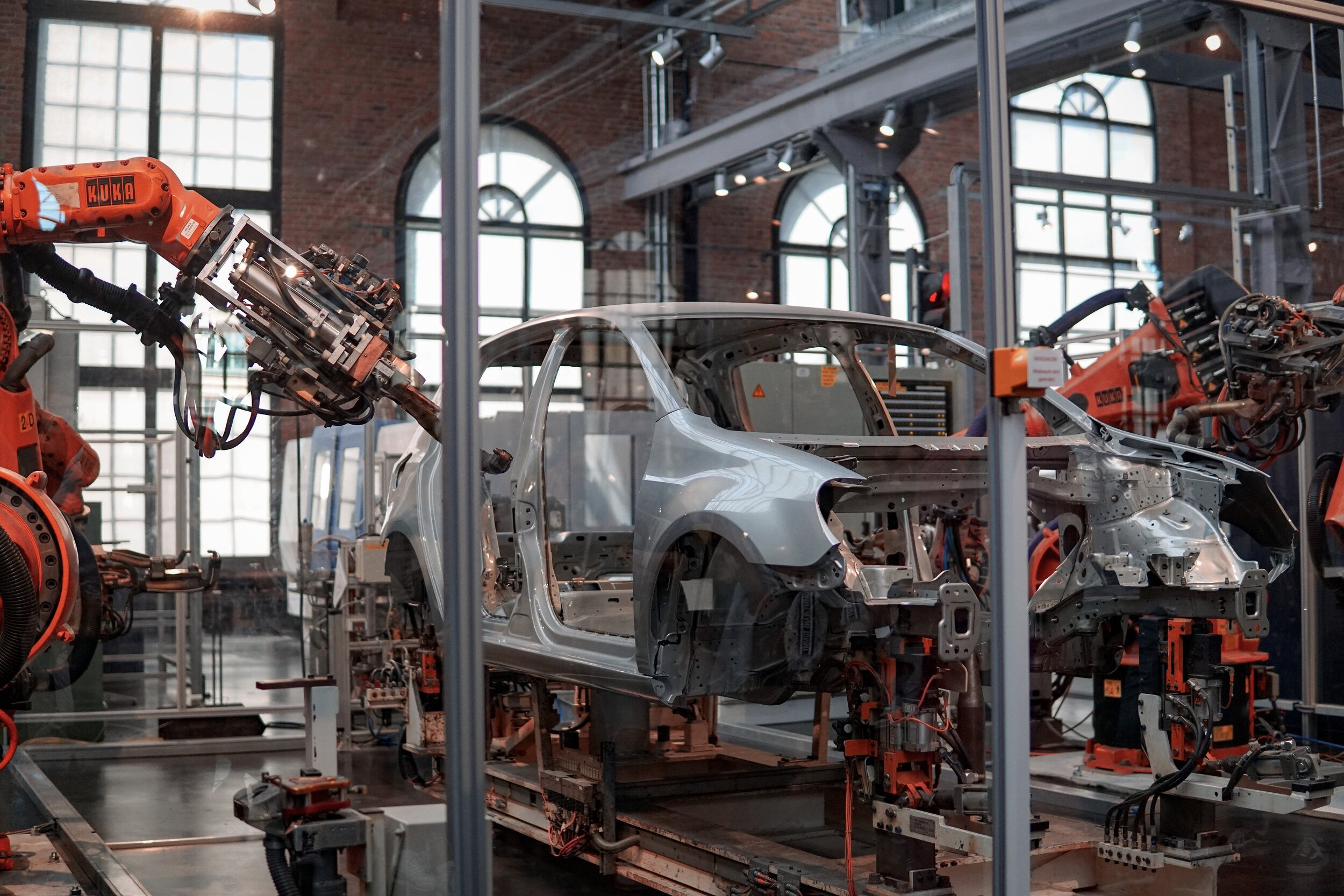
LANGUAGE OF LEAN
Change Over
Change overs refer to the process of switching a production line from producing one product to producing another.
Change overs refer to the process of switching a production line from producing one product to producing another. This process can have a significant impact on the efficiency and profitability of a manufacturing operation, and as a Lean Management Expert, I would like to provide an overview of change overs and how they can be improved with SMED (Single Minute Exchange of Dies) Workshops.
One of the main challenges with change overs is the time it takes to complete the process. In many cases, change overs can take several hours or even days, which can result in decreased production and increased costs. This can be a significant issue for manufacturers who need to be able to switch between products quickly and efficiently to meet customer demand.
Another challenge with change overs is the potential for mistakes and errors during the process. When a production line is being changed over, there is an increased risk of mistakes being made, such as incorrect parts being installed or procedures being skipped. This can result in decreased production quality, increased defects, and increased lead time.
In order to improve change overs, manufacturers can implement SMED Workshops. SMED Workshops are designed to streamline the change over process and reduce the time it takes to switch between products. This is achieved by identifying and eliminating non-value-added activities, such as time spent waiting for equipment to cool down or procedures that can be done in parallel. By eliminating these activities, SMED Workshops can significantly reduce the time it takes to complete change overs, allowing manufacturers to increase production efficiency and responsiveness.
SMED Workshops also help to reduce the potential for mistakes and errors during change overs by standardizing the process and reducing the number of activities that need to be performed. This can improve overall production quality, reduce defects, and increase customer satisfaction.
In nutshell, change overs can have a significant impact on the efficiency and profitability of a manufacturing operation. By implementing SMED Workshops, manufacturers can streamline the change over process, reduce the time it takes to switch between products, and improve production quality and customer satisfaction. As a Lean Management Expert, I recommend that manufacturers consider implementing SMED Workshops as a means of improving their overall production efficiency and competitiveness.
YOKOTEN
Japanese for “across everywhere”.
Japanese term meaning “across everywhere”. With Yokoten the knowledgetransfer is carried out and all activities and countermeasures along the continuous improvement process are communicated organization wide and with other branches of the organization and its affiliates.
Yokoten is not just another Japanese word of the lean world. It might seem fancy to have only Japanese terms on the lean journey but one word isn’t that mainstream and well known but crucial when it comes to lean transformation in your organization. Yokoten describes the process of sharing knowledge across your organization. It includes systematics such as lead plans for copying and improving kaizen activities that work in your complete organization.
Think of Yokoten as horizontal deployment of improvement actions. The Yokoten approach is horizontal and peer-to-peer, with the expectation of Gemba Culture that your people go and see for themselves and learn how other departments or plants in your organization improved their processes. The idea behind is global knowledge transfer of improvement actions as basis for individual local solutions.
It is crucial that it is not a top-down thing where in all plants of your organization everything has to be the exact same. That simply will not work. It is more a benchmark where e.g. one plant in your organization is the champion of one manufacturing process (e.g. injection moulding). Therefore this plant is the “Lead Plant” and by this the benchmark for injection moulding organization wide. All other plants with injection moulding are welcome to the “Lead Plant” to learn from their experience and adopt the Kaizen activities to their own individual needs. With this kind of knowledge transfer a sustainable improvement and collaboration in your organization will be established.
In a nutshell, Yokoten can be understood as internal copy and improve. The role as senior manager is to spread the information and build bridges between the different locations/plants and give the transfer of knowledge a little jump start. Make your organization learn and improve from each other, most of the time there are already good examples out there and just want to be explored and further improved.
The long term success will prove that it is not the processes but the people that are continuously developed, that make the difference between a growing and successful organization or a simple copy cat of Kaizen activities.
The effective Yokoten process is a crucial brick for the foundation of a true learning organization. And no matter where you look at, truly successful organizations have a functioning organization wide knowledge transfer installed.
Stay Connected
Ad
We want information fast and in a nutshell. We from OI recommend Blinkist* - because it’s simply the best.
* = Affiliate Link