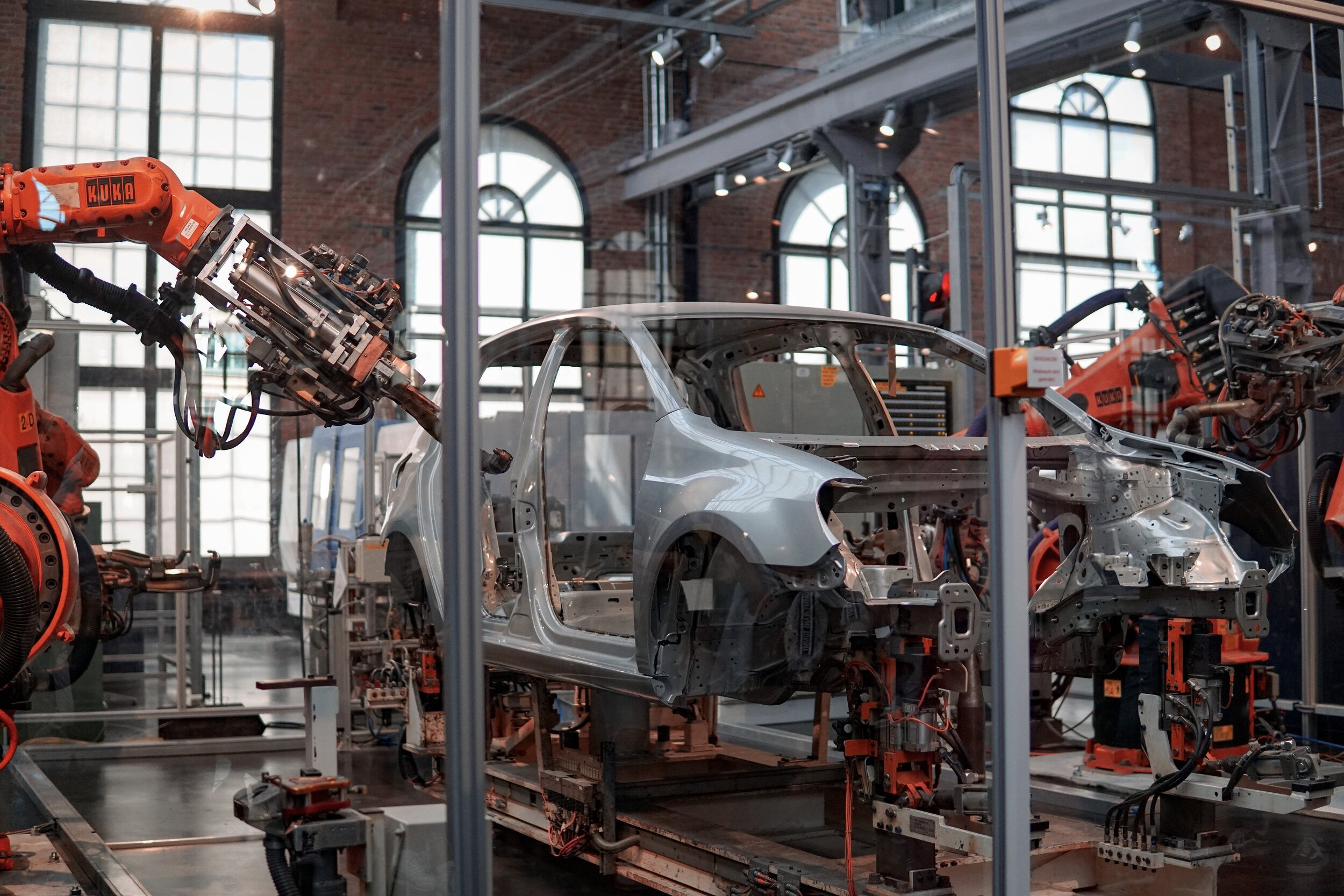
LANGUAGE OF LEAN
Mixed Model Production
We believe that MMP has the potential to bring significant benefits to a production line by increasing efficiency, reducing waste, and improving customer satisfaction.
Mixed Model Production (MMP) is a flexible production strategy that is gaining popularity in the manufacturing industry. We believe that MMP has the potential to bring significant benefits to a production line by increasing efficiency, reducing waste, and improving customer satisfaction.
Mixed Model Production is characterized by the simultaneous production of different models and variations of a product on the same production line. This approach is in contrast to the traditional practice of having a dedicated production line for each product type. In MMP, production is optimized by using a mix of products, models, and variations that can be produced on the same equipment, thereby reducing the need for changeovers, equipment downtime, and material waste.
One of the key benefits of MMP is increased production efficiency. By producing multiple products on the same production line, changeovers and downtime are minimized, reducing the time it takes to produce each product. This increased efficiency results in improved productivity, lower production costs, and higher customer satisfaction.
Another advantage of MMP is reduced waste. The production of multiple products on the same line results in a better utilization of resources and raw materials. This, in turn, reduces the amount of waste generated and the costs associated with waste disposal. Additionally, the reduced downtime results in less energy consumption and a more sustainable production process.
In MMP, the key to success is the ability to schedule production effectively. This requires a deep understanding of the production process, the equipment, and the capabilities of the workforce. A well-designed MMP strategy should be based on a detailed analysis of the production line and a comprehensive understanding of the production process.
The first step in implementing MMP is to identify the different products, models, and variations that can be produced on the same production line. This requires a thorough analysis of the production process and the equipment used. Once the different products have been identified, the next step is to determine the most efficient scheduling of production. This requires a detailed understanding of the production process and the equipment used, as well as the capabilities of the workforce.
The implementation of MMP requires a cross-functional approach that involves teams from different areas of the organization, including production, engineering, and logistics. The success of MMP depends on the collaboration and cooperation of these teams, as well as the effective communication of the MMP strategy to all stakeholders.
In a nutshell, Mixed Model Production is a flexible production strategy that has the potential to bring significant benefits to the manufacturing industry. As a Lean Management and Operational Excellence expert, I believe that MMP has the potential to increase production efficiency, reduce waste, and improve customer satisfaction. However, the success of MMP depends on a detailed understanding of the production process, the equipment, and the workforce, as well as a cross-functional approach that involves teams from different areas of the organization.
Product Machine Matrix
The Product Machine Matrix is a methodology that can be used in the manufacturing industry to improve production processes and achieve operational excellence.
The Product Machine Matrix is a methodology that can be used in the manufacturing industry to improve production processes and achieve operational excellence. The idea behind this approach is to create a matrix that matches the type of product being produced with the appropriate machine for that product.
The first step in implementing the Product Machine Matrix is to analyze the current production process and identify areas where improvements can be made. This can be done through the use of data and performance measurement tools, as well as by observing the process and gathering feedback from employees.
Once the areas for improvement have been identified, the next step is to determine the optimal machine for each type of product. This involves considering factors such as the complexity of the product, the volume of production, and the skill level of the operator. It may also be necessary to make changes to the existing machines or to purchase new equipment in order to meet the needs of the production process.
The Product Machine Matrix also requires the establishment of standard work procedures for each machine and product type. This helps to ensure that the production process is consistent and efficient, and it also provides a roadmap for continuous improvement. Standard work procedures should be regularly reviewed and updated based on performance data and feedback from employees.
Another important aspect of the Product Machine Matrix is the need for visual management. This involves creating clear and easy-to-understand visual aids, such as work instructions and flow charts, that help to guide employees through the production process. This helps to prevent errors and improve productivity, as well as making it easier for employees to quickly identify and resolve any issues that may arise.
To be effective, the Product Machine Matrix must be integrated into the overall culture of the organization. This requires the commitment and engagement of employees at all levels, as well as a focus on continuous improvement and a willingness to embrace change. Regular training and communication is also key to the success of the methodology, as it helps to build the necessary skills and knowledge, and ensures that everyone is working towards a common goal.
In a nutshell, the Product Machine Matrix is a powerful methodology that can be used to improve production processes in the manufacturing industry. By carefully matching the type of product with the appropriate machine, and by establishing standard work procedures and utilizing visual management techniques, organizations can achieve operational excellence and drive continuous improvement. With the right approach and commitment, this methodology can deliver significant benefits to any organization looking to optimize its production processes.
Inventory
Inventory is often viewed as a necessary evil, as it provides a safety net to ensure that products are available to meet customer demand.
Inventory is often viewed as a necessary evil, as it provides a safety net to ensure that products are available to meet customer demand. However, from the perspective of Lean Management, inventory can also be seen as a type of waste.
In Lean, waste is defined as anything that does not add value to the customer. From this perspective, inventory can be considered waste because it ties up valuable resources such as space, money, and time without providing any immediate value to the customer. This is because inventory requires storage, which takes up valuable space, and also requires investment in the products themselves. In addition, inventory can lead to obsolescence, as products may become outdated or go out of fashion before they can be sold. Furthermore, inventory can lead to inefficiencies in the supply chain, as products may sit on shelves for extended periods of time before they are sold, adding unnecessary time to the overall lead time.
Despite these challenges, inventory is also an essential component of most businesses. Inventory provides a safety net, ensuring that there are products available to meet customer demand even when there are disruptions in the supply chain. It also allows businesses to take advantage of bulk purchasing discounts, and to manage seasonal variations in demand.
So, how can Lean Management help businesses to steer inventory in the best direction? There are several key steps that can be taken to minimize the waste associated with inventory while still ensuring that the business has the products it needs to meet customer demand.
The first step is to implement a Lean production system. This involves using the principles of Lean Management to streamline production processes and reduce waste in all areas of the business, including inventory management. By reducing waste in the production process, it is possible to minimize the amount of inventory that is required, freeing up valuable resources for other areas of the business.
The second step is to implement a pull-based production system. This involves using customer demand as the driving force behind production, rather than using forecasted demand to determine production schedules. This can help to minimize inventory waste by ensuring that products are only produced when there is a genuine demand for them.
The third step is to implement just-in-time (JIT) inventory management. JIT is a Lean approach to inventory management that involves only ordering the products that are required to meet customer demand, and no more. This can help to minimize inventory waste by reducing the amount of product that is held in reserve, freeing up valuable resources such as space and money.
The fourth step is to implement a continuous improvement program. This involves regularly reviewing inventory levels and processes, and making changes where necessary to reduce waste and increase efficiency. This can help to ensure that inventory management processes are constantly evolving, and that the business is always adapting to changing customer demand.
In a nutshell, inventory management is an important aspect of any business, as it helps to ensure that the right products are available at the right time to meet customer demand. However, from the perspective of Lean Management, inventory can also be seen as a type of waste. By implementing a Lean production system, a pull-based production system, JIT inventory management, and a continuous improvement program, businesses can minimize the waste associated with inventory while still ensuring that they have the products they need to meet customer demand. By adopting these principles, businesses can increase efficiency, reduce costs, and improve overall customer satisfaction.
Standardization
Standardization is a vital aspect of a successful lean management strategy and can be defined as the process of establishing and maintaining common procedures and processes throughout the manufacturing organization.
Standardization is a key principle in lean manufacturing, which is focused on maximizing efficiency, minimizing waste, and continuously improving processes. It is a vital aspect of a successful lean management strategy and can be defined as the process of establishing and maintaining common procedures and processes throughout the manufacturing organization. This principle is based on the idea that standardization leads to improved productivity and a higher level of consistency in the production process.
A lean manufacturing expert knows the importance of standardization, as it helps to reduce variation and streamline processes, resulting in increased efficiency and improved quality. This is because standardization helps to eliminate inefficiencies, errors, and inconsistencies in the production process, allowing employees to focus on the tasks that are most important. This in turn leads to improved cycle times, reduced lead times, and increased customer satisfaction.
Standardization also helps to eliminate confusion and misunderstandings, as all employees are following the same procedures and processes. This makes it easier for employees to work together, as everyone is working from the same set of guidelines. This also makes it easier for management to train new employees, as they can be taught the standard procedures from the outset.
Standardization also helps to facilitate continuous improvement. By standardizing processes, it is easier to identify areas where improvement is needed, and changes can be made more easily. This is because employees are all working from the same set of guidelines, making it easier to see where improvements can be made and implement changes.
In order to effectively implement standardization in manufacturing, a Lean Management Expert would typically follow three steps:
Process Mapping: The first step is to map out the processes and procedures used in the manufacturing organization. This helps to identify areas where standardization can be implemented, and where improvements can be made.
Standardization: The second step is to develop and implement standardized procedures and processes. This involves working with employees to ensure that everyone is following the same procedures, and that they are understood by all.
Continuous Improvement: The final step is to continuously monitor and improve the standardization process. This involves regularly reviewing the procedures and processes to identify areas for improvement, and making changes as necessary to ensure that the standardization process remains effective.
In a nutshell, standardization is a key principle in lean manufacturing, and is essential for maximizing efficiency, minimizing waste, and continuously improving processes. By following the three steps outlined above, a Lean Management Expert can effectively implement standardization in their organization, leading to improved productivity, higher levels of consistency, and increased customer satisfaction.
Six Sigma
Six Sigma is a highly structured and data-driven methodology used in the manufacturing industry to improve quality and efficiency. Six Sigma offers a powerful toolset to help organizations achieve operational excellence and continuous improvement.
Six Sigma is a highly structured and data-driven methodology used in the manufacturing industry to improve quality and efficiency. Six Sigma offers a powerful toolset to help organizations achieve operational excellence and continuous improvement.
The primary goal of Six Sigma is to eliminate defects and minimize variability in processes, leading to improved customer satisfaction, reduced costs, and increased profitability. This is achieved through a combination of data analysis, statistical methods, and team-based problem-solving.
One of the key elements of Six Sigma is the DMAIC process, which stands for Define, Measure, Analyze, Improve, and Control. This process provides a systematic approach to solving problems and improving processes, starting with a clear definition of the problem, followed by the collection and analysis of data, and ending with the implementation of sustainable solutions.
Another key aspect of Six Sigma is the use of statistical tools and techniques to measure and improve process performance. This includes process mapping, hypothesis testing, design of experiments, and control charts, among others. Six Sigma also relies on a highly-skilled workforce, with individuals trained in statistical analysis and problem-solving techniques.
One of the key benefits of Six Sigma is its ability to drive continuous improvement. This is achieved through regular monitoring and measurement of processes, coupled with ongoing analysis and improvement efforts. Six Sigma provides organizations with a roadmap for sustained, data-driven improvement, helping to ensure that performance gains are maintained over the long-term.
In a nutshell, Six Sigma is a powerful tool in the arsenal of any Lean Management Expert. It provides organizations with a systematic approach to improving quality and efficiency, while also driving continuous improvement and driving long-term success. Whether you are looking to optimize a specific process, or seeking to drive broader organizational change, Six Sigma provides the methodology and tools to help you achieve your goals.
Annual Objectives
The use of annual objectives with 3 to 5 years breakthrough objectives is a crucial aspect of policy development in an organization.
The use of annual objectives with 3 to 5 years breakthrough objectives is a crucial aspect of policy development in an organization. This approach to setting goals allows an organization to balance both short-term and long-term objectives, ensuring that progress is being made towards both immediate and ultimate goals. In this article, an operational excellence expert will discuss the importance of this approach and the steps organizations can take to implement it effectively.
The first step in setting annual objectives with 3 to 5 years breakthrough objectives is to define the long-term vision of the organization. This vision should reflect the organization's ultimate goals and should be ambitious yet achievable. It should also align with the organization's mission and values, as well as the larger goals of the industry or sector in which it operates.
Once the long-term vision has been defined, the organization can begin setting its annual objectives. These objectives should be specific, measurable, achievable, relevant, and time-bound (SMART). They should also align with the long-term vision of the organization. For example, if the long-term vision is to become the leader in a particular market, an annual objective might be to increase market share by a certain percentage each year.
The next step is to set the 3 to 5 years breakthrough objectives. These objectives should be significant milestones that are critical to achieving the long-term vision. They should also be challenging, yet achievable, and should align with the annual objectives. For example, if the long-term vision is to become the leader in a particular market, a 3 to 5 years breakthrough objective might be to become the market leader in a particular geographic region.
Once the objectives have been set, the organization can develop a policy to support their achievement. This policy should include specific strategies and initiatives that will help the organization achieve its objectives. For example, the policy might include initiatives to improve product quality, increase customer satisfaction, reduce costs, or increase market share.
In order to effectively implement the policy, the organization must allocate resources appropriately. This includes allocating both financial and human resources, as well as the time and energy of key stakeholders. The organization must also establish a process for monitoring progress towards the objectives and for making adjustments as needed.
The use of annual objectives with 3 to 5 years breakthrough objectives can be a powerful tool for organizations that are seeking to improve their performance and achieve their goals. However, it is important to remember that this approach requires a significant investment of time and resources, as well as a commitment to ongoing improvement. Organizations that are willing to make this investment will be well-positioned to achieve their goals and create a bright future for themselves and their stakeholders.
In a nutshell, the use of annual objectives with 3 to 5 years breakthrough objectives is a crucial aspect of policy development in an organization. It allows organizations to balance both short-term and long-term objectives, ensuring that progress is being made towards both immediate and ultimate goals. By following the steps outlined in this article, organizations can effectively implement this approach and achieve their goals.
Cell Production
Cell Production focuses on optimizing the flow of work and improving efficiency in manufacturing and operations.
Cell Production focuses on optimizing the flow of work and improving efficiency in manufacturing and operations. It is based on the concept of organizing work into cells, which are self-contained units responsible for performing a specific set of tasks. The goal of cell production is to minimize waste, increase flexibility, and improve overall performance.
The origins of cell production can be traced back to the 1950s and 60s, when Toyota and other Japanese companies were experimenting with new approaches to manufacturing. Over time, the concept of cell production has evolved and been refined, and today it is widely used in a variety of industries, including automotive, electronics, and consumer goods.
In order to implement cell production effectively, there are several key steps that organizations must take. Firstly, it is important to conduct a thorough analysis of the current state of the manufacturing or operations process, in order to identify areas where improvements can be made. This may involve mapping out the flow of work and identifying bottlenecks or other inefficiencies.
Once these areas have been identified, the next step is to reorganize the work into cells, taking into account the specific requirements of each cell and the skills and expertise of the employees who will be working in them. This may involve rearranging physical work spaces, or changing the way that work is assigned and managed.
It is also important to establish clear communication and feedback mechanisms, so that employees and teams can work together effectively. This may involve setting up regular meetings to discuss performance, or implementing systems for tracking and reporting on key metrics.
In order to ensure a successful implementation of cell production, it is also important to provide training and support for employees. This may involve providing training on the new processes and procedures, or offering coaching and mentoring to help employees develop the skills and knowledge they need to be effective.
Another key aspect of cell production is continuous improvement. This involves regularly reviewing performance and making adjustments as needed, in order to optimize efficiency and reduce waste. This may involve experimenting with different approaches, such as implementing new technologies or streamlining processes, in order to find the best solutions.
In conclusion, cell production is a powerful methodology for optimizing performance in operations and manufacturing. By reorganizing work into cells, minimizing waste, and continuously improving performance, organizations can increase efficiency, reduce costs, and improve overall performance. In order to be successful, organizations must take a structured and systematic approach, and be committed to ongoing improvement.
Bullwhip Effect
The bullwhip effect is a well-known phenomenon in lean management that can have a significant impact on the push and pull principles of supply chain management.
The bullwhip effect is a well-known phenomenon that can have a significant impact on the push and pull principles of supply chain management. The bullwhip effect refers to the amplification of demand fluctuations as they move up the supply chain, leading to increased inventory, increased costs, and decreased customer satisfaction.
The bullwhip effect is caused by a number of factors, including demand forecast errors, order batching, price fluctuations, and the use of incentives that encourage suppliers to order more than they need. These factors can cause suppliers to overreact to demand changes, leading to excessive inventory levels and higher costs.
The impact of the bullwhip effect on the push and pull principles of supply chain management can be significant. The push principle is based on the idea that suppliers produce goods based on demand forecasts, and then push the goods to the customer. The bullwhip effect can cause demand forecasts to become less accurate, leading to increased inventory levels, increased costs, and decreased customer satisfaction.
The pull principle, on the other hand, is based on the idea that suppliers produce goods based on actual customer demand. The bullwhip effect can cause suppliers to overreact to demand changes, leading to increased inventory levels and higher costs. This can result in a situation where suppliers are producing goods that are not actually needed, leading to a decrease in customer satisfaction and increased waste.
To address the bullwhip effect, organizations can implement a number of strategies, including improving demand forecasting accuracy, reducing order batching, reducing price fluctuations, and using incentives that encourage suppliers to order what they need, when they need it.
One approach to reducing the bullwhip effect is to implement a demand-driven supply chain management system. This involves using real-time data to better understand customer demand, and using this information to make informed decisions about inventory levels and production schedules. This can help to reduce the bullwhip effect, leading to more accurate demand forecasts, lower inventory levels, and increased customer satisfaction.
Another strategy to address the bullwhip effect is to implement a lean supply chain management system. This involves reducing waste, streamlining processes, and improving communication and collaboration between suppliers, manufacturers, and customers. This can help to reduce the bullwhip effect, leading to improved supply chain efficiency, lower costs, and increased customer satisfaction.
In a nutshell, the bullwhip effect is a well-known phenomenon in lean management that can have a significant impact on the push and pull principles of supply chain management. To address the bullwhip effect, organizations can implement a number of strategies, including improving demand forecasting accuracy, reducing order batching, reducing price fluctuations, and using incentives that encourage suppliers to order what they need, when they need it. By implementing these strategies, organizations can reduce the bullwhip effect, leading to more accurate demand forecasts, lower inventory levels, and increased customer satisfaction.
Stay Connected
Ad
We want information fast and in a nutshell. We from OI recommend Blinkist* - because it’s simply the best.
* = Affiliate Link