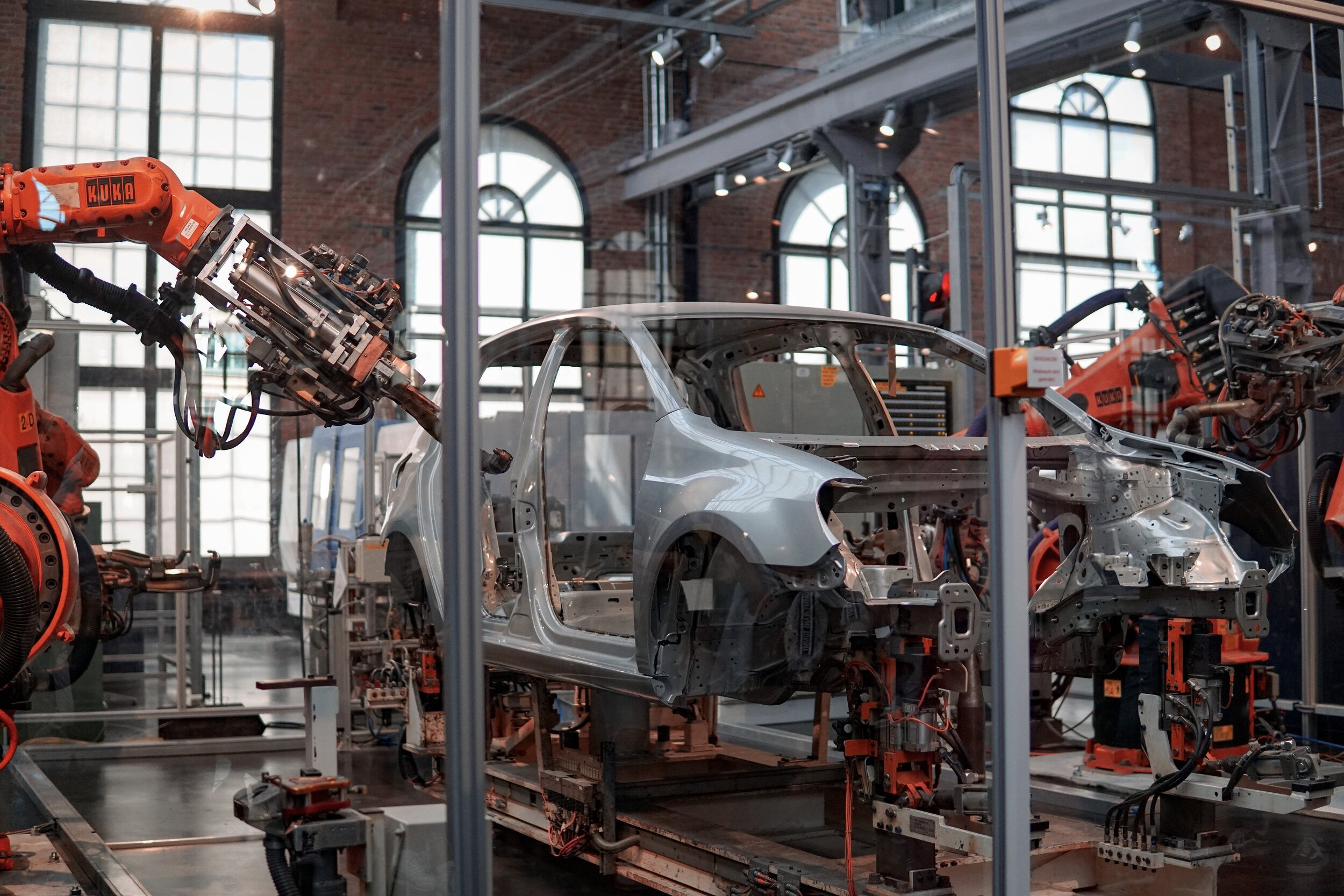
LANGUAGE OF LEAN
Internal Setup
Internal Setup, also known as Machine Changeover or Equipment Changeover, is a critical aspect of Lean Manufacturing. It refers to the process of switching a production machine from one product or production run to another.
Internal Setup, also known as Machine Changeover or Equipment Changeover, is a critical aspect of Lean Manufacturing. It refers to the process of switching a production machine from one product or production run to another. This process can be time-consuming and impact the overall efficiency of a manufacturing plant. For this reason, Lean experts have developed techniques to optimize the Internal Setup process and minimize downtime.
The Internal Setup process can be seen as a non-value-adding (NVA) activity. NVA activities are those that do not directly contribute to the production of a good or service. In the case of Internal Setup, it is necessary but does not add any value to the final product. The goal of Lean is to minimize NVA activities, and the Internal Setup process is no exception.
One of the key strategies for optimizing Internal Setup is to standardize the process. This can be achieved by creating detailed Standard Operating Procedures (SOPs) that outline each step of the setup process. SOPs should include clear instructions, diagrams, and photos to help guide employees through the process. The SOPs should also be reviewed and updated regularly to ensure they are up-to-date and accurate.
In addition to standardizing the process, Lean experts also focus on reducing the time required for Internal Setup. This can be achieved through a combination of reducing the number of steps required and streamlining the process. For example, the use of Quick Changeover fixtures or tools can reduce the time required to changeover a machine. Other strategies include minimizing the number of tools required, using visual aids to guide employees through the process, and using checklists to ensure all steps are completed.
Another important aspect of optimizing Internal Setup is employee engagement and involvement. Lean experts believe that employees who are involved in the process are more likely to take ownership of the process and be more committed to making it as efficient as possible. Encouraging employees to identify areas for improvement and participate in Kaizen events can also help drive continuous improvement.
Finally, it is important to monitor and evaluate the Internal Setup process on a regular basis. This can be done by tracking key performance indicators (KPIs) such as changeover time, number of changeovers, and machine downtime. The KPIs can be used to identify areas for improvement and measure the success of continuous improvement initiatives.
In a nutshell, Internal Setup is a critical aspect of Lean Manufacturing and Operational Excellence. To optimize the process and minimize downtime, Lean experts focus on standardizing the process, reducing the time required, involving employees, and monitoring and evaluating the process. By following these principles, manufacturers can achieve a more efficient and streamlined Internal Setup process, resulting in increased productivity, reduced waste, and improved bottom-line results.
Change Over
Change overs refer to the process of switching a production line from producing one product to producing another.
Change overs refer to the process of switching a production line from producing one product to producing another. This process can have a significant impact on the efficiency and profitability of a manufacturing operation, and as a Lean Management Expert, I would like to provide an overview of change overs and how they can be improved with SMED (Single Minute Exchange of Dies) Workshops.
One of the main challenges with change overs is the time it takes to complete the process. In many cases, change overs can take several hours or even days, which can result in decreased production and increased costs. This can be a significant issue for manufacturers who need to be able to switch between products quickly and efficiently to meet customer demand.
Another challenge with change overs is the potential for mistakes and errors during the process. When a production line is being changed over, there is an increased risk of mistakes being made, such as incorrect parts being installed or procedures being skipped. This can result in decreased production quality, increased defects, and increased lead time.
In order to improve change overs, manufacturers can implement SMED Workshops. SMED Workshops are designed to streamline the change over process and reduce the time it takes to switch between products. This is achieved by identifying and eliminating non-value-added activities, such as time spent waiting for equipment to cool down or procedures that can be done in parallel. By eliminating these activities, SMED Workshops can significantly reduce the time it takes to complete change overs, allowing manufacturers to increase production efficiency and responsiveness.
SMED Workshops also help to reduce the potential for mistakes and errors during change overs by standardizing the process and reducing the number of activities that need to be performed. This can improve overall production quality, reduce defects, and increase customer satisfaction.
In nutshell, change overs can have a significant impact on the efficiency and profitability of a manufacturing operation. By implementing SMED Workshops, manufacturers can streamline the change over process, reduce the time it takes to switch between products, and improve production quality and customer satisfaction. As a Lean Management Expert, I recommend that manufacturers consider implementing SMED Workshops as a means of improving their overall production efficiency and competitiveness.
Standard Layout
A standard layout is a detailed, visual representation of the ideal workflow and arrangement of resources in a given area.
Standard Layout: The Key to Unlocking Efficiency in Lean Management
Standardization is one of the fundamental principles of lean management, and it's no surprise that it's also one of the most effective ways to improve efficiency and reduce waste in your operations. One of the most powerful tools in the standardization toolbox is the standard layout, also known as "taikyō-sei" in Japanese.
A standard layout is a detailed, visual representation of the ideal workflow and arrangement of resources in a given area. This can include anything from the placement of tools and equipment to the flow of materials and the location of workstations. The goal is to create a clear and consistent way of working that minimizes waste, maximizes efficiency, and makes it easy for everyone on the team to understand and follow.
One of the most important benefits of a standard layout is that it makes it much easier to identify and eliminate sources of waste and inefficiency. By clearly defining the ideal way of working, it becomes much easier to see where things are going wrong and to make adjustments as needed. This can include anything from adjusting the location of workstations to the flow of materials, to the type and size of tools and equipment.
Another key benefit of a standard layout is that it makes it much easier to train new employees and to ensure that everyone is following the same processes. When everyone is working in the same way, it becomes much easier to share knowledge and best practices, which can help to improve the overall performance of the team.
Finally, a standard layout can also be a powerful tool for continuous improvement. By clearly defining the ideal way of working, it becomes much easier to measure performance and to identify areas for improvement. This can include anything from adjusting the flow of materials to the location of workstations, to the type and size of tools and equipment.
So, how do you go about creating a standard layout? The first step is to conduct a thorough analysis of your current operations. This should include a detailed study of the flow of materials, the location of workstations, and the type and size of tools and equipment. You should also pay close attention to the flow of people and information, as this can have a big impact on overall efficiency.
Once you have a good understanding of your current operations, you can then begin to create a detailed, visual representation of the ideal workflow and arrangement of resources. This should include everything from the placement of tools and equipment to the flow of materials and the location of workstations.
It's also important to involve your entire team in the process of creating a standard layout. This will help to ensure that everyone is on board with the changes and that everyone understands the benefits of standardization.
Once you have a standard layout in place, it's important to monitor and measure its effectiveness on a regular basis. This can include anything from tracking the flow of materials to the location of workstations, to the type and size of tools and equipment. It's also important to involve your entire team in the process of monitoring and measuring performance, as this will help to ensure that everyone is committed to continuous improvement.
In conclusion, a standard layout is a powerful tool for unlocking efficiency in lean management. By clearly defining the ideal way of working, it becomes much easier to see where things are going wrong and to make adjustments as needed. This can include anything from adjusting the flow of materials to the location of workstations, to the type and size of tools and equipment. Furthermore, it is a powerful tool for training, knowledge sharing, and continuous improvement. If you're looking to improve efficiency and reduce waste in your operations, a standard layout is definitely worth considering.
Stay Connected
Ad
We want information fast and in a nutshell. We from OI recommend Blinkist* - because it’s simply the best.
* = Affiliate Link