a rapid and efficient manner.
At the heart of a Rapid Improvement Event is the involvement of a cross-functional team of employees, each bringing a unique perspective and skillset to the table. The team works together to identify and solve problems, test new ideas, and implement solutions that can have an immediate impact on the production process.
One of the key benefits of Rapid Improvement Events is the speed with which they can deliver results. By focusing on a specific problem and working together as a team, significant improvements can be made in just a few days or weeks. This can be especially valuable in the manufacturing industry, where time is often of the essence and even small improvements can make a big difference.
To ensure the success of a Rapid Improvement Event, it's important to follow a structured methodology. This typically includes the following steps:
Define the problem and scope of the event. What is the specific issue that needs to be addressed, and what is the desired outcome of the event?
Assemble the cross-functional team. Choose team members who have a strong understanding of the problem and can bring a variety of skills and perspectives to the table.
Conduct a thorough analysis of the problem. Gather data, observe processes, and engage in root cause analysis to understand the underlying cause of the problem.
Develop and implement a plan of action. Based on the findings of the analysis, create a plan of action that addresses the root cause of the problem and implements solutions that will improve the production process.
Implement and monitor the changes. Once the plan of action is in place, implement the changes and monitor the results to ensure they are having the desired impact.
Reflect and celebrate successes. Reflect on the successes of the event and celebrate the improvements that were made.
Rapid Improvement Events are a powerful tool for improving production processes in the manufacturing industry. By bringing together a cross-functional team, focusing on a specific problem, and following a structured methodology, organizations can achieve significant improvements in a short amount of time.
In a nutshell, it is important to embrace a continuous improvement mindset and actively seek out opportunities to improve production processes. Rapid Improvement Events provide a structured and efficient way to do just that, delivering results that can have a lasting impact on an organization's success.
Cell Production
Cell Production focuses on optimizing the flow of work and improving efficiency in manufacturing and operations.
Cell Production focuses on optimizing the flow of work and improving efficiency in manufacturing and operations. It is based on the concept of organizing work into cells, which are self-contained units responsible for performing a specific set of tasks. The goal of cell production is to minimize waste, increase flexibility, and improve overall performance.
The origins of cell production can be traced back to the 1950s and 60s, when Toyota and other Japanese companies were experimenting with new approaches to manufacturing. Over time, the concept of cell production has evolved and been refined, and today it is widely used in a variety of industries, including automotive, electronics, and consumer goods.
In order to implement cell production effectively, there are several key steps that organizations must take. Firstly, it is important to conduct a thorough analysis of the current state of the manufacturing or operations process, in order to identify areas where improvements can be made. This may involve mapping out the flow of work and identifying bottlenecks or other inefficiencies.
Once these areas have been identified, the next step is to reorganize the work into cells, taking into account the specific requirements of each cell and the skills and expertise of the employees who will be working in them. This may involve rearranging physical work spaces, or changing the way that work is assigned and managed.
It is also important to establish clear communication and feedback mechanisms, so that employees and teams can work together effectively. This may involve setting up regular meetings to discuss performance, or implementing systems for tracking and reporting on key metrics.
In order to ensure a successful implementation of cell production, it is also important to provide training and support for employees. This may involve providing training on the new processes and procedures, or offering coaching and mentoring to help employees develop the skills and knowledge they need to be effective.
Another key aspect of cell production is continuous improvement. This involves regularly reviewing performance and making adjustments as needed, in order to optimize efficiency and reduce waste. This may involve experimenting with different approaches, such as implementing new technologies or streamlining processes, in order to find the best solutions.
In conclusion, cell production is a powerful methodology for optimizing performance in operations and manufacturing. By reorganizing work into cells, minimizing waste, and continuously improving performance, organizations can increase efficiency, reduce costs, and improve overall performance. In order to be successful, organizations must take a structured and systematic approach, and be committed to ongoing improvement.
TPM - Total Productive Maintenance
Total Productive Maintenance (TPM) is a maintenance strategy that involves involving all employees in the maintenance process to maximize equipment productivity and minimize downtime.
Total Productive Maintenance (TPM) is a methodology that originated in Japan in the 1970s and has since become a widely recognized and adopted approach to operational excellence in manufacturing and other operations-focused industries. It is a comprehensive approach that seeks to optimize the performance of equipment and processes through a focus on maintaining and improving reliability and efficiency.
The origins of TPM can be traced back to the Japanese auto industry, where manufacturers were seeking ways to increase productivity and competitiveness in the face of increasing global competition. TPM emerged as a response to the need for a more proactive and integrated approach to equipment maintenance, with the goal of improving both productivity and overall equipment effectiveness (OEE).
Over time, TPM has evolved and expanded to encompass a wider range of objectives and activities. Today, it is widely regarded as a best-practice approach to operational excellence, and is widely used in many different industries, including manufacturing, healthcare, and government operations.
One of the key features of TPM is its focus on involving all employees in the maintenance and improvement process. This is achieved through the creation of cross-functional teams and the use of a range of techniques, including root cause analysis, standardization, and continuous improvement.
Another key aspect of TPM is its focus on data-driven decision-making and performance measurement. This involves the collection and analysis of data on equipment and process performance, which is then used to identify areas for improvement and to drive continuous improvement efforts.
When properly implemented, TPM can have a significant impact on organizational performance and competitiveness. This can include improvements in equipment reliability, increased productivity, reduced waste, and improved overall equipment effectiveness (OEE).
To achieve these benefits, it is important to implement TPM in a structured and systematic way, with clear goals and objectives and a strong focus on continuous improvement. This typically involves a multi-phased approach, starting with an assessment of existing processes and equipment, followed by the development of a comprehensive improvement plan and the implementation of specific improvement initiatives.
In a nutshell, TPM is a proven methodology that can help organizations achieve operational excellence by optimizing the performance of their equipment and processes. To achieve success, organizations must approach TPM in a systematic and structured way, with clear goals and objectives, and a strong focus on continuous improvement.
Key points for a successful TPM implementation:
Involve all employees in the process
Focus on data-driven decision-making
Adopt a multi-phased approach
Prioritize continuous improvement
Develop a comprehensive improvement plan.
Standard Layout
A standard layout is a detailed, visual representation of the ideal workflow and arrangement of resources in a given area.
Standard Layout: The Key to Unlocking Efficiency in Lean Management
Standardization is one of the fundamental principles of lean management, and it's no surprise that it's also one of the most effective ways to improve efficiency and reduce waste in your operations. One of the most powerful tools in the standardization toolbox is the standard layout, also known as "taikyō-sei" in Japanese.
A standard layout is a detailed, visual representation of the ideal workflow and arrangement of resources in a given area. This can include anything from the placement of tools and equipment to the flow of materials and the location of workstations. The goal is to create a clear and consistent way of working that minimizes waste, maximizes efficiency, and makes it easy for everyone on the team to understand and follow.
One of the most important benefits of a standard layout is that it makes it much easier to identify and eliminate sources of waste and inefficiency. By clearly defining the ideal way of working, it becomes much easier to see where things are going wrong and to make adjustments as needed. This can include anything from adjusting the location of workstations to the flow of materials, to the type and size of tools and equipment.
Another key benefit of a standard layout is that it makes it much easier to train new employees and to ensure that everyone is following the same processes. When everyone is working in the same way, it becomes much easier to share knowledge and best practices, which can help to improve the overall performance of the team.
Finally, a standard layout can also be a powerful tool for continuous improvement. By clearly defining the ideal way of working, it becomes much easier to measure performance and to identify areas for improvement. This can include anything from adjusting the flow of materials to the location of workstations, to the type and size of tools and equipment.
So, how do you go about creating a standard layout? The first step is to conduct a thorough analysis of your current operations. This should include a detailed study of the flow of materials, the location of workstations, and the type and size of tools and equipment. You should also pay close attention to the flow of people and information, as this can have a big impact on overall efficiency.
Once you have a good understanding of your current operations, you can then begin to create a detailed, visual representation of the ideal workflow and arrangement of resources. This should include everything from the placement of tools and equipment to the flow of materials and the location of workstations.
It's also important to involve your entire team in the process of creating a standard layout. This will help to ensure that everyone is on board with the changes and that everyone understands the benefits of standardization.
Once you have a standard layout in place, it's important to monitor and measure its effectiveness on a regular basis. This can include anything from tracking the flow of materials to the location of workstations, to the type and size of tools and equipment. It's also important to involve your entire team in the process of monitoring and measuring performance, as this will help to ensure that everyone is committed to continuous improvement.
In conclusion, a standard layout is a powerful tool for unlocking efficiency in lean management. By clearly defining the ideal way of working, it becomes much easier to see where things are going wrong and to make adjustments as needed. This can include anything from adjusting the flow of materials to the location of workstations, to the type and size of tools and equipment. Furthermore, it is a powerful tool for training, knowledge sharing, and continuous improvement. If you're looking to improve efficiency and reduce waste in your operations, a standard layout is definitely worth considering.
Implementation of 5S
The 5S Method is a five-level system for the provision of safety, cleanliness and orderliness on the workplace.
If you want the short version just go here. Otherwise we will deep dive in this article on how to implement the 5S methodology in your organization. We will simply follow the 5 Steps and explain the topics.
1st S SEIRI = Sort out all unnecessary objects
Unnecessary objects are all objects that are not needed for the current manufacturing processes (production, logistics, quality, and administration, etc.), that means, defective parts, unused material, material that has been written-off, all spare parts, non-utilized tables and so on
Determine in advance, what is truly needed. This is helpful when dealing with statements such as: “That still can be used“, “That should be useful for something,“ etc.
Remove all redundant objects or at least visually mark them so that everybody is aware that they are to be disposed of
Unused objects should be concentrated in one marked closed area. The decision about those that can not be immediately liquidated, as whether to dispose of them, should be made by the person responsible within 2 weeks
Target: At the workplace are only objects essential for the current work in progress.
Red Tag Campaign
Ask three questions for each separate object:
Is this object useful?
How many of these objects do we need?
Where should this object be stored?
Don‘t support others in searching for excuses. Be fair – mark objects that should be removed in all divisions of the company
Don‘t compromise! When in doubt - the rule applies: Get rid of it!
If there are suggestions for improvement of the current manufacturing process, it is possible to “red tag“ even objects still in use
Make sure that everybody understands what should be marked and why
Course of action and rules for the “Red Tag Campaign”
Write on the tag why the marked object is not needed (Example: Surplus packing boxes; parts stored in boxes are not used any more)
Contact Information about the person who made the decision that the object is superfluous (name and department)
The person responsible for the object will be informed and their name will be entered on the “Red Tag”, and along with the agreed-upon date of removal (maximum 3 days), the action should be recorded (Example: The employee who recognized that the boxes are not used anymore, will inform the warehouse attendant and will appeal to him to verify if they are really not of use anymore. If it will be discovered that the object is still in use, the “Red Tag” will be removed. (For instance: The warehouse manager finds out that the boxes will be used to store other parts very soon)
If the object will be classified among the superfluous, it must be removed within three days by the person who has the responsibility for this area. (For instance: Redundant storage boxes - person responsible for the warehouse). Afterwards the “Red Tag” can be liquidated
Objects can be “Red Tagged” only in working areas of ones responsibility. The Shift Leader can issue “Red Tags” in the entire area they are responsible for
The “Red Tag” will be filled out by hand and attached to the unwanted object.
Examples of unwanted objects:
1 Defective products
Faulty parts
Rejects
2 Unnecessary objects
Unused empty packaging
Personal objects (on undefined places)
Unneeded assembly sets
Unused material (remaining bundles)
Unused tools, auxiliary and production material
Inventory no longer being used
Surplus of manufactured components
2nd S SEITON = Clean-up and correct arrangement of needed objects
After the removal of all unnecessary objects, remove all uncleanness, as new organization of areas for laying down objects or their storage can start only after everything is clean
Each machine and each tool must have its designated place.
Thoroughly deliberate about where you will store material, tools, and equipment
Use colored markings (for instance stickers) to designate areas, cabinets, shelves, cupboards with shelves, important places, direction of work procedures, etc.
With each object ask three key questions: Where? What? How many?
Permanent storage of objects in
Targets:
A place for each object and each object in its place
Visual control and expedient detection of deviations
Proper storage of all needed objects in the right place. These objects can then be found and used whenever needed
Every thing has its own place and after its use is always returned to its place!
Think about color markings on the floor e.g.:
Yellow = transportation zone
White = raw material
Green = finished goods
Red = closed area/NOK parts
3rd S SEISO = Keeping the workplace tidy so as to achieve the already established standards through 5S
The purpose of the cleaning action is to remove all contamination from the workplace and to maintain it in order.
For this purpose a cleaning schedule will be formulated that will determine what is to be cleaned, with what, and by whom
If you discover any shortcomings or abnormalities during the cleaning process – mark them down
All employees of the workplace / work area will participate in the cleaning process
Keep records of the cleaning process, display visually “Red Tags,” as well as the clean-up time schedule of your workplace. Display results
Define responsibilities with consideration even to the smallest work sections
Be effective. Even a five-minute cleansing action can achieve a lot
Targets:
Cleaner and safer workplace
Achieving the already established standards
Cleanliness
Cleanliness at the workplace must be observed, because a clean workplace is essential towards quality and safety at work
If the workplace is not dirty it is not necessary to clean it
Any kind of uncleanness and any kind of untidiness will be visible thanks to the initiation of a regular cleaning process – for instance, dusting, sweeping, and waste disposal
Continuous usage of equipment
Removal of all uncleanness and untidiness
Prevention of working accidents
Cleanliness means controlling, which implies that when cleaning a certain workplace, also check the state of the machinery, equipment, and working conditions
4th S SEIKETSU – Establishing regulations for work standards
SEIKETSU has the greatest importance of all 5S Steps.
With this 5S Step the main focus is on three aspects:
No unnecessary objects
No messiness and
No uncleanliness
Visual control is the first step towards discipline. The ideal workplace is that with which any eventual problems can be detected at first glance – any corrective measures can be immediately implemented
Use control lists to control the 5S standard and to identify deviations from the defined 5S standards
Conduct 5S audits with consideration to the situation on the individual work place. Attempt to identify deviations from the 5S standards
Ask yourself “follow-up questions”, as for instance: Has the mess been cleaned up immediately? Is it clear who is supposed to do the job? Can the clean-up be done quickly? - and others
Targets:
Securing the adherence to the 5S Standards
Increasing the team responsibility on the work place
Schedule of everyday clean-up
5th S SHITSUKE – Adherence to the Work standards and continuous improvement
Discipline, namely, adherence to work standards is basically a question of personal attitude. For it to be easier, various teaching aids are used, e.g. Courses of the 5S Basics
Use photographs, single-topic lectures, video-programs and presentations
Constructive criticism is the foundation for proper 5S training
Take pictures to document the status quo before and after
The Team Leader functions as an example to the team. During his work he should focus on the goals of 5S, he should strive for a continuous improvement of quality and in this direction aim his training activity also
Define together the measures for improvement and how to realize them.
Regulations are better than criticism and a system is better than regulations
Targets:
Promotion of this know-how in the entire company from top-to-bottom
Well-organized work places that require only the minimum attention
5S
The 5S Method is a five-level system for the provision of safety, cleanliness and orderliness on the workplace.
The 5S Method is a five-level system for the provision of safety, cleanliness and orderliness at the workplace. The term „5S“ is coming from 5 Japanese words that begin with the letter „S“.
These 5 words describe the 5 principles for the organization of the workplace:
1S – SEIRI
Cleaning: Sorting-out and get rid of all unwanted objects.
2S – SEITON
Orderliness: Clean-up and proper arrange tools needed.
3S – SEISO
Cleanliness: Maintain cleanliness at the workplace and keep the standards established through 5S workshops.
4S – SEIKETSU
Standardization: Establishing work standards developed by 5S sessions.
5S – SHITSU
Discipline: Observing compliance of new work standards and drive for continuous improvement.
Why do we need 5S?
Goals of the 5S during the implementation:
Safety
Flexibility
Quality
Costs
Ergonomics
How can you implement 5S at your organization?
How to implement 5S
The 5 steps of the 5S-Method:
Sorting out all unnecessary objects at your workplace
All needed objects have to be arranged in a proper way
Keep your workplace clean
Standardize the steps 1 to 3
Keep your new standard or improve it even more
5S is a continuous process!
The 5S checklist
In order to maintain the 5S procedure and standard you should be implementing a routine of a so called 5S audit. The 5S audit is an instrument of sustainable implementation of the five step system for safety, cleanliness and order at your workplace.
Therefore 5S is relevant in all areas of your company, no matter if you are working in a office or your focus is on the shop floor. To maintain the 5S implementation and the ongoing improvement of all 5 steps. The audit can support you on identifying deviation and to improve.
So why do you need the 5S Method?
It supports you on
Reduction of uncleanliness and its causes in the company
Reduction of latent waste in the company (e.g. untidiness, unneeded objects)
Reduction of defective equipment and tooling
Reduction of deviations from standardized manufacturing procedures due to unnecessary objects and frequent searches for misplaced objects
Increasing the awareness of the employees about tidiness, cleanliness, waste and deviations from standardized manufacturing procedures
Enhancing the positive impression of the company towards the customer
So what are the goals when you implement 5S in your company?
1 Increase safety at the workplace
Everything lies in its right place and employees receive a standardized and up-to-date description of their workplace
The employees know where to find everything needed in the case of an emergency
Markings on the floor are used as a visual control aid to help the employees to stay clear of any dangerous situations
2 Increased capability to react
Expeditious reaction to the requests of the customer and expediting the manufacturing process
By involving all employees, the internal flow of communication is enhanced along with the identification and removal of mistakes
It supports the expeditious preparation of e.g. work procedures, replacement of tools, increased flexibility of the employees, streamlines the work processes, increases the general economy by making the work procedures more effective; and expedites the continuous process of enhancement
Mistakes and deviations from the standardized work procedures become an exception and can be quickly eliminated
This reading pick will show you the methodology as well as real doing and conducting of 5S Sessions. It is a great guidance and a step by step instruction with lots of advice and practical tools that will allow you to conduct your 5S project from A-Z.
Read more in our reading picks here.
3 Enhanced quality
The proper arrangement of material and equipment decreases the amount of defective products and improves the repeatability of the work process
Enables the employees to determine at first glance what is needed to do to ensure quality
Makes the problems more perceivable and thus enables their solution
4 Cost reduction
Shortens unnecessary searches and reduces the time needed to find objects
Shortening time for exchange of tools > SMED
Creating new areas
Eliminating all unnecessary objects
Too excessive or insufficient supplies are discovered and are made visible
Expedient realization of counter-measures
5S designates the 5 basic principles for creating a clean, well-arranged and effective workplace with competent employees – the basis is orderliness = 5S.
5 Developing a “Visual Workplace”
In the case of a visually created workplace the work procedures are adjusted to enable all employees to have the possibility to observe the actual work process
Visualization:
Organization of the workplace
Manufacturing process
Distractions, such as defective objects, sources of danger etc.
Production indicators (plan, overproduction, or as the case may be, underproduction)
How can a 5S Audit support you?
The 5S Method makes sure that each workplace, in the production or office, is organized according to the principles of cleanliness, orderliness and safety
To secure the permanence and the continuity of adherence to the defined 5S standards it is necessary to regularly conduct 5S Audits
For the different areas of Production or Administration and others, specific questionnaires are prepared, on basis of which the obvious deviations from the defined planned state can be detected
The 5S questionnaires are combined with a list of counter-measures necessary to rectify the situation along with the names of responsible persons
Stay Connected
Ad
We want information fast and in a nutshell. We from OI recommend Blinkist* - because it’s simply the best.
* = Affiliate Link