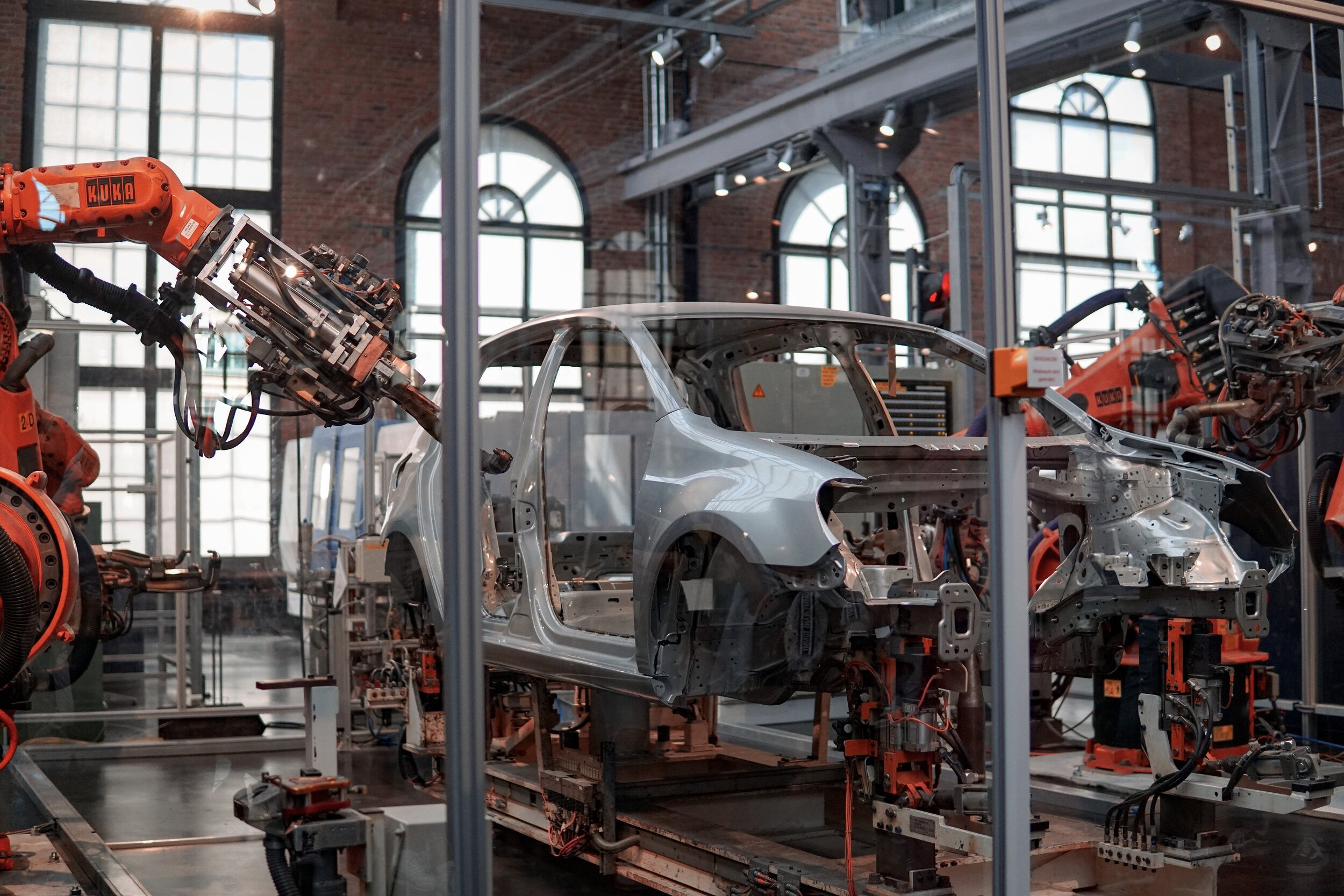
LANGUAGE OF LEAN
Flow Cell
One of the key principles of lean management is the flow cell principle, which is all about optimizing the flow of materials, information, and processes within a manufacturing facility.
Lean management is a production philosophy that seeks to streamline operations and eliminate waste, thereby improving efficiency and reducing costs. One of the key principles of lean management is the flow cell principle, which is all about optimizing the flow of materials, information, and processes within a manufacturing facility.
The flow cell principle is based on the idea that work should be performed in a continuous and uninterrupted flow, without any idle time or unnecessary delays. This principle is critical to achieving lean goals such as reducing lead times, improving quality, and increasing productivity. In order to implement the flow cell principle, a manufacturing facility must first identify and eliminate bottlenecks and constraints in its operations.
The flow cell principle can be applied to a variety of processes within a manufacturing facility, from raw material intake to finished product shipment. For example, in a manufacturing cell, raw materials are moved from one station to another in a continuous flow, without any stops or interruptions. Each station is designed to perform a specific task, and the flow of materials is carefully controlled to ensure that the entire process is as efficient as possible.
The flow cell principle is not just about physical movement of materials, however. It also involves the flow of information, as data must be shared in real-time across different departments and processes in order to optimize flow. A well-designed flow cell system should also include checks and balances to ensure that quality standards are met and that products are being produced to the required specifications.
Another key aspect of the flow cell principle is continuous improvement. Lean management emphasizes the importance of continuous improvement, and the flow cell principle is no exception. By constantly monitoring and analyzing the flow of materials, information, and processes, manufacturing facilities can identify areas for improvement and make the necessary changes to optimize their operations.
In conclusion, the flow cell principle is a critical component of lean management and is essential for achieving lean goals such as reducing lead times, improving quality, and increasing productivity. To fully realize the benefits of the flow cell principle, manufacturing facilities must implement it as part of a comprehensive lean management program, which includes continuous improvement, real-time data sharing, and strict quality control measures.
Automated Replenishement
Automated replenishment refers to the use of technology and systems to automatically manage the replenishment of materials and supplies in a manufacturing environment.
In recent years, the manufacturing industry has seen a shift towards automation and digitization. One of the areas that has seen significant growth in this regard is automated replenishment. Automated replenishment refers to the use of technology and systems to automatically manage the replenishment of materials and supplies in a manufacturing environment. This approach eliminates manual processes, reduces waste, and increases efficiency and productivity.
The origin of automated replenishment can be traced back to the development of just-in-time (JIT) inventory management. JIT is a lean manufacturing philosophy that emphasizes the importance of only having the necessary materials on hand, when they are needed, to minimize waste and optimize production. Automated replenishment builds on this philosophy by using technology to manage the ordering and delivery of materials, reducing the need for manual intervention.
One of the key benefits of automated replenishment is that it reduces the risk of stockouts. Stockouts occur when a manufacturing facility runs out of a material or supplies it needs to continue production. This can result in downtime, reduced efficiency, and increased costs. Automated replenishment systems monitor inventory levels in real-time and automatically order replacements when levels fall below a predetermined threshold, reducing the risk of stockouts and ensuring that materials are always available when they are needed.
Another advantage of automated replenishment is that it helps to optimize inventory levels. By monitoring inventory levels and usage patterns, automated replenishment systems can help to determine the optimal ordering quantities and frequencies, reducing the risk of overstocking and minimizing waste. This helps to reduce the overall costs associated with inventory management and increase the efficiency of the production process.
The implementation of automated replenishment can be a complex process, but it can be done successfully with the right approach. One of the key considerations is the technology and systems that will be used to manage the replenishment process. It is important to choose a system that integrates seamlessly with existing systems and processes, and that is easy to use and manage.
Another important factor in the successful implementation of automated replenishment is the development of a clear strategy. This should include a clear understanding of the goals and objectives of the project, as well as a detailed plan for the implementation process, including the resources that will be required and the timeline for completion. The strategy should also include a plan for monitoring and evaluating the success of the implementation, including regular assessments of inventory levels, costs, and production efficiency.
In addition to the technology and strategy, it is also important to consider the people and processes that will be impacted by the implementation of automated replenishment. This includes training and support for employees, as well as changes to existing processes and procedures. It is important to involve all stakeholders in the implementation process, including employees, suppliers, and customers, to ensure that everyone is on board and that the implementation is successful.
In a nutshell, automated replenishment is an important tool in the arsenal of any lean management expert. It can help to reduce waste, increase efficiency, and optimize production. The successful implementation of automated replenishment requires a clear strategy, the right technology, and the involvement of all stakeholders. By taking these factors into consideration, manufacturers can successfully implement automated replenishment and reap the benefits of a lean and efficient production process.
Cardboard Engineering
Cardboard engineering, also known as corrugated cardboard engineering, is a concept that is gaining popularity in the world of manufacturing.
Cardboard engineering, also known as corrugated cardboard engineering, is a concept that is gaining popularity in the world of manufacturing. This approach is based on the use of cardboard mock-ups, prototypes, and models to visualize, test, and improve manufacturing processes and product design.
We would like to provide an overview of cardboard engineering and its application in a manufacturing setting.
Cardboard engineering is a low-cost, fast, and efficient method for testing and refining manufacturing processes and product design. The approach is based on the use of cardboard prototypes and models to simulate the manufacturing process and identify potential challenges and limitations. This allows manufacturers to quickly test and refine their processes and products without incurring the costs and delays associated with traditional prototyping methods.
The use of cardboard engineering has several benefits in a manufacturing setting. Some of these benefits include:
Low cost: Cardboard engineering is a low-cost method for testing and refining manufacturing processes and product design. This makes it accessible to a wide range of manufacturers, regardless of size or budget.
Fast: Cardboard engineering allows manufacturers to quickly test and refine their processes and products, reducing the time required to bring new products to market.
Improved design: By using cardboard prototypes and models, manufacturers can quickly identify potential challenges and limitations in their product design and make improvements accordingly.
Improved efficiency: Cardboard engineering helps manufacturers to optimize their processes and products, leading to improved efficiency and reduced waste.
Increased collaboration: The use of cardboard prototypes and models promotes collaboration and communication between departments, improving the overall efficiency of the manufacturing process.
In order to implement cardboard engineering in a manufacturing setting, it is important to follow a structured approach. This may include the following steps:
Identify the problem: Identify the challenges and limitations in the manufacturing process or product design that need to be addressed.
Create a cardboard prototype: Create a cardboard prototype or model that simulates the manufacturing process or product design.
Test and refine: Test the cardboard prototype or model and refine the process or product design as needed.
Implement changes: Implement any changes identified during the testing and refinement process.
Continuous improvement: Continuously monitor the manufacturing process and make improvements as needed to optimize efficiency and reduce waste.
In a nutshell, cardboard engineering is a valuable tool for manufacturers looking to improve their processes and products. By using cardboard prototypes and models, manufacturers can quickly test and refine their processes and products, leading to improved efficiency, reduced waste, and increased collaboration. By following a structured approach and continuously monitoring their processes, manufacturers can ensure that they are always working to improve their operations and products
Line Balancing
Line balancing is a critical component of lean manufacturing and is a key tool for improving efficiency, reducing waste, and increasing productivity.
Line balancing is a critical component of lean manufacturing and is a key tool for improving efficiency, reducing waste, and increasing productivity. The principle of line balancing is to ensure that every workstation on a production line is working at optimal capacity and that the overall line is balanced in terms of the workload and resources available.
We would like to provide an overview of the line balancing principle and its application in a manufacturing setting.
Line balancing is a process that involves analyzing the production line and determining the ideal workload for each workstation. This is done by breaking down the tasks involved in producing a product into individual steps, and then determining the time required to complete each step. Once this has been done, the steps are assigned to workstations, taking into account the workload and resources available.
The goal of line balancing is to ensure that each workstation is working at optimal capacity, with no workstation being overworked or underutilized. This results in a more efficient production line, with less waste and reduced lead times.
There are several benefits to line balancing in a manufacturing setting. Some of these benefits include:
Increased efficiency: Line balancing helps to ensure that each workstation is working at optimal capacity, which leads to increased efficiency and reduced waste.
Reduced lead times: By ensuring that each workstation is working efficiently, line balancing can help to reduce lead times and improve delivery times.
Improved quality: Line balancing helps to ensure that each workstation is working at the appropriate pace, which can help to improve quality and reduce the risk of defects.
Increased productivity: Line balancing helps to optimize the use of resources, which can lead to increased productivity and reduced costs.
Improved work environment: Line balancing helps to create a more balanced and less stressful work environment, which can improve employee morale and reduce turnover.
In order to implement line balancing in a manufacturing setting, it is important to follow a structured approach. This may include the following steps:
Define the production line: Define the production line and identify the workstations involved in the process.
Break down the process: Break down the process into individual steps and determine the time required to complete each step.
Assign tasks to workstations: Assign tasks to workstations based on the workload and resources available.
Monitor performance: Continuously monitor performance and make adjustments as necessary to ensure that the line is balanced and working at optimal capacity.
In a nutshell, line balancing is a key tool for improving efficiency and reducing waste in a manufacturing setting. By following a structured approach and continuously monitoring performance, manufacturers can ensure that their production lines are working at optimal capacity, leading to improved efficiency, reduced lead times, and increased productivity.
Overproduction
Overproduction is one of the seven kinds of wastes in the Lean Manufacturing methodology and refers to the production of goods in excess of what is immediately required by the customer. Operations Insider - connecting the dots.
Overproduction is one of the seven kinds of wastes in the Lean Manufacturing methodology and refers to the production of goods in excess of what is immediately required by the customer. This type of waste can have a significant impact on the efficiency and profitability of a manufacturing operation, and as a Lean Management Expert, I would like to provide an overview of the negative effects of overproduction.
One of the main negative effects of overproduction is increased inventory costs. When a manufacturer produces more goods than are immediately required by the customer, the excess inventory takes up valuable space in the warehouse and incurs additional costs for storage and handling. This inventory also ties up capital that could be used elsewhere in the business, reducing the overall financial performance of the company.
Another negative effect of overproduction is increased lead time. When a manufacturer produces goods in excess of what is immediately required, the production line may become congested, leading to delays and increased lead time. This can negatively impact customer satisfaction and reduce the competitiveness of the manufacturer.
Overproduction can also lead to increased defects and decreased quality. When a manufacturer produces more goods than are immediately required, the pressure to maintain production speed and volume can lead to shortcuts being taken and decreased attention to detail. This can result in an increase in defects and a decrease in overall product quality, leading to customer complaints and reduced customer loyalty.
Finally, overproduction can contribute to a lack of flexibility and responsiveness. When a manufacturer produces more goods than are immediately required, they may not be able to respond quickly to changes in customer demand, leading to increased lead time and decreased customer satisfaction. This can also result in increased costs due to the need to adjust production processes and manage excess inventory.
In a nutshell, overproduction is a significant waste in the manufacturing process and can have a negative impact on efficiency, profitability, and customer satisfaction. By focusing on reducing overproduction and improving production processes, manufacturers can increase their competitiveness and improve their overall performance. We recommend that manufacturers continuously monitor their production processes and work to reduce overproduction and improve the overall efficiency of their operations
Zero Defects
Zero Defects, also known as "Zero Quality Control" or "ZQC," is a quality improvement philosophy that seeks to eliminate defects in the production process.
In other projects we have witnessed the significant impact that Zero Defects programs can have on a manufacturing organization. Zero Defects, also known as "Zero Quality Control" or "ZQC," is a quality improvement philosophy that seeks to eliminate defects in the production process. This philosophy has its roots in the Total Quality Management (TQM) movement and has been widely adopted by many manufacturing organizations.
The Zero Defects philosophy is based on the belief that quality should be built into every product, from start to finish. The goal is to eliminate defects and ensure that products are produced to the highest standard, meeting or exceeding customer expectations. This approach to quality focuses on the entire production process, from raw materials to finished goods, and encourages all employees to be actively involved in the quest for zero defects.
One of the key benefits of a Zero Defects program is that it helps to create a culture of continuous improvement. Employees are encouraged to identify areas where defects are occurring, and to work together to eliminate these issues. This creates a sense of ownership and engagement among employees, which in turn drives improved performance and results.
Another key benefit of Zero Defects is that it reduces the costs associated with rework and product defects. Defects in the production process can lead to increased costs, such as scrap, waste, and retooling. By reducing or eliminating these costs, organizations can improve their bottom line and remain competitive in their industry.
The key to success with Zero Defects is to have a well-defined process in place. This process should start with defining the standards for each product and then identifying the critical-to-quality characteristics that must be met. From there, a detailed process map should be created that outlines the steps involved in the production process, from raw materials to finished goods. This process map should also identify the potential sources of defects and highlight the steps that need to be taken to eliminate these defects.
Once the process map is in place, the next step is to implement the Zero Defects program. This involves training employees on the Zero Defects philosophy, as well as the process map and the critical-to-quality characteristics. It is also important to provide employees with the necessary tools and resources to identify and eliminate defects. This may include things like checklists, forms, and software programs.
In addition to training and tools, it is also important to have a robust feedback and continuous improvement process in place. This can include regular quality audits, customer feedback, and employee suggestion programs. The goal of these programs is to identify areas where defects are occurring, and to work together to eliminate these issues.
Finally, it is important to track progress and measure success. This can be done by tracking key performance indicators (KPIs), such as the number of defects, scrap rates, and customer satisfaction levels. By tracking these KPIs, organizations can determine whether their Zero Defects program is having a positive impact and make adjustments as needed.
In conclusion, Zero Defects is a powerful tool for organizations looking to improve the quality of their products and processes. By eliminating defects, organizations can improve customer satisfaction, reduce costs, and remain competitive in their industry. The key to success with Zero Defects is to have a well-defined process in place, and to actively involve employees in the quest for zero defects. By doing so, organizations can achieve operational excellence and realize their full potential.
Change Over
Change overs refer to the process of switching a production line from producing one product to producing another.
Change overs refer to the process of switching a production line from producing one product to producing another. This process can have a significant impact on the efficiency and profitability of a manufacturing operation, and as a Lean Management Expert, I would like to provide an overview of change overs and how they can be improved with SMED (Single Minute Exchange of Dies) Workshops.
One of the main challenges with change overs is the time it takes to complete the process. In many cases, change overs can take several hours or even days, which can result in decreased production and increased costs. This can be a significant issue for manufacturers who need to be able to switch between products quickly and efficiently to meet customer demand.
Another challenge with change overs is the potential for mistakes and errors during the process. When a production line is being changed over, there is an increased risk of mistakes being made, such as incorrect parts being installed or procedures being skipped. This can result in decreased production quality, increased defects, and increased lead time.
In order to improve change overs, manufacturers can implement SMED Workshops. SMED Workshops are designed to streamline the change over process and reduce the time it takes to switch between products. This is achieved by identifying and eliminating non-value-added activities, such as time spent waiting for equipment to cool down or procedures that can be done in parallel. By eliminating these activities, SMED Workshops can significantly reduce the time it takes to complete change overs, allowing manufacturers to increase production efficiency and responsiveness.
SMED Workshops also help to reduce the potential for mistakes and errors during change overs by standardizing the process and reducing the number of activities that need to be performed. This can improve overall production quality, reduce defects, and increase customer satisfaction.
In nutshell, change overs can have a significant impact on the efficiency and profitability of a manufacturing operation. By implementing SMED Workshops, manufacturers can streamline the change over process, reduce the time it takes to switch between products, and improve production quality and customer satisfaction. As a Lean Management Expert, I recommend that manufacturers consider implementing SMED Workshops as a means of improving their overall production efficiency and competitiveness.
Stay Connected
Ad
We want information fast and in a nutshell. We from OI recommend Blinkist* - because it’s simply the best.
* = Affiliate Link