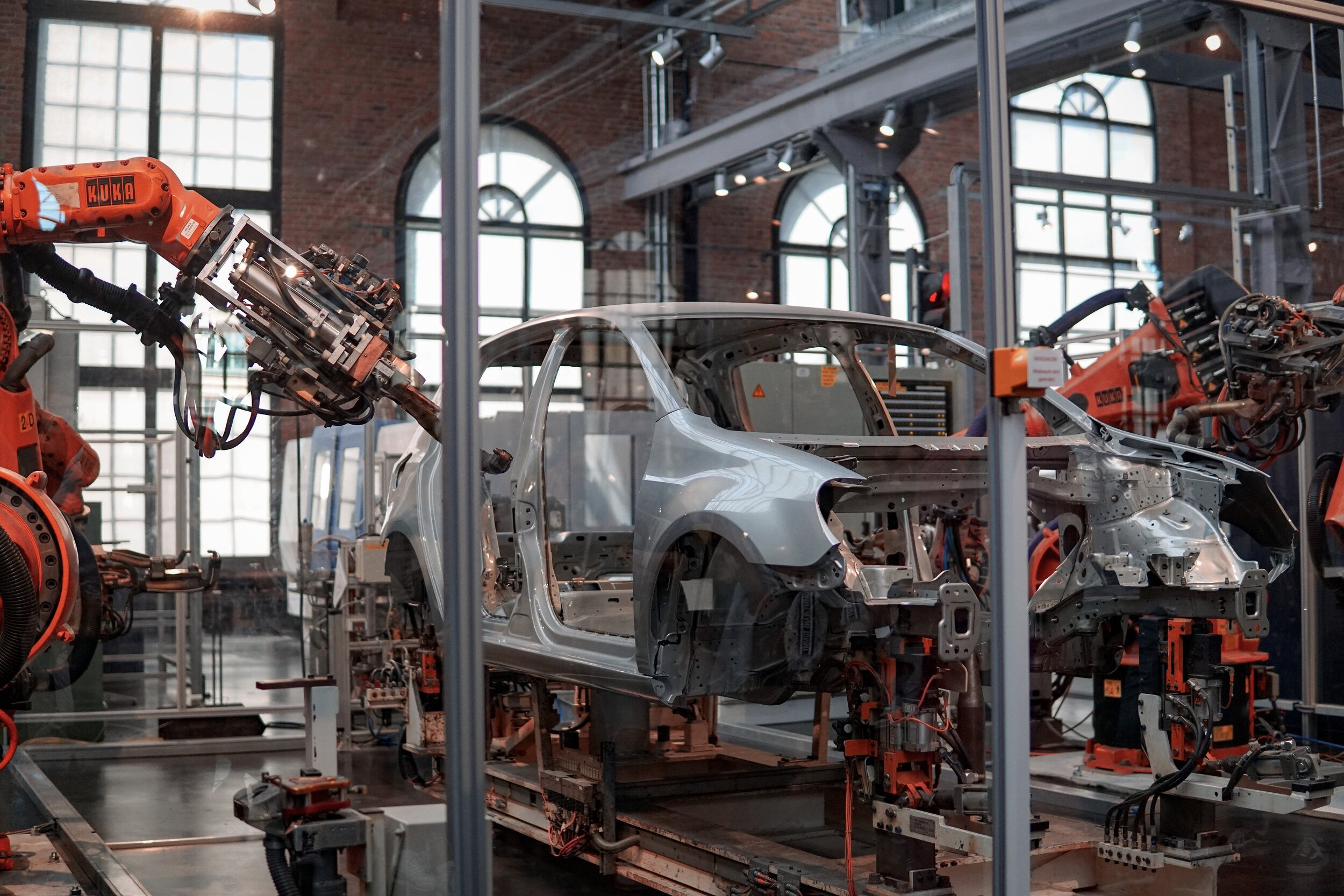
LANGUAGE OF LEAN
FLOW
Flow is one of the key principles of Lean, and it refers to the smooth, uninterrupted progression of work from one step to the next.
Flow is an essential aspect of Lean Management and is closely tied to the value stream of an organization. Lean is a management philosophy that emphasizes the elimination of waste and the creation of value in all areas of a business, from the production floor to the office. Flow is one of the key principles of Lean, and it refers to the smooth, uninterrupted progression of work from one step to the next.
The value stream is the series of activities that a company performs to deliver its products or services to customers. It includes everything from the design and development of a product to the delivery of that product to the customer. The goal of Lean is to optimize the value stream, eliminating waste and ensuring that the flow of work is as efficient as possible.
To achieve flow, Lean experts focus on creating a smooth and continuous flow of work, from the initial stages of design and development to the final stages of delivery and customer service. This requires a deep understanding of the value stream and the identification of any bottlenecks, or areas where work is slowing down or coming to a stop. By removing bottlenecks, Lean experts can increase the speed of work and improve overall efficiency.
One of the key tools used in Lean for optimizing flow is Value Stream Mapping (VSM). VSM is a visual representation of the value stream, showing the flow of work from start to finish, including all the steps involved and the time required for each step. With VSM, Lean experts can identify areas of waste and inefficiency, such as excessive inventory, overprocessing, and wait times.
Another important tool for optimizing flow is Just-In-Time (JIT) manufacturing. JIT is a Lean method that emphasizes the need for production to occur only when it is needed, and no earlier. This helps to eliminate inventory waste and reduces the amount of time spent waiting for parts or materials. JIT also helps to minimize the risks associated with inventory, such as obsolescence, damage, and theft.
Another aspect of flow in Lean is the concept of "pull" production. This means that production should be driven by the demand from customers, rather than by forecasting and forecasting-based production schedules. Pull production helps to ensure that work is only done when it is needed, eliminating the waste associated with overproduction and reducing the risk of obsolescence.
Finally, it's important to understand that flow is not just about efficiency and productivity. It is also about creating a culture of continuous improvement and empowering employees to identify and eliminate waste in their own work. This can be achieved through the use of tools such as Kaizen, a Lean method that encourages employees to identify and suggest improvements to the value stream.
In a nutshell, flow is a critical aspect of Lean Management and is closely tied to the value stream of an organization. By focusing on creating a smooth and continuous flow of work, Lean experts can optimize the value stream, eliminate waste, and improve overall efficiency. Whether through the use of tools such as VSM and JIT, or through a focus on continuous improvement and employee empowerment, flow is a key part of the Lean philosophy and is essential for success in the modern business environment.
One Point Lesson
One Point Lesson (OPL) is a method used in the manufacturing industry that can greatly improve operational efficiency and overall quality.
One Point Lesson (OPL) is a method used in the manufacturing industry that can greatly improve operational efficiency and overall quality. This method is often used within the context of Lean Management, which is a strategy that focuses on maximizing value while minimizing waste. As a Lean Management Expert, I will be discussing how OPL can be used to improve operations in the manufacturing industry.
OPL is a simple but effective tool that helps to standardize and spread best practices across an organization. It is a one-page document that summarizes a lesson learned from a problem or improvement opportunity. This document is designed to be easy to understand and share, so that others can learn from the lesson and apply it in their own work. The purpose of OPL is to promote continuous improvement by capturing and sharing knowledge that can be used to prevent similar problems from happening again in the future.
One of the key benefits of using OPL is that it allows for quick and easy dissemination of knowledge and best practices. The one-page format makes it easy for employees to understand and remember the information, and the lessons learned can be quickly spread throughout the organization. This can lead to significant improvements in the quality of products and services, as well as increased efficiency in operations.
OPL can also help organizations to identify and eliminate non-value-adding activities. This is because the lessons learned can be used to identify areas where improvements can be made, and then the appropriate changes can be implemented. For example, if a problem occurs during the production process, an OPL can be created to document the cause of the problem and how it was resolved. This information can then be used to make changes that will prevent the problem from happening again in the future.
In addition to improving quality and efficiency, OPL can also help organizations to foster a culture of continuous improvement. By capturing and sharing knowledge, employees are encouraged to look for ways to improve processes and to find solutions to problems. This leads to a more engaged workforce, as employees feel that their ideas and contributions are valued.
In order to successfully implement OPL in the manufacturing industry, there are a few key steps that organizations should follow. Firstly, it is important to have a clear understanding of what information should be included in each OPL. This includes the problem or opportunity that was identified, the cause of the problem, the solution that was implemented, and the results of the solution.
Secondly, organizations should develop a system for sharing OPLs throughout the organization. This could be done through regular meetings, email, or an online platform. The key is to make sure that the information is easily accessible and can be quickly shared with others.
Finally, organizations should ensure that they have the resources in place to support the implementation of OPL. This includes providing training to employees on how to create and use OPLs, as well as having dedicated staff to manage the process.
In a nutshell, One Point Lesson (OPL) is a powerful tool that can help organizations in the manufacturing industry to improve quality, efficiency, and overall operations. By standardizing and spreading best practices, organizations can foster a culture of continuous improvement and identify and eliminate non-value-adding activities. To successfully implement OPL, organizations should follow a few key steps, including having a clear understanding of what information should be included in each OPL, developing a system for sharing OPLs, and ensuring that they have the resources in place to support the implementation.
Production Smoothing (Heijunka)
Production smoothing, also known as Heijunka, is a key aspect of modern operations management. It refers to the leveling of production to match customer demand, while maximizing efficiency and minimizing waste.
Production smoothing, also known as Heijunka, is a key aspect of modern operations management. It refers to the leveling of production to match customer demand, while maximizing efficiency and minimizing waste. This technique has been proven to be an effective way to manage production processes and increase competitiveness in the marketplace.
The objective of production smoothing is to create a steady flow of products and services, reducing the variability and fluctuations in the production process. This helps to minimize the waste and resources associated with overproduction, excess inventory, and bottlenecks in the production line. By leveling production, companies can better predict customer demand and adjust their production processes accordingly.
One of the primary benefits of production smoothing is the reduction of waste in the production process. By leveling production, it minimizes the need for excess inventory and eliminates the waste associated with overproduction. This helps to minimize the costs associated with storage, handling, and transportation of excess inventory, while improving overall efficiency.
Another advantage of production smoothing is the improvement of customer satisfaction. By better predicting and matching customer demand, companies can ensure that they have the right products and services available at the right time. This helps to build stronger relationships with customers and improves the overall perception of the company.
To implement production smoothing, companies must first understand their customer demand patterns and the production processes that support them. This requires a thorough analysis of the production line, including the identification of bottlenecks and areas of waste. The company should then develop a production plan that balances customer demand with the production processes to create a steady flow of goods and services.
The company should also implement effective communication and collaboration between all departments, including sales, marketing, engineering, and production. This helps to ensure that all processes are aligned and working together towards the common goal of production smoothing. The company should also consider the use of technology and equipment to automate the production process and improve efficiency.
It is also important to engage employees in the production smoothing process. By involving employees in the implementation and ongoing management of production smoothing, companies can tap into their expertise and insights, and build a culture of continuous improvement. Employees should also receive training and development opportunities to enhance their skills and knowledge in production smoothing techniques.
In a nutshell, production smoothing is an effective way to manage production processes and increase competitiveness in the marketplace. By reducing waste, improving customer satisfaction, and engaging employees, companies can create a steady flow of goods and services, and improve their overall production efficiency. By embracing this technique, companies can achieve operational excellence and maintain their competitive edge in the marketplace.
Product Machine Matrix
The Product Machine Matrix is a methodology that can be used in the manufacturing industry to improve production processes and achieve operational excellence.
The Product Machine Matrix is a methodology that can be used in the manufacturing industry to improve production processes and achieve operational excellence. The idea behind this approach is to create a matrix that matches the type of product being produced with the appropriate machine for that product.
The first step in implementing the Product Machine Matrix is to analyze the current production process and identify areas where improvements can be made. This can be done through the use of data and performance measurement tools, as well as by observing the process and gathering feedback from employees.
Once the areas for improvement have been identified, the next step is to determine the optimal machine for each type of product. This involves considering factors such as the complexity of the product, the volume of production, and the skill level of the operator. It may also be necessary to make changes to the existing machines or to purchase new equipment in order to meet the needs of the production process.
The Product Machine Matrix also requires the establishment of standard work procedures for each machine and product type. This helps to ensure that the production process is consistent and efficient, and it also provides a roadmap for continuous improvement. Standard work procedures should be regularly reviewed and updated based on performance data and feedback from employees.
Another important aspect of the Product Machine Matrix is the need for visual management. This involves creating clear and easy-to-understand visual aids, such as work instructions and flow charts, that help to guide employees through the production process. This helps to prevent errors and improve productivity, as well as making it easier for employees to quickly identify and resolve any issues that may arise.
To be effective, the Product Machine Matrix must be integrated into the overall culture of the organization. This requires the commitment and engagement of employees at all levels, as well as a focus on continuous improvement and a willingness to embrace change. Regular training and communication is also key to the success of the methodology, as it helps to build the necessary skills and knowledge, and ensures that everyone is working towards a common goal.
In a nutshell, the Product Machine Matrix is a powerful methodology that can be used to improve production processes in the manufacturing industry. By carefully matching the type of product with the appropriate machine, and by establishing standard work procedures and utilizing visual management techniques, organizations can achieve operational excellence and drive continuous improvement. With the right approach and commitment, this methodology can deliver significant benefits to any organization looking to optimize its production processes.
Regular Communication
Regular communication refers to the continuous exchange of information between different departments and individuals within an organization.
Regular communication refers to the continuous exchange of information between different departments and individuals within an organization. The aim of this communication is to ensure that everyone is on the same page, working towards the same goals, and that any problems or obstacles are addressed promptly. In this article, we will explore the positives aspects of using regular communication in manufacturing and how it supports shop floor management in three steps.
Improves Collaboration and Cooperation
Regular communication plays an important role in improving collaboration and cooperation within an organization. When everyone is kept informed about the latest developments, it becomes easier for employees to work together effectively. They can share ideas and best practices, identify areas for improvement, and help each other overcome challenges. As a result, teamwork becomes more efficient, and everyone is able to contribute to the success of the organization.
Facilitates Problem Solving
Problems and obstacles are a natural part of any manufacturing process. However, if they are not addressed promptly, they can quickly escalate into bigger issues. Regular communication helps to ensure that problems are identified and addressed in a timely manner. When employees are able to openly communicate with each other, they can work together to find solutions and prevent problems from getting worse. This helps to minimize the impact of any issues on production and ensures that the organization is able to maintain its competitiveness.
Supports Shop Floor Management
Regular communication is also an important aspect of shop floor management. Shop floor management refers to the process of managing the day-to-day operations of a manufacturing facility. Regular communication helps to ensure that everyone is aware of their responsibilities and is able to perform their duties effectively. It also helps to identify areas for improvement and makes it easier for managers to provide feedback and guidance. In addition, regular communication helps to create a culture of continuous improvement, where everyone is encouraged to take an active role in driving progress and improving performance.
In a nutshell, regular communication is a crucial aspect of Lean management in manufacturing. It plays an important role in improving collaboration and cooperation, facilitating problem solving, and supporting shop floor management. By incorporating regular communication into their operations, organizations can ensure that everyone is working together effectively, that problems are addressed promptly, and that the organization is able to maintain its competitiveness.
Cell Production
Cell Production focuses on optimizing the flow of work and improving efficiency in manufacturing and operations.
Cell Production focuses on optimizing the flow of work and improving efficiency in manufacturing and operations. It is based on the concept of organizing work into cells, which are self-contained units responsible for performing a specific set of tasks. The goal of cell production is to minimize waste, increase flexibility, and improve overall performance.
The origins of cell production can be traced back to the 1950s and 60s, when Toyota and other Japanese companies were experimenting with new approaches to manufacturing. Over time, the concept of cell production has evolved and been refined, and today it is widely used in a variety of industries, including automotive, electronics, and consumer goods.
In order to implement cell production effectively, there are several key steps that organizations must take. Firstly, it is important to conduct a thorough analysis of the current state of the manufacturing or operations process, in order to identify areas where improvements can be made. This may involve mapping out the flow of work and identifying bottlenecks or other inefficiencies.
Once these areas have been identified, the next step is to reorganize the work into cells, taking into account the specific requirements of each cell and the skills and expertise of the employees who will be working in them. This may involve rearranging physical work spaces, or changing the way that work is assigned and managed.
It is also important to establish clear communication and feedback mechanisms, so that employees and teams can work together effectively. This may involve setting up regular meetings to discuss performance, or implementing systems for tracking and reporting on key metrics.
In order to ensure a successful implementation of cell production, it is also important to provide training and support for employees. This may involve providing training on the new processes and procedures, or offering coaching and mentoring to help employees develop the skills and knowledge they need to be effective.
Another key aspect of cell production is continuous improvement. This involves regularly reviewing performance and making adjustments as needed, in order to optimize efficiency and reduce waste. This may involve experimenting with different approaches, such as implementing new technologies or streamlining processes, in order to find the best solutions.
In conclusion, cell production is a powerful methodology for optimizing performance in operations and manufacturing. By reorganizing work into cells, minimizing waste, and continuously improving performance, organizations can increase efficiency, reduce costs, and improve overall performance. In order to be successful, organizations must take a structured and systematic approach, and be committed to ongoing improvement.
Blue Sky Workshop
A Blue Sky Workshop is a process that is often used in organizational change management and is designed to promote creative thinking and help organizations to think beyond the boundaries of their current systems and practices.
A Blue Sky Workshop is a process that is often used in organizational change management and is designed to promote creative thinking and help organizations to think beyond the boundaries of their current systems and practices. The origin of Blue Sky Workshops can be traced back to Japan, where they were first developed by a group of industrial engineers as a way to encourage free thinking and help organizations to achieve their full potential.
The purpose of a Blue Sky Workshop is to provide a structured process that allows an organization to step outside of its normal routines and think creatively about the future. This process involves bringing together a group of stakeholders, including senior executives, managers, and employees, to brainstorm and imagine new and innovative ways of working. The workshop is designed to provide a safe and supportive environment where people can let their imaginations run wild and come up with ideas that may not be possible within the constraints of the current organizational structure.
To conduct a Blue Sky Workshop, it is essential to create an atmosphere of openness and collaboration. The facilitator should encourage participants to think outside the box and challenge their existing assumptions about what is possible. It is also important to provide participants with the necessary tools and resources to help them come up with innovative ideas, such as whiteboards, sticky notes, and brainstorming software.
The first step in conducting a Blue Sky Workshop is to establish the objective of the workshop. This should be a specific, measurable, and achievable goal that the participants are trying to achieve. For example, the objective might be to develop a new product, improve customer satisfaction, or reduce costs.
Once the objective has been established, the facilitator should begin by encouraging participants to think about their ideal future. They should ask participants to imagine what their organization would look like if they could achieve their goal, and what challenges they might face along the way. This exercise helps participants to think creatively and generate new ideas that they may not have considered before.
After the initial brainstorming session, the facilitator should then encourage participants to refine their ideas and develop them further. This may involve breaking down the ideas into smaller sub-goals, or exploring the feasibility of different approaches.
Once the ideas have been refined, the facilitator should then help participants to prioritize their ideas based on their potential impact, feasibility, and potential risks. Participants should then be encouraged to develop action plans that outline the steps they will take to achieve their goals.
The final step in the Blue Sky Workshop process is to review and evaluate the progress made. This may involve regular check-ins, progress reports, or other methods of monitoring progress.
In conclusion, the Blue Sky Workshop is a powerful tool for organizations that want to think creatively about the future and develop new and innovative solutions to their problems. By encouraging participants to think beyond their current systems and practices, organizations can achieve their full potential and create a brighter future for themselves and their stakeholders.
Stay Connected
Ad
We want information fast and in a nutshell. We from OI recommend Blinkist* - because it’s simply the best.
* = Affiliate Link