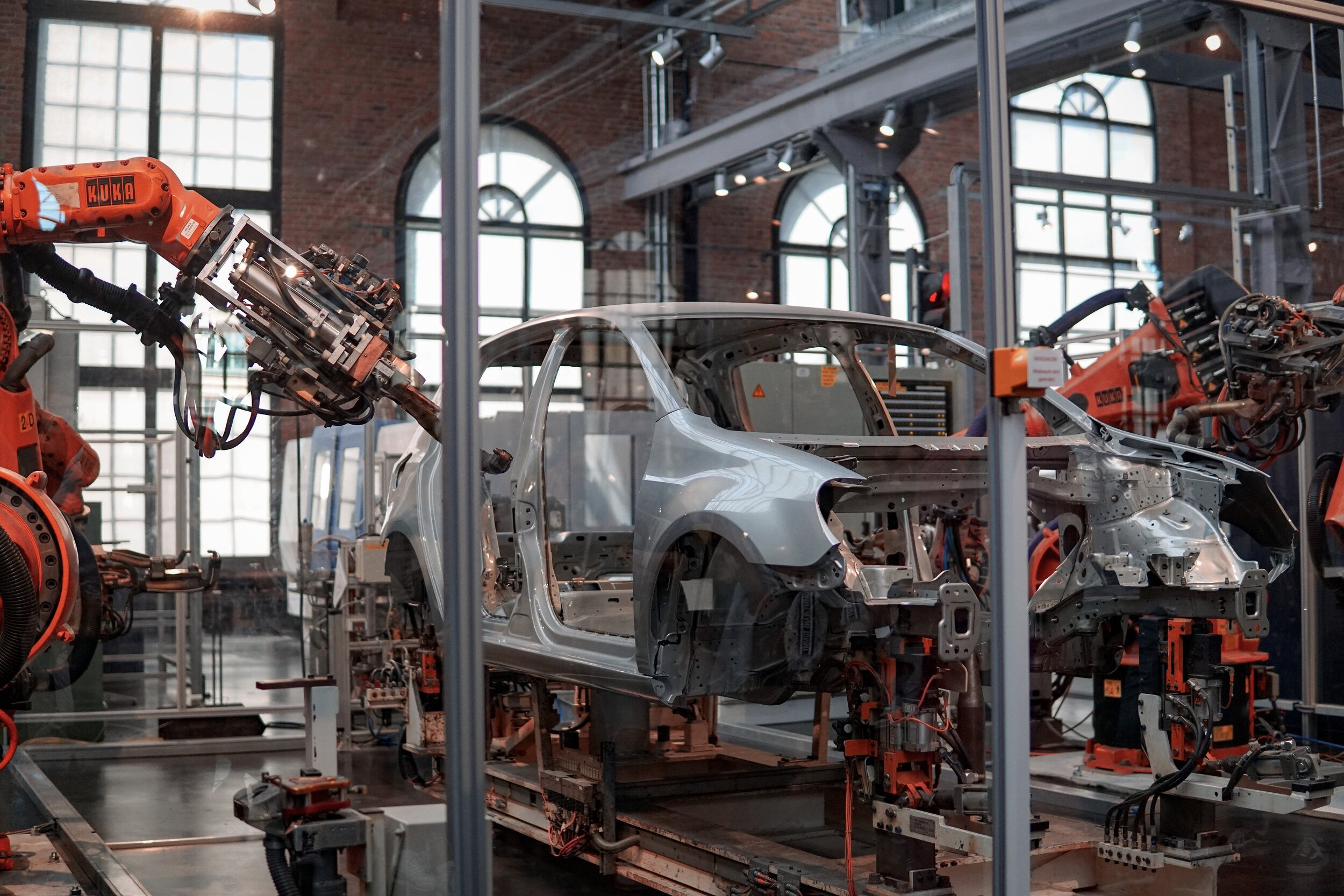
LANGUAGE OF LEAN
MUDA
Read and learn about the 7 kinds of waste.
MUDA – Also see Timwood
In this article we want to talk about MUDA or the 7 kinds of waste known as TIMWOOD.
The seven kinds of waste have to be discovered and eliminated in daily operations. Therefore we will be looking at the 7 kinds of waste and learn how to use appropriate lean tools to reduce these non value-adding activities.
First of all use Gemba Walks to find out more about whats happening on the shop floor. Only through the on-site inspection you can see what is really going on. It is simply not possible to record the types of waste in the conference room at the green table. The CIP Kaizen action on site is always necessary to reduce waste.
When talking about production the ultimate goal is to increase value-creating activities in the complete organization and not to reduce them. Therefore non-value-adding activities are called MUDA - Japanese for wasteful.
Overview of the 7 kinds of waste and the lean approach to avoid these
The individual parts of muda are easily remembered with a simple mnemonic aid called TIMWOOD. TIMWOOD stands for the first letters of the several kinds of waste. Lets have a look at those and some hints what it means:
T = Transport
Material flow
Product-/Value-/Process orientation
Just in Time material supply of workstations
Pull steering of production with the Kanban principle
I = Inventory
Just in Time or Just in Sequence material supply
Pull steering of production with the Kanban principle
Takt time
Linking suppliers
Reduction of batch sizes or production lots
Implementation of One Piece Flow principle
M = Motion
6 S principle
Standardization
Fixed allocated spaces
Shortest ways
W = Waiting
Multi machining
Multi process handling
Material flow in U-shaped manufacturing lines
Implementation of SMED
Installation of Andon Boards
O = Overproduction
Leveling of manufacturing orders
Mixed-Model-Production
One-Piece-Flow
O = Overprocessing/-engineering
Processes are not necessary
Kaizen activities
Quality circle
Idea Management
Reduction of complexity
Reduction of components needed
Reduction of unnecessary process steps
Reduction of hand overs and quality loops
D = Defects
Reduction of scrap rate or rework
Internal customer supplier management
Self-inspection
Poka Yoke principle
Automation
Zero Defects principle
Stop the line authority
5S activities as part of the standard work
Visual Management and visual aids
S = Unutilized Staff
Idea Mgt.
Shop Floor Mgt.
Lean Innovation
Each of the individual elements of the 7 kinds of waste often interact with each other. If you think about your organization as a system, it is necessary to classify not only one characteristics. An approach can only be derived when several classifications of waste have been analyzed.
The 3 MUDA expressions
With the individual process sections and activities and the corresponding 7 kinds of waste, they can be divided into the following activities:
Value Adding Activities
Kanji Muda - Waste in terms of machinery and equipment
Hiragana Muda - Work that needs to be done in order to fulfill the task but not really add value
Katakana Muda - Everything not needed
All this combined is your total workflow
As seen in real life up to 75% of non-optimized processes are non-value-adding activities which means they are pure waste and eat up your resources. Therefore it always makes sense to eliminate each of the 7 kinds of waste in order to increase productivity. To get an idea see the following picture:
Katakana Muda (red - waste that can be eliminated immediately)
Waiting
Searching
Filling
Double work
Stacking of components
Kanji Muda (gray and yellow - waste based on machines and equipment)
Machinery movement without any function
Oversized machines that can produce more than the required parts during the cycle time
Hiragan muda (green - work that is necessary for the provision of services under the current conditions; value-adding process steps)
Return to starting position
Cleaning
Tightening
Manual operation of machines
So how to recognize and eliminate the 7 kinds of waste?
Muda can always only be detected at the place of action. Therefore Gemba Walks are the best way to go on the search. But one thing has to be clear - it does not have to be always big projects to reduce waste. Continuous Improvement is key - recurring CIP or Kaizen activities are very supportive to develop an eye for the 7 kinds of waste. Training makes masters.
Second - it doesn’t has to be expensive. Most actions can be implemented at low cost. E.g. make a spaghetti plot to visualize and recognize obvious unnecessary movements.
Third - always have an eye on the value-adding activities. With a trained eye from GEMBA WALKS you will have improved awareness of waste already in the planing phase of new processes. Use those lessons learned and avoid waste in the beginning.
We don’t want to go into details but there are two other types of losses that can be witnessed in an organization. Mura meaning deviation and muri meaning overload (man, machine, material equally). If you want to read more about these, have a look here.
Let us come to an end - even when it is hard, we could keep going on and on…
But some rules:
No excuses!
Be creative in first place - money always comes second
Never try to explain why something doesn't work, try how it works!
Adjustments kills your time and ambitions. Adjustment means to fight the symptoms not the root cause!
Do not worry about problems that do not yet exist.
Happy Improving!
Stay Connected
Ad
We want information fast and in a nutshell. We from OI recommend Blinkist* - because it’s simply the best.
* = Affiliate Link