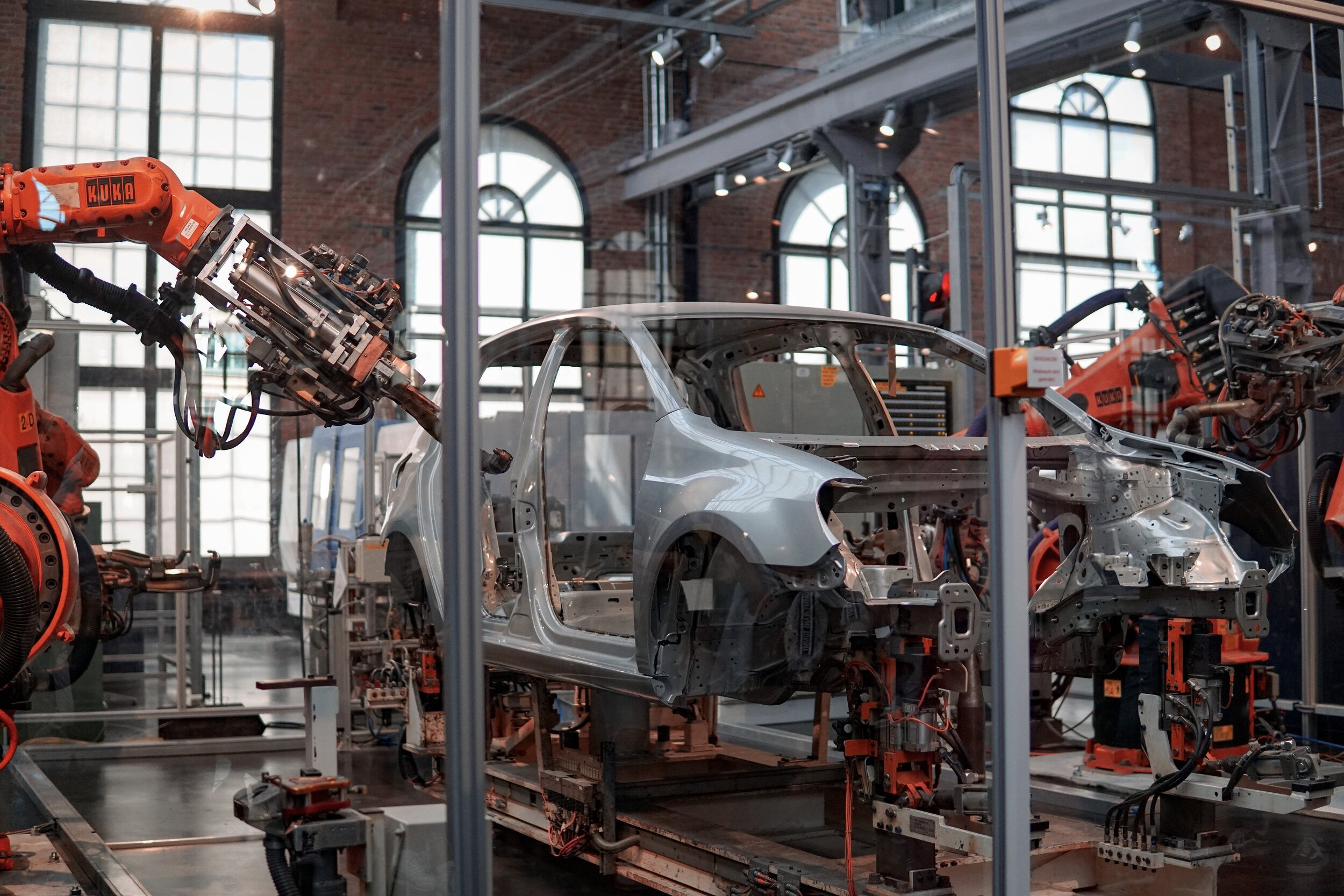
LANGUAGE OF LEAN
Perfection
Perfection is a goal that many organizations strive for, and it is no different in the manufacturing industry.
Perfection is a goal that many organizations strive for, and it is no different in the manufacturing industry. By striving for perfection, manufacturers can improve the quality of their products, reduce waste, and increase efficiency. But how exactly can perfection be achieved in the manufacturing industry?
One of the key components of achieving perfection is through the implementation of a continuous improvement mindset. This involves constantly looking for ways to improve processes, systems, and products. This could include implementing new technology, streamlining processes, or making changes based on customer feedback. By continuously seeking out ways to improve, manufacturers are able to stay ahead of the curve and remain competitive in an ever-evolving industry.
Another critical component of achieving perfection in the manufacturing industry is through effective communication. Communication is key when it comes to identifying and addressing areas for improvement. Whether it is between departments, between management and employees, or between a manufacturer and its customers, effective communication is essential to achieving perfection.
Another way to achieve perfection in the manufacturing industry is through standardization. By establishing and following standardized processes, manufacturers are able to reduce waste, improve quality, and increase efficiency. This could involve standardizing equipment, tools, and work processes, or even creating a standard operating procedure manual that outlines the steps involved in a particular process. By having standardized procedures in place, manufacturers are able to ensure that their products are of the highest quality and that their processes are as efficient as possible.
Quality control is another critical component of achieving perfection in the manufacturing industry. This involves inspecting products and processes to ensure that they meet the standards set by the manufacturer. Quality control processes could include regular inspections, audits, and testing of products, as well as processes such as supplier selection and product design. By implementing a robust quality control system, manufacturers are able to identify and address any issues before they become major problems.
Investing in training and development is another important step in achieving perfection in the manufacturing industry. By providing employees with the training and resources they need to succeed, manufacturers are able to improve the skills and knowledge of their workforce. This could include providing employees with training on new technologies, new processes, or even soft skills such as effective communication and teamwork. By investing in their employees, manufacturers are able to improve their overall operations and move closer to their goal of perfection.
In a nutshell, achieving perfection in the manufacturing industry is a goal that can be achieved through a combination of continuous improvement, effective communication, standardization, quality control, and employee training and development. By striving for excellence in all areas of their operations, manufacturers are able to remain competitive, improve the quality of their products, and provide customers with the best possible experience.
Rapid Improvement Event
Rapid Improvement Events, also known as Kaizen events, are a powerful tool for improving production processes in every industry.
Rapid Improvement Events, also known as Kaizen events, are a powerful tool for improving production processes in the manufacturing industry. They are focused, short-term initiatives aimed at solving specific problems and improving processes in a rapid and efficient manner.
At the heart of a Rapid Improvement Event is the involvement of a cross-functional team of employees, each bringing a unique perspective and skillset to the table. The team works together to identify and solve problems, test new ideas, and implement solutions that can have an immediate impact on the production process.
One of the key benefits of Rapid Improvement Events is the speed with which they can deliver results. By focusing on a specific problem and working together as a team, significant improvements can be made in just a few days or weeks. This can be especially valuable in the manufacturing industry, where time is often of the essence and even small improvements can make a big difference.
To ensure the success of a Rapid Improvement Event, it's important to follow a structured methodology. This typically includes the following steps:
Define the problem and scope of the event. What is the specific issue that needs to be addressed, and what is the desired outcome of the event?
Assemble the cross-functional team. Choose team members who have a strong understanding of the problem and can bring a variety of skills and perspectives to the table.
Conduct a thorough analysis of the problem. Gather data, observe processes, and engage in root cause analysis to understand the underlying cause of the problem.
Develop and implement a plan of action. Based on the findings of the analysis, create a plan of action that addresses the root cause of the problem and implements solutions that will improve the production process.
Implement and monitor the changes. Once the plan of action is in place, implement the changes and monitor the results to ensure they are having the desired impact.
Reflect and celebrate successes. Reflect on the successes of the event and celebrate the improvements that were made.
Rapid Improvement Events are a powerful tool for improving production processes in the manufacturing industry. By bringing together a cross-functional team, focusing on a specific problem, and following a structured methodology, organizations can achieve significant improvements in a short amount of time.
In a nutshell, it is important to embrace a continuous improvement mindset and actively seek out opportunities to improve production processes. Rapid Improvement Events provide a structured and efficient way to do just that, delivering results that can have a lasting impact on an organization's success.
Product Machine Matrix
The Product Machine Matrix is a methodology that can be used in the manufacturing industry to improve production processes and achieve operational excellence.
The Product Machine Matrix is a methodology that can be used in the manufacturing industry to improve production processes and achieve operational excellence. The idea behind this approach is to create a matrix that matches the type of product being produced with the appropriate machine for that product.
The first step in implementing the Product Machine Matrix is to analyze the current production process and identify areas where improvements can be made. This can be done through the use of data and performance measurement tools, as well as by observing the process and gathering feedback from employees.
Once the areas for improvement have been identified, the next step is to determine the optimal machine for each type of product. This involves considering factors such as the complexity of the product, the volume of production, and the skill level of the operator. It may also be necessary to make changes to the existing machines or to purchase new equipment in order to meet the needs of the production process.
The Product Machine Matrix also requires the establishment of standard work procedures for each machine and product type. This helps to ensure that the production process is consistent and efficient, and it also provides a roadmap for continuous improvement. Standard work procedures should be regularly reviewed and updated based on performance data and feedback from employees.
Another important aspect of the Product Machine Matrix is the need for visual management. This involves creating clear and easy-to-understand visual aids, such as work instructions and flow charts, that help to guide employees through the production process. This helps to prevent errors and improve productivity, as well as making it easier for employees to quickly identify and resolve any issues that may arise.
To be effective, the Product Machine Matrix must be integrated into the overall culture of the organization. This requires the commitment and engagement of employees at all levels, as well as a focus on continuous improvement and a willingness to embrace change. Regular training and communication is also key to the success of the methodology, as it helps to build the necessary skills and knowledge, and ensures that everyone is working towards a common goal.
In a nutshell, the Product Machine Matrix is a powerful methodology that can be used to improve production processes in the manufacturing industry. By carefully matching the type of product with the appropriate machine, and by establishing standard work procedures and utilizing visual management techniques, organizations can achieve operational excellence and drive continuous improvement. With the right approach and commitment, this methodology can deliver significant benefits to any organization looking to optimize its production processes.
ABC Analysis
ABC Analysis is a method used in the manufacturing industry to categorize inventory based on its value and usage.
ABC Analysis is a method used in the manufacturing industry to categorize inventory based on its value and usage. The goal of this analysis is to prioritize items for better inventory management and streamline production processes.
In ABC Analysis, items are divided into three categories: A, B, and C. A items are the most valuable and frequently used, B items are less valuable but still used regularly, and C items are the least valuable and used infrequently. This categorization helps identify areas where improvements can be made to reduce inventory costs and increase efficiency.
To implement ABC Analysis, it is necessary to first gather data on the value and usage of each item in the inventory. This can be done by tracking the usage frequency, cost, and demand of each item. Once the data is collected, the items can be divided into the three categories based on their value and usage.
Once the items are categorized, the focus can be placed on the A items. These items should be closely managed and monitored to ensure they are always in stock and available for production. This may involve implementing a just-in-time (JIT) system for these items, which reduces the amount of inventory that needs to be kept on hand.
B items can also be managed, but to a lesser extent. These items may not be as critical to production, but they still need to be available when needed. Inventory levels for B items should be managed to minimize excess inventory, but not at the cost of stockouts.
C items are typically low-cost items that are not used frequently. The focus for these items should be on reducing the amount of inventory that is kept on hand. This can be done by reducing the order frequency or implementing a safety stock system to ensure that the item is available when needed.
In a nutshell, ABC Analysis is a simple and effective method to prioritize inventory and streamline production processes. By categorizing inventory based on its value and usage, it is possible to focus on the most important items and reduce the amount of inventory that is kept on hand. This leads to cost savings, increased efficiency, and improved production processes.
Bowling Chart
The bowling chart is a visual representation used in the manufacturing industry to track and monitor key performance indicators (KPIs)
The bowling chart is a visual representation used in the manufacturing industry to track and monitor key performance indicators (KPIs). Its origins can be traced back to the Toyota Production System, where it was used as a simple and effective tool to measure and improve the performance of the production line.
The basic concept of a bowling chart is to provide a visual representation of the performance of a particular KPI over time. The chart takes the form of a bowling pin, with each pin representing a performance target. The height of the pin corresponds to the actual performance achieved for that period, with higher pins indicating better performance.
One of the main benefits of using a bowling chart is that it provides a simple and intuitive way to track progress towards performance targets. The visual representation allows stakeholders to quickly understand the current state of the performance and identify areas where improvement is needed.
In the manufacturing industry, bowling charts are often used in combination with other KPIs to provide a comprehensive view of the performance of the production line. For example, a bowling chart could be used to track the number of defects produced in a particular production run, while another KPI might track the overall cycle time for the production line.
To get the most out of a bowling chart, it is important to ensure that the KPIs being tracked are relevant to the performance of the production line. This requires a clear understanding of the goals and objectives of the production process and the factors that influence performance.
Once the appropriate KPIs have been identified, the next step is to establish performance targets for each KPI. These targets should be based on historical data, industry benchmarks, and the overall goals and objectives of the production line.
Once the performance targets have been established, the bowling chart can be populated with data on a regular basis, such as weekly or monthly. This data can then be analyzed to identify areas where performance is exceeding expectations and areas where improvement is needed.
In conclusion, the bowling chart is a simple and effective tool for tracking and monitoring KPIs in the manufacturing industry. When used in combination with other KPIs and as part of a systematic approach to performance improvement, it can provide valuable insights into the performance of the production line and help drive continuous improvement.
Process Chain
The manufacturing industry is a complex system of processes, with each stage relying on the success of the previous one to achieve the final product.
The manufacturing industry is a complex system of processes, with each stage relying on the success of the previous one to achieve the final product. The process chain is the backbone of this system, connecting each stage together to ensure a seamless flow of goods and services.
To achieve the highest level of efficiency in the production process, it is important to understand the process chain and how it serves the production processes. This includes identifying the inputs, outputs, and key activities of each stage, as well as the flow of goods, services, and information throughout the chain.
One of the first steps in optimizing the process chain is to establish clear and standardized procedures for each stage. This includes defining the roles and responsibilities of each team member, as well as establishing a clear communication plan to ensure that everyone is aware of the status of each stage.
Another important factor in optimizing the process chain is to reduce waste and increase efficiency. This can be achieved through continuous improvement efforts, such as streamlining processes, reducing inventory, and minimizing lead times. Lean tools, such as value stream mapping, can be used to identify areas of waste and opportunities for improvement.
Additionally, investing in new technology and equipment can also help to improve the process chain. Automation and digitalization of the production process can lead to faster and more accurate production, as well as reduced labor costs and increased productivity.
Furthermore, involving employees in the continuous improvement process is crucial in achieving the best results. Encouraging their input and ideas can lead to new solutions and creative thinking that can drive process improvement. Employee training and development programs can also help to enhance the skills and knowledge of the workforce, leading to increased efficiency and effectiveness.
Another important aspect of the process chain is supplier selection and management. Careful selection of suppliers can ensure that high-quality inputs are used in the production process, reducing the likelihood of defects and increasing efficiency. Effective supplier management can also ensure timely delivery of goods and services, reducing lead times and minimizing the impact of supply chain disruptions.
In a nutshell, the process chain is a critical component of the manufacturing industry, serving as the foundation for the production processes. By establishing clear procedures, reducing waste and increasing efficiency, investing in new technology, involving employees, and carefully selecting and managing suppliers, manufacturers can optimize the process chain and achieve operational excellence
Pacemaker
"Pacemaker" is a term commonly used in the manufacturing industry to describe a production process that sets the pace for the rest of the production line. Sometimes also considered as bottleneck station.
"Pacemaker" is a term commonly used in the manufacturing industry to describe a production process that sets the pace for the rest of the production line. A pacemaker process is the one that determines the speed and flow of the entire production process, and therefore has a significant impact on the efficiency and productivity of the manufacturing operation. As a Lean Management Expert, it is important to understand the role and significance of a pacemaker in manufacturing, and how to effectively implement this principle for maximum efficiency and profitability.
The concept of a pacemaker process has its roots in the Toyota Production System (TPS), which is the foundation of the Lean Manufacturing philosophy. TPS emphasizes the importance of flow and standardization in manufacturing, and the pacemaker process is a key component in achieving these goals. The pacemaker process is the first step in the production line and sets the standard for the rest of the processes to follow. This means that the pace, efficiency, and quality of the pacemaker process have a direct impact on the entire production line.
In order to effectively implement the pacemaker principle, it is important to carefully select the appropriate process to serve as the pacemaker. This process should be stable, consistent, and capable of producing high-quality products in a timely manner. It is also important to standardize the pacemaker process to ensure that it runs smoothly and consistently, and that the production line can respond to changes in demand or other factors.
Once the pacemaker process has been established, it is important to monitor and measure its performance regularly. This can be done through the use of Key Performance Indicators (KPIs), such as cycle time, quality rate, and productivity. By monitoring these KPIs, it is possible to identify areas for improvement and to make changes to the pacemaker process or the rest of the production line to improve overall efficiency.
In addition to setting the pace for the production line, a pacemaker process can also have a positive impact on the morale of the manufacturing workforce. When employees see that their efforts are making a significant impact on the overall efficiency and success of the operation, they are more likely to be motivated and engaged in their work.
In a nutshell, the pacemaker principle is a key component of the Lean Manufacturing philosophy, and a valuable tool for Lean Management Experts looking to improve the efficiency and profitability of their manufacturing operations. By carefully selecting the pacemaker process, standardizing its performance, monitoring its performance regularly, and using KPIs to track progress, it is possible to achieve maximum efficiency and profitability in the manufacturing industry.
TPM - Total Productive Maintenance
Total Productive Maintenance (TPM) is a maintenance strategy that involves involving all employees in the maintenance process to maximize equipment productivity and minimize downtime.
Total Productive Maintenance (TPM) is a methodology that originated in Japan in the 1970s and has since become a widely recognized and adopted approach to operational excellence in manufacturing and other operations-focused industries. It is a comprehensive approach that seeks to optimize the performance of equipment and processes through a focus on maintaining and improving reliability and efficiency.
The origins of TPM can be traced back to the Japanese auto industry, where manufacturers were seeking ways to increase productivity and competitiveness in the face of increasing global competition. TPM emerged as a response to the need for a more proactive and integrated approach to equipment maintenance, with the goal of improving both productivity and overall equipment effectiveness (OEE).
Over time, TPM has evolved and expanded to encompass a wider range of objectives and activities. Today, it is widely regarded as a best-practice approach to operational excellence, and is widely used in many different industries, including manufacturing, healthcare, and government operations.
One of the key features of TPM is its focus on involving all employees in the maintenance and improvement process. This is achieved through the creation of cross-functional teams and the use of a range of techniques, including root cause analysis, standardization, and continuous improvement.
Another key aspect of TPM is its focus on data-driven decision-making and performance measurement. This involves the collection and analysis of data on equipment and process performance, which is then used to identify areas for improvement and to drive continuous improvement efforts.
When properly implemented, TPM can have a significant impact on organizational performance and competitiveness. This can include improvements in equipment reliability, increased productivity, reduced waste, and improved overall equipment effectiveness (OEE).
To achieve these benefits, it is important to implement TPM in a structured and systematic way, with clear goals and objectives and a strong focus on continuous improvement. This typically involves a multi-phased approach, starting with an assessment of existing processes and equipment, followed by the development of a comprehensive improvement plan and the implementation of specific improvement initiatives.
In a nutshell, TPM is a proven methodology that can help organizations achieve operational excellence by optimizing the performance of their equipment and processes. To achieve success, organizations must approach TPM in a systematic and structured way, with clear goals and objectives, and a strong focus on continuous improvement.
Key points for a successful TPM implementation:
Involve all employees in the process
Focus on data-driven decision-making
Adopt a multi-phased approach
Prioritize continuous improvement
Develop a comprehensive improvement plan.
Stay Connected
Ad
We want information fast and in a nutshell. We from OI recommend Blinkist* - because it’s simply the best.
* = Affiliate Link