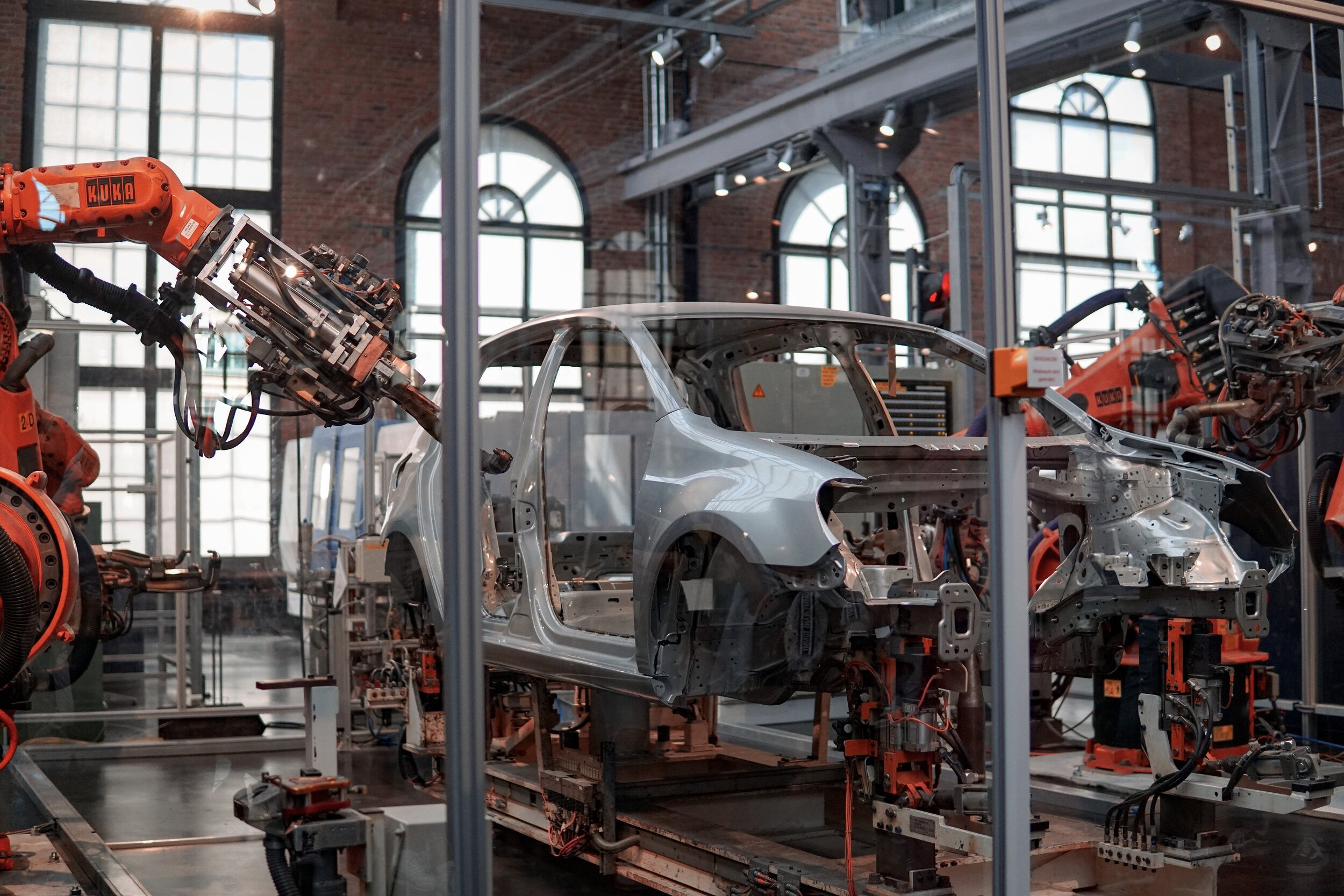
LANGUAGE OF LEAN
One Point Lesson
One Point Lesson (OPL) is a method used in the manufacturing industry that can greatly improve operational efficiency and overall quality.
One Point Lesson (OPL) is a method used in the manufacturing industry that can greatly improve operational efficiency and overall quality. This method is often used within the context of Lean Management, which is a strategy that focuses on maximizing value while minimizing waste. As a Lean Management Expert, I will be discussing how OPL can be used to improve operations in the manufacturing industry.
OPL is a simple but effective tool that helps to standardize and spread best practices across an organization. It is a one-page document that summarizes a lesson learned from a problem or improvement opportunity. This document is designed to be easy to understand and share, so that others can learn from the lesson and apply it in their own work. The purpose of OPL is to promote continuous improvement by capturing and sharing knowledge that can be used to prevent similar problems from happening again in the future.
One of the key benefits of using OPL is that it allows for quick and easy dissemination of knowledge and best practices. The one-page format makes it easy for employees to understand and remember the information, and the lessons learned can be quickly spread throughout the organization. This can lead to significant improvements in the quality of products and services, as well as increased efficiency in operations.
OPL can also help organizations to identify and eliminate non-value-adding activities. This is because the lessons learned can be used to identify areas where improvements can be made, and then the appropriate changes can be implemented. For example, if a problem occurs during the production process, an OPL can be created to document the cause of the problem and how it was resolved. This information can then be used to make changes that will prevent the problem from happening again in the future.
In addition to improving quality and efficiency, OPL can also help organizations to foster a culture of continuous improvement. By capturing and sharing knowledge, employees are encouraged to look for ways to improve processes and to find solutions to problems. This leads to a more engaged workforce, as employees feel that their ideas and contributions are valued.
In order to successfully implement OPL in the manufacturing industry, there are a few key steps that organizations should follow. Firstly, it is important to have a clear understanding of what information should be included in each OPL. This includes the problem or opportunity that was identified, the cause of the problem, the solution that was implemented, and the results of the solution.
Secondly, organizations should develop a system for sharing OPLs throughout the organization. This could be done through regular meetings, email, or an online platform. The key is to make sure that the information is easily accessible and can be quickly shared with others.
Finally, organizations should ensure that they have the resources in place to support the implementation of OPL. This includes providing training to employees on how to create and use OPLs, as well as having dedicated staff to manage the process.
In a nutshell, One Point Lesson (OPL) is a powerful tool that can help organizations in the manufacturing industry to improve quality, efficiency, and overall operations. By standardizing and spreading best practices, organizations can foster a culture of continuous improvement and identify and eliminate non-value-adding activities. To successfully implement OPL, organizations should follow a few key steps, including having a clear understanding of what information should be included in each OPL, developing a system for sharing OPLs, and ensuring that they have the resources in place to support the implementation.
Point Of Use
Point of Use (POU) is a key component of Lean initiatives aimed at reducing waste, increasing efficiency, and improving overall production processes.
Point of Use (POU) is a key component of Lean initiatives aimed at reducing waste, increasing efficiency, and improving overall production processes. It is a philosophy that focuses on delivering materials, tools, and equipment directly to the worker at the moment they need them. The goal of POU is to minimize unnecessary movement, handling, and storage of materials, which not only streamlines production but also reduces the risk of damage, loss, and obsolescence.
In traditional manufacturing processes, raw materials and supplies are often stored in central locations, such as inventory rooms, and are retrieved and moved to the production line as needed. This can result in excess inventory, increased lead times, and the need for multiple trips to retrieve materials. Additionally, workers may spend significant amounts of time searching for the tools or materials they need, which reduces productivity and increases the risk of mistakes.
Point of Use aims to eliminate these inefficiencies by bringing materials and supplies directly to the worker at the point of need. This reduces the need for workers to search for materials and increases the speed and accuracy of the production process. POU also reduces the amount of inventory that needs to be stored and managed, which helps to reduce the risk of damage, loss, and obsolescence.
There are several different approaches to implementing POU, each with its own set of benefits and challenges. One approach is to use kanban systems, which are visual signals that tell workers when it’s time to replenish materials or supplies. Another approach is to use automated systems, such as conveyors or robots, which move materials and supplies directly to the production line as needed.
Regardless of the approach used, POU requires careful planning and coordination between all departments involved in the production process. It also requires regular monitoring and adjustments to ensure that the system is working as intended. This can include tracking key performance indicators (KPIs) such as inventory levels, production lead times, and worker productivity.
One of the benefits of POU is that it helps to improve worker morale and job satisfaction. When workers have access to the materials and supplies they need exactly when they need them, they are able to focus on their work without worrying about finding the right tools or supplies. Additionally, POU helps to eliminate the frustration that workers may feel when they are unable to find the materials they need, which can lead to decreased job satisfaction and even burnout.
Another benefit of POU is that it helps to reduce the risk of mistakes and increase quality. When workers have everything they need at their fingertips, they are able to focus on their work without worrying about searching for materials or supplies. This reduces the risk of errors, which in turn helps to improve overall quality and reduce the need for rework.
In a nutshell, Point of Use is an important concept in Lean Manufacturing that aims to reduce waste, increase efficiency, and improve overall production processes. By bringing materials and supplies directly to the worker at the point of need, POU streamlines production, reduces the risk of damage, loss, and obsolescence, and improves worker morale and job satisfaction. To be successful, POU requires careful planning, coordination, and monitoring, as well as a focus on continuous improvement. By implementing POU and other Lean principles, manufacturers can reduce costs, increase efficiency, and improve overall production outcomes.
Product Machine Matrix
The Product Machine Matrix is a methodology that can be used in the manufacturing industry to improve production processes and achieve operational excellence.
The Product Machine Matrix is a methodology that can be used in the manufacturing industry to improve production processes and achieve operational excellence. The idea behind this approach is to create a matrix that matches the type of product being produced with the appropriate machine for that product.
The first step in implementing the Product Machine Matrix is to analyze the current production process and identify areas where improvements can be made. This can be done through the use of data and performance measurement tools, as well as by observing the process and gathering feedback from employees.
Once the areas for improvement have been identified, the next step is to determine the optimal machine for each type of product. This involves considering factors such as the complexity of the product, the volume of production, and the skill level of the operator. It may also be necessary to make changes to the existing machines or to purchase new equipment in order to meet the needs of the production process.
The Product Machine Matrix also requires the establishment of standard work procedures for each machine and product type. This helps to ensure that the production process is consistent and efficient, and it also provides a roadmap for continuous improvement. Standard work procedures should be regularly reviewed and updated based on performance data and feedback from employees.
Another important aspect of the Product Machine Matrix is the need for visual management. This involves creating clear and easy-to-understand visual aids, such as work instructions and flow charts, that help to guide employees through the production process. This helps to prevent errors and improve productivity, as well as making it easier for employees to quickly identify and resolve any issues that may arise.
To be effective, the Product Machine Matrix must be integrated into the overall culture of the organization. This requires the commitment and engagement of employees at all levels, as well as a focus on continuous improvement and a willingness to embrace change. Regular training and communication is also key to the success of the methodology, as it helps to build the necessary skills and knowledge, and ensures that everyone is working towards a common goal.
In a nutshell, the Product Machine Matrix is a powerful methodology that can be used to improve production processes in the manufacturing industry. By carefully matching the type of product with the appropriate machine, and by establishing standard work procedures and utilizing visual management techniques, organizations can achieve operational excellence and drive continuous improvement. With the right approach and commitment, this methodology can deliver significant benefits to any organization looking to optimize its production processes.
Inventory
Inventory is often viewed as a necessary evil, as it provides a safety net to ensure that products are available to meet customer demand.
Inventory is often viewed as a necessary evil, as it provides a safety net to ensure that products are available to meet customer demand. However, from the perspective of Lean Management, inventory can also be seen as a type of waste.
In Lean, waste is defined as anything that does not add value to the customer. From this perspective, inventory can be considered waste because it ties up valuable resources such as space, money, and time without providing any immediate value to the customer. This is because inventory requires storage, which takes up valuable space, and also requires investment in the products themselves. In addition, inventory can lead to obsolescence, as products may become outdated or go out of fashion before they can be sold. Furthermore, inventory can lead to inefficiencies in the supply chain, as products may sit on shelves for extended periods of time before they are sold, adding unnecessary time to the overall lead time.
Despite these challenges, inventory is also an essential component of most businesses. Inventory provides a safety net, ensuring that there are products available to meet customer demand even when there are disruptions in the supply chain. It also allows businesses to take advantage of bulk purchasing discounts, and to manage seasonal variations in demand.
So, how can Lean Management help businesses to steer inventory in the best direction? There are several key steps that can be taken to minimize the waste associated with inventory while still ensuring that the business has the products it needs to meet customer demand.
The first step is to implement a Lean production system. This involves using the principles of Lean Management to streamline production processes and reduce waste in all areas of the business, including inventory management. By reducing waste in the production process, it is possible to minimize the amount of inventory that is required, freeing up valuable resources for other areas of the business.
The second step is to implement a pull-based production system. This involves using customer demand as the driving force behind production, rather than using forecasted demand to determine production schedules. This can help to minimize inventory waste by ensuring that products are only produced when there is a genuine demand for them.
The third step is to implement just-in-time (JIT) inventory management. JIT is a Lean approach to inventory management that involves only ordering the products that are required to meet customer demand, and no more. This can help to minimize inventory waste by reducing the amount of product that is held in reserve, freeing up valuable resources such as space and money.
The fourth step is to implement a continuous improvement program. This involves regularly reviewing inventory levels and processes, and making changes where necessary to reduce waste and increase efficiency. This can help to ensure that inventory management processes are constantly evolving, and that the business is always adapting to changing customer demand.
In a nutshell, inventory management is an important aspect of any business, as it helps to ensure that the right products are available at the right time to meet customer demand. However, from the perspective of Lean Management, inventory can also be seen as a type of waste. By implementing a Lean production system, a pull-based production system, JIT inventory management, and a continuous improvement program, businesses can minimize the waste associated with inventory while still ensuring that they have the products they need to meet customer demand. By adopting these principles, businesses can increase efficiency, reduce costs, and improve overall customer satisfaction.
Annual Objectives
The use of annual objectives with 3 to 5 years breakthrough objectives is a crucial aspect of policy development in an organization.
The use of annual objectives with 3 to 5 years breakthrough objectives is a crucial aspect of policy development in an organization. This approach to setting goals allows an organization to balance both short-term and long-term objectives, ensuring that progress is being made towards both immediate and ultimate goals. In this article, an operational excellence expert will discuss the importance of this approach and the steps organizations can take to implement it effectively.
The first step in setting annual objectives with 3 to 5 years breakthrough objectives is to define the long-term vision of the organization. This vision should reflect the organization's ultimate goals and should be ambitious yet achievable. It should also align with the organization's mission and values, as well as the larger goals of the industry or sector in which it operates.
Once the long-term vision has been defined, the organization can begin setting its annual objectives. These objectives should be specific, measurable, achievable, relevant, and time-bound (SMART). They should also align with the long-term vision of the organization. For example, if the long-term vision is to become the leader in a particular market, an annual objective might be to increase market share by a certain percentage each year.
The next step is to set the 3 to 5 years breakthrough objectives. These objectives should be significant milestones that are critical to achieving the long-term vision. They should also be challenging, yet achievable, and should align with the annual objectives. For example, if the long-term vision is to become the leader in a particular market, a 3 to 5 years breakthrough objective might be to become the market leader in a particular geographic region.
Once the objectives have been set, the organization can develop a policy to support their achievement. This policy should include specific strategies and initiatives that will help the organization achieve its objectives. For example, the policy might include initiatives to improve product quality, increase customer satisfaction, reduce costs, or increase market share.
In order to effectively implement the policy, the organization must allocate resources appropriately. This includes allocating both financial and human resources, as well as the time and energy of key stakeholders. The organization must also establish a process for monitoring progress towards the objectives and for making adjustments as needed.
The use of annual objectives with 3 to 5 years breakthrough objectives can be a powerful tool for organizations that are seeking to improve their performance and achieve their goals. However, it is important to remember that this approach requires a significant investment of time and resources, as well as a commitment to ongoing improvement. Organizations that are willing to make this investment will be well-positioned to achieve their goals and create a bright future for themselves and their stakeholders.
In a nutshell, the use of annual objectives with 3 to 5 years breakthrough objectives is a crucial aspect of policy development in an organization. It allows organizations to balance both short-term and long-term objectives, ensuring that progress is being made towards both immediate and ultimate goals. By following the steps outlined in this article, organizations can effectively implement this approach and achieve their goals.
TPM - Total Productive Maintenance
Total Productive Maintenance (TPM) is a maintenance strategy that involves involving all employees in the maintenance process to maximize equipment productivity and minimize downtime.
Total Productive Maintenance (TPM) is a methodology that originated in Japan in the 1970s and has since become a widely recognized and adopted approach to operational excellence in manufacturing and other operations-focused industries. It is a comprehensive approach that seeks to optimize the performance of equipment and processes through a focus on maintaining and improving reliability and efficiency.
The origins of TPM can be traced back to the Japanese auto industry, where manufacturers were seeking ways to increase productivity and competitiveness in the face of increasing global competition. TPM emerged as a response to the need for a more proactive and integrated approach to equipment maintenance, with the goal of improving both productivity and overall equipment effectiveness (OEE).
Over time, TPM has evolved and expanded to encompass a wider range of objectives and activities. Today, it is widely regarded as a best-practice approach to operational excellence, and is widely used in many different industries, including manufacturing, healthcare, and government operations.
One of the key features of TPM is its focus on involving all employees in the maintenance and improvement process. This is achieved through the creation of cross-functional teams and the use of a range of techniques, including root cause analysis, standardization, and continuous improvement.
Another key aspect of TPM is its focus on data-driven decision-making and performance measurement. This involves the collection and analysis of data on equipment and process performance, which is then used to identify areas for improvement and to drive continuous improvement efforts.
When properly implemented, TPM can have a significant impact on organizational performance and competitiveness. This can include improvements in equipment reliability, increased productivity, reduced waste, and improved overall equipment effectiveness (OEE).
To achieve these benefits, it is important to implement TPM in a structured and systematic way, with clear goals and objectives and a strong focus on continuous improvement. This typically involves a multi-phased approach, starting with an assessment of existing processes and equipment, followed by the development of a comprehensive improvement plan and the implementation of specific improvement initiatives.
In a nutshell, TPM is a proven methodology that can help organizations achieve operational excellence by optimizing the performance of their equipment and processes. To achieve success, organizations must approach TPM in a systematic and structured way, with clear goals and objectives, and a strong focus on continuous improvement.
Key points for a successful TPM implementation:
Involve all employees in the process
Focus on data-driven decision-making
Adopt a multi-phased approach
Prioritize continuous improvement
Develop a comprehensive improvement plan.
JIT
Just-in-Time (JIT) is a manufacturing and inventory control system in which raw materials, components, and finished products are delivered to the production line exactly when they are needed.
Just-in-Time (JIT) is a manufacturing and inventory control system in which raw materials, components, and finished products are delivered to the production line exactly when they are needed. The goal of JIT is to minimize inventory levels and reduce lead times, while maintaining high levels of production efficiency.
JIT is a pull-based system, which means that production is driven by customer demand rather than by a production schedule. This is achieved by using Kanban, a signaling system that alerts the supplier to send more materials or components when the inventory level of a specific item reaches a predetermined minimum level.
The origins of JIT can be traced back to the manufacturing practices of the Toyota Motor Company in the 1950s. It was developed by Taiichi Ohno, an engineer at Toyota, as a response to the inefficiencies he observed in the company's production processes. Ohno recognized that by reducing the amount of inventory and increasing the flow of materials, Toyota could improve its production efficiency and responsiveness to customer demand.
One of the key principles of JIT is the elimination of waste, or "muda" in Japanese. Ohno identified seven types of waste in manufacturing: overproduction, waiting, unnecessary motion, overprocessing, defects, excess inventory, and unused human potential. JIT aims to eliminate these forms of waste by creating a smooth and efficient flow of materials and products through the production process.
JIT also relies on the concept of "one piece flow", which is the production of one item at a time, rather than producing large batches of items. This allows for better control of the production process, as well as the ability to quickly identify and correct any problems that may arise.
Another important aspect of JIT is the use of visual management tools, such as Andon boards and Kanban boards. These tools allow for real-time monitoring of the production process, and can alert workers to potential problems before they become major issues.
JIT also requires a high level of collaboration and communication between suppliers, manufacturers, and customers. This is necessary to ensure that materials and components are delivered to the production line exactly when they are needed, and that finished products are delivered to customers in a timely manner.
JIT has a number of benefits for manufacturers. One of the most significant is that it can help to reduce inventory levels, which can free up valuable floor space, reduce storage costs, and minimize the risk of stockouts. JIT can also help to improve production efficiency by reducing lead times and minimizing downtime caused by waiting for materials or components.
JIT can also help to improve product quality by reducing defects, and increasing the ability to quickly identify and correct any problems that may arise in the production process.
JIT also helps companies to be more responsive to customer demand by reducing lead times and increasing the speed of delivery. This can help to improve customer satisfaction, and increase the chances of repeat business.
JIT also helps companies to be more flexible and adaptable to changes in customer demand. It allows companies to more easily shift production to different products or product lines, which can help to maintain profitability during periods of slow sales.
However, it's worth noting that JIT is not suitable for all industries and companies, it's best applied in companies where the production process is well-defined, the demand is stable and predictable, and the lead times are short. Implementing JIT can also be challenging and requires a significant investment of time and resources to establish an effective system.
Additionally, JIT requires a high level of coordination and communication with suppliers and customers, which can be difficult to achieve. This is particularly true for companies that have a large number of suppliers or customers, or those that operate in
Stay Connected
Ad
We want information fast and in a nutshell. We from OI recommend Blinkist* - because it’s simply the best.
* = Affiliate Link