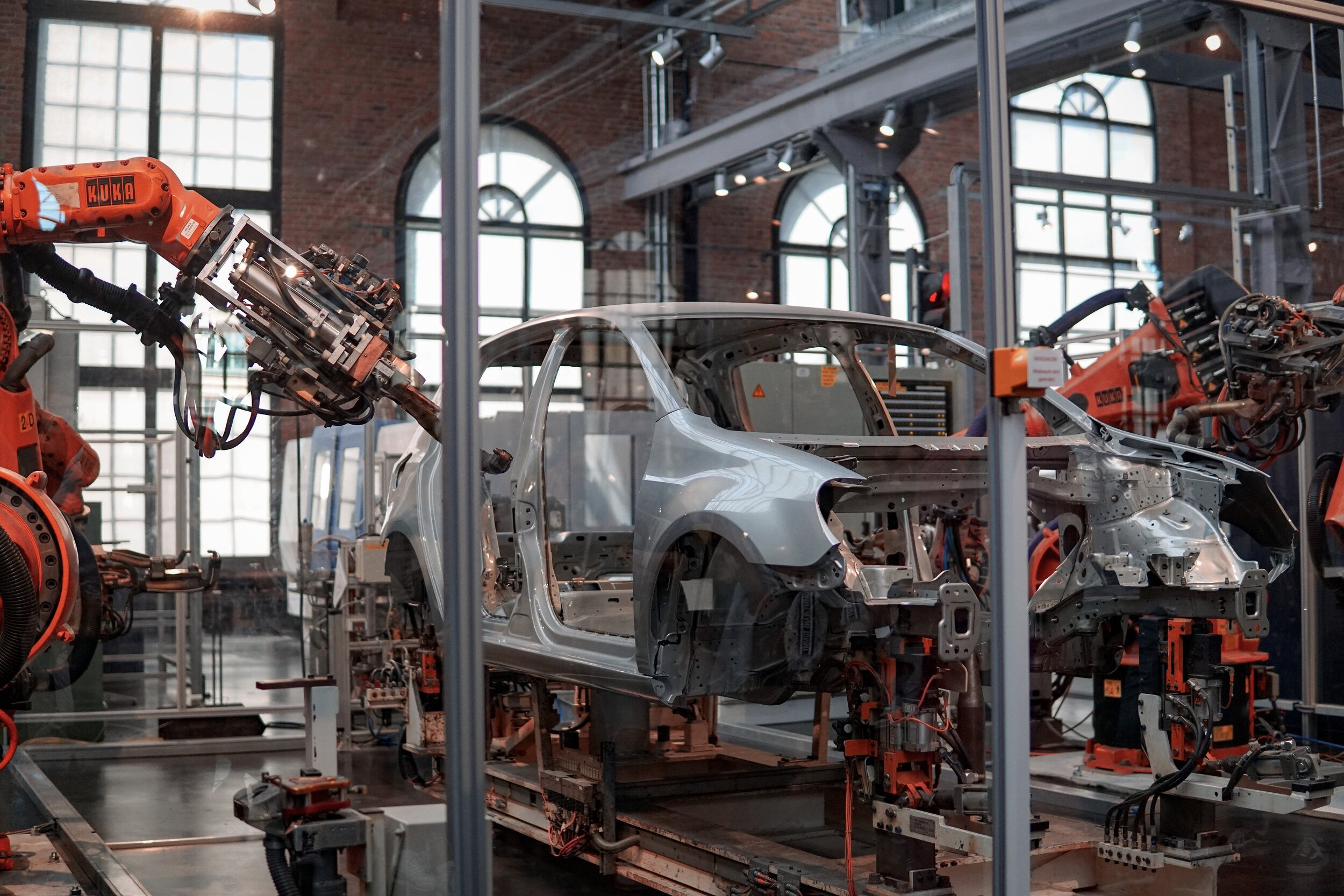
LANGUAGE OF LEAN
Point Of Use
Point of Use (POU) is a key component of Lean initiatives aimed at reducing waste, increasing efficiency, and improving overall production processes.
Point of Use (POU) is a key component of Lean initiatives aimed at reducing waste, increasing efficiency, and improving overall production processes. It is a philosophy that focuses on delivering materials, tools, and equipment directly to the worker at the moment they need them. The goal of POU is to minimize unnecessary movement, handling, and storage of materials, which not only streamlines production but also reduces the risk of damage, loss, and obsolescence.
In traditional manufacturing processes, raw materials and supplies are often stored in central locations, such as inventory rooms, and are retrieved and moved to the production line as needed. This can result in excess inventory, increased lead times, and the need for multiple trips to retrieve materials. Additionally, workers may spend significant amounts of time searching for the tools or materials they need, which reduces productivity and increases the risk of mistakes.
Point of Use aims to eliminate these inefficiencies by bringing materials and supplies directly to the worker at the point of need. This reduces the need for workers to search for materials and increases the speed and accuracy of the production process. POU also reduces the amount of inventory that needs to be stored and managed, which helps to reduce the risk of damage, loss, and obsolescence.
There are several different approaches to implementing POU, each with its own set of benefits and challenges. One approach is to use kanban systems, which are visual signals that tell workers when it’s time to replenish materials or supplies. Another approach is to use automated systems, such as conveyors or robots, which move materials and supplies directly to the production line as needed.
Regardless of the approach used, POU requires careful planning and coordination between all departments involved in the production process. It also requires regular monitoring and adjustments to ensure that the system is working as intended. This can include tracking key performance indicators (KPIs) such as inventory levels, production lead times, and worker productivity.
One of the benefits of POU is that it helps to improve worker morale and job satisfaction. When workers have access to the materials and supplies they need exactly when they need them, they are able to focus on their work without worrying about finding the right tools or supplies. Additionally, POU helps to eliminate the frustration that workers may feel when they are unable to find the materials they need, which can lead to decreased job satisfaction and even burnout.
Another benefit of POU is that it helps to reduce the risk of mistakes and increase quality. When workers have everything they need at their fingertips, they are able to focus on their work without worrying about searching for materials or supplies. This reduces the risk of errors, which in turn helps to improve overall quality and reduce the need for rework.
In a nutshell, Point of Use is an important concept in Lean Manufacturing that aims to reduce waste, increase efficiency, and improve overall production processes. By bringing materials and supplies directly to the worker at the point of need, POU streamlines production, reduces the risk of damage, loss, and obsolescence, and improves worker morale and job satisfaction. To be successful, POU requires careful planning, coordination, and monitoring, as well as a focus on continuous improvement. By implementing POU and other Lean principles, manufacturers can reduce costs, increase efficiency, and improve overall production outcomes.
Production Smoothing (Heijunka)
Production smoothing, also known as Heijunka, is a key aspect of modern operations management. It refers to the leveling of production to match customer demand, while maximizing efficiency and minimizing waste.
Production smoothing, also known as Heijunka, is a key aspect of modern operations management. It refers to the leveling of production to match customer demand, while maximizing efficiency and minimizing waste. This technique has been proven to be an effective way to manage production processes and increase competitiveness in the marketplace.
The objective of production smoothing is to create a steady flow of products and services, reducing the variability and fluctuations in the production process. This helps to minimize the waste and resources associated with overproduction, excess inventory, and bottlenecks in the production line. By leveling production, companies can better predict customer demand and adjust their production processes accordingly.
One of the primary benefits of production smoothing is the reduction of waste in the production process. By leveling production, it minimizes the need for excess inventory and eliminates the waste associated with overproduction. This helps to minimize the costs associated with storage, handling, and transportation of excess inventory, while improving overall efficiency.
Another advantage of production smoothing is the improvement of customer satisfaction. By better predicting and matching customer demand, companies can ensure that they have the right products and services available at the right time. This helps to build stronger relationships with customers and improves the overall perception of the company.
To implement production smoothing, companies must first understand their customer demand patterns and the production processes that support them. This requires a thorough analysis of the production line, including the identification of bottlenecks and areas of waste. The company should then develop a production plan that balances customer demand with the production processes to create a steady flow of goods and services.
The company should also implement effective communication and collaboration between all departments, including sales, marketing, engineering, and production. This helps to ensure that all processes are aligned and working together towards the common goal of production smoothing. The company should also consider the use of technology and equipment to automate the production process and improve efficiency.
It is also important to engage employees in the production smoothing process. By involving employees in the implementation and ongoing management of production smoothing, companies can tap into their expertise and insights, and build a culture of continuous improvement. Employees should also receive training and development opportunities to enhance their skills and knowledge in production smoothing techniques.
In a nutshell, production smoothing is an effective way to manage production processes and increase competitiveness in the marketplace. By reducing waste, improving customer satisfaction, and engaging employees, companies can create a steady flow of goods and services, and improve their overall production efficiency. By embracing this technique, companies can achieve operational excellence and maintain their competitive edge in the marketplace.
Stay Connected
Ad
We want information fast and in a nutshell. We from OI recommend Blinkist* - because it’s simply the best.
* = Affiliate Link