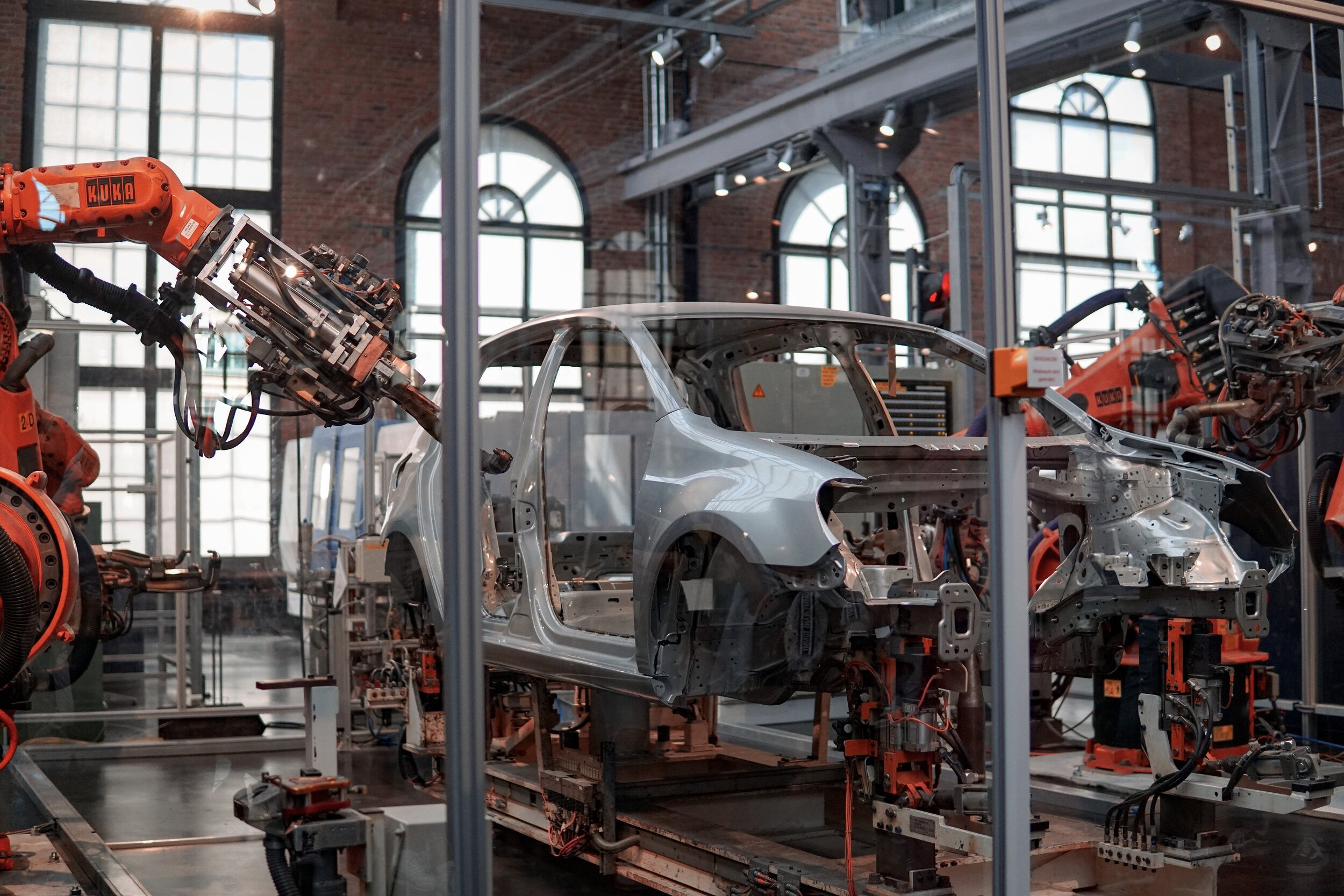
LANGUAGE OF LEAN
Cell Production
Cell Production focuses on optimizing the flow of work and improving efficiency in manufacturing and operations.
Cell Production focuses on optimizing the flow of work and improving efficiency in manufacturing and operations. It is based on the concept of organizing work into cells, which are self-contained units responsible for performing a specific set of tasks. The goal of cell production is to minimize waste, increase flexibility, and improve overall performance.
The origins of cell production can be traced back to the 1950s and 60s, when Toyota and other Japanese companies were experimenting with new approaches to manufacturing. Over time, the concept of cell production has evolved and been refined, and today it is widely used in a variety of industries, including automotive, electronics, and consumer goods.
In order to implement cell production effectively, there are several key steps that organizations must take. Firstly, it is important to conduct a thorough analysis of the current state of the manufacturing or operations process, in order to identify areas where improvements can be made. This may involve mapping out the flow of work and identifying bottlenecks or other inefficiencies.
Once these areas have been identified, the next step is to reorganize the work into cells, taking into account the specific requirements of each cell and the skills and expertise of the employees who will be working in them. This may involve rearranging physical work spaces, or changing the way that work is assigned and managed.
It is also important to establish clear communication and feedback mechanisms, so that employees and teams can work together effectively. This may involve setting up regular meetings to discuss performance, or implementing systems for tracking and reporting on key metrics.
In order to ensure a successful implementation of cell production, it is also important to provide training and support for employees. This may involve providing training on the new processes and procedures, or offering coaching and mentoring to help employees develop the skills and knowledge they need to be effective.
Another key aspect of cell production is continuous improvement. This involves regularly reviewing performance and making adjustments as needed, in order to optimize efficiency and reduce waste. This may involve experimenting with different approaches, such as implementing new technologies or streamlining processes, in order to find the best solutions.
In conclusion, cell production is a powerful methodology for optimizing performance in operations and manufacturing. By reorganizing work into cells, minimizing waste, and continuously improving performance, organizations can increase efficiency, reduce costs, and improve overall performance. In order to be successful, organizations must take a structured and systematic approach, and be committed to ongoing improvement.
U-Shape Layout
The U-shape layout describes the layout of machines and workstations in a one-piece-flow, where they are laid out in the shape of the letter “U”.
The U-shape layout describes the format of the manufacturing or assembly lines of machines and workstations following the principle of one-piece-flow which is laid out in the shape of the letter "U". The operators are working inside the "U" and with the proper supply of components or material allocation from the outside the movement is reduced to the minimum. The goal is also with the U-Shape layout to have interruption free assembly.
Using “U” Shaped Cells
Generally speaking the u-shaped layout of a manufacturing cell allows operators to easily move from one process step to the other as well as passing on parts or pre-assembled units to the following step with little effort. It is not a necessity to have the U-shaped configuration. This comes mostly from maximizing throughput on less manufacturing space (€/sqm).
The layout of assembly lines in a “U” shaped layout has several advantages:
The Start en End are close together, allowing with an installed 2 container mgt. to have full visual control. Following the mizusumashi principle - one operator can handle feeding the line including supply of raw material as well as the transport of finished goods.
The shortening of distances allows to share process steps, like in a chaku chaku* line, as well as reducing the wastes of transport and motion.
The U-shaped layout provides you the foundation for interruption free one-piece-flow.
Transparent and open communication within the work cell is easier.
Value adding process is done inside the assembly line, material supply is done from the outside.
Following the principles of flexible equipments - high level performance is when your machines and tables are on rollers to have a quick reconfiguration.
Typically as mentioned before:, it is less floor space required than with a stretched line, as well as distances for movement are reduced.
Chaku Chaku is a takt flow oriented manufacturing process model. It means load load and describes that one operator follows the complete assembly process - walks with the good - and conducts each assembly process. To learn more about Chaku Chaku read here.
Stay Connected
Ad
We want information fast and in a nutshell. We from OI recommend Blinkist* - because it’s simply the best.
* = Affiliate Link