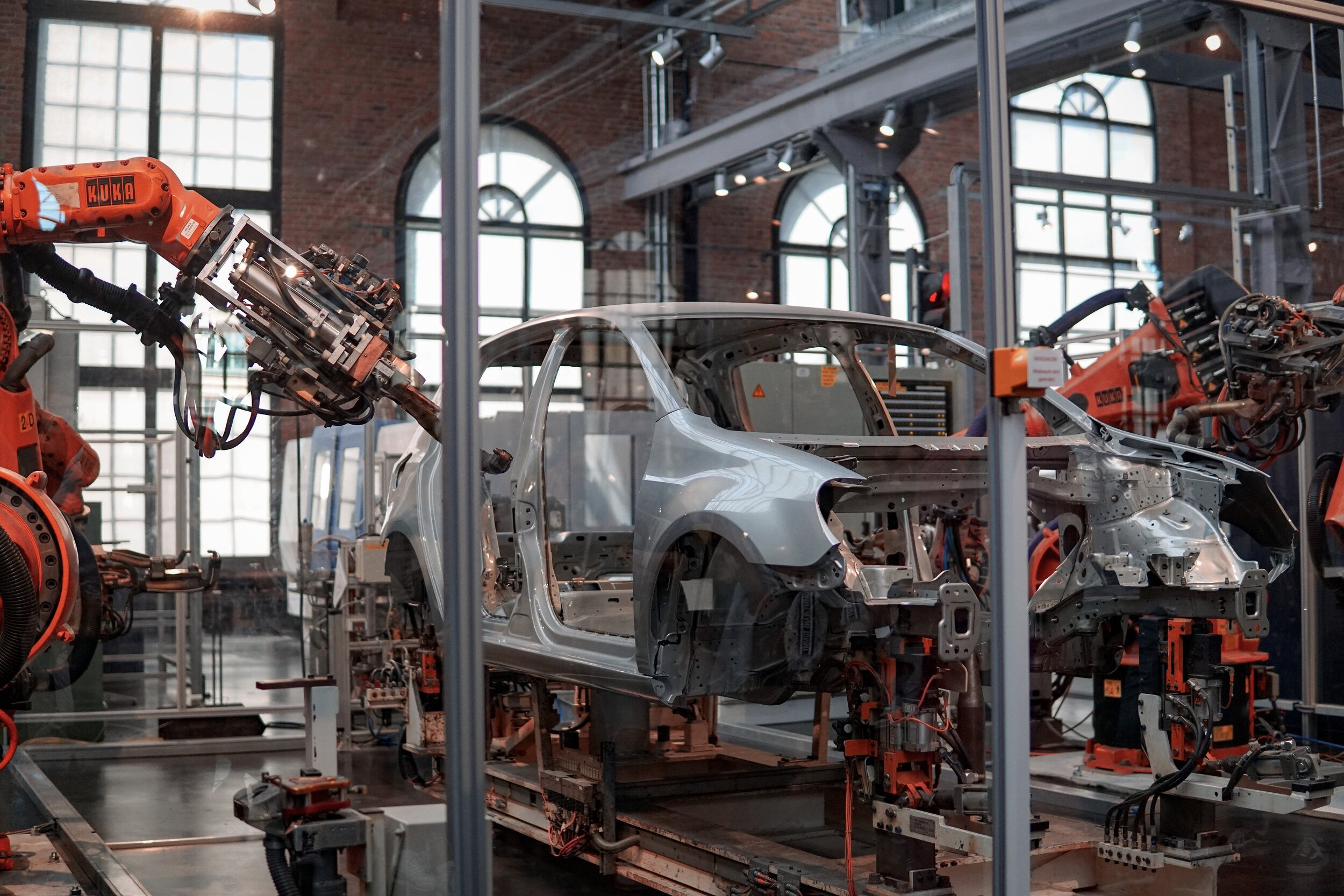
LANGUAGE OF LEAN
Rapid Improvement Event
Rapid Improvement Events, also known as Kaizen events, are a powerful tool for improving production processes in every industry.
Rapid Improvement Events, also known as Kaizen events, are a powerful tool for improving production processes in the manufacturing industry. They are focused, short-term initiatives aimed at solving specific problems and improving processes in a rapid and efficient manner.
At the heart of a Rapid Improvement Event is the involvement of a cross-functional team of employees, each bringing a unique perspective and skillset to the table. The team works together to identify and solve problems, test new ideas, and implement solutions that can have an immediate impact on the production process.
One of the key benefits of Rapid Improvement Events is the speed with which they can deliver results. By focusing on a specific problem and working together as a team, significant improvements can be made in just a few days or weeks. This can be especially valuable in the manufacturing industry, where time is often of the essence and even small improvements can make a big difference.
To ensure the success of a Rapid Improvement Event, it's important to follow a structured methodology. This typically includes the following steps:
Define the problem and scope of the event. What is the specific issue that needs to be addressed, and what is the desired outcome of the event?
Assemble the cross-functional team. Choose team members who have a strong understanding of the problem and can bring a variety of skills and perspectives to the table.
Conduct a thorough analysis of the problem. Gather data, observe processes, and engage in root cause analysis to understand the underlying cause of the problem.
Develop and implement a plan of action. Based on the findings of the analysis, create a plan of action that addresses the root cause of the problem and implements solutions that will improve the production process.
Implement and monitor the changes. Once the plan of action is in place, implement the changes and monitor the results to ensure they are having the desired impact.
Reflect and celebrate successes. Reflect on the successes of the event and celebrate the improvements that were made.
Rapid Improvement Events are a powerful tool for improving production processes in the manufacturing industry. By bringing together a cross-functional team, focusing on a specific problem, and following a structured methodology, organizations can achieve significant improvements in a short amount of time.
In a nutshell, it is important to embrace a continuous improvement mindset and actively seek out opportunities to improve production processes. Rapid Improvement Events provide a structured and efficient way to do just that, delivering results that can have a lasting impact on an organization's success.
Standard Work
Standard work is a fundamental principle of Lean manufacturing, a management philosophy that focuses on the elimination of waste and the continuous improvement of processes in order to increase efficiency, quality, and customer satisfaction.
Standard work is a fundamental principle of Lean manufacturing, a management philosophy that focuses on the elimination of waste and the continuous improvement of processes in order to increase efficiency, quality, and customer satisfaction. From the perspective of a Lean management expert, standard work is an essential tool for achieving operational excellence in the manufacturing industry.
Standard work refers to the detailed documentation of the best way to perform a specific task, taking into account factors such as the skills and experience of the workers, the equipment and materials used, and the desired outcome. This documentation should include step-by-step instructions, visual aids, and clear specifications for each step of the process. The goal of standard work is to ensure that each task is performed consistently and to the highest standard possible, regardless of who is performing it or when it is performed.
There are several key benefits to implementing standard work in manufacturing. Firstly, standard work helps to increase efficiency by eliminating waste and reducing variability in the production process. This leads to shorter lead times, lower costs, and improved quality. Secondly, standard work provides a clear understanding of the expected outcome of each task, making it easier for workers to know what is expected of them and to continuously improve their performance. Thirdly, standard work helps to promote a culture of continuous improvement by empowering workers to identify opportunities for improvement and to suggest changes to the standard work documentation.
To implement standard work effectively, Lean management experts typically follow a five-step process:
Define the task: Clearly define what needs to be accomplished and what the desired outcome is.
Observe and document the current process: Observe the current process, and document each step, including the time taken for each step and any variation in the process.
Determine the standard work: Analyze the data from the observation and determine the best way to perform the task, taking into account the skills and experience of the workers, the equipment and materials used, and the desired outcome.
Train the workers: Train the workers on the standard work and ensure that they understand the expectations and how to perform the task to the standard.
Continuously improve: Regularly review the standard work and identify opportunities for improvement.
In addition to the five-step process, Lean management experts also recommend the following ten tips for a successful implementation of standard work:
Start with a few simple tasks and gradually expand the implementation to other areas of the organization.
Engage the workers in the implementation process and involve them in the development of the standard work.
Focus on standardizing the process, not the workers.
Use visual aids, such as flow charts, to help the workers understand the standard work.
Regularly review and update the standard work to reflect changes in the process, the workers, or the equipment.
Foster a culture of continuous improvement by encouraging workers to suggest changes to the standard work.
Make standard work a part of the performance evaluation process for workers.
Use standard work as a tool for training new workers.
Use standard work to identify opportunities for process improvement.
Regularly communicate the importance of standard work and the benefits of implementing it.
In a nutshell, standard work is a powerful tool for achieving operational excellence in the manufacturing industry. From the perspective of a Lean management expert, standard work helps to increase efficiency, improve quality, and empower workers to continuously improve their performance. By following the five-step process and the ten tips for a successful implementation, organizations can reap the benefits of standard work and achieve their operational excellence goals.
Stay Connected
Ad
We want information fast and in a nutshell. We from OI recommend Blinkist* - because it’s simply the best.
* = Affiliate Link