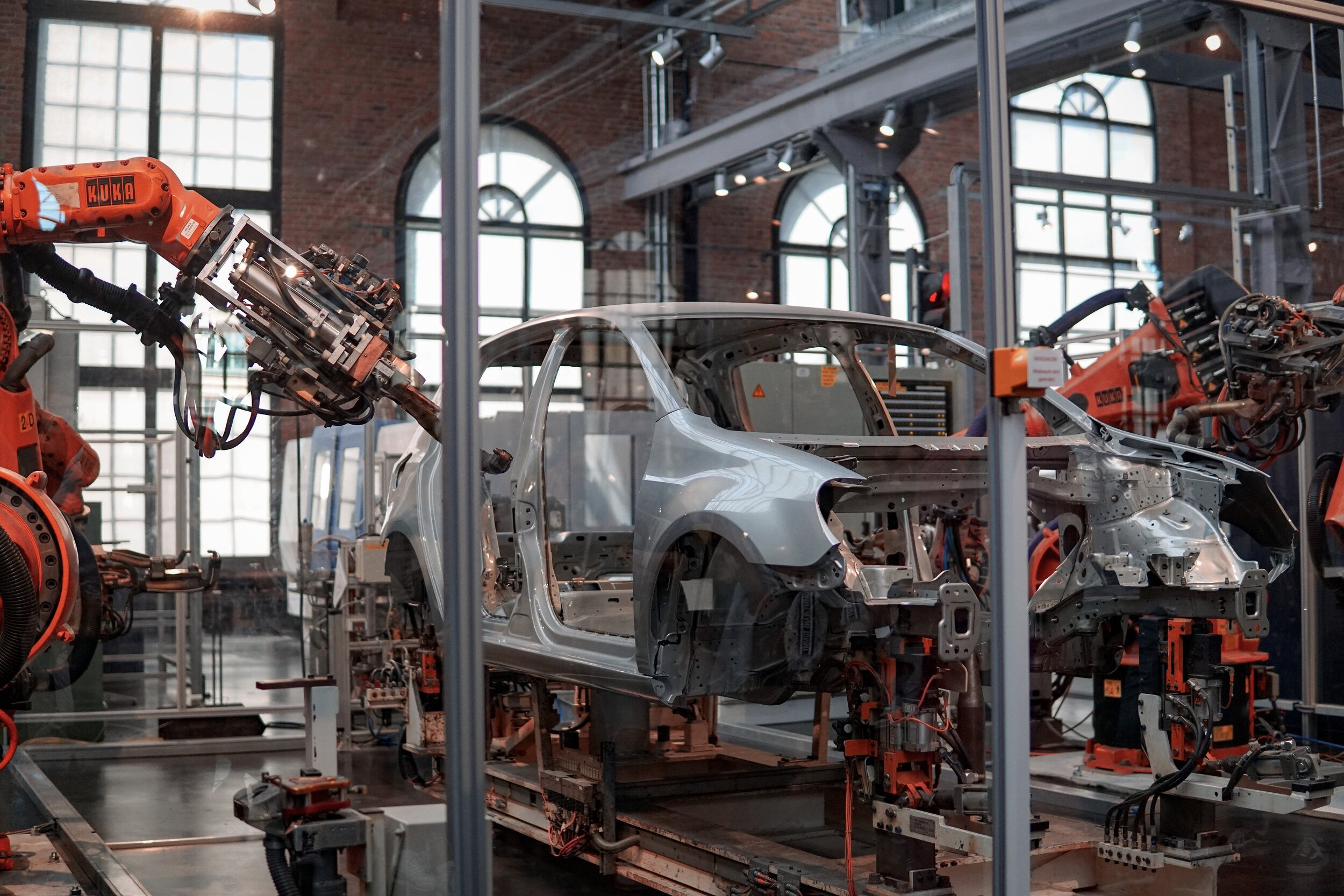
LANGUAGE OF LEAN
Mixed Model Production
We believe that MMP has the potential to bring significant benefits to a production line by increasing efficiency, reducing waste, and improving customer satisfaction.
Mixed Model Production (MMP) is a flexible production strategy that is gaining popularity in the manufacturing industry. We believe that MMP has the potential to bring significant benefits to a production line by increasing efficiency, reducing waste, and improving customer satisfaction.
Mixed Model Production is characterized by the simultaneous production of different models and variations of a product on the same production line. This approach is in contrast to the traditional practice of having a dedicated production line for each product type. In MMP, production is optimized by using a mix of products, models, and variations that can be produced on the same equipment, thereby reducing the need for changeovers, equipment downtime, and material waste.
One of the key benefits of MMP is increased production efficiency. By producing multiple products on the same production line, changeovers and downtime are minimized, reducing the time it takes to produce each product. This increased efficiency results in improved productivity, lower production costs, and higher customer satisfaction.
Another advantage of MMP is reduced waste. The production of multiple products on the same line results in a better utilization of resources and raw materials. This, in turn, reduces the amount of waste generated and the costs associated with waste disposal. Additionally, the reduced downtime results in less energy consumption and a more sustainable production process.
In MMP, the key to success is the ability to schedule production effectively. This requires a deep understanding of the production process, the equipment, and the capabilities of the workforce. A well-designed MMP strategy should be based on a detailed analysis of the production line and a comprehensive understanding of the production process.
The first step in implementing MMP is to identify the different products, models, and variations that can be produced on the same production line. This requires a thorough analysis of the production process and the equipment used. Once the different products have been identified, the next step is to determine the most efficient scheduling of production. This requires a detailed understanding of the production process and the equipment used, as well as the capabilities of the workforce.
The implementation of MMP requires a cross-functional approach that involves teams from different areas of the organization, including production, engineering, and logistics. The success of MMP depends on the collaboration and cooperation of these teams, as well as the effective communication of the MMP strategy to all stakeholders.
In a nutshell, Mixed Model Production is a flexible production strategy that has the potential to bring significant benefits to the manufacturing industry. As a Lean Management and Operational Excellence expert, I believe that MMP has the potential to increase production efficiency, reduce waste, and improve customer satisfaction. However, the success of MMP depends on a detailed understanding of the production process, the equipment, and the workforce, as well as a cross-functional approach that involves teams from different areas of the organization.
Point Of Use
Point of Use (POU) is a key component of Lean initiatives aimed at reducing waste, increasing efficiency, and improving overall production processes.
Point of Use (POU) is a key component of Lean initiatives aimed at reducing waste, increasing efficiency, and improving overall production processes. It is a philosophy that focuses on delivering materials, tools, and equipment directly to the worker at the moment they need them. The goal of POU is to minimize unnecessary movement, handling, and storage of materials, which not only streamlines production but also reduces the risk of damage, loss, and obsolescence.
In traditional manufacturing processes, raw materials and supplies are often stored in central locations, such as inventory rooms, and are retrieved and moved to the production line as needed. This can result in excess inventory, increased lead times, and the need for multiple trips to retrieve materials. Additionally, workers may spend significant amounts of time searching for the tools or materials they need, which reduces productivity and increases the risk of mistakes.
Point of Use aims to eliminate these inefficiencies by bringing materials and supplies directly to the worker at the point of need. This reduces the need for workers to search for materials and increases the speed and accuracy of the production process. POU also reduces the amount of inventory that needs to be stored and managed, which helps to reduce the risk of damage, loss, and obsolescence.
There are several different approaches to implementing POU, each with its own set of benefits and challenges. One approach is to use kanban systems, which are visual signals that tell workers when it’s time to replenish materials or supplies. Another approach is to use automated systems, such as conveyors or robots, which move materials and supplies directly to the production line as needed.
Regardless of the approach used, POU requires careful planning and coordination between all departments involved in the production process. It also requires regular monitoring and adjustments to ensure that the system is working as intended. This can include tracking key performance indicators (KPIs) such as inventory levels, production lead times, and worker productivity.
One of the benefits of POU is that it helps to improve worker morale and job satisfaction. When workers have access to the materials and supplies they need exactly when they need them, they are able to focus on their work without worrying about finding the right tools or supplies. Additionally, POU helps to eliminate the frustration that workers may feel when they are unable to find the materials they need, which can lead to decreased job satisfaction and even burnout.
Another benefit of POU is that it helps to reduce the risk of mistakes and increase quality. When workers have everything they need at their fingertips, they are able to focus on their work without worrying about searching for materials or supplies. This reduces the risk of errors, which in turn helps to improve overall quality and reduce the need for rework.
In a nutshell, Point of Use is an important concept in Lean Manufacturing that aims to reduce waste, increase efficiency, and improve overall production processes. By bringing materials and supplies directly to the worker at the point of need, POU streamlines production, reduces the risk of damage, loss, and obsolescence, and improves worker morale and job satisfaction. To be successful, POU requires careful planning, coordination, and monitoring, as well as a focus on continuous improvement. By implementing POU and other Lean principles, manufacturers can reduce costs, increase efficiency, and improve overall production outcomes.
MTM
MTM (Methods Time Measurement) is a systematic method for analyzing and optimizing work processes that is widely used in the field of Lean Management.
MTM (Methods Time Measurement) is a systematic method for analyzing and optimizing work processes that is widely used in the field of Lean Management. MTM is based on the idea of breaking down work into small, easily analyzed and optimized tasks, and is therefore an important tool for improving efficiency and productivity in operations.
The origin of MTM can be traced back to the early 20th century, when industrial engineers in Europe and the United States first began to develop time-and-motion studies. These early studies sought to identify the most efficient ways to perform tasks and reduce waste in manufacturing operations. Over time, MTM evolved into a standardized methodology, with clear guidelines and tools for process analysis and improvement.
One of the key features of MTM is its focus on standardizing work processes. This is accomplished by breaking down each task into its component parts and then determining the most efficient way to perform each part. The result of this analysis is a set of standardized work methods that can be used to train workers and ensure consistency in operations.
Another important aspect of MTM is its focus on continuous improvement. The MTM methodology includes regular reviews of work processes and the use of data and analysis to identify areas for improvement. This approach helps organizations to continuously improve their operations and remain competitive over time.
One of the best ways to utilize MTM is in the context of Lean management. In Lean, the focus is on identifying and eliminating waste in all aspects of operations. By applying the MTM methodology to work processes, organizations can identify inefficiencies and then work to eliminate them. This helps to create a more streamlined, efficient, and productive work environment.
Another important application of MTM is in the context of training and development. By using MTM to analyze and standardize work processes, organizations can provide clear and consistent training to workers. This helps to ensure that all workers are performing their tasks in the most efficient way, which leads to improved productivity and reduced waste.
Finally, MTM can also be used in the context of project management. By analyzing work processes in advance of a project, organizations can ensure that they have the resources and capabilities needed to complete the project on time and within budget.
In a nutshell, MTM is a powerful tool for improving efficiency and productivity in operations. Its focus on standardizing work processes and its emphasis on continuous improvement make it an ideal methodology for Lean management and for organizations looking to improve their operations over time.
Stay Connected
Ad
We want information fast and in a nutshell. We from OI recommend Blinkist* - because it’s simply the best.
* = Affiliate Link