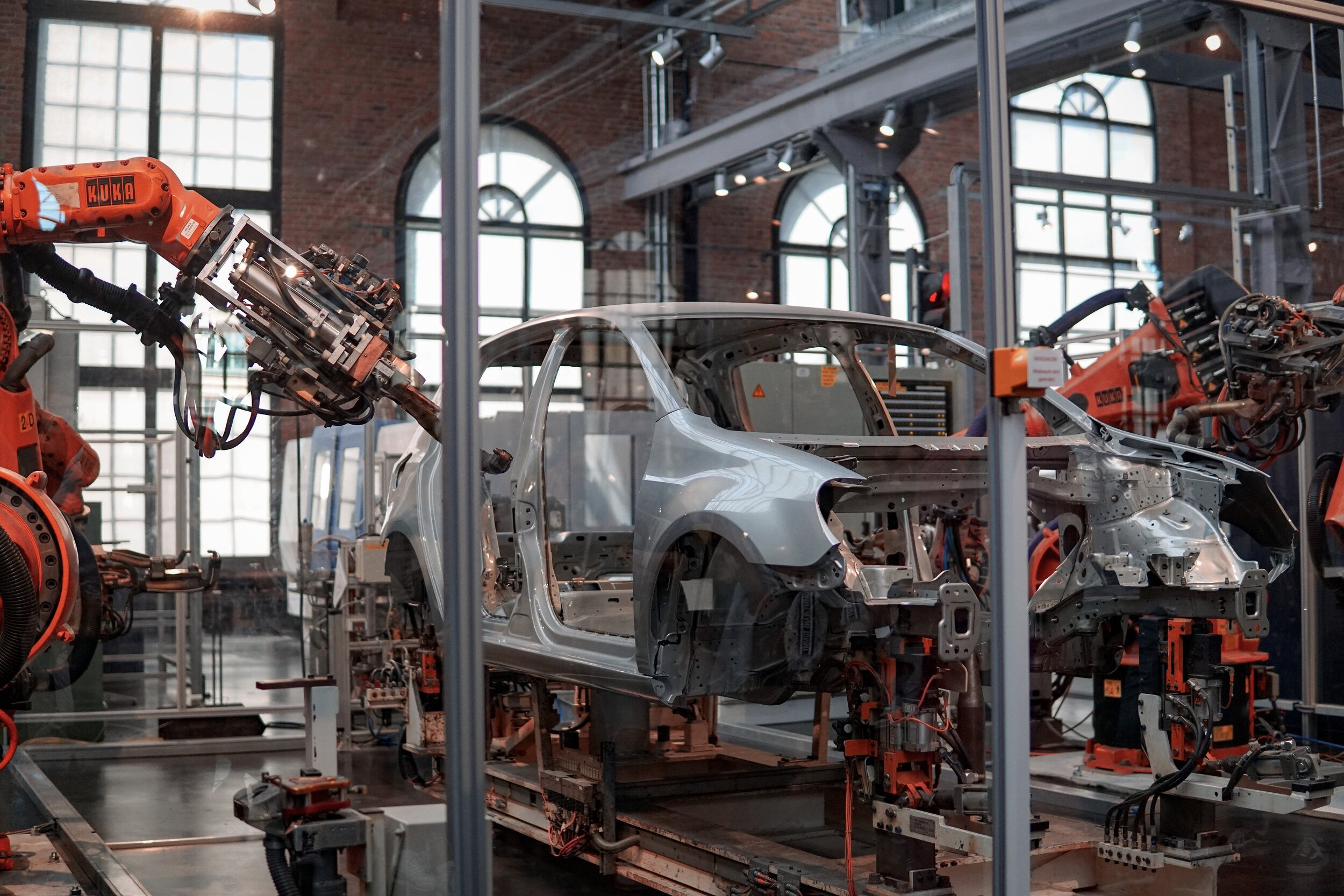
LANGUAGE OF LEAN
Flow Cell
One of the key principles of lean management is the flow cell principle, which is all about optimizing the flow of materials, information, and processes within a manufacturing facility.
Lean management is a production philosophy that seeks to streamline operations and eliminate waste, thereby improving efficiency and reducing costs. One of the key principles of lean management is the flow cell principle, which is all about optimizing the flow of materials, information, and processes within a manufacturing facility.
The flow cell principle is based on the idea that work should be performed in a continuous and uninterrupted flow, without any idle time or unnecessary delays. This principle is critical to achieving lean goals such as reducing lead times, improving quality, and increasing productivity. In order to implement the flow cell principle, a manufacturing facility must first identify and eliminate bottlenecks and constraints in its operations.
The flow cell principle can be applied to a variety of processes within a manufacturing facility, from raw material intake to finished product shipment. For example, in a manufacturing cell, raw materials are moved from one station to another in a continuous flow, without any stops or interruptions. Each station is designed to perform a specific task, and the flow of materials is carefully controlled to ensure that the entire process is as efficient as possible.
The flow cell principle is not just about physical movement of materials, however. It also involves the flow of information, as data must be shared in real-time across different departments and processes in order to optimize flow. A well-designed flow cell system should also include checks and balances to ensure that quality standards are met and that products are being produced to the required specifications.
Another key aspect of the flow cell principle is continuous improvement. Lean management emphasizes the importance of continuous improvement, and the flow cell principle is no exception. By constantly monitoring and analyzing the flow of materials, information, and processes, manufacturing facilities can identify areas for improvement and make the necessary changes to optimize their operations.
In conclusion, the flow cell principle is a critical component of lean management and is essential for achieving lean goals such as reducing lead times, improving quality, and increasing productivity. To fully realize the benefits of the flow cell principle, manufacturing facilities must implement it as part of a comprehensive lean management program, which includes continuous improvement, real-time data sharing, and strict quality control measures.
Just in Sequence - JIS
Just in Sequence (JIS) is a lean manufacturing principle that emphasizes the importance of delivering components to the production line at the exact moment they are needed.
Just in Sequence (JIS) is a lean manufacturing principle that emphasizes the importance of delivering components to the production line at the exact moment they are needed. The goal of JIS is to minimize waste and improve efficiency by avoiding overproduction and reducing the amount of inventory in the production process.
In traditional manufacturing processes, components are often delivered to the production line well in advance of when they are needed, leading to large amounts of inventory and unnecessary waste. With JIS, components are delivered to the production line just in time, reducing the amount of inventory and freeing up valuable storage space.
JIS also helps to minimize the risk of stock obsolescence, as inventory is not kept for long periods of time. In addition, JIS reduces the risk of quality problems and defects, as components are delivered only when they are needed and there is less chance for them to become damaged or lost.
Implementing JIS in a manufacturing facility requires a high level of coordination and communication between suppliers, manufacturers, and logistics providers. A just-in-sequence system should be carefully planned and implemented to ensure that components are delivered exactly when they are needed, without any delays or interruptions.
One of the key components of a successful JIS system is a strong logistics network that can ensure timely and accurate delivery of components. This may involve using advanced technologies such as real-time tracking and data analysis to monitor the delivery of components and identify potential issues before they become problems.
Another critical aspect of JIS is the need for clear and accurate communication between suppliers and manufacturers. This can include the use of automated systems and data sharing to ensure that all parties are aware of the status of deliveries and can take the necessary actions to resolve any issues.
In a nutshell, the Just in Sequence (JIS) principle is an important component of lean manufacturing, as it helps to minimize waste, reduce inventory, and improve efficiency. To fully realize the benefits of JIS, manufacturers must implement it as part of a comprehensive lean manufacturing program that includes strong logistics, clear communication, and the use of advanced technologies. With the right approach, JIS can help manufacturers to achieve significant improvements in their operations, leading to increased competitiveness and profitability.
Stay Connected
Ad
We want information fast and in a nutshell. We from OI recommend Blinkist* - because it’s simply the best.
* = Affiliate Link