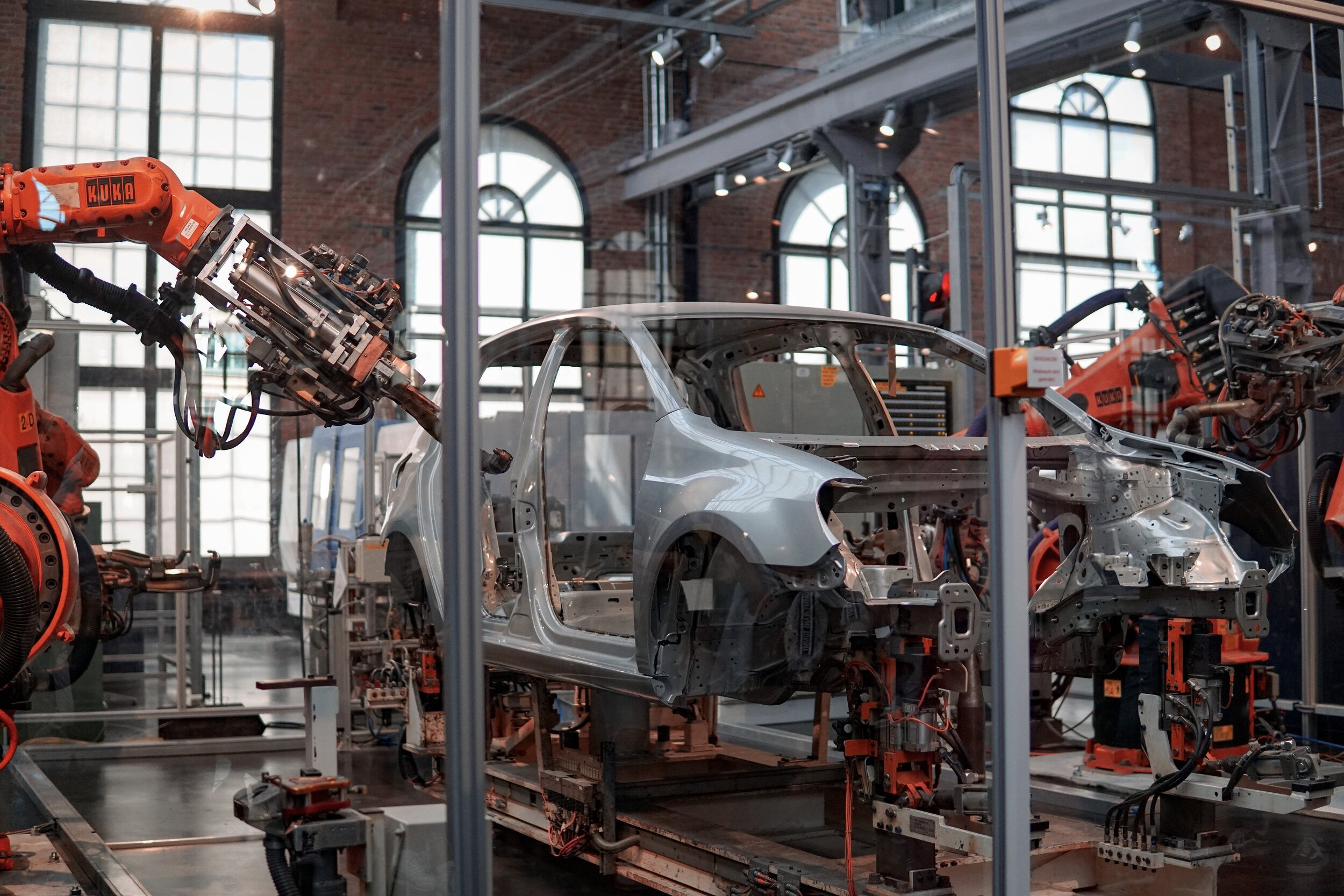
LANGUAGE OF LEAN
Visual Management
How visual management can help you to keep the overview of your operations.
Hej there! Great to have you back! In this article we want to show how visual management can help you to keep track in daily operations.
Generally speaking Lean Management can be seen as a clearly organized workflow that defines the way your organization should work following given principles. Above all principles existing lies to avoid waste in any kind following the 5S Principle as foundation: 1 Sort out 2 Set in order 3 Shine 4 Standardize 5 Sustain.
For a clear visualization of running process in your organization, cleanliness and orderliness is the main part of it. Clarity of your processes on the shop floor is the foundation for all lean manufacturing activities. Having the clarity the implementation and maintaining of visual management methods will guide you to a real state of flow.
In the following we want to describe key basic visual management elements that every production, following the lean principles, should have.
Boards, Notes, Infographics, Brochures and even Movies
Don’t panic and try to explain all those Japanese words it works well without being too technical. Many instruments of the Lean Manufacturing Methodology are very useful to raise the awareness of your employees about lean management. Once implemented and continuously driven by the management the incentives are there to drive daily improvement measures.
The target with visual management and those methods are all the same:
Create transparency
Visual representation of procedures processes and services
Making problems (or bottlenecks) visible
Kanban Boards
Kanban can be literally translated as “card” in the context of a production system. No matter what processes you have, it all starts with a customer’s order. The Kanban card is then used to inform upstream processes about the need of materials, pre-assemblies or process steps. This automatically leads to a cycle that triggers itself through the complete value creation chain.
This is the so called pull principle the advantage if this principle is that, in best case, you have no work in progress which means you have no stock of semi finished goods built up, because only what the following process steps need is produced.
A3 Reports
The term A3 Report comes simply from the size of paper which is used for the documentation of the report. The structure itself follows the PDCA methodology.
The A3 Report is the representation of a problem to be solved. In this case the responsible person from the quality department takes the A3 Report, starts the problem solving actions and follows a systematic structure that makes it possible to describe the effects that are currently leading to a deviation from the standard. Using the A3 only makes sense when you don’t know the root cause yet. If you already know the root cause don’t waste your time. Fix it and go back to normal.
Andon: Lean management with boards and ripcords.
Andon again a Japanese word meaning “lantern”, at least in the context with lean manufacturing. It is a visual aid that is there to draw attention to problems on the shop floor when machines or processes are causing defects or simply stop working.
You might think you have seen them all by walking through production and seeing all those PLC signal lamps indicating green or red, but there is so much more. Just have a look at the Andon article.
Just want to name administration, maybe there is nothing to indicate, but when you think about a document that is needed in a different department, waiting for this is one of the TIMWOODS MUDA. The time waiting is probably the best indicator to start with lean admin activities.
Andon Cords - Please pull the rip cord in an emergency!
Andon Cords are rip cords or a simple button straight at the operation on the shop floor that gives the operator in the process the possibility to instantly stop the line when problems or defects occur.
Andon Boards
Andon Boards are displays or nowadays mainly TV screens that are showing the actual status of the manufacturing line e.g. PPM, down times, etc. Typically it is automatically feeded by the machineries of the production line. With the standard defined color indication everyone sees if they are doing great or not so great. In the second case an automated alert to supervisors or maintenance is triggered.
You see there are many possibilities, but the target is always the same. One hint at the end: Make your boards, infographics or brochures as simple as possible! (or just use mine ;))
WHY? As with processes > it is only a good process when you can’t cut anything more away from it. In other words: What is the value you get from something that nobody understands?
If you take the principle of visual management seriously it will help you to bring all processes in your organization to live.
Stay Connected
Ad
We want information fast and in a nutshell. We from OI recommend Blinkist* - because it’s simply the best.
* = Affiliate Link