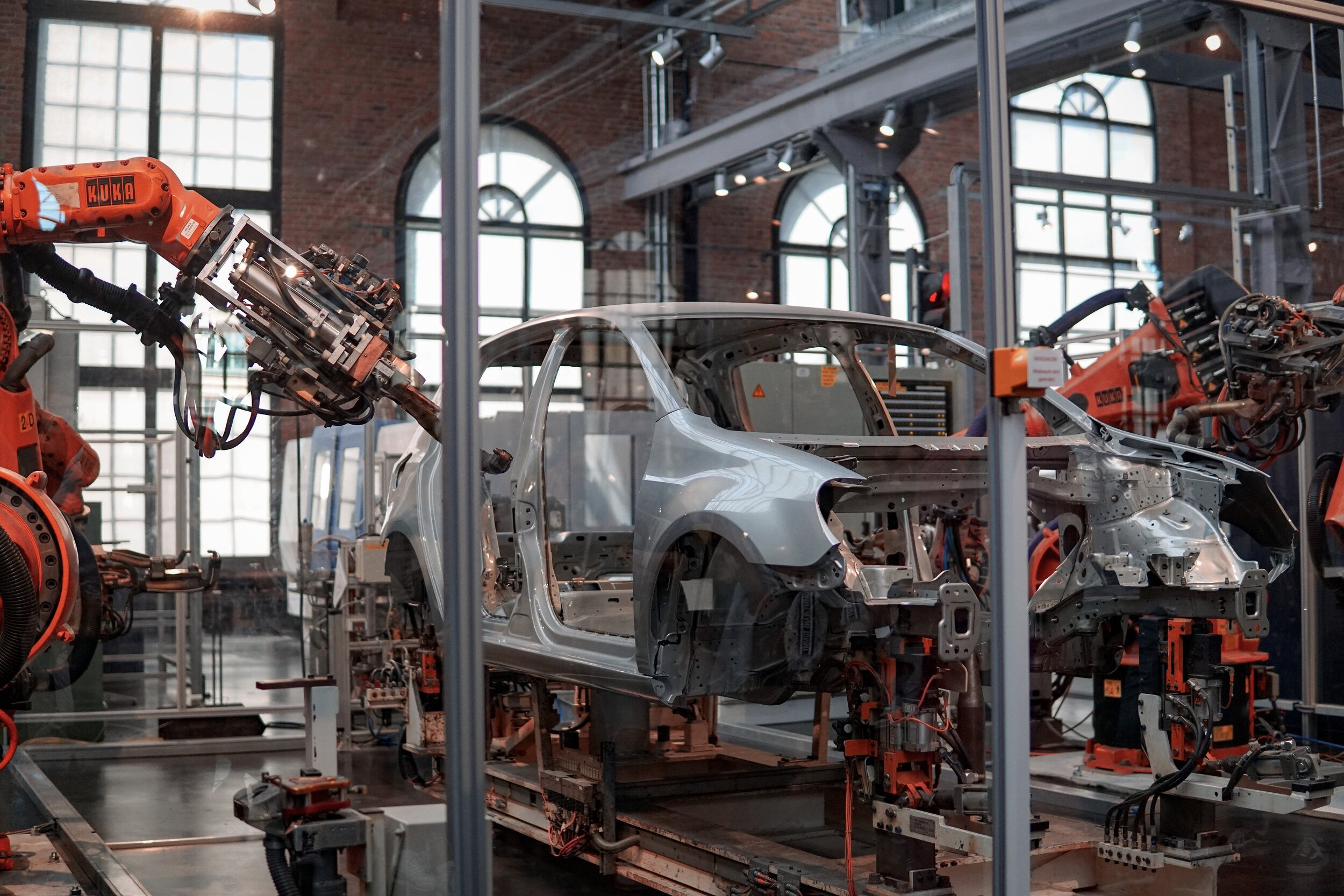
LANGUAGE OF LEAN
Automated Replenishement
Automated replenishment refers to the use of technology and systems to automatically manage the replenishment of materials and supplies in a manufacturing environment.
In recent years, the manufacturing industry has seen a shift towards automation and digitization. One of the areas that has seen significant growth in this regard is automated replenishment. Automated replenishment refers to the use of technology and systems to automatically manage the replenishment of materials and supplies in a manufacturing environment. This approach eliminates manual processes, reduces waste, and increases efficiency and productivity.
The origin of automated replenishment can be traced back to the development of just-in-time (JIT) inventory management. JIT is a lean manufacturing philosophy that emphasizes the importance of only having the necessary materials on hand, when they are needed, to minimize waste and optimize production. Automated replenishment builds on this philosophy by using technology to manage the ordering and delivery of materials, reducing the need for manual intervention.
One of the key benefits of automated replenishment is that it reduces the risk of stockouts. Stockouts occur when a manufacturing facility runs out of a material or supplies it needs to continue production. This can result in downtime, reduced efficiency, and increased costs. Automated replenishment systems monitor inventory levels in real-time and automatically order replacements when levels fall below a predetermined threshold, reducing the risk of stockouts and ensuring that materials are always available when they are needed.
Another advantage of automated replenishment is that it helps to optimize inventory levels. By monitoring inventory levels and usage patterns, automated replenishment systems can help to determine the optimal ordering quantities and frequencies, reducing the risk of overstocking and minimizing waste. This helps to reduce the overall costs associated with inventory management and increase the efficiency of the production process.
The implementation of automated replenishment can be a complex process, but it can be done successfully with the right approach. One of the key considerations is the technology and systems that will be used to manage the replenishment process. It is important to choose a system that integrates seamlessly with existing systems and processes, and that is easy to use and manage.
Another important factor in the successful implementation of automated replenishment is the development of a clear strategy. This should include a clear understanding of the goals and objectives of the project, as well as a detailed plan for the implementation process, including the resources that will be required and the timeline for completion. The strategy should also include a plan for monitoring and evaluating the success of the implementation, including regular assessments of inventory levels, costs, and production efficiency.
In addition to the technology and strategy, it is also important to consider the people and processes that will be impacted by the implementation of automated replenishment. This includes training and support for employees, as well as changes to existing processes and procedures. It is important to involve all stakeholders in the implementation process, including employees, suppliers, and customers, to ensure that everyone is on board and that the implementation is successful.
In a nutshell, automated replenishment is an important tool in the arsenal of any lean management expert. It can help to reduce waste, increase efficiency, and optimize production. The successful implementation of automated replenishment requires a clear strategy, the right technology, and the involvement of all stakeholders. By taking these factors into consideration, manufacturers can successfully implement automated replenishment and reap the benefits of a lean and efficient production process.
Cardboard Engineering
Cardboard engineering, also known as corrugated cardboard engineering, is a concept that is gaining popularity in the world of manufacturing.
Cardboard engineering, also known as corrugated cardboard engineering, is a concept that is gaining popularity in the world of manufacturing. This approach is based on the use of cardboard mock-ups, prototypes, and models to visualize, test, and improve manufacturing processes and product design.
We would like to provide an overview of cardboard engineering and its application in a manufacturing setting.
Cardboard engineering is a low-cost, fast, and efficient method for testing and refining manufacturing processes and product design. The approach is based on the use of cardboard prototypes and models to simulate the manufacturing process and identify potential challenges and limitations. This allows manufacturers to quickly test and refine their processes and products without incurring the costs and delays associated with traditional prototyping methods.
The use of cardboard engineering has several benefits in a manufacturing setting. Some of these benefits include:
Low cost: Cardboard engineering is a low-cost method for testing and refining manufacturing processes and product design. This makes it accessible to a wide range of manufacturers, regardless of size or budget.
Fast: Cardboard engineering allows manufacturers to quickly test and refine their processes and products, reducing the time required to bring new products to market.
Improved design: By using cardboard prototypes and models, manufacturers can quickly identify potential challenges and limitations in their product design and make improvements accordingly.
Improved efficiency: Cardboard engineering helps manufacturers to optimize their processes and products, leading to improved efficiency and reduced waste.
Increased collaboration: The use of cardboard prototypes and models promotes collaboration and communication between departments, improving the overall efficiency of the manufacturing process.
In order to implement cardboard engineering in a manufacturing setting, it is important to follow a structured approach. This may include the following steps:
Identify the problem: Identify the challenges and limitations in the manufacturing process or product design that need to be addressed.
Create a cardboard prototype: Create a cardboard prototype or model that simulates the manufacturing process or product design.
Test and refine: Test the cardboard prototype or model and refine the process or product design as needed.
Implement changes: Implement any changes identified during the testing and refinement process.
Continuous improvement: Continuously monitor the manufacturing process and make improvements as needed to optimize efficiency and reduce waste.
In a nutshell, cardboard engineering is a valuable tool for manufacturers looking to improve their processes and products. By using cardboard prototypes and models, manufacturers can quickly test and refine their processes and products, leading to improved efficiency, reduced waste, and increased collaboration. By following a structured approach and continuously monitoring their processes, manufacturers can ensure that they are always working to improve their operations and products
Stay Connected
Ad
We want information fast and in a nutshell. We from OI recommend Blinkist* - because it’s simply the best.
* = Affiliate Link