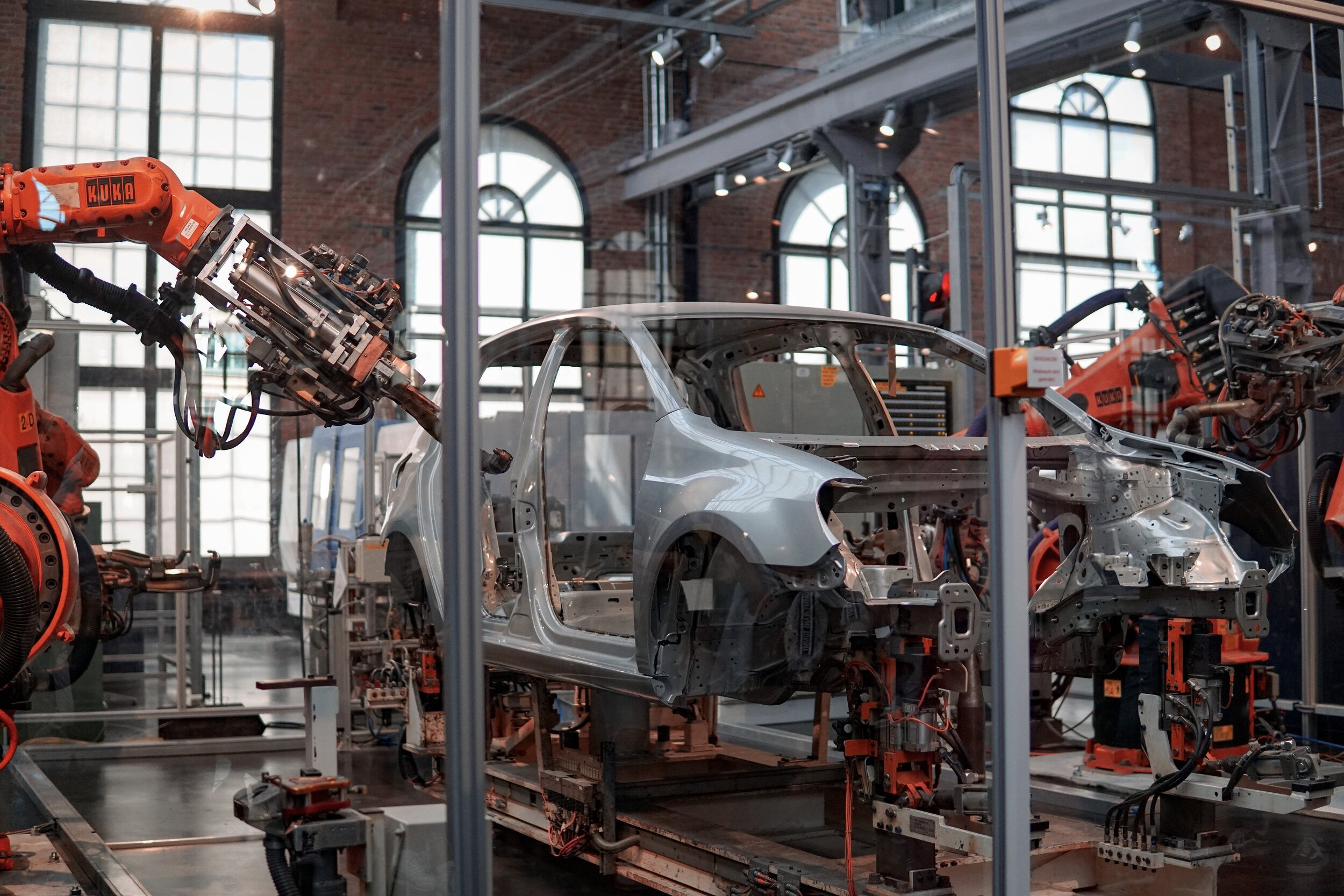
LANGUAGE OF LEAN
Internal Setup
Internal Setup, also known as Machine Changeover or Equipment Changeover, is a critical aspect of Lean Manufacturing. It refers to the process of switching a production machine from one product or production run to another.
Internal Setup, also known as Machine Changeover or Equipment Changeover, is a critical aspect of Lean Manufacturing. It refers to the process of switching a production machine from one product or production run to another. This process can be time-consuming and impact the overall efficiency of a manufacturing plant. For this reason, Lean experts have developed techniques to optimize the Internal Setup process and minimize downtime.
The Internal Setup process can be seen as a non-value-adding (NVA) activity. NVA activities are those that do not directly contribute to the production of a good or service. In the case of Internal Setup, it is necessary but does not add any value to the final product. The goal of Lean is to minimize NVA activities, and the Internal Setup process is no exception.
One of the key strategies for optimizing Internal Setup is to standardize the process. This can be achieved by creating detailed Standard Operating Procedures (SOPs) that outline each step of the setup process. SOPs should include clear instructions, diagrams, and photos to help guide employees through the process. The SOPs should also be reviewed and updated regularly to ensure they are up-to-date and accurate.
In addition to standardizing the process, Lean experts also focus on reducing the time required for Internal Setup. This can be achieved through a combination of reducing the number of steps required and streamlining the process. For example, the use of Quick Changeover fixtures or tools can reduce the time required to changeover a machine. Other strategies include minimizing the number of tools required, using visual aids to guide employees through the process, and using checklists to ensure all steps are completed.
Another important aspect of optimizing Internal Setup is employee engagement and involvement. Lean experts believe that employees who are involved in the process are more likely to take ownership of the process and be more committed to making it as efficient as possible. Encouraging employees to identify areas for improvement and participate in Kaizen events can also help drive continuous improvement.
Finally, it is important to monitor and evaluate the Internal Setup process on a regular basis. This can be done by tracking key performance indicators (KPIs) such as changeover time, number of changeovers, and machine downtime. The KPIs can be used to identify areas for improvement and measure the success of continuous improvement initiatives.
In a nutshell, Internal Setup is a critical aspect of Lean Manufacturing and Operational Excellence. To optimize the process and minimize downtime, Lean experts focus on standardizing the process, reducing the time required, involving employees, and monitoring and evaluating the process. By following these principles, manufacturers can achieve a more efficient and streamlined Internal Setup process, resulting in increased productivity, reduced waste, and improved bottom-line results.
LCIA
Low Cost Intelligent Automation (LCIA) has been a buzzword in the manufacturing industry for the past few years, promising to revolutionize the way companies approach production and efficiency.
Low Cost Intelligent Automation (LCIA) has been a buzzword in the manufacturing industry for the past few years, promising to revolutionize the way companies approach production and efficiency. We have seen the impact that LCIA can have on a company and how it can drive significant improvements in the areas of cost, productivity, and quality. In this article, we will discuss the origin of LCIA, how it works, and what it takes to implement it successfully in the manufacturing industry.
The concept of LCIA originated from the need for companies to stay competitive in an increasingly challenging market environment. The global market is more competitive than ever before, and companies must continuously look for new ways to streamline their operations, reduce costs, and improve their overall performance. The traditional approaches to automation, such as custom-made solutions and expensive software packages, have been prohibitively expensive for many companies. LCIA provides a cost-effective alternative, allowing companies to automate their processes without breaking the bank.
LCIA works by using commercially available hardware and software components to create an automation solution tailored to a company's specific needs. The use of off-the-shelf components reduces costs significantly and also speeds up the implementation process. The system is designed to be flexible and easily adaptable, allowing companies to make changes as their business needs evolve. The automation solution is typically designed to be as simple as possible, reducing the need for extensive training and minimizing the risk of downtime.
Implementing LCIA in a manufacturing environment requires careful planning and execution. The first step is to assess the current state of the operation, identify areas where automation can improve efficiency and productivity, and determine the specific requirements of the LCIA solution. This requires a thorough understanding of the production process, the use of data analysis tools to identify areas of waste and inefficiency, and a clear vision of what the desired outcome of the implementation will be.
Once the assessment is complete, the next step is to develop an implementation plan. This plan should outline the goals and objectives of the LCIA implementation, the resources required, the timeline, and the budget. It should also outline the role of key stakeholders, such as employees, suppliers, and customers, in the implementation process. Effective communication with all stakeholders is critical to ensure that everyone understands the objectives of the implementation and is able to provide the necessary support.
The implementation of LCIA requires a comprehensive approach that involves the right tools, the right mindset, and the right approach. This means that companies must invest in the necessary hardware and software components, ensure that their employees are trained in the use of the new systems and technologies, and work to integrate the LCIA solution into their existing processes and systems.
Monitoring and evaluation are critical components of any LCIA implementation. The effectiveness of the solution must be continuously monitored, and adjustments must be made as necessary to ensure that the desired outcomes are achieved. The implementation should be evaluated regularly to determine its impact on operational performance, customer satisfaction, and process and system improvement.
In a nutshell, LCIA provides a cost-effective alternative to traditional automation solutions, and has the potential to drive significant improvements in the areas of cost, productivity, and quality in the manufacturing industry. Successful implementation requires careful planning, a comprehensive approach, and continuous monitoring and evaluation. Companies that invest in LCIA can expect to achieve their desired outcomes, while maintaining a lean and efficient operation.
Stay Connected
Ad
We want information fast and in a nutshell. We from OI recommend Blinkist* - because it’s simply the best.
* = Affiliate Link