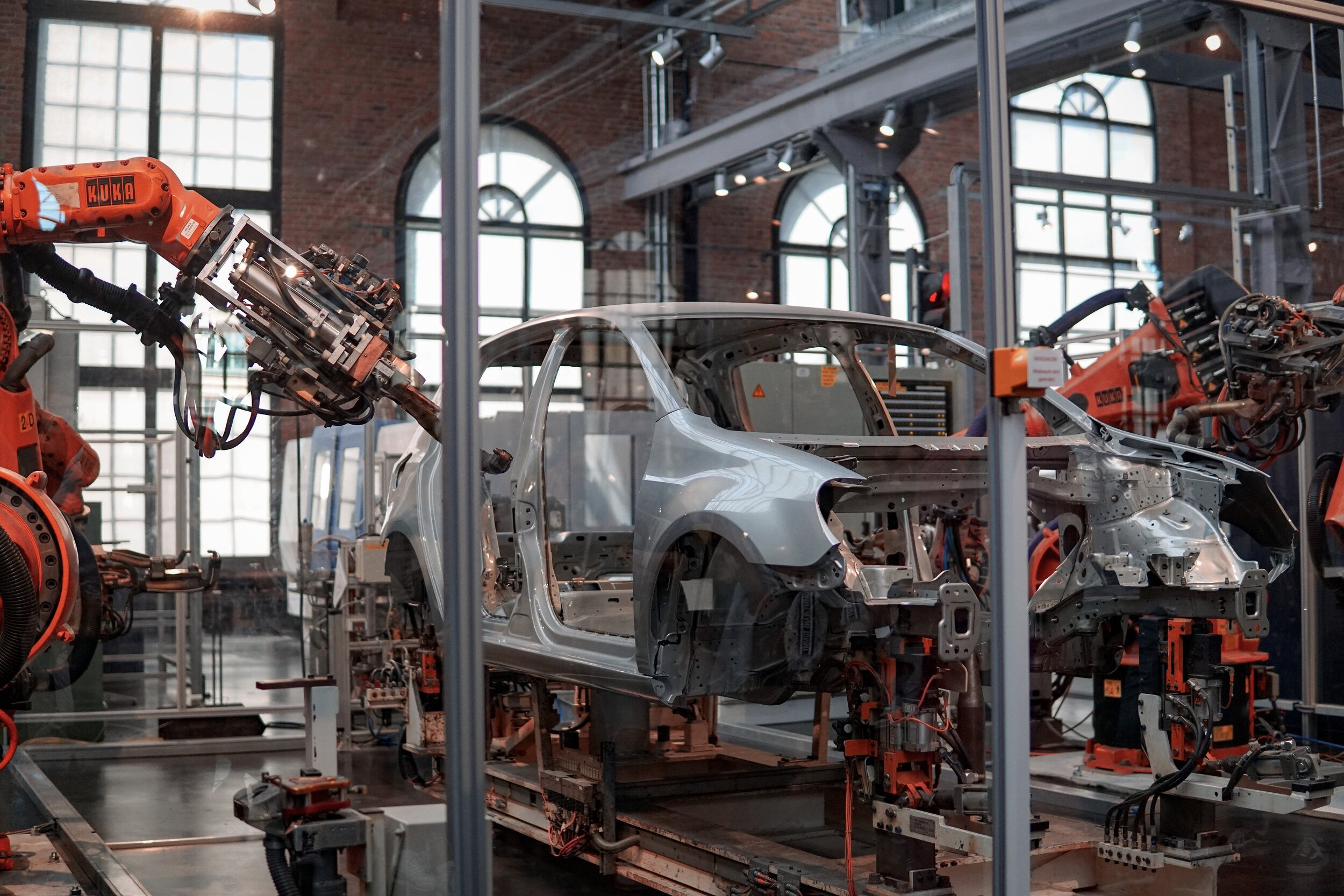
LANGUAGE OF LEAN
SMED
Single Minute Exchange of Die. A method of increasing the amount of productive time and to reduce the planned downtime to single digit minutes.
Single Minute Exchange of a Die
This series of techniques was invented by Shigeo Shingo to set-up manufacturing equipment in less than 10 minutes. Most of the time people think in one minute but is thought as single digit minutes.
So what is behind the set-up time reduction?
This method is driving to increase the net production time as much as possible by minimizing the needed time to change from one model to another. As far as you have two or more products running on your line or to simply exchange parts of your machine or equipment that regularly needs to be replaced. This is increasing the flexibility of your production and allows you to react on changes in demand more quickly.
When trying to reduce changeover tomes the typical goal is to reach less than 10 minutes. The short summary of SMED activities is to analyze each element of the changeover with the EMIPS method to see if it can be eliminated, modified or moved outside the process, integrated, tasks are parallelized or synchronized.
SMED
When looking at those three stages we can simplify it further for each stage:
Just ask yourself:
Separate:
Can this task, as currently performed, be done while the line is still running?
Convert:
Which process steps can be moved out of the changeover itself and be parallelized or completely taken out? How can you do it?
Synchronize:
How can the remaining tasks be synchronized so you need as little time as possible to complete the changeover?
I save you the story with the pit stop in formula 1 - just google it by yourself and you will find the evolution of pit stops. Quite interesting and still valuable.
So what are the benefits of SMED?
The first effect you will see on improvements of the OEE of your manufacturing facility. If this is important for you and you are numbers driven. In the end you will reduce downtimes and therefore manufacturing costs as your machines will have a greater net operating time.
With a long term perspective SMED will enable you to have smaller batch sizes, which will improve your possibilities to react faster on changes of customer demands and in addition your inventory (tied capital) and WIP (work in progress) will decrease.
Stay Connected
Ad
We want information fast and in a nutshell. We from OI recommend Blinkist* - because it’s simply the best.
* = Affiliate Link
In a world where leadership often equates to tough exteriors and unyielding authority, "Dare to Lead: Brave Work. Tough Conversations. Whole Hearts." stands as a beacon of hope and transformation.
In the realm of business literature, few books tackle the unglamorous, gritty realities of leading a company through turbulent times. "The Hard Thing About Hard Things: Building a Business When There Are No Easy Answers" by Ben Horowitz does just that.
Why does Emotional Intelligence (EQ) matter, and in what ways can it impact our lives more significantly than IQ? In "Emotional Intelligence: Why It Can Matter More Than IQ," Daniel Goleman introduces a groundbreaking argument that our emotional abilities can be more powerful than our measured intelligence.
Why do some organizations succeed in inspiring action, both internally among employees and externally among consumers, while others falter? "Start with Why: How Great Leaders Inspire Everyone to Take Action" by Simon Sinek
"How to Win Friends and Influence People" is one of the quintessential self-help books, penned by Dale Carnegie in 1936, yet its teachings remain relevant today.
"The Fifth Discipline: The Art & Practice of The Learning Organization" by Peter M. Senge is a pioneering book that introduced the idea of a "learning organization."
In "Side Hustle: From Idea to Income in 27 Days," Guillebeau outlines a step-by-step plan for anyone looking to create an additional income stream without quitting their day job.
"The $100 Startup: Fire Your Boss, Do What You Love and Work Better To Live More" is a compelling narrative that inspires readers to turn their passions into income.
"How to Grow Your Small Business: A 6-Step Plan to Help Your Business Take Off" is an insightful guide that provides a clear roadmap for small business owners looking to grow and expand their operations.
"The First Minute: How to Start Conversations That Get Results" focuses on the importance of the first minute in any conversation.
"The Almanack of Naval Ravikant: A Guide to Wealth and Happiness" is a compilation of Naval Ravikant's wisdom and experience from the last ten years.
"Ikigai: The Japanese Secret to a Long and Happy Life" takes the reader on a journey to explore the concept of Ikigai, a term that translates loosely as 'reason for being.'
"The Courage To Be Disliked" by Fumitake Koga and Ichiro Kishimi is a thought-provoking book that presents a dialogue between a philosopher and a young man, discussing the principles of Adlerian psychology.
"Talk Like TED" by Carmine Gallo is a powerful guide that reveals the secrets of delivering engaging and impactful presentations.
"I Will Teach You to Be Rich: No Guilt. No Excuses. No BS. Just a 6-Week Program That Works" is a personal finance book written by Ramit Sethi.
"Nudge: Improving Decisions About Health, Wealth, and Happiness" by Richard H. Thaler and Cass R. Sunstein is a groundbreaking book that explores the concept of "nudging" and how small changes in the way choices are presented can have a significant impact on decision-making.
"The E-Myth Revisited: Why Most Small Businesses Don't Work and What to Do About It" by Michael E. Gerber is a compelling book that explores the common pitfalls and misconceptions surrounding small businesses.
The book "4-Hour Body: An Uncommon Guide to Rapid Fat-Loss, Incredible Sex, and Becoming Superhuman" by Timothy Ferriss is a comprehensive guide to optimizing various aspects of your body and life.
"Never Finished: Unshackle Your Mind and Win the War Within" by David Goggins is a powerful and inspiring book that explores the concept of pushing past your limits and overcoming mental barriers to achieve greatness.
"The Business of the 21st Century" by Robert Kiyosaki is a book that explores the changing landscape of business in the modern era.
"Man's Search for Meaning: The Classic Tribute to Hope from the Holocaust" by Viktor E. Frankl is a powerful memoir that delves into the human search for meaning in the midst of extreme suffering.
"How to Be a Stoic: Using Ancient Philosophy to Live a Modern Life" by Massimo Pigliucci is a thought-provoking book that explores the principles of Stoicism and how they can be applied to navigate the challenges of modern life.
"Deep Work: Rules for Focused Success in a Distracted World" by Cal Newport is a compelling book that explores the value of deep work and provides practical strategies for achieving it in our increasingly distracted world.
In this book, Covey emphasizes the importance of developing a strong set of principles that will guide and govern our personal and professional lives.
"Who Moved My Cheese?" is a classic self-help book written by Dr. Spencer Johnson. The book is a parable that teaches readers to cope with change and navigate uncertain times.
"The Goal" is a business novel written by Israeli physicist Eliyahu M. Goldratt, first published in 1984. The book follows the protagonist, plant manager Alex Rogo, as he seeks to improve the performance of his struggling manufacturing plant while dealing with personal and professional challenges.
"The 4-Hour Work Week" is a self-help book written by entrepreneur and podcaster Tim Ferriss.
"The Power of Full Engagement" is a book written by Jim Loehr and Tony Schwartz that challenges the conventional notion of time management.
In "The Effective Executive," Drucker shares his insights on what makes a successful executive and provides practical advice on how to become one.