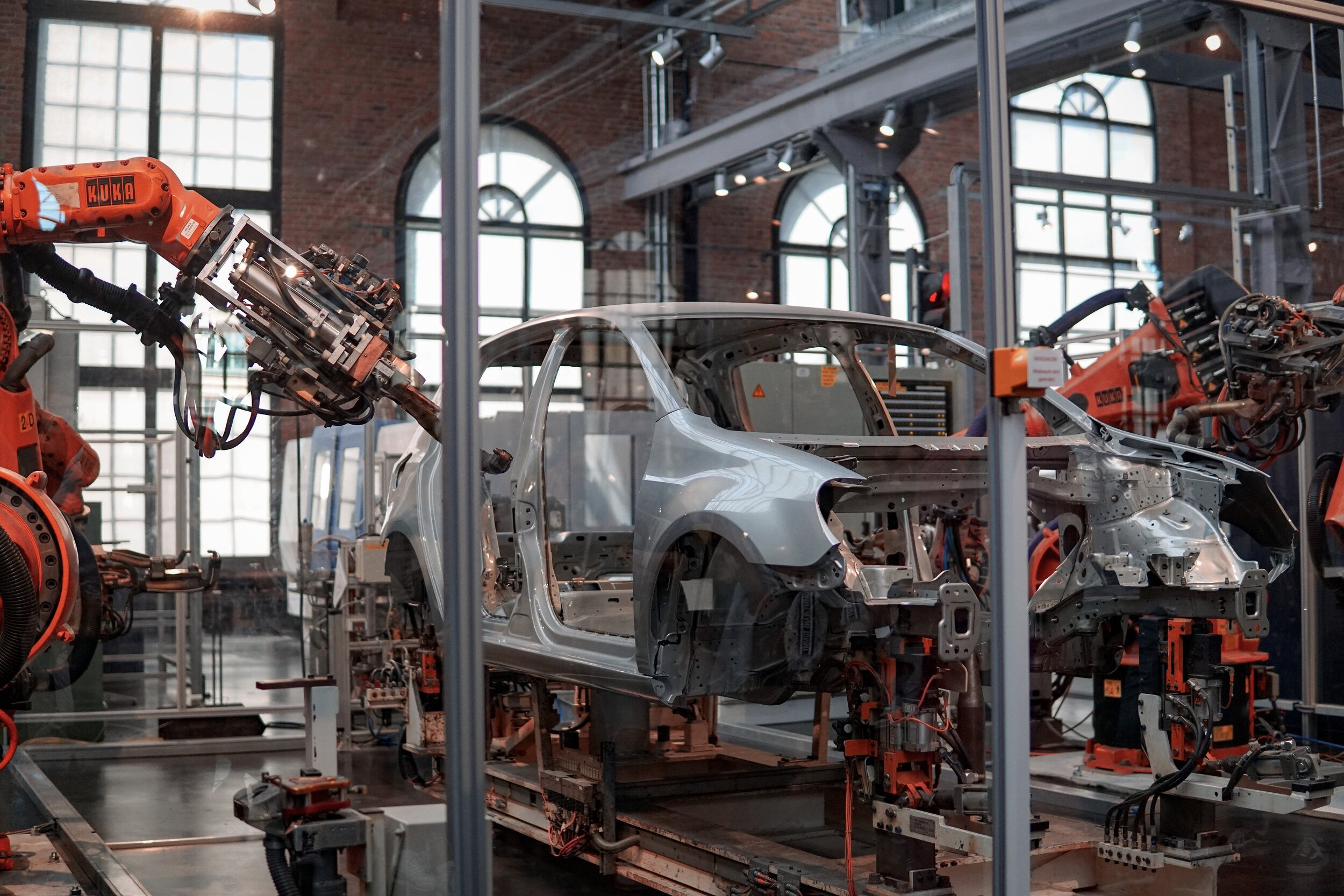
LANGUAGE OF LEAN
Overproduction
Overproduction is one of the seven kinds of wastes in the Lean Manufacturing methodology and refers to the production of goods in excess of what is immediately required by the customer. Operations Insider - connecting the dots.
Overproduction is one of the seven kinds of wastes in the Lean Manufacturing methodology and refers to the production of goods in excess of what is immediately required by the customer. This type of waste can have a significant impact on the efficiency and profitability of a manufacturing operation, and as a Lean Management Expert, I would like to provide an overview of the negative effects of overproduction.
One of the main negative effects of overproduction is increased inventory costs. When a manufacturer produces more goods than are immediately required by the customer, the excess inventory takes up valuable space in the warehouse and incurs additional costs for storage and handling. This inventory also ties up capital that could be used elsewhere in the business, reducing the overall financial performance of the company.
Another negative effect of overproduction is increased lead time. When a manufacturer produces goods in excess of what is immediately required, the production line may become congested, leading to delays and increased lead time. This can negatively impact customer satisfaction and reduce the competitiveness of the manufacturer.
Overproduction can also lead to increased defects and decreased quality. When a manufacturer produces more goods than are immediately required, the pressure to maintain production speed and volume can lead to shortcuts being taken and decreased attention to detail. This can result in an increase in defects and a decrease in overall product quality, leading to customer complaints and reduced customer loyalty.
Finally, overproduction can contribute to a lack of flexibility and responsiveness. When a manufacturer produces more goods than are immediately required, they may not be able to respond quickly to changes in customer demand, leading to increased lead time and decreased customer satisfaction. This can also result in increased costs due to the need to adjust production processes and manage excess inventory.
In a nutshell, overproduction is a significant waste in the manufacturing process and can have a negative impact on efficiency, profitability, and customer satisfaction. By focusing on reducing overproduction and improving production processes, manufacturers can increase their competitiveness and improve their overall performance. We recommend that manufacturers continuously monitor their production processes and work to reduce overproduction and improve the overall efficiency of their operations
Change Over
Change overs refer to the process of switching a production line from producing one product to producing another.
Change overs refer to the process of switching a production line from producing one product to producing another. This process can have a significant impact on the efficiency and profitability of a manufacturing operation, and as a Lean Management Expert, I would like to provide an overview of change overs and how they can be improved with SMED (Single Minute Exchange of Dies) Workshops.
One of the main challenges with change overs is the time it takes to complete the process. In many cases, change overs can take several hours or even days, which can result in decreased production and increased costs. This can be a significant issue for manufacturers who need to be able to switch between products quickly and efficiently to meet customer demand.
Another challenge with change overs is the potential for mistakes and errors during the process. When a production line is being changed over, there is an increased risk of mistakes being made, such as incorrect parts being installed or procedures being skipped. This can result in decreased production quality, increased defects, and increased lead time.
In order to improve change overs, manufacturers can implement SMED Workshops. SMED Workshops are designed to streamline the change over process and reduce the time it takes to switch between products. This is achieved by identifying and eliminating non-value-added activities, such as time spent waiting for equipment to cool down or procedures that can be done in parallel. By eliminating these activities, SMED Workshops can significantly reduce the time it takes to complete change overs, allowing manufacturers to increase production efficiency and responsiveness.
SMED Workshops also help to reduce the potential for mistakes and errors during change overs by standardizing the process and reducing the number of activities that need to be performed. This can improve overall production quality, reduce defects, and increase customer satisfaction.
In nutshell, change overs can have a significant impact on the efficiency and profitability of a manufacturing operation. By implementing SMED Workshops, manufacturers can streamline the change over process, reduce the time it takes to switch between products, and improve production quality and customer satisfaction. As a Lean Management Expert, I recommend that manufacturers consider implementing SMED Workshops as a means of improving their overall production efficiency and competitiveness.
Stay Connected
Ad
We want information fast and in a nutshell. We from OI recommend Blinkist* - because it’s simply the best.
* = Affiliate Link