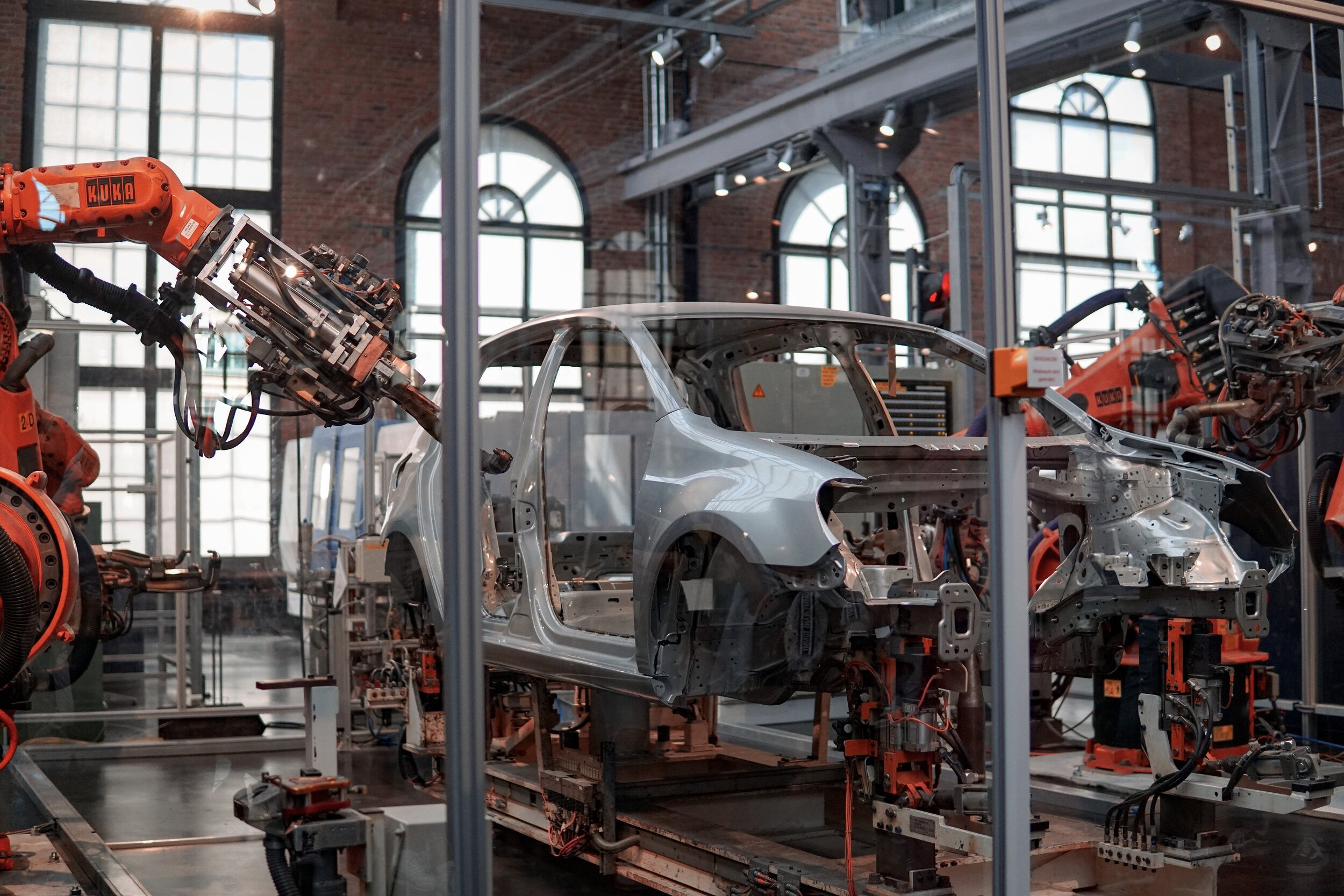
LANGUAGE OF LEAN
Rapid Improvement Event
Rapid Improvement Events, also known as Kaizen events, are a powerful tool for improving production processes in every industry.
Rapid Improvement Events, also known as Kaizen events, are a powerful tool for improving production processes in the manufacturing industry. They are focused, short-term initiatives aimed at solving specific problems and improving processes in a rapid and efficient manner.
At the heart of a Rapid Improvement Event is the involvement of a cross-functional team of employees, each bringing a unique perspective and skillset to the table. The team works together to identify and solve problems, test new ideas, and implement solutions that can have an immediate impact on the production process.
One of the key benefits of Rapid Improvement Events is the speed with which they can deliver results. By focusing on a specific problem and working together as a team, significant improvements can be made in just a few days or weeks. This can be especially valuable in the manufacturing industry, where time is often of the essence and even small improvements can make a big difference.
To ensure the success of a Rapid Improvement Event, it's important to follow a structured methodology. This typically includes the following steps:
Define the problem and scope of the event. What is the specific issue that needs to be addressed, and what is the desired outcome of the event?
Assemble the cross-functional team. Choose team members who have a strong understanding of the problem and can bring a variety of skills and perspectives to the table.
Conduct a thorough analysis of the problem. Gather data, observe processes, and engage in root cause analysis to understand the underlying cause of the problem.
Develop and implement a plan of action. Based on the findings of the analysis, create a plan of action that addresses the root cause of the problem and implements solutions that will improve the production process.
Implement and monitor the changes. Once the plan of action is in place, implement the changes and monitor the results to ensure they are having the desired impact.
Reflect and celebrate successes. Reflect on the successes of the event and celebrate the improvements that were made.
Rapid Improvement Events are a powerful tool for improving production processes in the manufacturing industry. By bringing together a cross-functional team, focusing on a specific problem, and following a structured methodology, organizations can achieve significant improvements in a short amount of time.
In a nutshell, it is important to embrace a continuous improvement mindset and actively seek out opportunities to improve production processes. Rapid Improvement Events provide a structured and efficient way to do just that, delivering results that can have a lasting impact on an organization's success.
Kanban
The material in the Kanban System is exclusively oriented to the consumption of your production process.
In this article we want to talk about another classic from Lean Management Kanban or the so called Pull System.
The word Kanban itself has its roots in the Chinese Japanese language and means card, label or sticker. In industrial manufacturing planning systems or general in logistics control Kanban describes a replenishment system for consumed parts according to the amount used steered by cards that give the signal following the Pull Principle.
The material in the Kanban System is exclusively oriented to the consumption of your production process. The cards are a key element of this kind of control system and provide proper information transfer. Kanban control loops from the work station of flexible production control and serves to smooth material flow through your inbound or even outbound logistics. In addition Kanban serves you to implement a sustainable reduction of material stocks, increases the ability to deliver and saves you pure cash.
In an ideal world Kanban would control your entire value chain from the supplier to the end customer. In this way you would have installed an complete smooth supply chain with almost no chance of interruption and massive stocks. And now comes the but – to steer production with Kanban – a continuous monitoring is required for a smooth material supply. To make it short: it requires discipline from all involved parties along the supply chain.
Lets have a look to the development of Kanban.
The first Kanban System was developed by none other than Taiici Ohno (of course) at Toyota Motor in the 1940s. One of the main reasons for the implementation of Kanban was the low productivity and efficiency of Toyota compared to western competitors. With the Kanban System, Toyota achieved a significant change towards flexible and efficient production control that had a massive impact on productions output while at the same time reducing the costs for inventory in raw material, work in progress (WIP) and finished goods.
To give the complete picture it wasn’t implementing the Kanban system itself to drive the success of Toyota, there are other key factors that together where making the difference. Just to name Just in time as an example of key elements of the Toyota Production System. It is and always will be a combination of different methods and philosophy that brings you forward.
In the 1970s the Kanban Concept was adapted in the industry in the USA and Germany. As they haven’t known better, they pretty much copied the complete Toyota Production System (TPS) in order to get the principles running.
Pull or Kanban System
Either way you call it, the material flow is controlled by boxes or cards. Kanban Cards serving in a simple way all information needed to identify what parts are needed in what quantity at what place. The amount typically is defined by the replenishment time at the work station. With the so called two box principle you make sure that the operator never runs short on components. Nowadays there are also digital version of it called eKanban, but the principle behind is the same. The trigger of supply is the Kanban Card starting of the pull chain of material.
To use Kanban efficient, it is not suitable for all parts. Kanban is perfect for small parts with a small amount of variants and a consistent demand. For this reason, you’ll see Kanban Systems in the industry mostly used for C-Parts management. The rest of the components are steered with the support of MRP. Only in rare cases you find that even the supply of big components are controlled with the Kanban methodology.
One nice side effect with Kanban, you can set up the way you can steer your bottleneck. That means, when you have done a proper value stream analysis you know the capacity for your bottleneck and will only order what this process step can handle.
Poka Yoke
Poka Yoke are all mechanisms that prevent unplanned mistakes from happening.
Poka-Yoke is any mechanism that helps to avoid unplanned mistakes. Poka-Yoke is that the application of straightforward, error-proof mechanisms to systematically avoid incorrect assembly, mix-ups or the downstream movement of defective parts. As a result of stable and high-quality methods begin long before the assembly section, simple Poka-Yoke measures will be enforced preventively within the construction and coming up with phase to make sure quality. Poka-Yoke is implemented to avoid: going away out or forgetting process steps, process or operational-related mistakes, incorrect or missing parts, setup or installation errors.
POKA YOKE ポカヨケ ("stupid mistakes - avoidance") is associate ideology that takes a spread of approaches to optimize production processes, particularly assembly. The main target of Poka-Yoke is strive for zero-defect production and to attain it approximately. If defects are detected, the cause is determined. If the cause can be avoided, it's eliminated pretty much as good as doable within the sense of Poka-Yoke and at the best doesn't occur again at all. Poka-Yoke was originally an initiative of Dr. Shingo, Shigeo (新郷 重夫), who is additionally a co-founder of the Toyota production system, of that Poka-Yoke is a core component. Poka-Yoke is beneath the umbrella of Kaizen 改善 ("continuous improvement for the better").
Poka-Yoke may be about recognizing the root causes in time and so eliminating them. Mistakes shouldn't solely be corrected, however prevented the in the longterm by eliminating their root causes. Within the ideal case, in the sense of Poka-Yoke, there are measures that utterly rule out a discovered error by eliminating the cause in the future, e.g. as a result of incorrect mounting is not any longer doable because of fixed given mounting ways (e.g. fitting shapes). Poka-Yoke demands product style ability to make a product design that forestalls errors (avoid incorrect operation) and is powerful against errors (despite incorrect operation no faulty processes). Thus the philosophy of Poka-Yoke doesn't solely begin within the production, however already in the product design.
A widely known everyday example is that the plug of the electric devices and the power outlets, that can't be inserted into the socket the incorrect way round. Measuring instruments may also be designed or programmed in such a way that they will not be misused. Poka-Yoke principles can also be found in other cases, e.g. ATMs dispense your credit card before the payout takes place. Fuel dispenser faucets solely work into the right tank for diesel or petrol, creating it tougher to refuel incorrectly. And so on.
Looking at Poka-Yoke in production "Nobody makes any mistakes" is the target of the Poka-Yoke methodology. Here a list of some mistakes that can typically be found in production:
Incorrect positioning of assembly components
Incorrect change of a die
Incorrect mounting
Wrong interpretation of directions
Incorrect polarity in electrical connections
Incorrect reading of measured values
Incorrect connection of hoses
Incorrect entries in devices
Assembly of wrong components
Skipped operations
Operation/programming errors on machines
POKA YOKE follows three simple steps
Measurement:
If you can’t measure you can’t control. Simple fixtures or sensors up to high performance camera systems can support the right execution of processes and provides feedback about the correct or incorrect task completion. Measures can be taken by cameras, mechanical, sensor for light and colors, position, vibration, voltage or temperature.
Detection of deviation:
E.g. deviations are determined by checking the amount of tasks done during one operation - has had the operator enough movement to do the job? Are enough components used? (actual-target comparison). Or simple exploitation geometric mismatches when pins or special marking at the workstation are still visible or not used.
Regulation
When deviations occur make sure that measures are taken such as pulling the ANDON CORD by the so called stop the line authority. Only when error-causing steps are cancelled out a permanent production of OK parts can be achieved.
Only when living according to the Poka-Yoke philosophy on a daily basis and following the principles of Poka-Yoke you will be able to achieve with smart automation and trained operators long term success. Root Cause Analysis and sustainable counter measurements are key. In addition each operator should be trained to detect their own faults during operation.
It might seam to be waste to train operators to detect failures, but no matter how much you planing and effort you put in design, failures occur during assembly or manufacturing. Just think about wiring that is now crossing moving components, parts where the collision was not seen during design and so on, trust me the list can be endless. Some failures will be detected with smart automation checking devices. But these are typically very costly and need special trained people to maintain and most of the time these little pieces of technology can only do one job. Here joins Poka-Yoke the game. Cost efficient, failures or incorrect assemblies can’t be passed on and each operator develops an eye for deviation.
Just keep in mind that if you have mass production or small to middle series can determine if you should install a 100% check or if simple Poka-Yokes can get you where you want.
The most important part of Poka-Yoke at all is that failures are detected when they occur and the exponentially rising costs of defective parts passed on are prevented.
KAIZEN
The mother of all lean terms. The change for good.
KAIZEN the mother of all lean terms.
The word Kaizen is a combination of two Japanese words - KAI meaning change and ZEN meaning good. Kaizen is the epitome of continuous improvement and stands for the “change for the good”. Kaizen for your organization means continuous improvement involving everyone.
All together Kaizen is a collection of simple principles for improving your work but also stands for a management philosophy that has turned manufacturing principles upside down the way organizations think and act. The key of all success is that all employee should constantly critically review their processes and workplaces and improve them every day a little more.
You see Kaizen is a fundamental attitude for all players in your organization that results in high quality processes with zero defects on finished goods. Living Kaizen is the continuous strive to improve, simplify or optimize. This ongoing never ending process is therefore best known as the Continuous Improvement Process (CIP).
You can’t say that Kaizen is a methodology or tool, it is a mindset. I can’t emphasize this enough.
““The message of Kaizen is that no day should go by without any improvement in the company””
Kaizen does not depend on major innovations or fundamental changes, but on the everyday small improvements of your employees. The multiple suggestions for improvements paired with a rapid implementation mentality will show really fast their effect on success. The term of continuous improvement is fairly said just another way of the old fashioned suggestions scheme or idea management, which has a long history in the industry but less successful communicated and accepted.
To make a little list before writing too much I want to make it short. In order to pave the way for Kaizen thinking, a number of principles are linked to it, which should guide the thinking and behavior of all players in your organization.
Daily small improvements in all areas of your organization
Avoid any waste of material, time and money
Consider all downstream process steps as customers and then improve performance and quality
Improvements are always possible, it will never stop
Constant improvements are made on a small scale and step by step
No restrictions in terms of scope; products, services, processes, activities, technology, workplace - everything can be improved
Different methods and tools can be used, the decisive factor is the effect, not the procedure
Workplaces, work areas and the situation are viewed "on site", things are viewed and analyzed live (Gemba Walks)
with constant improvements, higher and higher standards are set and made the rule
Kaizen is a task for all employees in the company
All employees of your organization are directly involved in the Kaizen activities and everyone has to participate. To secure the success of Kaizen each individual should invest an adequate amount of time of their working hours in Kaizen activities and focus on their commitment on improvements. As your organization has different departments and by this different employee groups their Kaizen activities are different as well (e.g.):
Top management has to introduce and promote Kaizen as the fundamental principle and drive and monitor its implementation. It creates the right conditions within your organization
Middle management implements the requirements of top management and ensures that standards are kept. It also promotes the way of thinking by offering appropriate training
Team leaders support employees in developing ideas and implementing them. They are responsible for execution and success confirmation
The operators or administrators at the operational level work out concrete suggestions for improvement and implement them. This can also be done in small groups. Kaizen employees improve their specialist knowledge and experience by participating in further training courses.
To give you an example of daily Kaizen routines 5S seems the all time favorite.
You can read the full article on how to implement 5S here. But I will make a short excursion on 5S just to explain the way of thinking. 5S prescribes:
Seiri: Sort out all unnecessary objects
Seiton: Clean-up and correct arrangement of needed objects
Seiso: Keeping the workplace tidy so as to achieve the already established standards through 5S
Seiketsu: Establishing regulations for work standards
Shitsuke: Adherence to the Work standards and continuous improvement
Kaizen is always and everywhere its right to be applied.
Even when most of the people think that it is originally developed and deployed for the automotive industry (best known as the Toyota Production System) with clear mass manufacturing and assembly processes, there is no organization, yours included, that can not improve its performance and quality in terms of customer satisfaction, services, products and processes.
You see Kaizen has become a general way of thinking in all organizations and industries.
Thinking about organizations without Kaizen, you’ll see employees stick to rules and procedures with a “not my task” mentality. Only a few managers have to come up with fundamental long term changes. Kaizen on the other hand stands for the involvement of all employees and that everybody has to think every day what he/she can improve, simplify or optimize in his/her area of work for the “change for the good” of the complete organization, securing the long term success of your organization
Point Kaizen
Point Kaizen describes improvement actions concentrated on one workstation = on the spot.
Point Kaizen describes improvement actions concentrated on one workstation = on the spot.
In general, all lean activities are striving to increase the output of your processes by simultaneously increasing the level of quality by shorten lead times and using less resources. But not all lean initiatives are reaching these targets. Typically the cause lies in the lack of clear targets by the management combined with a misinterpretation of kaizen activities and organizational change.
Kaizen is the Japanese term for “change for the better” on a continuous matter. Point Kaizen refers to a compressed focus on one workstation and improvement actions during a few days, where e.g. in the end the station is no more the bottleneck of the line/cell. For many people this is considered as “Lean”, but it is only a small part of the journey to real operational excellence.
As mentioned Point Kaizen is a scheduled event. When you have an own Lean Management Team or Kaizen Manager these are the guys who are in charge for the upcoming days. Once the team is gathered the action starts.
5S all over: Yes! Let’s start! Use the euphoria and sort out, get rid of all unwanted objects. Clean-up and proper arrange tools needed. Install e.g. flow racks following the 2 bin principle to ensure straight material flow. The Kanban System and FIFO can’t be skipped. Once the workstation is transformed - everybody is proud to have been part this lean activity and communicates the success story.
If you continue with Point Kaizen activities you will reach a better performance on each isolated workstation and probably everybody thinks that you have a great lean initiative. But the real long term results are missing out. So why to continue with lean activities?
Take a step back and see what you have so far. With the improvement actions on each workstation you have raised the efficiency of all single steps but didn’t consider the flow of material in between. It might be tiring to put all this effort in and then the management comes along and sees no obvious progress. This is the point when you move from Point Kaizen action to a systematical organizational change. This process is focusing on the underlying targets of the organization, such as raising performance, decreasing lead times, improving quality and making more profit.
The A3 format comes back in the game. Not only the A3-report and A3 problem solving but more the target setting on an A3 format that tells the story of how the targets can be reached by preset measures. Combined with the future state Value Stream Map showing all Kaizen Bursts each representing a Point Kaizen activity. All those measures lead to a future state of material and information flow that drives your organization into new spheres. In the future with the new Value Stream your bottlenecks will shift along this stream and always creating new point kaizen starting points. Bottlenecks by this can be either stocks of material, high process times or a lack of information. All Kaizen activities, no matter concerning material or information flow, are implemented following a prioritized list. You not only will have to reallocate resources, but also actively participate on the process of organizational change. You and your mid-management are in the driving seat, you have to know where your organization is heading, so make sure that you and your management are participating on Kaizen activities.
Point Kaizen is the first brick of the foundation for organizational change. With the systematic identification of bottlenecks, Point Kaizen activities can be planned and conducted. To have quick changes but is still able to deliver, one bottleneck after the other is worked on. Each Point Kaizen delivers one piece of improvement for the overall improvement needed. These superordinate targets are an increased output, reduction of lead times by simultaneously achieving Zero Defects Policy and all this combined with lower labor costs.
Set up time reduction
Set up time reduction. Nice and simple.
First things first. In order to reduce set-up time the set-up process itself must be observed and analyzed (e.g. by using the EMIPS - eliminate, minimize, integrate, parallelize or synchronize - methodology).
After you have analyzed the process make sure you write down all identified kinds of waste. Try to define the ideal state of the new procedure. Only after verification through testing of the new procedure make it a standard and implement it in your TPM framework. By doing so your operators are now responsible for the new set-up procedure, assumed that your operators are properly trained.
The whole focus on set-up time reduction comes from the customer requirements to manufacture a higher variety of goods in smaller batches. In order to meet those requirements set-up or change over must be kept as short as possible.
But let us go a little bit more into the details.
The pure set-up time is defined as the time needed to change from the last part of a batch to the first part of the following batch.
The set-up includes all activities needed, preparation, action on side and adjustments needed. By doing this you automatically differentiate between so called “external” and “internal” activities.
The following steps should help you to make it easier to reduce set-up times
1 Classify each part of the set-up process to either internal or external. Internal steps are those that only can be done while the production is or has to be inactive. External steps are done without interrupting production.
2 Convert internal steps to external ones. The whole idea is to minimize the time needed shutting down operations. This is why we want to take internal steps out as much as possible.
3 Reduce the time needed for the remaining internal steps. There are for sure some steps you can not take out, for those the manufacturing has to be stopped. The whole focus is now on this internal steps and how to reduce them to an absolute minimum. Here the SMED methodology (Single Minute Exchange of a Die) can help. Too find out more you can read here.
4 Eliminate adjustments. Last but not least try to get stable process parameters. With effective process control in place you can get rid off adjustment activities.
A Pareto Diagram can be useful to prioritize the setup time reduction activities. Don’t start everywhere at the same time! Start with the biggest loss and you will see over the time how it will change. It also gives you a great opportunity to see the progress that you are making on set-up time reduction.
DMAIC
Define, Measure, Analyze, Improve, Control. DMAIC is an incremental process improvement using Six Sigma methodology.
Define, Measure, Analyze, Improve, Control. Incremental process improvement using Six Sigma methodology.
DMAIC can bee seen as a data-driven improvement strategy and for sure is part, or will be a part, of your organizations SIX SIGMA quality initiative. DMAIC is an acronym for: Define, Measure, Analyze, Improve, and Control.
DMAIC is a cyclical process such as the PDCA is. The reason to go for the DMAIC is to strive for the best result possible with a structured approach.
These process steps are:
DEFINE: the customers and their CTQ (Critical to Quality) and the core process involved.
Who are your customers?
What are their requirements for products or services?
What are their expectations?
Go for a value stream and map the process flow through the complete business process
MEASURE:
Define a plan on how to collect data from your core process
Go for different sources of data in order to be as specific as possible on defects and metrics
ANALYZE:
While analyzing the data along the process map make sure to identify the real root cause of defects and
point out opportunities for improvement
Compare shortfalls with the results of customer surveys
Determine gaps between targeted performance and current performance
Prioritize potential improvement measures
Identify variation and their source
IMPROVE:
Kaizen Workshops
Target is to improve the current process in a simple and effective way
Develop a prioritized action plan
Do it!
If you want a structured approach, just read our PDCA article.
CONTROL:
Stay tuned on your process improvement measures
Make sure that they stay on track
Prevent falling back to the “old way”
In the end, when you are in charge, require the full documentation. Make sure that everything implemented is well documented and a clear monitoring is installed that deviation can be fast identified.
Having or installing a sustainable problem solving culture in your organization will be key for the future. Make sure to institutionalize problem solving or a kaizen culture through training, training and more training.
Waste
The opposite of value creating are non-value adding activities. Those can be remembered with TIMWOOD.
Waste (MUDA)
Waste or MUDA is the opposite of value creation. Waste describes all non-value-adding activities the customers are not willing to pay for. The two main categories are obvious and hidden waste. While obvious waste can be eliminated, hidden waste can only be minimized.
When talking about waste there is no way around the 7 kinds of waste according to Taiichi Ohno most known in the lean world as TIMWOOD. Feel free to read the complete article on TIMWOOD(S) - yes you are right - where is this S coming from… keep on reading and you will see.
The 7(8) kinds of waste:
T = Transportation
I = Inventory
M = Motion
W = Waiting
O = Overproduction
O = Overprocessing or - engineering
D = Defects
S = Unutilized stuff
It is important to be aware of these kinds of waste in the list. But overproduction is the worst and typically initiates the other types of waste.
To read more in detail about TIMWOOD go here.
Pareto Principle
The 80/20 rule demonstrates that things have an unequal distribution. Out of 5 one will fly and have the most impact. With 20 percent of action 80 percent of your target state is already reached.
The Pareto Principle describes that 80% of problems can be closed with 20% of the causes. This principle is named after Vilfredo Pareto who found out that 80% of Italy’s wealth belonged to 20% of the population.
With this in mind it is worth to have a look at it.
Let us start with an assumption, according to the Pareto Principle it allows us to assume that
20% of input creates 80% of the output
20% of customers create 80% of your revenue
20% of causes create 80% of failures
20% of your employees create 80% of sales
and so on…
But before you run away now and think you have the answer hold a second. With the 80/20 rule you might tend to say that it always have to be 100 - it’s not. Make a deep analysis before making such statements! 20% of your employees can also make only 20% of sales or 60%. So before you fire 80% of your employees keep in mind that the Pareto Principle only gives you an idea on the distribution.
The whole idea behind it is that most things in life are not distributed evenly!
When we talk about value adding activities and the final product is 100% What is with all the necessary tasks, that are not adding any value to the final product but have to be done to run the company.
Or think about failures and finding the root cause, where to start to take actions? This is great when you think about a Failure Pareto and you want to satisfy your customer as quick as possible. Of course you are focusing first on the most failures and most of the time - not always - the other failures will disappear as well.
But most important of all, your customer gains trust in you that you have the competencies to do the job.
The key point is that most things are not in a 1/1 actio = reactio relationship.
So what can we use it for this 80/20 rule?
The Pareto Principle in first place supports you on realizing that most of the outcome are based on a minority of inputs. This means:
20% of input creates 80% of the output > try to reduce those non value adding activities
20% of customers create 80% of your revenue > install a key account manager that the customers knows he/she is important to your company > your customers success is your companies success
20% of causes create 80% of failures > Focus on fixing those failures first
20% of your employees create 80% of sales > get those employees a reward
We could continue on and on. To bring it to the point > focus on the 20% and not on everything at the same time.
Some examples that might help you for a better understanding:
Instead of spending a whole night to prepare a presentation and thinking about where to start > focus on one topic and do it. You will get a feedback anyway during the pitch. This feedback gives you the chance to take it and improve it.
Instead of focusing on one solution that might be the best and go through all the details. Make a list of three and go through the pros and cons with your colleagues that probably know the topic better anyway and based on their opinion make a decision with what to go on.
Maybe this examples are nuts for you but we want to emphasize that you should focus only on the important 20% and forget - for the moment - the other 80.
Last but not least - the Pareto Principle is not a law of nature it is a guideline to steer your focus and to save time on problem solving or simply getting your job done faster.
FMEA
The method of the FMEA - Failure Mode and Effect Analysis has been used for years in the automotive and manufacturing industry.
Failure Mode Effects Analysis - FMEA
The method of the FMEA - Failure Mode and Effect Analysis has been used for years in the automotive and manufacturing industry.
The risk analysis framework has been applied in a wide range of industrial sectors. The first areas of application were traditionally in product development. Based on this the integration of the production process planning and the production. In the automotive industry, the joint creation of FMEA for products and processes by Today customer, supplier and subcontractor are a natural part of a cooperation.
The user is guided through the "10 Steps to Creation of the FMEA".
Step 1 - Review the process
Use a process flow chart or an already existing value stream map to identify each part of a process
List all process steps in a FMEA table
If you think the list gets too long it might is. Use this chance to split up the process and cut the elephant. It makes more sense to work on smaller parts of the process instead of getting lost in the woods.
Step 2 - List potential failures
Review all existing data and documents that can give you a hint about each component that can lead to a failure
After having a complete list try to cut it down and to combine the parts of the initial list
The chances are high that you will identify several potential risks of failures for each component
Step 3 - List potential effects of failures
The effect is the outcome of a failure on the finished good or a process step
It is common that not only one effect will occur for a single failure, don’t be suprised
Step 4 - Assign the level of failure to risks
This is based on the consequences for each failure
Think about the ranking as the worst impact that it can have
Step 5 - Assign the possibility of occurrence
How high is the possibility of occurrence
What impact will it have if occur
Step 6 - How can it be detected
What are the chances that you will detect the failure before occurring
Step 7 - Calculate the RPN (Risk Priority Number)
Severity (S)
Severity x Occurence (S x O) = criticality
Severity x Occurence x Detection (S x O x D) = RPN
Step 8 - Define the action plan
With the decision making process followed by the prioritization from the RPN (Step 7) focus on the topics with the highest RPNs
Follow a classic action plan by defining who will be doing what till when
Step 9 - Take action
Get things done!
Implement the defined improvement actions
Follow the PDCA principle
Plan - done
Do - right now
Check - Step 10
Act - loop starts over
Step 10 - Re-evaluate the RPN
Time to check on the impact of your actions
Re-evaluate each potential failure identified and determine if the improvement measures have an effect or not
If not follow the PDCA and start over with step 8
The FMEA is linked to all CIP and Kaizen activities - there is always something to improve.
Doctor Nurse Principle
The operator creating the value (doctor) receives the materials and tools from the logistics provider (nurse), so that his/her primary activity is not interrupted by secondary activities.
In the Doctor Nurse principle, the operator creating value is considered as the doctor, he receives tools and goods he needs to do his job from the nurse in this case logistics. For this reason, the doctor can’t do his job without the support of the nurse.
What can we learn from hospitals and how can we adapt it to the lean world.
In hospitals it is crucial that the doctor can fully concentrate on a surgery, the doctor is the single point of contact towards the patient using his tools combined with his training. Everything distracting him from being focused has to be eliminated. In order to give him this capability he needs assistant right next to him. The nurse’s job is to support the doctor and provide him with all equipment, tools and material he needs just in time.
Applying this principle to production is not that hard. To use the doctor nurse principle on the shop floor some requirements have to be met. As mentioned think about the operators as the doctor, they have to concentrate on production. As they are the once generating value for the whole organization by assembling the components which customer are willing to pay for – they need to be placed in the center of all activities – the rest is supportive.
In lean manufacturing this is called the line-back approach. Primary processes are the once that add value so focus on the operation and prepare everything that supports it. The nurse takes care of all other activities, most of the time non-value adding activities but necessary.
Doctor Nurse Principle
Arrange the work station in a way that gives the nurse free accessibility to the work area without disturbing the doctor, i.e. filling up kanban shelfs with new material while simultaneously removing empty boxes.
With the approach of separation of primary and secondary processes in two physical areas none of the process will be interrupted by the other.
In addition, this principle is driving the mindset of the organization to focus on a lean production process and how best it can be supported. If you do so, you will also have the advantage by separating value-adding and non-value-adding activities to find you approaches to minimize the non-value adding activities.
Another way of calling the nurse a nurse is a water spider or in lean terms a Mizusumashi – the inbound material supplier.
Kamishibai Board
The Kamishibai Board helps your organization to visualize and manage recurring tasks in a very simple but effective way.
The Kamishibai Board is part of the visual management in Lean Management that supports you on managing recurring tasks in a way that the status of each task is clearly recognizable by everyone in your organization.
The tasks are listed by their frequency and the responsible persons. The design of the cards can vary, but typically T-Cards are used as the handling is quite easy. These cards contain on both sides the information of each task. One side of the card is red the other one green. RED: to do, GREEN: done. So the color is indicating the status of each task.
By using these two color coded cards everybody in the organization will recognize if all activities are on track or if there is a backlog ahead on performing daily, weekly or monthly activities.
Example Kamishibai Board - weekly tasks with assigned persons
Kamishibai is a Japanese term, to bring it in operations terms it can be understood as mini-audits. The Kamishibai is a great starting point for Gemba Walks mainly in the admin area of your organization but can also be utilized in the service and maintenance department. It also supports 5S activities and assists in checking the continuous improvement actions on checking on standards and improvements during regular meet ups.
The Kamishibai approach has different sections. E.g. a simple planning board with T-cards with a red and a green side, a list of person in charge and a 3C list. The 3C list thereby describes the Concern, defines the Cause and lists the Countermeasures, find a free template (in flip chart format) here.
The planning section has the tasks tank, on the far left side all tasks are stored in holders (T-Cards) or e.g. magnetic cards that are also green on the one and red on the other side. One section further to the right you can implement a matrix with responsible person for each row and all weekdays as column. By this you can easily assign tasks.
Between the organizational and the problem solving part there should be space for the escalation or support needed tasks. It might happen that an assignee is not able to fulfill a task as he/she is in the need of information or active support from a different level or department.
To sum it up. The benefits of the Kamishibai methodology is mainly the visualization part. It gives clear structure and is understandable at first sight. With the Kamishibai you are able to perform so called “mini-audits” on a regular basis that helps you driving the continuous improvement process in your organization and supports you on performing effective Gemba Walks. Instead of heaving some chit chats you can bring information straight to the point and address any issues fast.
You can use the Kamishibai methodology for all kinds of work areas in your organization, e.g. you have control indicators for methods, processes, documents, standards and much more. In the end the Kamishibai helps you to keep the routine of defined standard work procedures as results of KAIZEN activities. If it works congrats, if not congrats - you found something that can be improved.
Kaizen Manager
Kaizen Mangers are the people in your organization who initiate changes within your organization or support departments on the path along the continuous improvement process (CIP).
Kaizen Manager (Change Agents)
Kaizen Mangers are the people in your organization who initiate changes within your organization or support departments on the path along the continuous improvement process (CIP).
Change Agents are the key players in your organization to integrate new processes or improvement actions and simultaneously stabilize departments throughout a change or transformation process.
When talking about a Kaizen Manager or Change Agent he/she has the following duties with the support of the Change Leader:
Support the change process by defining the program, participants, selecting suitable processes and defining the targeted state
Set individual targets for responsible/affected persons
Support responsible persons for each individual improvement process through coaching or scheduling exchange rounds with other key players. (To stay on track)
Support the onboarding process for new people to the program
Support on the transformation process from learning to actually doing
Coordinate and support further expansion within departments
Support on the transformation process of organizational culture
Challenge status quo with fundamental questions on existing procedures
Work closely with the heads of departments to anchor the new improvement culture across the complete organization
What ever it takes, it has to be clear that a sustainable change culture can only be established if all of your mid and top mgmt. themselves drive the integration of all their direct reports. The Kaizen Manager is the pure supportive function in the role of an internal consultant to guide the process.
Stay Connected
Ad
We want information fast and in a nutshell. We from OI recommend Blinkist* - because it’s simply the best.
* = Affiliate Link