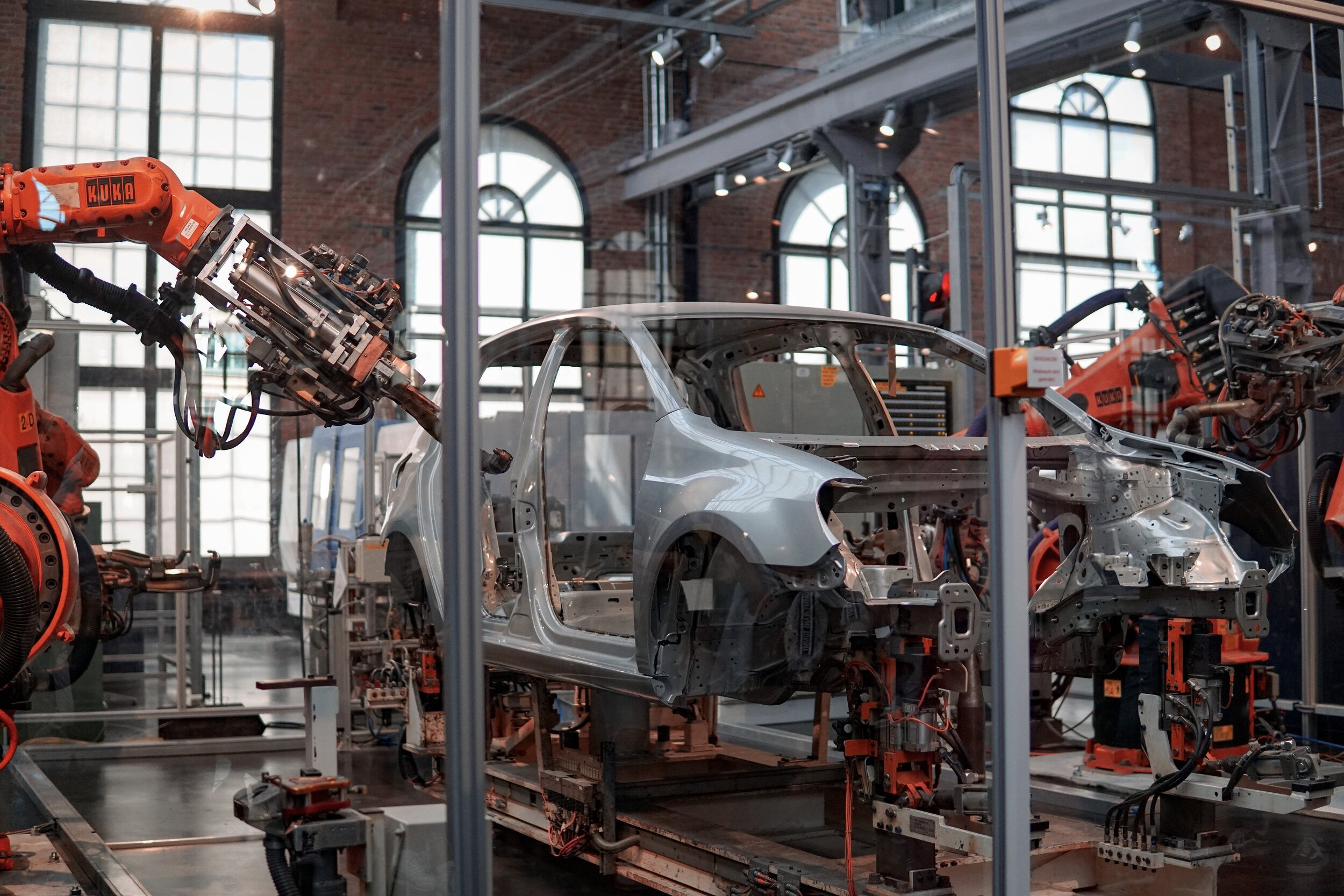
LANGUAGE OF LEAN
Pacemaker
"Pacemaker" is a term commonly used in the manufacturing industry to describe a production process that sets the pace for the rest of the production line. Sometimes also considered as bottleneck station.
"Pacemaker" is a term commonly used in the manufacturing industry to describe a production process that sets the pace for the rest of the production line. A pacemaker process is the one that determines the speed and flow of the entire production process, and therefore has a significant impact on the efficiency and productivity of the manufacturing operation. As a Lean Management Expert, it is important to understand the role and significance of a pacemaker in manufacturing, and how to effectively implement this principle for maximum efficiency and profitability.
The concept of a pacemaker process has its roots in the Toyota Production System (TPS), which is the foundation of the Lean Manufacturing philosophy. TPS emphasizes the importance of flow and standardization in manufacturing, and the pacemaker process is a key component in achieving these goals. The pacemaker process is the first step in the production line and sets the standard for the rest of the processes to follow. This means that the pace, efficiency, and quality of the pacemaker process have a direct impact on the entire production line.
In order to effectively implement the pacemaker principle, it is important to carefully select the appropriate process to serve as the pacemaker. This process should be stable, consistent, and capable of producing high-quality products in a timely manner. It is also important to standardize the pacemaker process to ensure that it runs smoothly and consistently, and that the production line can respond to changes in demand or other factors.
Once the pacemaker process has been established, it is important to monitor and measure its performance regularly. This can be done through the use of Key Performance Indicators (KPIs), such as cycle time, quality rate, and productivity. By monitoring these KPIs, it is possible to identify areas for improvement and to make changes to the pacemaker process or the rest of the production line to improve overall efficiency.
In addition to setting the pace for the production line, a pacemaker process can also have a positive impact on the morale of the manufacturing workforce. When employees see that their efforts are making a significant impact on the overall efficiency and success of the operation, they are more likely to be motivated and engaged in their work.
In a nutshell, the pacemaker principle is a key component of the Lean Manufacturing philosophy, and a valuable tool for Lean Management Experts looking to improve the efficiency and profitability of their manufacturing operations. By carefully selecting the pacemaker process, standardizing its performance, monitoring its performance regularly, and using KPIs to track progress, it is possible to achieve maximum efficiency and profitability in the manufacturing industry.
DMAIC
Define, Measure, Analyze, Improve, Control. DMAIC is an incremental process improvement using Six Sigma methodology.
Define, Measure, Analyze, Improve, Control. Incremental process improvement using Six Sigma methodology.
DMAIC can bee seen as a data-driven improvement strategy and for sure is part, or will be a part, of your organizations SIX SIGMA quality initiative. DMAIC is an acronym for: Define, Measure, Analyze, Improve, and Control.
DMAIC is a cyclical process such as the PDCA is. The reason to go for the DMAIC is to strive for the best result possible with a structured approach.
These process steps are:
DEFINE: the customers and their CTQ (Critical to Quality) and the core process involved.
Who are your customers?
What are their requirements for products or services?
What are their expectations?
Go for a value stream and map the process flow through the complete business process
MEASURE:
Define a plan on how to collect data from your core process
Go for different sources of data in order to be as specific as possible on defects and metrics
ANALYZE:
While analyzing the data along the process map make sure to identify the real root cause of defects and
point out opportunities for improvement
Compare shortfalls with the results of customer surveys
Determine gaps between targeted performance and current performance
Prioritize potential improvement measures
Identify variation and their source
IMPROVE:
Kaizen Workshops
Target is to improve the current process in a simple and effective way
Develop a prioritized action plan
Do it!
If you want a structured approach, just read our PDCA article.
CONTROL:
Stay tuned on your process improvement measures
Make sure that they stay on track
Prevent falling back to the “old way”
In the end, when you are in charge, require the full documentation. Make sure that everything implemented is well documented and a clear monitoring is installed that deviation can be fast identified.
Having or installing a sustainable problem solving culture in your organization will be key for the future. Make sure to institutionalize problem solving or a kaizen culture through training, training and more training.
Stay Connected
Ad
We want information fast and in a nutshell. We from OI recommend Blinkist* - because it’s simply the best.
* = Affiliate Link