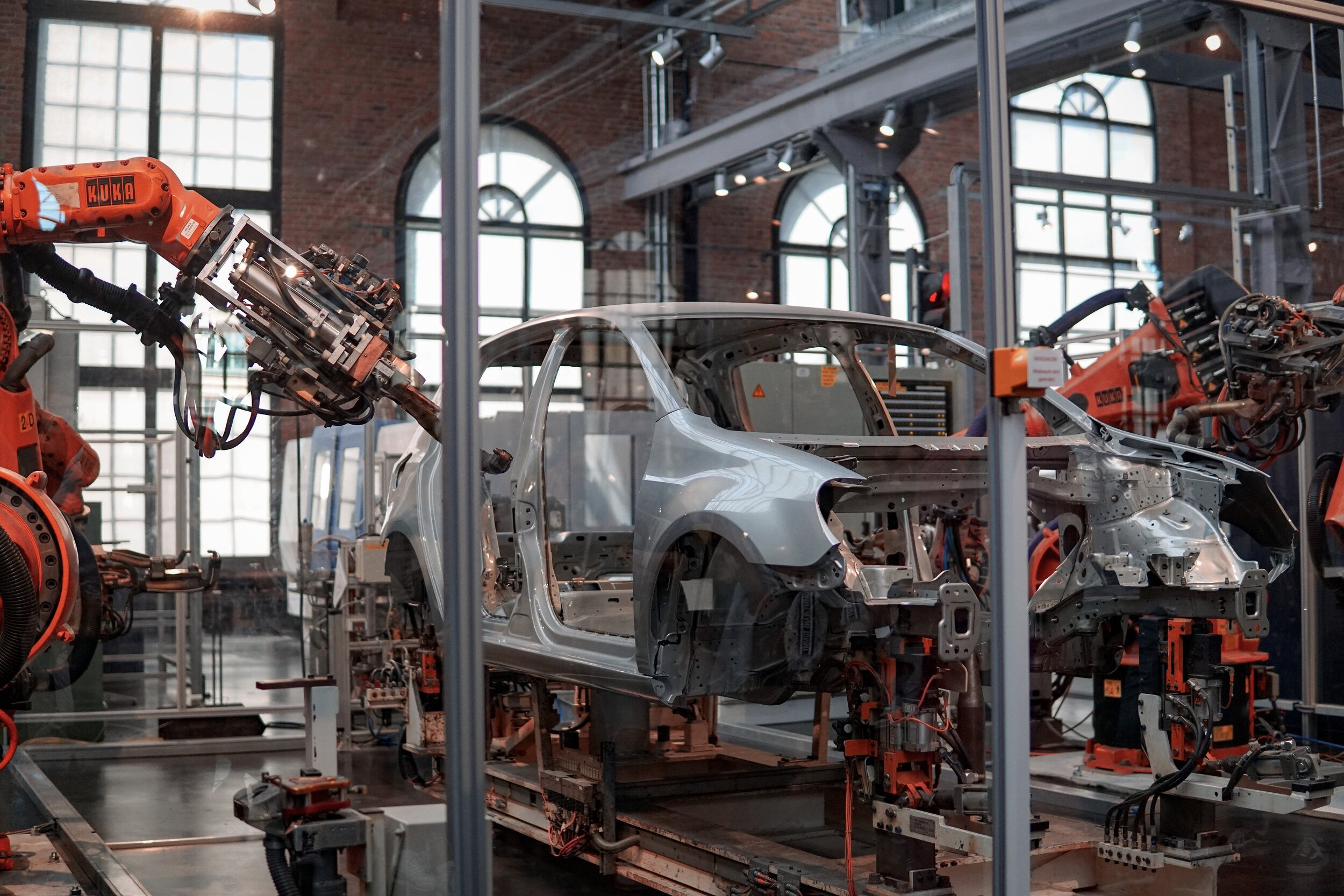
LANGUAGE OF LEAN
Flow Cell
One of the key principles of lean management is the flow cell principle, which is all about optimizing the flow of materials, information, and processes within a manufacturing facility.
Lean management is a production philosophy that seeks to streamline operations and eliminate waste, thereby improving efficiency and reducing costs. One of the key principles of lean management is the flow cell principle, which is all about optimizing the flow of materials, information, and processes within a manufacturing facility.
The flow cell principle is based on the idea that work should be performed in a continuous and uninterrupted flow, without any idle time or unnecessary delays. This principle is critical to achieving lean goals such as reducing lead times, improving quality, and increasing productivity. In order to implement the flow cell principle, a manufacturing facility must first identify and eliminate bottlenecks and constraints in its operations.
The flow cell principle can be applied to a variety of processes within a manufacturing facility, from raw material intake to finished product shipment. For example, in a manufacturing cell, raw materials are moved from one station to another in a continuous flow, without any stops or interruptions. Each station is designed to perform a specific task, and the flow of materials is carefully controlled to ensure that the entire process is as efficient as possible.
The flow cell principle is not just about physical movement of materials, however. It also involves the flow of information, as data must be shared in real-time across different departments and processes in order to optimize flow. A well-designed flow cell system should also include checks and balances to ensure that quality standards are met and that products are being produced to the required specifications.
Another key aspect of the flow cell principle is continuous improvement. Lean management emphasizes the importance of continuous improvement, and the flow cell principle is no exception. By constantly monitoring and analyzing the flow of materials, information, and processes, manufacturing facilities can identify areas for improvement and make the necessary changes to optimize their operations.
In conclusion, the flow cell principle is a critical component of lean management and is essential for achieving lean goals such as reducing lead times, improving quality, and increasing productivity. To fully realize the benefits of the flow cell principle, manufacturing facilities must implement it as part of a comprehensive lean management program, which includes continuous improvement, real-time data sharing, and strict quality control measures.
Change Over
Change overs refer to the process of switching a production line from producing one product to producing another.
Change overs refer to the process of switching a production line from producing one product to producing another. This process can have a significant impact on the efficiency and profitability of a manufacturing operation, and as a Lean Management Expert, I would like to provide an overview of change overs and how they can be improved with SMED (Single Minute Exchange of Dies) Workshops.
One of the main challenges with change overs is the time it takes to complete the process. In many cases, change overs can take several hours or even days, which can result in decreased production and increased costs. This can be a significant issue for manufacturers who need to be able to switch between products quickly and efficiently to meet customer demand.
Another challenge with change overs is the potential for mistakes and errors during the process. When a production line is being changed over, there is an increased risk of mistakes being made, such as incorrect parts being installed or procedures being skipped. This can result in decreased production quality, increased defects, and increased lead time.
In order to improve change overs, manufacturers can implement SMED Workshops. SMED Workshops are designed to streamline the change over process and reduce the time it takes to switch between products. This is achieved by identifying and eliminating non-value-added activities, such as time spent waiting for equipment to cool down or procedures that can be done in parallel. By eliminating these activities, SMED Workshops can significantly reduce the time it takes to complete change overs, allowing manufacturers to increase production efficiency and responsiveness.
SMED Workshops also help to reduce the potential for mistakes and errors during change overs by standardizing the process and reducing the number of activities that need to be performed. This can improve overall production quality, reduce defects, and increase customer satisfaction.
In nutshell, change overs can have a significant impact on the efficiency and profitability of a manufacturing operation. By implementing SMED Workshops, manufacturers can streamline the change over process, reduce the time it takes to switch between products, and improve production quality and customer satisfaction. As a Lean Management Expert, I recommend that manufacturers consider implementing SMED Workshops as a means of improving their overall production efficiency and competitiveness.
Stay Connected
Ad
We want information fast and in a nutshell. We from OI recommend Blinkist* - because it’s simply the best.
* = Affiliate Link