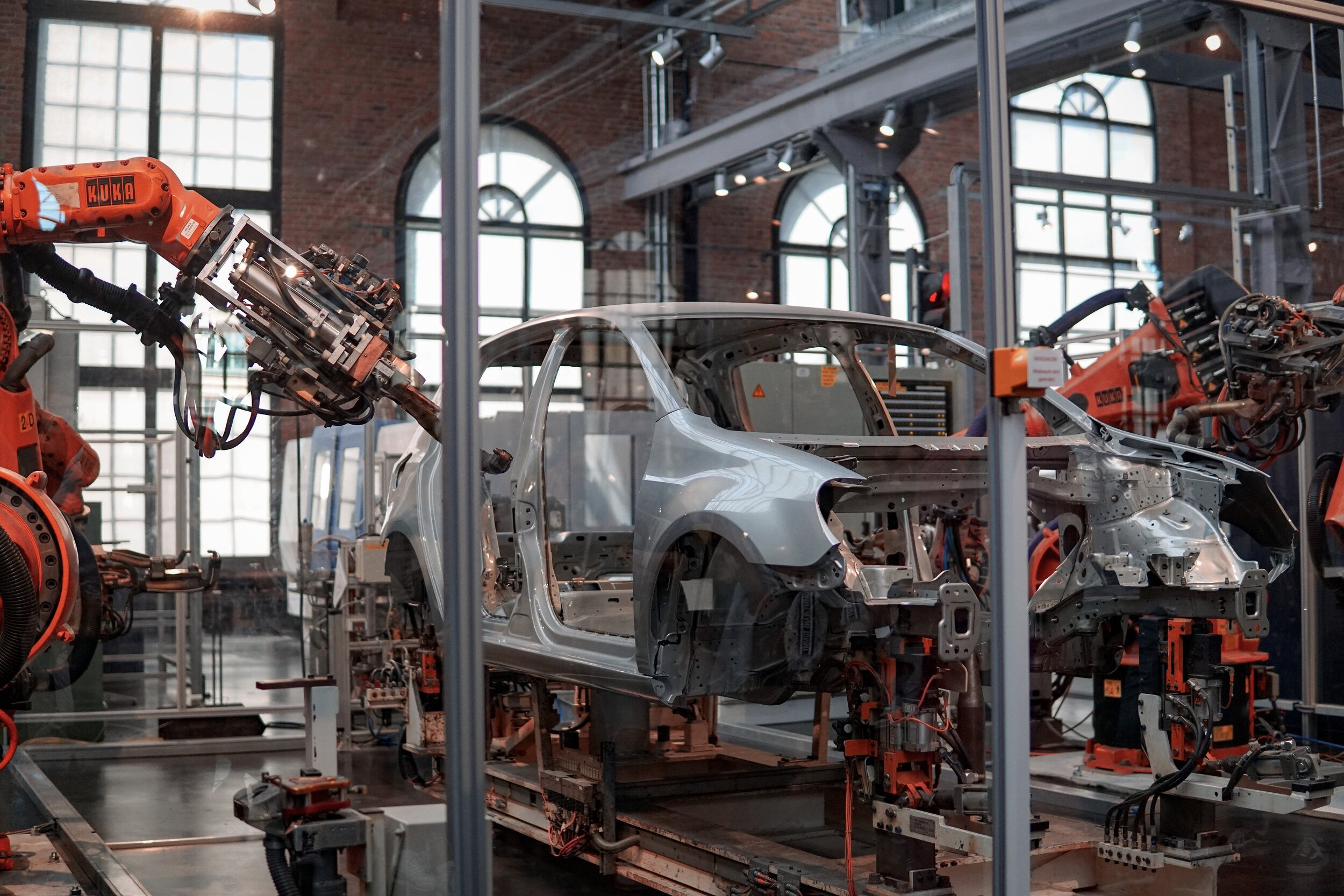
LANGUAGE OF LEAN
Rapid Improvement Event
Rapid Improvement Events, also known as Kaizen events, are a powerful tool for improving production processes in every industry.
Rapid Improvement Events, also known as Kaizen events, are a powerful tool for improving production processes in the manufacturing industry. They are focused, short-term initiatives aimed at solving specific problems and improving processes in a rapid and efficient manner.
At the heart of a Rapid Improvement Event is the involvement of a cross-functional team of employees, each bringing a unique perspective and skillset to the table. The team works together to identify and solve problems, test new ideas, and implement solutions that can have an immediate impact on the production process.
One of the key benefits of Rapid Improvement Events is the speed with which they can deliver results. By focusing on a specific problem and working together as a team, significant improvements can be made in just a few days or weeks. This can be especially valuable in the manufacturing industry, where time is often of the essence and even small improvements can make a big difference.
To ensure the success of a Rapid Improvement Event, it's important to follow a structured methodology. This typically includes the following steps:
Define the problem and scope of the event. What is the specific issue that needs to be addressed, and what is the desired outcome of the event?
Assemble the cross-functional team. Choose team members who have a strong understanding of the problem and can bring a variety of skills and perspectives to the table.
Conduct a thorough analysis of the problem. Gather data, observe processes, and engage in root cause analysis to understand the underlying cause of the problem.
Develop and implement a plan of action. Based on the findings of the analysis, create a plan of action that addresses the root cause of the problem and implements solutions that will improve the production process.
Implement and monitor the changes. Once the plan of action is in place, implement the changes and monitor the results to ensure they are having the desired impact.
Reflect and celebrate successes. Reflect on the successes of the event and celebrate the improvements that were made.
Rapid Improvement Events are a powerful tool for improving production processes in the manufacturing industry. By bringing together a cross-functional team, focusing on a specific problem, and following a structured methodology, organizations can achieve significant improvements in a short amount of time.
In a nutshell, it is important to embrace a continuous improvement mindset and actively seek out opportunities to improve production processes. Rapid Improvement Events provide a structured and efficient way to do just that, delivering results that can have a lasting impact on an organization's success.
Six Sigma
Six Sigma is a highly structured and data-driven methodology used in the manufacturing industry to improve quality and efficiency. Six Sigma offers a powerful toolset to help organizations achieve operational excellence and continuous improvement.
Six Sigma is a highly structured and data-driven methodology used in the manufacturing industry to improve quality and efficiency. Six Sigma offers a powerful toolset to help organizations achieve operational excellence and continuous improvement.
The primary goal of Six Sigma is to eliminate defects and minimize variability in processes, leading to improved customer satisfaction, reduced costs, and increased profitability. This is achieved through a combination of data analysis, statistical methods, and team-based problem-solving.
One of the key elements of Six Sigma is the DMAIC process, which stands for Define, Measure, Analyze, Improve, and Control. This process provides a systematic approach to solving problems and improving processes, starting with a clear definition of the problem, followed by the collection and analysis of data, and ending with the implementation of sustainable solutions.
Another key aspect of Six Sigma is the use of statistical tools and techniques to measure and improve process performance. This includes process mapping, hypothesis testing, design of experiments, and control charts, among others. Six Sigma also relies on a highly-skilled workforce, with individuals trained in statistical analysis and problem-solving techniques.
One of the key benefits of Six Sigma is its ability to drive continuous improvement. This is achieved through regular monitoring and measurement of processes, coupled with ongoing analysis and improvement efforts. Six Sigma provides organizations with a roadmap for sustained, data-driven improvement, helping to ensure that performance gains are maintained over the long-term.
In a nutshell, Six Sigma is a powerful tool in the arsenal of any Lean Management Expert. It provides organizations with a systematic approach to improving quality and efficiency, while also driving continuous improvement and driving long-term success. Whether you are looking to optimize a specific process, or seeking to drive broader organizational change, Six Sigma provides the methodology and tools to help you achieve your goals.
Cell Production
Cell Production focuses on optimizing the flow of work and improving efficiency in manufacturing and operations.
Cell Production focuses on optimizing the flow of work and improving efficiency in manufacturing and operations. It is based on the concept of organizing work into cells, which are self-contained units responsible for performing a specific set of tasks. The goal of cell production is to minimize waste, increase flexibility, and improve overall performance.
The origins of cell production can be traced back to the 1950s and 60s, when Toyota and other Japanese companies were experimenting with new approaches to manufacturing. Over time, the concept of cell production has evolved and been refined, and today it is widely used in a variety of industries, including automotive, electronics, and consumer goods.
In order to implement cell production effectively, there are several key steps that organizations must take. Firstly, it is important to conduct a thorough analysis of the current state of the manufacturing or operations process, in order to identify areas where improvements can be made. This may involve mapping out the flow of work and identifying bottlenecks or other inefficiencies.
Once these areas have been identified, the next step is to reorganize the work into cells, taking into account the specific requirements of each cell and the skills and expertise of the employees who will be working in them. This may involve rearranging physical work spaces, or changing the way that work is assigned and managed.
It is also important to establish clear communication and feedback mechanisms, so that employees and teams can work together effectively. This may involve setting up regular meetings to discuss performance, or implementing systems for tracking and reporting on key metrics.
In order to ensure a successful implementation of cell production, it is also important to provide training and support for employees. This may involve providing training on the new processes and procedures, or offering coaching and mentoring to help employees develop the skills and knowledge they need to be effective.
Another key aspect of cell production is continuous improvement. This involves regularly reviewing performance and making adjustments as needed, in order to optimize efficiency and reduce waste. This may involve experimenting with different approaches, such as implementing new technologies or streamlining processes, in order to find the best solutions.
In conclusion, cell production is a powerful methodology for optimizing performance in operations and manufacturing. By reorganizing work into cells, minimizing waste, and continuously improving performance, organizations can increase efficiency, reduce costs, and improve overall performance. In order to be successful, organizations must take a structured and systematic approach, and be committed to ongoing improvement.
5M Method
5M Method is an other way of describing an ISHIKAWA Diagram.
5M Method is just an other way of describing an ISHIKAWA Diagram. This diagram is pre-structured with five given categories of potential causes: “Man”, “Machine”, “Material”, “Mileu = Environment” and “Methodology”. In a more detailed form of the environment you can further divide it in “management” and “measurement” which then is considered as 7M methodology.
Brown Paper Method
The Brown Paper Method is a practical tool to develop or improve process management in your organization.
What is the Brown Paper Method?
In this article we want to talk about the Brown Paper Method (BPM) in the context of process management.
The Brown Paper Method is an easy to use tool for process development or management for your organization. During a workshop processes are drawn on a large piece of paper (typically from big brown paper roll sticked to a wall) and then analyzed.
Important: Draw the process as they really are not as you think the are. Do a Gemba Walk before this session.
So let us take it as a tool for process management. To be able to understand processes and procedures in your organization and to find out the weak points of them, it is depending on details. Getting those details can be tricky as they might be hidden in the process or in your employees minds and not always so obvious. As mentioned take the Gemba Walks and have a close look on the processes because it usually comes with a taste of complexity. With the Brown Paper Method you then have a simple tool to visualize the complexity in a simply way.
The Brown Paper Method is a pragmatic and result-oriented approach for process audits, presentations or analysis. It is based on a workshop where all involved persons of a process come together in person and collect their findings and doings on brown paper and draw the big picture of the process in total. Through the discussions, that will appear during the workshop, details will be pointed out that matter and defects or weakness will be described and visualized.
With the BPM, the actual process is collected, visualized and analyzed. Target processes can be also developed together. With the Big Picture of the process on brown paper all becomes clear for those involved and the tricky parts of the process are worked out and presented.
Based on the findings of the initial workshop the results are taken to the next level of process modeling. This includes the definition of the target process, implementation of automated workflows and process optimizations.
The process representation on the wall covered with brown paper can contain the following process characteristics:
What triggers and ends the process
Single process steps
Events
Suppliers and customers
KPIs can be important for the process flow (Defect rates, process times, etc.)
Process Input such as raw material, semi finished goods, pre-assemblies, toolings but also information and data such as reports or KPIs
Output and outcome such as finished goods or services
Employees actually executing process steps in the process flow
Employees that have an indirect influence on the process
Other teams or departments related to the process
and so on…
For the upcoming analysis following parts of the brown paper are discussed, additional information added and highlighted:
Critical activities that have a direct impact on the final result of the process including costs and time
Missing or missleading inputs such as information or defective parts
Wrong process steps that are distort the result
Incorrect or missing process step outputs
All potential to improve the process e.g. Kaizen activities marked with a KAIZEN flash
Which of these characteristics finally are listed in the process representation is up to the team as well as the weighting of each. This will then prioritize the potentials identified and when they will be tackled.
Stay Connected
Ad
We want information fast and in a nutshell. We from OI recommend Blinkist* - because it’s simply the best.
* = Affiliate Link