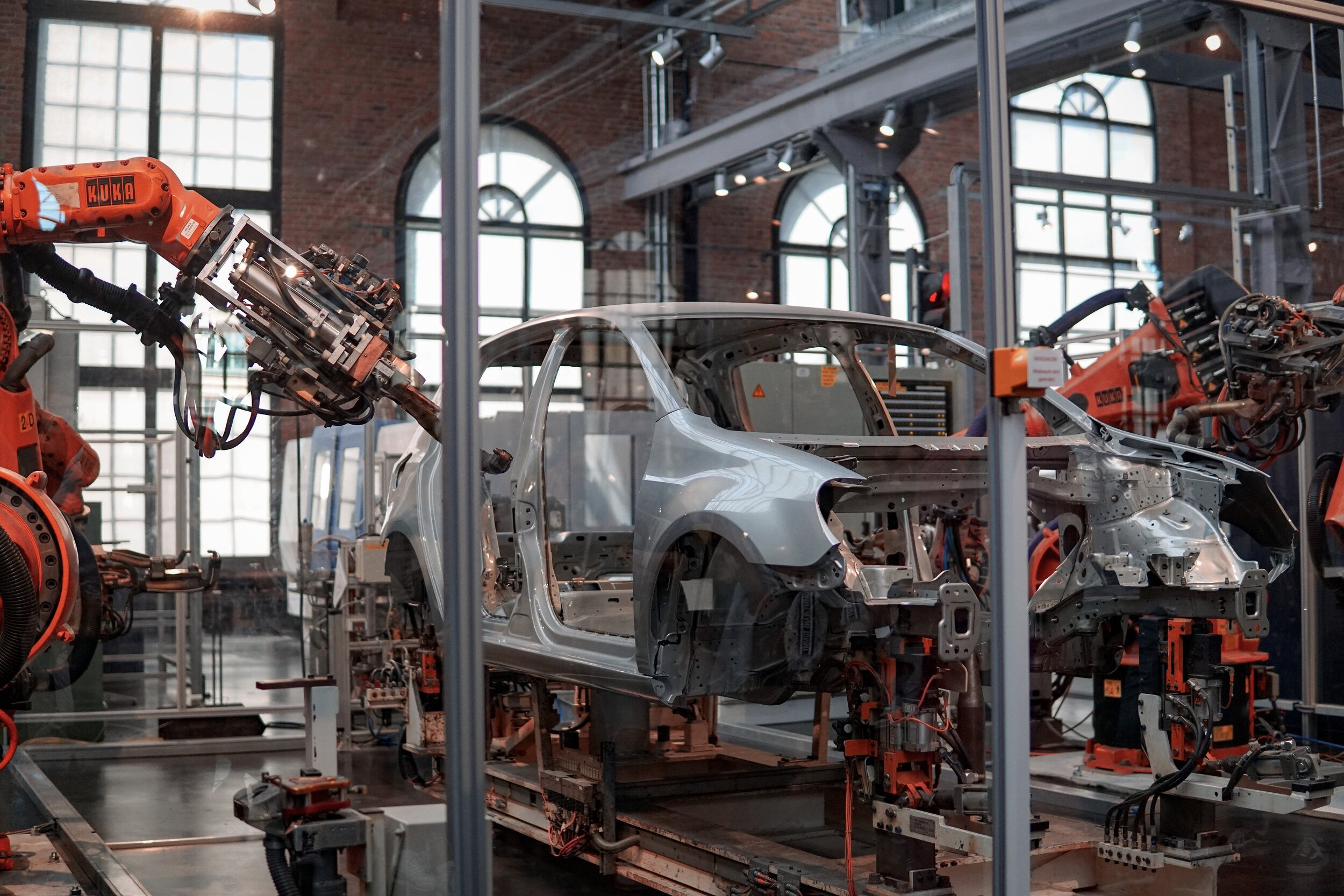
LANGUAGE OF LEAN
Flow Cell
One of the key principles of lean management is the flow cell principle, which is all about optimizing the flow of materials, information, and processes within a manufacturing facility.
Lean management is a production philosophy that seeks to streamline operations and eliminate waste, thereby improving efficiency and reducing costs. One of the key principles of lean management is the flow cell principle, which is all about optimizing the flow of materials, information, and processes within a manufacturing facility.
The flow cell principle is based on the idea that work should be performed in a continuous and uninterrupted flow, without any idle time or unnecessary delays. This principle is critical to achieving lean goals such as reducing lead times, improving quality, and increasing productivity. In order to implement the flow cell principle, a manufacturing facility must first identify and eliminate bottlenecks and constraints in its operations.
The flow cell principle can be applied to a variety of processes within a manufacturing facility, from raw material intake to finished product shipment. For example, in a manufacturing cell, raw materials are moved from one station to another in a continuous flow, without any stops or interruptions. Each station is designed to perform a specific task, and the flow of materials is carefully controlled to ensure that the entire process is as efficient as possible.
The flow cell principle is not just about physical movement of materials, however. It also involves the flow of information, as data must be shared in real-time across different departments and processes in order to optimize flow. A well-designed flow cell system should also include checks and balances to ensure that quality standards are met and that products are being produced to the required specifications.
Another key aspect of the flow cell principle is continuous improvement. Lean management emphasizes the importance of continuous improvement, and the flow cell principle is no exception. By constantly monitoring and analyzing the flow of materials, information, and processes, manufacturing facilities can identify areas for improvement and make the necessary changes to optimize their operations.
In conclusion, the flow cell principle is a critical component of lean management and is essential for achieving lean goals such as reducing lead times, improving quality, and increasing productivity. To fully realize the benefits of the flow cell principle, manufacturing facilities must implement it as part of a comprehensive lean management program, which includes continuous improvement, real-time data sharing, and strict quality control measures.
Cardboard Engineering
Cardboard engineering, also known as corrugated cardboard engineering, is a concept that is gaining popularity in the world of manufacturing.
Cardboard engineering, also known as corrugated cardboard engineering, is a concept that is gaining popularity in the world of manufacturing. This approach is based on the use of cardboard mock-ups, prototypes, and models to visualize, test, and improve manufacturing processes and product design.
We would like to provide an overview of cardboard engineering and its application in a manufacturing setting.
Cardboard engineering is a low-cost, fast, and efficient method for testing and refining manufacturing processes and product design. The approach is based on the use of cardboard prototypes and models to simulate the manufacturing process and identify potential challenges and limitations. This allows manufacturers to quickly test and refine their processes and products without incurring the costs and delays associated with traditional prototyping methods.
The use of cardboard engineering has several benefits in a manufacturing setting. Some of these benefits include:
Low cost: Cardboard engineering is a low-cost method for testing and refining manufacturing processes and product design. This makes it accessible to a wide range of manufacturers, regardless of size or budget.
Fast: Cardboard engineering allows manufacturers to quickly test and refine their processes and products, reducing the time required to bring new products to market.
Improved design: By using cardboard prototypes and models, manufacturers can quickly identify potential challenges and limitations in their product design and make improvements accordingly.
Improved efficiency: Cardboard engineering helps manufacturers to optimize their processes and products, leading to improved efficiency and reduced waste.
Increased collaboration: The use of cardboard prototypes and models promotes collaboration and communication between departments, improving the overall efficiency of the manufacturing process.
In order to implement cardboard engineering in a manufacturing setting, it is important to follow a structured approach. This may include the following steps:
Identify the problem: Identify the challenges and limitations in the manufacturing process or product design that need to be addressed.
Create a cardboard prototype: Create a cardboard prototype or model that simulates the manufacturing process or product design.
Test and refine: Test the cardboard prototype or model and refine the process or product design as needed.
Implement changes: Implement any changes identified during the testing and refinement process.
Continuous improvement: Continuously monitor the manufacturing process and make improvements as needed to optimize efficiency and reduce waste.
In a nutshell, cardboard engineering is a valuable tool for manufacturers looking to improve their processes and products. By using cardboard prototypes and models, manufacturers can quickly test and refine their processes and products, leading to improved efficiency, reduced waste, and increased collaboration. By following a structured approach and continuously monitoring their processes, manufacturers can ensure that they are always working to improve their operations and products
Line Balancing
Line balancing is a critical component of lean manufacturing and is a key tool for improving efficiency, reducing waste, and increasing productivity.
Line balancing is a critical component of lean manufacturing and is a key tool for improving efficiency, reducing waste, and increasing productivity. The principle of line balancing is to ensure that every workstation on a production line is working at optimal capacity and that the overall line is balanced in terms of the workload and resources available.
We would like to provide an overview of the line balancing principle and its application in a manufacturing setting.
Line balancing is a process that involves analyzing the production line and determining the ideal workload for each workstation. This is done by breaking down the tasks involved in producing a product into individual steps, and then determining the time required to complete each step. Once this has been done, the steps are assigned to workstations, taking into account the workload and resources available.
The goal of line balancing is to ensure that each workstation is working at optimal capacity, with no workstation being overworked or underutilized. This results in a more efficient production line, with less waste and reduced lead times.
There are several benefits to line balancing in a manufacturing setting. Some of these benefits include:
Increased efficiency: Line balancing helps to ensure that each workstation is working at optimal capacity, which leads to increased efficiency and reduced waste.
Reduced lead times: By ensuring that each workstation is working efficiently, line balancing can help to reduce lead times and improve delivery times.
Improved quality: Line balancing helps to ensure that each workstation is working at the appropriate pace, which can help to improve quality and reduce the risk of defects.
Increased productivity: Line balancing helps to optimize the use of resources, which can lead to increased productivity and reduced costs.
Improved work environment: Line balancing helps to create a more balanced and less stressful work environment, which can improve employee morale and reduce turnover.
In order to implement line balancing in a manufacturing setting, it is important to follow a structured approach. This may include the following steps:
Define the production line: Define the production line and identify the workstations involved in the process.
Break down the process: Break down the process into individual steps and determine the time required to complete each step.
Assign tasks to workstations: Assign tasks to workstations based on the workload and resources available.
Monitor performance: Continuously monitor performance and make adjustments as necessary to ensure that the line is balanced and working at optimal capacity.
In a nutshell, line balancing is a key tool for improving efficiency and reducing waste in a manufacturing setting. By following a structured approach and continuously monitoring performance, manufacturers can ensure that their production lines are working at optimal capacity, leading to improved efficiency, reduced lead times, and increased productivity.
Change Over
Change overs refer to the process of switching a production line from producing one product to producing another.
Change overs refer to the process of switching a production line from producing one product to producing another. This process can have a significant impact on the efficiency and profitability of a manufacturing operation, and as a Lean Management Expert, I would like to provide an overview of change overs and how they can be improved with SMED (Single Minute Exchange of Dies) Workshops.
One of the main challenges with change overs is the time it takes to complete the process. In many cases, change overs can take several hours or even days, which can result in decreased production and increased costs. This can be a significant issue for manufacturers who need to be able to switch between products quickly and efficiently to meet customer demand.
Another challenge with change overs is the potential for mistakes and errors during the process. When a production line is being changed over, there is an increased risk of mistakes being made, such as incorrect parts being installed or procedures being skipped. This can result in decreased production quality, increased defects, and increased lead time.
In order to improve change overs, manufacturers can implement SMED Workshops. SMED Workshops are designed to streamline the change over process and reduce the time it takes to switch between products. This is achieved by identifying and eliminating non-value-added activities, such as time spent waiting for equipment to cool down or procedures that can be done in parallel. By eliminating these activities, SMED Workshops can significantly reduce the time it takes to complete change overs, allowing manufacturers to increase production efficiency and responsiveness.
SMED Workshops also help to reduce the potential for mistakes and errors during change overs by standardizing the process and reducing the number of activities that need to be performed. This can improve overall production quality, reduce defects, and increase customer satisfaction.
In nutshell, change overs can have a significant impact on the efficiency and profitability of a manufacturing operation. By implementing SMED Workshops, manufacturers can streamline the change over process, reduce the time it takes to switch between products, and improve production quality and customer satisfaction. As a Lean Management Expert, I recommend that manufacturers consider implementing SMED Workshops as a means of improving their overall production efficiency and competitiveness.
Audit
Audits are a critical component of any lean manufacturing program, as they provide a structured and systematic approach for evaluating the effectiveness of the processes and procedures in place.
Audits are a critical component of any lean manufacturing program, as they provide a structured and systematic approach for evaluating the effectiveness of the processes and procedures in place. Audits help to identify areas for improvement, track progress, and ensure that best practices are being followed.
We would like to outline the 5 steps in order to prepare and conduct a successful audit in a manufacturing setting. These steps are as follows:
Define the audit scope: Determine what areas of the manufacturing process will be evaluated during the audit. This may include areas such as production line processes, inventory management, and quality control procedures.
Gather data: Collect relevant data and information that will be used during the audit. This may include data on production volumes, inventory levels, and quality control data.
Prepare audit checklists: Develop a detailed set of checklists that will be used to evaluate the different areas of the manufacturing process. These checklists should be comprehensive and include questions about process flow, standard operating procedures, and key performance indicators.
Conduct the audit: Conduct the audit using the checklists developed in step 3. This should be done by a team of experts who have a thorough understanding of the manufacturing process and best practices.
Analyze the results: After the audit is complete, analyze the results to identify areas for improvement. This may include the development of action plans to address any areas of weakness or non-compliance.
In order to ensure a successful audit, it is important to follow a set of best practices. Here are 10 tips for a successful audit in a manufacturing setting:
Be well-prepared: Ensure that you have a thorough understanding of the manufacturing process and the areas that will be evaluated during the audit.
Use a team approach: Conduct the audit as a team to ensure that all areas are thoroughly evaluated and that all perspectives are taken into account.
Follow a structured approach: Use a structured approach and follow the audit checklists developed in step 3 to ensure a consistent and systematic evaluation of the manufacturing process.
Be objective: Maintain objectivity throughout the audit and avoid making assumptions about the manufacturing process or the results.
Focus on best practices: Evaluate the manufacturing process against best practices and ensure that these are being followed.
Be open-minded: Be open-minded and willing to consider alternative approaches and new ideas for improvement.
Be transparent: Be transparent about the audit process and the results, and communicate openly with all stakeholders.
Follow-up on action plans: Ensure that action plans are developed to address any areas of weakness or non-compliance identified during the audit.
Continuously monitor progress: Continuously monitor progress and track progress against the action plans to ensure that improvements are being made.
Encourage continuous improvement: Encourage continuous improvement and encourage all stakeholders to be involved in the audit process and to contribute to the improvement of the manufacturing process.
In a nutshell, audits are an essential component of a successful lean manufacturing program. By following the 5 steps and the 10 tips outlined above, manufacturers can ensure that they are conducting effective and successful audits that lead to continuous improvement and enhanced competitiveness.
Standard Layout
A standard layout is a detailed, visual representation of the ideal workflow and arrangement of resources in a given area.
Standard Layout: The Key to Unlocking Efficiency in Lean Management
Standardization is one of the fundamental principles of lean management, and it's no surprise that it's also one of the most effective ways to improve efficiency and reduce waste in your operations. One of the most powerful tools in the standardization toolbox is the standard layout, also known as "taikyō-sei" in Japanese.
A standard layout is a detailed, visual representation of the ideal workflow and arrangement of resources in a given area. This can include anything from the placement of tools and equipment to the flow of materials and the location of workstations. The goal is to create a clear and consistent way of working that minimizes waste, maximizes efficiency, and makes it easy for everyone on the team to understand and follow.
One of the most important benefits of a standard layout is that it makes it much easier to identify and eliminate sources of waste and inefficiency. By clearly defining the ideal way of working, it becomes much easier to see where things are going wrong and to make adjustments as needed. This can include anything from adjusting the location of workstations to the flow of materials, to the type and size of tools and equipment.
Another key benefit of a standard layout is that it makes it much easier to train new employees and to ensure that everyone is following the same processes. When everyone is working in the same way, it becomes much easier to share knowledge and best practices, which can help to improve the overall performance of the team.
Finally, a standard layout can also be a powerful tool for continuous improvement. By clearly defining the ideal way of working, it becomes much easier to measure performance and to identify areas for improvement. This can include anything from adjusting the flow of materials to the location of workstations, to the type and size of tools and equipment.
So, how do you go about creating a standard layout? The first step is to conduct a thorough analysis of your current operations. This should include a detailed study of the flow of materials, the location of workstations, and the type and size of tools and equipment. You should also pay close attention to the flow of people and information, as this can have a big impact on overall efficiency.
Once you have a good understanding of your current operations, you can then begin to create a detailed, visual representation of the ideal workflow and arrangement of resources. This should include everything from the placement of tools and equipment to the flow of materials and the location of workstations.
It's also important to involve your entire team in the process of creating a standard layout. This will help to ensure that everyone is on board with the changes and that everyone understands the benefits of standardization.
Once you have a standard layout in place, it's important to monitor and measure its effectiveness on a regular basis. This can include anything from tracking the flow of materials to the location of workstations, to the type and size of tools and equipment. It's also important to involve your entire team in the process of monitoring and measuring performance, as this will help to ensure that everyone is committed to continuous improvement.
In conclusion, a standard layout is a powerful tool for unlocking efficiency in lean management. By clearly defining the ideal way of working, it becomes much easier to see where things are going wrong and to make adjustments as needed. This can include anything from adjusting the flow of materials to the location of workstations, to the type and size of tools and equipment. Furthermore, it is a powerful tool for training, knowledge sharing, and continuous improvement. If you're looking to improve efficiency and reduce waste in your operations, a standard layout is definitely worth considering.
Stay Connected
Ad
We want information fast and in a nutshell. We from OI recommend Blinkist* - because it’s simply the best.
* = Affiliate Link