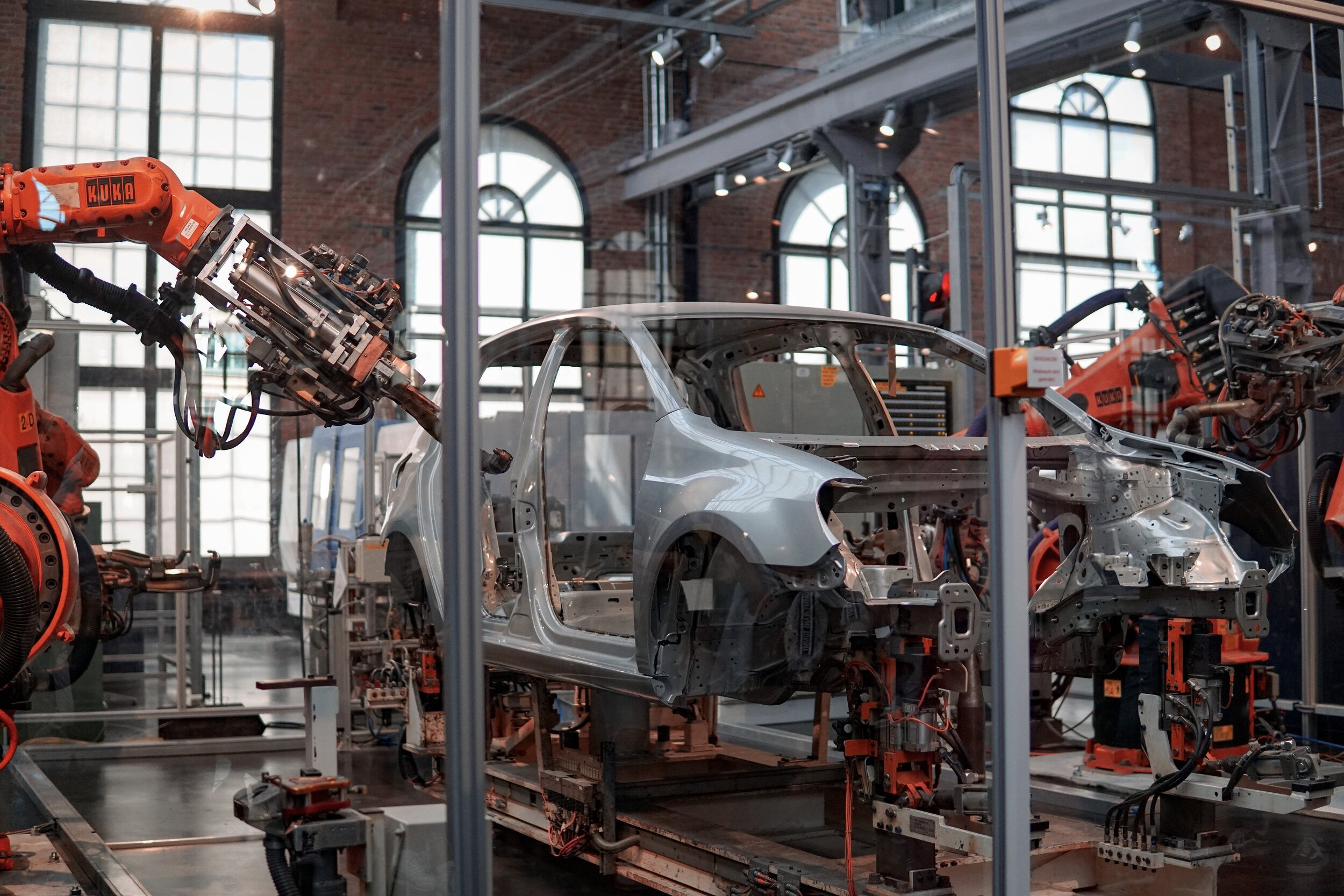
LANGUAGE OF LEAN
Counter Measure
Counter Measurements are a powerful way to track progress and identify areas for improvement, but it is important to understand the difference between short, mid, and long-term actions.
In the manufacturing industry, it is essential to continuously monitor and improve processes to achieve Operational Excellence. One key tool in this effort is the use of Counter Measurements. Counter Measurements are a powerful way to track progress and identify areas for improvement, but it is important to understand the difference between short, mid, and long-term actions.
Short-term actions are immediate solutions to problems that need to be addressed quickly. They are typically reactive, focused on addressing a specific issue and achieving a quick win. Examples of short-term actions include implementing a temporary fix to a machine that is causing production delays, or adjusting a process to improve efficiency.
Mid-term actions are solutions that address underlying issues and provide a longer-lasting impact. These actions may take a bit more time to implement, but they are more comprehensive and often involve a deeper analysis of the problem and its root causes. Examples of mid-term actions include optimizing a production line, improving maintenance procedures, or reducing waste in a process.
Long-term actions are focused on transforming the organization and achieving sustainable change. These actions are strategic, and often require significant investment and planning. They are designed to address the biggest problems facing the organization and to create lasting improvements in processes and systems. Examples of long-term actions include implementing a new production line, modernizing technology, or transforming the supply chain.
So, what makes the difference between short, mid, and long-term actions, and when should each be used? The key difference is the time frame and the level of investment required. Short-term actions are quick, low-investment solutions that can be implemented quickly. Mid-term actions are more comprehensive, requiring a deeper analysis and investment, but they provide a longer-lasting impact. Long-term actions are the most transformative, requiring significant investment and planning, but they are also the most impactful.
To make the most of Counter Measurements, it is important to understand the difference between these types of actions and to choose the right type for each situation. By selecting the right type of action, organizations can achieve quick wins, drive sustainable change, and achieve Operational Excellence.
In a nutshell, Counter Measurements are a critical tool for tracking progress and identifying areas for improvement in the manufacturing industry. By understanding the difference between short, mid, and long-term actions, and by choosing the right type of action for each situation, organizations can achieve continuous improvement and drive sustainable change. With the right approach and the right tools, organizations can achieve Operational Excellence and transform their operations.
Mentor
In the world of lean, the mentor strives to improve the competencies of his / her charge and thereby improve the level of problem-solving and improvement within the organization.
The concept of mentorship can be traced back to the story of "The Odyssey" by Homer, where Mentor was a trusted advisor to Odysseus and a mentor figure to Telemachus.
Telemachus viewed him as a wise and experienced older person who guided him, offered him encouragement and support, and helped him develop into his role and responsibilities.
Lean management is a methodology that aims to eliminate waste and optimize resources in order to improve efficiency and productivity. It is widely used in various industries and has been proven to be highly effective in reducing costs, increasing quality, and improving overall performance. However, implementing lean management can be challenging, especially for those who are new to the field. This is where the role of a mentor comes in.
A mentor is a seasoned professional who has extensive experience in lean management and is willing to share their knowledge and expertise with others. The mentor's role is to guide, advise, and support the mentee in their journey to become proficient in lean management. They provide valuable insights and practical advice that can help the mentee avoid common pitfalls and achieve their goals more quickly.
One of the main benefits of having a mentor is that they can provide the mentee with a different perspective on the problems they are facing. Mentors have a wealth of experience and have likely encountered similar issues in the past. They can share their knowledge and offer solutions that the mentee may not have considered. This can be especially valuable when the mentee is dealing with a complex problem that requires a unique solution.
Another benefit of having a mentor is that they can provide guidance on how to implement lean management in a specific industry or organization. Lean management can be applied to many different types of businesses, but the specific implementation may vary depending on the industry or organization. A mentor can provide guidance on how to tailor lean management to the mentee's specific situation and help them avoid common mistakes.
Moreover, mentors can provide a sounding board for the mentee to discuss their ideas and concerns. This can be particularly beneficial when the mentee is dealing with a difficult situation or trying to navigate a complex process. Mentors can help the mentee to think through their options and make the best decision for their situation.
In addition, mentors can provide the mentee with access to a network of professionals who can offer additional support and advice. This can be especially valuable when the mentee is trying to find resources or connect with other professionals who can help them with their specific goals.
Overall, the role of a mentor in lean management is crucial. They provide guidance, support, and practical advice that can help the mentee become proficient in lean management more quickly and effectively. They offer a different perspective on problems and can provide guidance on how to implement lean management in a specific industry or organization. And they offer a sounding board and access to a network of professionals.
In a nutshell, having a mentor can make a significant difference in the mentee's ability to implement lean management successfully and achieve their goals. It is important for organizations and individuals to find a mentor who can provide the guidance and support they need to excel in their journey of implementing lean management.
Stay Connected
Ad
We want information fast and in a nutshell. We from OI recommend Blinkist* - because it’s simply the best.
* = Affiliate Link