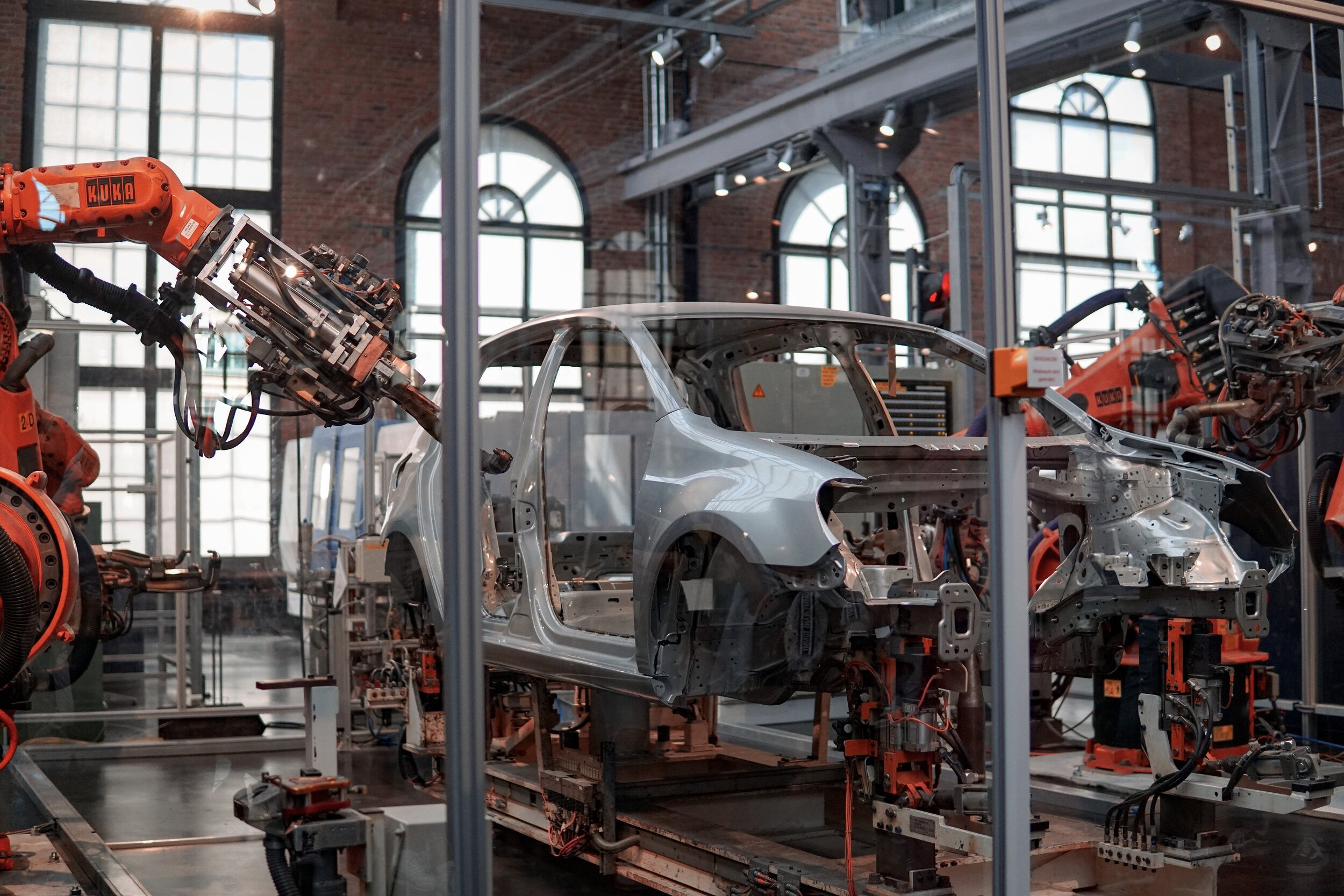
LANGUAGE OF LEAN
Just in Sequence - JIS
Just in Sequence (JIS) is a lean manufacturing principle that emphasizes the importance of delivering components to the production line at the exact moment they are needed.
Just in Sequence (JIS) is a lean manufacturing principle that emphasizes the importance of delivering components to the production line at the exact moment they are needed. The goal of JIS is to minimize waste and improve efficiency by avoiding overproduction and reducing the amount of inventory in the production process.
In traditional manufacturing processes, components are often delivered to the production line well in advance of when they are needed, leading to large amounts of inventory and unnecessary waste. With JIS, components are delivered to the production line just in time, reducing the amount of inventory and freeing up valuable storage space.
JIS also helps to minimize the risk of stock obsolescence, as inventory is not kept for long periods of time. In addition, JIS reduces the risk of quality problems and defects, as components are delivered only when they are needed and there is less chance for them to become damaged or lost.
Implementing JIS in a manufacturing facility requires a high level of coordination and communication between suppliers, manufacturers, and logistics providers. A just-in-sequence system should be carefully planned and implemented to ensure that components are delivered exactly when they are needed, without any delays or interruptions.
One of the key components of a successful JIS system is a strong logistics network that can ensure timely and accurate delivery of components. This may involve using advanced technologies such as real-time tracking and data analysis to monitor the delivery of components and identify potential issues before they become problems.
Another critical aspect of JIS is the need for clear and accurate communication between suppliers and manufacturers. This can include the use of automated systems and data sharing to ensure that all parties are aware of the status of deliveries and can take the necessary actions to resolve any issues.
In a nutshell, the Just in Sequence (JIS) principle is an important component of lean manufacturing, as it helps to minimize waste, reduce inventory, and improve efficiency. To fully realize the benefits of JIS, manufacturers must implement it as part of a comprehensive lean manufacturing program that includes strong logistics, clear communication, and the use of advanced technologies. With the right approach, JIS can help manufacturers to achieve significant improvements in their operations, leading to increased competitiveness and profitability.
Standardization
Standardization is a vital aspect of a successful lean management strategy and can be defined as the process of establishing and maintaining common procedures and processes throughout the manufacturing organization.
Standardization is a key principle in lean manufacturing, which is focused on maximizing efficiency, minimizing waste, and continuously improving processes. It is a vital aspect of a successful lean management strategy and can be defined as the process of establishing and maintaining common procedures and processes throughout the manufacturing organization. This principle is based on the idea that standardization leads to improved productivity and a higher level of consistency in the production process.
A lean manufacturing expert knows the importance of standardization, as it helps to reduce variation and streamline processes, resulting in increased efficiency and improved quality. This is because standardization helps to eliminate inefficiencies, errors, and inconsistencies in the production process, allowing employees to focus on the tasks that are most important. This in turn leads to improved cycle times, reduced lead times, and increased customer satisfaction.
Standardization also helps to eliminate confusion and misunderstandings, as all employees are following the same procedures and processes. This makes it easier for employees to work together, as everyone is working from the same set of guidelines. This also makes it easier for management to train new employees, as they can be taught the standard procedures from the outset.
Standardization also helps to facilitate continuous improvement. By standardizing processes, it is easier to identify areas where improvement is needed, and changes can be made more easily. This is because employees are all working from the same set of guidelines, making it easier to see where improvements can be made and implement changes.
In order to effectively implement standardization in manufacturing, a Lean Management Expert would typically follow three steps:
Process Mapping: The first step is to map out the processes and procedures used in the manufacturing organization. This helps to identify areas where standardization can be implemented, and where improvements can be made.
Standardization: The second step is to develop and implement standardized procedures and processes. This involves working with employees to ensure that everyone is following the same procedures, and that they are understood by all.
Continuous Improvement: The final step is to continuously monitor and improve the standardization process. This involves regularly reviewing the procedures and processes to identify areas for improvement, and making changes as necessary to ensure that the standardization process remains effective.
In a nutshell, standardization is a key principle in lean manufacturing, and is essential for maximizing efficiency, minimizing waste, and continuously improving processes. By following the three steps outlined above, a Lean Management Expert can effectively implement standardization in their organization, leading to improved productivity, higher levels of consistency, and increased customer satisfaction.
Audit
Audits are a critical component of any lean manufacturing program, as they provide a structured and systematic approach for evaluating the effectiveness of the processes and procedures in place.
Audits are a critical component of any lean manufacturing program, as they provide a structured and systematic approach for evaluating the effectiveness of the processes and procedures in place. Audits help to identify areas for improvement, track progress, and ensure that best practices are being followed.
We would like to outline the 5 steps in order to prepare and conduct a successful audit in a manufacturing setting. These steps are as follows:
Define the audit scope: Determine what areas of the manufacturing process will be evaluated during the audit. This may include areas such as production line processes, inventory management, and quality control procedures.
Gather data: Collect relevant data and information that will be used during the audit. This may include data on production volumes, inventory levels, and quality control data.
Prepare audit checklists: Develop a detailed set of checklists that will be used to evaluate the different areas of the manufacturing process. These checklists should be comprehensive and include questions about process flow, standard operating procedures, and key performance indicators.
Conduct the audit: Conduct the audit using the checklists developed in step 3. This should be done by a team of experts who have a thorough understanding of the manufacturing process and best practices.
Analyze the results: After the audit is complete, analyze the results to identify areas for improvement. This may include the development of action plans to address any areas of weakness or non-compliance.
In order to ensure a successful audit, it is important to follow a set of best practices. Here are 10 tips for a successful audit in a manufacturing setting:
Be well-prepared: Ensure that you have a thorough understanding of the manufacturing process and the areas that will be evaluated during the audit.
Use a team approach: Conduct the audit as a team to ensure that all areas are thoroughly evaluated and that all perspectives are taken into account.
Follow a structured approach: Use a structured approach and follow the audit checklists developed in step 3 to ensure a consistent and systematic evaluation of the manufacturing process.
Be objective: Maintain objectivity throughout the audit and avoid making assumptions about the manufacturing process or the results.
Focus on best practices: Evaluate the manufacturing process against best practices and ensure that these are being followed.
Be open-minded: Be open-minded and willing to consider alternative approaches and new ideas for improvement.
Be transparent: Be transparent about the audit process and the results, and communicate openly with all stakeholders.
Follow-up on action plans: Ensure that action plans are developed to address any areas of weakness or non-compliance identified during the audit.
Continuously monitor progress: Continuously monitor progress and track progress against the action plans to ensure that improvements are being made.
Encourage continuous improvement: Encourage continuous improvement and encourage all stakeholders to be involved in the audit process and to contribute to the improvement of the manufacturing process.
In a nutshell, audits are an essential component of a successful lean manufacturing program. By following the 5 steps and the 10 tips outlined above, manufacturers can ensure that they are conducting effective and successful audits that lead to continuous improvement and enhanced competitiveness.
Kaikaku
Kaikaku first creates the basics to later carry the Kaizen idea into manual production with CIP.
KAIKAKU, which means "radical change" or "revolution" in Japanese, is a key concept in Lean management and operational excellence. It refers to a transformative approach to process improvement that aims to achieve significant and lasting improvements in performance. KAIKAKU is different from other process improvement methods, such as Kaizen, which focus on incremental improvements, KAIKAKU is characterized by a bold, dramatic change in the way a process is performed.
One of the key features of KAIKAKU is that it is not just about improving the existing process, but also about rethinking and redesigning the process from scratch. This approach allows organizations to identify and eliminate sources of waste, inefficiencies, and bottlenecks that may have been present in the process for years. By starting with a blank slate, organizations can create a new process that is more efficient, effective, and sustainable.
KAIKAKU is often used in manufacturing and production processes, where significant improvements in performance can have a major impact on the bottom line. For example, a manufacturing facility might use KAIKAKU to redesign its production process, eliminating bottlenecks, reducing waste, and increasing capacity. This could result in faster turnaround times, higher quality products, and lower costs.
Another key feature of KAIKAKU is that it often involves the use of new technologies and automation. By adopting new technologies and automating processes, organizations can achieve significant improvements in performance. For example, a manufacturing facility might use KAIKAKU to introduce robots, automated inspection systems, or artificial intelligence to its production process. This could result in faster turnaround times, higher quality products, and lower costs.
KAIKAKU also involves the active participation of employees, especially those who are directly involved in the process. By involving employees in the process improvement process, organizations can tap into their expertise and knowledge, and create a sense of ownership and engagement. Employees can also bring valuable insights into the process and suggest new ideas for improvement.
KAIKAKU is also closely linked to the concept of "Just-in-Time" (JIT) manufacturing. JIT is a production strategy that aims to produce the right products at the right time, and in the right quantities, by minimizing waste and unnecessary inventory. By implementing KAIKAKU, organizations can achieve significant improvements in performance and implement JIT successfully.
In a nutshell, KAIKAKU is a powerful method for organizations that are committed to operational excellence and continuous improvement. By rethinking and redesigning the process from scratch, organizations can identify and eliminate sources of waste, inefficiencies, and bottlenecks that may have been present in the process for years. By adopting new technologies and automating processes, organizations can achieve significant improvements in performance. By involving employees in the process improvement process, organizations can tap into their expertise and knowledge. By implementing KAIKAKU, organizations can achieve significant improvements in performance and implement JIT successfully.
Standard Layout
A standard layout is a detailed, visual representation of the ideal workflow and arrangement of resources in a given area.
Standard Layout: The Key to Unlocking Efficiency in Lean Management
Standardization is one of the fundamental principles of lean management, and it's no surprise that it's also one of the most effective ways to improve efficiency and reduce waste in your operations. One of the most powerful tools in the standardization toolbox is the standard layout, also known as "taikyō-sei" in Japanese.
A standard layout is a detailed, visual representation of the ideal workflow and arrangement of resources in a given area. This can include anything from the placement of tools and equipment to the flow of materials and the location of workstations. The goal is to create a clear and consistent way of working that minimizes waste, maximizes efficiency, and makes it easy for everyone on the team to understand and follow.
One of the most important benefits of a standard layout is that it makes it much easier to identify and eliminate sources of waste and inefficiency. By clearly defining the ideal way of working, it becomes much easier to see where things are going wrong and to make adjustments as needed. This can include anything from adjusting the location of workstations to the flow of materials, to the type and size of tools and equipment.
Another key benefit of a standard layout is that it makes it much easier to train new employees and to ensure that everyone is following the same processes. When everyone is working in the same way, it becomes much easier to share knowledge and best practices, which can help to improve the overall performance of the team.
Finally, a standard layout can also be a powerful tool for continuous improvement. By clearly defining the ideal way of working, it becomes much easier to measure performance and to identify areas for improvement. This can include anything from adjusting the flow of materials to the location of workstations, to the type and size of tools and equipment.
So, how do you go about creating a standard layout? The first step is to conduct a thorough analysis of your current operations. This should include a detailed study of the flow of materials, the location of workstations, and the type and size of tools and equipment. You should also pay close attention to the flow of people and information, as this can have a big impact on overall efficiency.
Once you have a good understanding of your current operations, you can then begin to create a detailed, visual representation of the ideal workflow and arrangement of resources. This should include everything from the placement of tools and equipment to the flow of materials and the location of workstations.
It's also important to involve your entire team in the process of creating a standard layout. This will help to ensure that everyone is on board with the changes and that everyone understands the benefits of standardization.
Once you have a standard layout in place, it's important to monitor and measure its effectiveness on a regular basis. This can include anything from tracking the flow of materials to the location of workstations, to the type and size of tools and equipment. It's also important to involve your entire team in the process of monitoring and measuring performance, as this will help to ensure that everyone is committed to continuous improvement.
In conclusion, a standard layout is a powerful tool for unlocking efficiency in lean management. By clearly defining the ideal way of working, it becomes much easier to see where things are going wrong and to make adjustments as needed. This can include anything from adjusting the flow of materials to the location of workstations, to the type and size of tools and equipment. Furthermore, it is a powerful tool for training, knowledge sharing, and continuous improvement. If you're looking to improve efficiency and reduce waste in your operations, a standard layout is definitely worth considering.
Stay Connected
Ad
We want information fast and in a nutshell. We from OI recommend Blinkist* - because it’s simply the best.
* = Affiliate Link