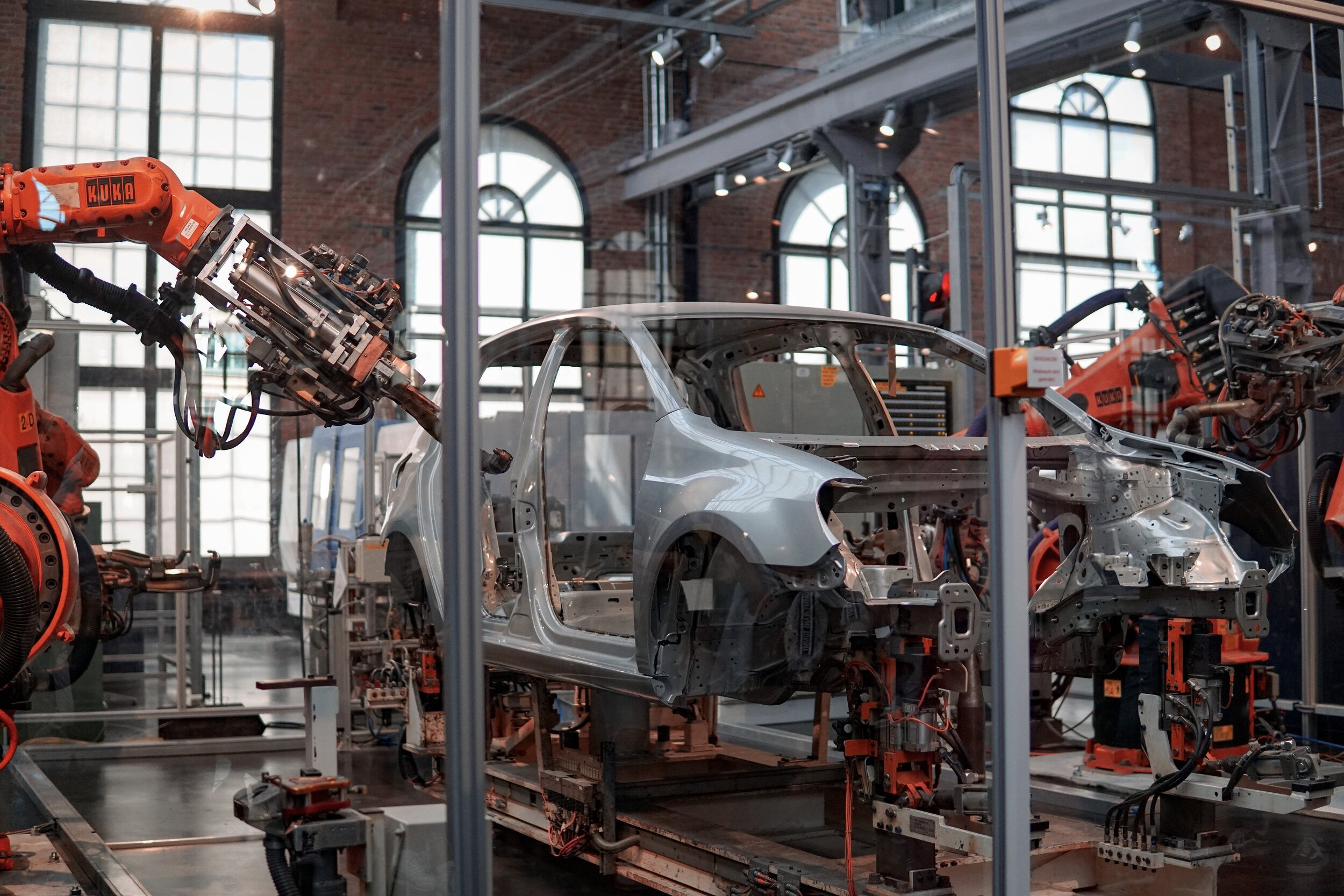
LANGUAGE OF LEAN
Internal Setup
Internal Setup, also known as Machine Changeover or Equipment Changeover, is a critical aspect of Lean Manufacturing. It refers to the process of switching a production machine from one product or production run to another.
Internal Setup, also known as Machine Changeover or Equipment Changeover, is a critical aspect of Lean Manufacturing. It refers to the process of switching a production machine from one product or production run to another. This process can be time-consuming and impact the overall efficiency of a manufacturing plant. For this reason, Lean experts have developed techniques to optimize the Internal Setup process and minimize downtime.
The Internal Setup process can be seen as a non-value-adding (NVA) activity. NVA activities are those that do not directly contribute to the production of a good or service. In the case of Internal Setup, it is necessary but does not add any value to the final product. The goal of Lean is to minimize NVA activities, and the Internal Setup process is no exception.
One of the key strategies for optimizing Internal Setup is to standardize the process. This can be achieved by creating detailed Standard Operating Procedures (SOPs) that outline each step of the setup process. SOPs should include clear instructions, diagrams, and photos to help guide employees through the process. The SOPs should also be reviewed and updated regularly to ensure they are up-to-date and accurate.
In addition to standardizing the process, Lean experts also focus on reducing the time required for Internal Setup. This can be achieved through a combination of reducing the number of steps required and streamlining the process. For example, the use of Quick Changeover fixtures or tools can reduce the time required to changeover a machine. Other strategies include minimizing the number of tools required, using visual aids to guide employees through the process, and using checklists to ensure all steps are completed.
Another important aspect of optimizing Internal Setup is employee engagement and involvement. Lean experts believe that employees who are involved in the process are more likely to take ownership of the process and be more committed to making it as efficient as possible. Encouraging employees to identify areas for improvement and participate in Kaizen events can also help drive continuous improvement.
Finally, it is important to monitor and evaluate the Internal Setup process on a regular basis. This can be done by tracking key performance indicators (KPIs) such as changeover time, number of changeovers, and machine downtime. The KPIs can be used to identify areas for improvement and measure the success of continuous improvement initiatives.
In a nutshell, Internal Setup is a critical aspect of Lean Manufacturing and Operational Excellence. To optimize the process and minimize downtime, Lean experts focus on standardizing the process, reducing the time required, involving employees, and monitoring and evaluating the process. By following these principles, manufacturers can achieve a more efficient and streamlined Internal Setup process, resulting in increased productivity, reduced waste, and improved bottom-line results.
Flow Cell
One of the key principles of lean management is the flow cell principle, which is all about optimizing the flow of materials, information, and processes within a manufacturing facility.
Lean management is a production philosophy that seeks to streamline operations and eliminate waste, thereby improving efficiency and reducing costs. One of the key principles of lean management is the flow cell principle, which is all about optimizing the flow of materials, information, and processes within a manufacturing facility.
The flow cell principle is based on the idea that work should be performed in a continuous and uninterrupted flow, without any idle time or unnecessary delays. This principle is critical to achieving lean goals such as reducing lead times, improving quality, and increasing productivity. In order to implement the flow cell principle, a manufacturing facility must first identify and eliminate bottlenecks and constraints in its operations.
The flow cell principle can be applied to a variety of processes within a manufacturing facility, from raw material intake to finished product shipment. For example, in a manufacturing cell, raw materials are moved from one station to another in a continuous flow, without any stops or interruptions. Each station is designed to perform a specific task, and the flow of materials is carefully controlled to ensure that the entire process is as efficient as possible.
The flow cell principle is not just about physical movement of materials, however. It also involves the flow of information, as data must be shared in real-time across different departments and processes in order to optimize flow. A well-designed flow cell system should also include checks and balances to ensure that quality standards are met and that products are being produced to the required specifications.
Another key aspect of the flow cell principle is continuous improvement. Lean management emphasizes the importance of continuous improvement, and the flow cell principle is no exception. By constantly monitoring and analyzing the flow of materials, information, and processes, manufacturing facilities can identify areas for improvement and make the necessary changes to optimize their operations.
In conclusion, the flow cell principle is a critical component of lean management and is essential for achieving lean goals such as reducing lead times, improving quality, and increasing productivity. To fully realize the benefits of the flow cell principle, manufacturing facilities must implement it as part of a comprehensive lean management program, which includes continuous improvement, real-time data sharing, and strict quality control measures.
Inventory
Inventory is often viewed as a necessary evil, as it provides a safety net to ensure that products are available to meet customer demand.
Inventory is often viewed as a necessary evil, as it provides a safety net to ensure that products are available to meet customer demand. However, from the perspective of Lean Management, inventory can also be seen as a type of waste.
In Lean, waste is defined as anything that does not add value to the customer. From this perspective, inventory can be considered waste because it ties up valuable resources such as space, money, and time without providing any immediate value to the customer. This is because inventory requires storage, which takes up valuable space, and also requires investment in the products themselves. In addition, inventory can lead to obsolescence, as products may become outdated or go out of fashion before they can be sold. Furthermore, inventory can lead to inefficiencies in the supply chain, as products may sit on shelves for extended periods of time before they are sold, adding unnecessary time to the overall lead time.
Despite these challenges, inventory is also an essential component of most businesses. Inventory provides a safety net, ensuring that there are products available to meet customer demand even when there are disruptions in the supply chain. It also allows businesses to take advantage of bulk purchasing discounts, and to manage seasonal variations in demand.
So, how can Lean Management help businesses to steer inventory in the best direction? There are several key steps that can be taken to minimize the waste associated with inventory while still ensuring that the business has the products it needs to meet customer demand.
The first step is to implement a Lean production system. This involves using the principles of Lean Management to streamline production processes and reduce waste in all areas of the business, including inventory management. By reducing waste in the production process, it is possible to minimize the amount of inventory that is required, freeing up valuable resources for other areas of the business.
The second step is to implement a pull-based production system. This involves using customer demand as the driving force behind production, rather than using forecasted demand to determine production schedules. This can help to minimize inventory waste by ensuring that products are only produced when there is a genuine demand for them.
The third step is to implement just-in-time (JIT) inventory management. JIT is a Lean approach to inventory management that involves only ordering the products that are required to meet customer demand, and no more. This can help to minimize inventory waste by reducing the amount of product that is held in reserve, freeing up valuable resources such as space and money.
The fourth step is to implement a continuous improvement program. This involves regularly reviewing inventory levels and processes, and making changes where necessary to reduce waste and increase efficiency. This can help to ensure that inventory management processes are constantly evolving, and that the business is always adapting to changing customer demand.
In a nutshell, inventory management is an important aspect of any business, as it helps to ensure that the right products are available at the right time to meet customer demand. However, from the perspective of Lean Management, inventory can also be seen as a type of waste. By implementing a Lean production system, a pull-based production system, JIT inventory management, and a continuous improvement program, businesses can minimize the waste associated with inventory while still ensuring that they have the products they need to meet customer demand. By adopting these principles, businesses can increase efficiency, reduce costs, and improve overall customer satisfaction.
Standard Work
Standard work is a fundamental principle of Lean manufacturing, a management philosophy that focuses on the elimination of waste and the continuous improvement of processes in order to increase efficiency, quality, and customer satisfaction.
Standard work is a fundamental principle of Lean manufacturing, a management philosophy that focuses on the elimination of waste and the continuous improvement of processes in order to increase efficiency, quality, and customer satisfaction. From the perspective of a Lean management expert, standard work is an essential tool for achieving operational excellence in the manufacturing industry.
Standard work refers to the detailed documentation of the best way to perform a specific task, taking into account factors such as the skills and experience of the workers, the equipment and materials used, and the desired outcome. This documentation should include step-by-step instructions, visual aids, and clear specifications for each step of the process. The goal of standard work is to ensure that each task is performed consistently and to the highest standard possible, regardless of who is performing it or when it is performed.
There are several key benefits to implementing standard work in manufacturing. Firstly, standard work helps to increase efficiency by eliminating waste and reducing variability in the production process. This leads to shorter lead times, lower costs, and improved quality. Secondly, standard work provides a clear understanding of the expected outcome of each task, making it easier for workers to know what is expected of them and to continuously improve their performance. Thirdly, standard work helps to promote a culture of continuous improvement by empowering workers to identify opportunities for improvement and to suggest changes to the standard work documentation.
To implement standard work effectively, Lean management experts typically follow a five-step process:
Define the task: Clearly define what needs to be accomplished and what the desired outcome is.
Observe and document the current process: Observe the current process, and document each step, including the time taken for each step and any variation in the process.
Determine the standard work: Analyze the data from the observation and determine the best way to perform the task, taking into account the skills and experience of the workers, the equipment and materials used, and the desired outcome.
Train the workers: Train the workers on the standard work and ensure that they understand the expectations and how to perform the task to the standard.
Continuously improve: Regularly review the standard work and identify opportunities for improvement.
In addition to the five-step process, Lean management experts also recommend the following ten tips for a successful implementation of standard work:
Start with a few simple tasks and gradually expand the implementation to other areas of the organization.
Engage the workers in the implementation process and involve them in the development of the standard work.
Focus on standardizing the process, not the workers.
Use visual aids, such as flow charts, to help the workers understand the standard work.
Regularly review and update the standard work to reflect changes in the process, the workers, or the equipment.
Foster a culture of continuous improvement by encouraging workers to suggest changes to the standard work.
Make standard work a part of the performance evaluation process for workers.
Use standard work as a tool for training new workers.
Use standard work to identify opportunities for process improvement.
Regularly communicate the importance of standard work and the benefits of implementing it.
In a nutshell, standard work is a powerful tool for achieving operational excellence in the manufacturing industry. From the perspective of a Lean management expert, standard work helps to increase efficiency, improve quality, and empower workers to continuously improve their performance. By following the five-step process and the ten tips for a successful implementation, organizations can reap the benefits of standard work and achieve their operational excellence goals.
Regular Communication
Regular communication refers to the continuous exchange of information between different departments and individuals within an organization.
Regular communication refers to the continuous exchange of information between different departments and individuals within an organization. The aim of this communication is to ensure that everyone is on the same page, working towards the same goals, and that any problems or obstacles are addressed promptly. In this article, we will explore the positives aspects of using regular communication in manufacturing and how it supports shop floor management in three steps.
Improves Collaboration and Cooperation
Regular communication plays an important role in improving collaboration and cooperation within an organization. When everyone is kept informed about the latest developments, it becomes easier for employees to work together effectively. They can share ideas and best practices, identify areas for improvement, and help each other overcome challenges. As a result, teamwork becomes more efficient, and everyone is able to contribute to the success of the organization.
Facilitates Problem Solving
Problems and obstacles are a natural part of any manufacturing process. However, if they are not addressed promptly, they can quickly escalate into bigger issues. Regular communication helps to ensure that problems are identified and addressed in a timely manner. When employees are able to openly communicate with each other, they can work together to find solutions and prevent problems from getting worse. This helps to minimize the impact of any issues on production and ensures that the organization is able to maintain its competitiveness.
Supports Shop Floor Management
Regular communication is also an important aspect of shop floor management. Shop floor management refers to the process of managing the day-to-day operations of a manufacturing facility. Regular communication helps to ensure that everyone is aware of their responsibilities and is able to perform their duties effectively. It also helps to identify areas for improvement and makes it easier for managers to provide feedback and guidance. In addition, regular communication helps to create a culture of continuous improvement, where everyone is encouraged to take an active role in driving progress and improving performance.
In a nutshell, regular communication is a crucial aspect of Lean management in manufacturing. It plays an important role in improving collaboration and cooperation, facilitating problem solving, and supporting shop floor management. By incorporating regular communication into their operations, organizations can ensure that everyone is working together effectively, that problems are addressed promptly, and that the organization is able to maintain its competitiveness.
Kaikaku
Kaikaku first creates the basics to later carry the Kaizen idea into manual production with CIP.
KAIKAKU, which means "radical change" or "revolution" in Japanese, is a key concept in Lean management and operational excellence. It refers to a transformative approach to process improvement that aims to achieve significant and lasting improvements in performance. KAIKAKU is different from other process improvement methods, such as Kaizen, which focus on incremental improvements, KAIKAKU is characterized by a bold, dramatic change in the way a process is performed.
One of the key features of KAIKAKU is that it is not just about improving the existing process, but also about rethinking and redesigning the process from scratch. This approach allows organizations to identify and eliminate sources of waste, inefficiencies, and bottlenecks that may have been present in the process for years. By starting with a blank slate, organizations can create a new process that is more efficient, effective, and sustainable.
KAIKAKU is often used in manufacturing and production processes, where significant improvements in performance can have a major impact on the bottom line. For example, a manufacturing facility might use KAIKAKU to redesign its production process, eliminating bottlenecks, reducing waste, and increasing capacity. This could result in faster turnaround times, higher quality products, and lower costs.
Another key feature of KAIKAKU is that it often involves the use of new technologies and automation. By adopting new technologies and automating processes, organizations can achieve significant improvements in performance. For example, a manufacturing facility might use KAIKAKU to introduce robots, automated inspection systems, or artificial intelligence to its production process. This could result in faster turnaround times, higher quality products, and lower costs.
KAIKAKU also involves the active participation of employees, especially those who are directly involved in the process. By involving employees in the process improvement process, organizations can tap into their expertise and knowledge, and create a sense of ownership and engagement. Employees can also bring valuable insights into the process and suggest new ideas for improvement.
KAIKAKU is also closely linked to the concept of "Just-in-Time" (JIT) manufacturing. JIT is a production strategy that aims to produce the right products at the right time, and in the right quantities, by minimizing waste and unnecessary inventory. By implementing KAIKAKU, organizations can achieve significant improvements in performance and implement JIT successfully.
In a nutshell, KAIKAKU is a powerful method for organizations that are committed to operational excellence and continuous improvement. By rethinking and redesigning the process from scratch, organizations can identify and eliminate sources of waste, inefficiencies, and bottlenecks that may have been present in the process for years. By adopting new technologies and automating processes, organizations can achieve significant improvements in performance. By involving employees in the process improvement process, organizations can tap into their expertise and knowledge. By implementing KAIKAKU, organizations can achieve significant improvements in performance and implement JIT successfully.
KOSU
KOSU, short for "Key Operating System Units", is a method used in Lean management and operational excellence to identify and measure the critical units of a process that are essential for the overall performance and success of the operation.
KOSU, short for "Key Operating System Units", is a method used in Lean management and operational excellence to identify and measure the critical units of a process that are essential for the overall performance and success of the operation. By identifying these key units, organizations can focus their improvement efforts on the areas that will have the greatest impact on performance.
The basic idea behind KOSU is to identify the critical units of a process that are essential for the overall performance and success of the operation. This can include things like machines, equipment, personnel, and processes. By identifying these key units, organizations can focus their improvement efforts on the areas that will have the greatest impact on performance.
One of the key benefits of using KOSU is that it helps organizations to identify and prioritize the areas of the process that are most critical to performance. By identifying the key units of a process, organizations can focus their improvement efforts on those areas that will have the greatest impact on performance. This allows them to make the most of their resources and achieve the greatest return on investment.
Another benefit of using KOSU is that it helps organizations to identify and eliminate bottlenecks in the process. By identifying the key units of a process, organizations can identify which units are causing delays and bottlenecks in the process, and then take action to eliminate those bottlenecks. This can include things like improving machine maintenance, optimizing production processes, or identifying areas where automation can be used to improve efficiency.
Using KOSU also helps organizations to identify areas where standardization can be used to improve a process. By identifying the key units of a process, organizations can identify which units are taking longer than they should, and then take action to standardize those processes. This can include things like implementing best practices, developing standard operating procedures, or identifying areas where automation can be used to improve efficiency.
In addition, KOSU can be used to identify areas where automation can be used to improve efficiency. By identifying the key units of a process, organizations can identify which units are taking longer than they should, and then take action to automate those processes. This can include things like using robotics, using automated inspection systems, or using artificial intelligence to optimize production processes.
KOSU also plays a critical role in analyzing machine’s capacity. By identifying the key units of a process, organizations can identify which units are operating at full capacity, and which ones have room for improvement. This can help organizations to optimize their production processes, and ultimately, increase their overall production capacity.
In a nutshell, KOSU is a powerful method for organizations that are committed to operational excellence and continuous improvement. By identifying the key units of a process, organizations can focus their improvement efforts on the areas that will have the greatest impact on performance, eliminate bottlenecks in the process, use standardization to improve a process, use automation to improve efficiency and increase their overall production capacity.
Standard Layout
A standard layout is a detailed, visual representation of the ideal workflow and arrangement of resources in a given area.
Standard Layout: The Key to Unlocking Efficiency in Lean Management
Standardization is one of the fundamental principles of lean management, and it's no surprise that it's also one of the most effective ways to improve efficiency and reduce waste in your operations. One of the most powerful tools in the standardization toolbox is the standard layout, also known as "taikyō-sei" in Japanese.
A standard layout is a detailed, visual representation of the ideal workflow and arrangement of resources in a given area. This can include anything from the placement of tools and equipment to the flow of materials and the location of workstations. The goal is to create a clear and consistent way of working that minimizes waste, maximizes efficiency, and makes it easy for everyone on the team to understand and follow.
One of the most important benefits of a standard layout is that it makes it much easier to identify and eliminate sources of waste and inefficiency. By clearly defining the ideal way of working, it becomes much easier to see where things are going wrong and to make adjustments as needed. This can include anything from adjusting the location of workstations to the flow of materials, to the type and size of tools and equipment.
Another key benefit of a standard layout is that it makes it much easier to train new employees and to ensure that everyone is following the same processes. When everyone is working in the same way, it becomes much easier to share knowledge and best practices, which can help to improve the overall performance of the team.
Finally, a standard layout can also be a powerful tool for continuous improvement. By clearly defining the ideal way of working, it becomes much easier to measure performance and to identify areas for improvement. This can include anything from adjusting the flow of materials to the location of workstations, to the type and size of tools and equipment.
So, how do you go about creating a standard layout? The first step is to conduct a thorough analysis of your current operations. This should include a detailed study of the flow of materials, the location of workstations, and the type and size of tools and equipment. You should also pay close attention to the flow of people and information, as this can have a big impact on overall efficiency.
Once you have a good understanding of your current operations, you can then begin to create a detailed, visual representation of the ideal workflow and arrangement of resources. This should include everything from the placement of tools and equipment to the flow of materials and the location of workstations.
It's also important to involve your entire team in the process of creating a standard layout. This will help to ensure that everyone is on board with the changes and that everyone understands the benefits of standardization.
Once you have a standard layout in place, it's important to monitor and measure its effectiveness on a regular basis. This can include anything from tracking the flow of materials to the location of workstations, to the type and size of tools and equipment. It's also important to involve your entire team in the process of monitoring and measuring performance, as this will help to ensure that everyone is committed to continuous improvement.
In conclusion, a standard layout is a powerful tool for unlocking efficiency in lean management. By clearly defining the ideal way of working, it becomes much easier to see where things are going wrong and to make adjustments as needed. This can include anything from adjusting the flow of materials to the location of workstations, to the type and size of tools and equipment. Furthermore, it is a powerful tool for training, knowledge sharing, and continuous improvement. If you're looking to improve efficiency and reduce waste in your operations, a standard layout is definitely worth considering.
Stay Connected
Ad
We want information fast and in a nutshell. We from OI recommend Blinkist* - because it’s simply the best.
* = Affiliate Link