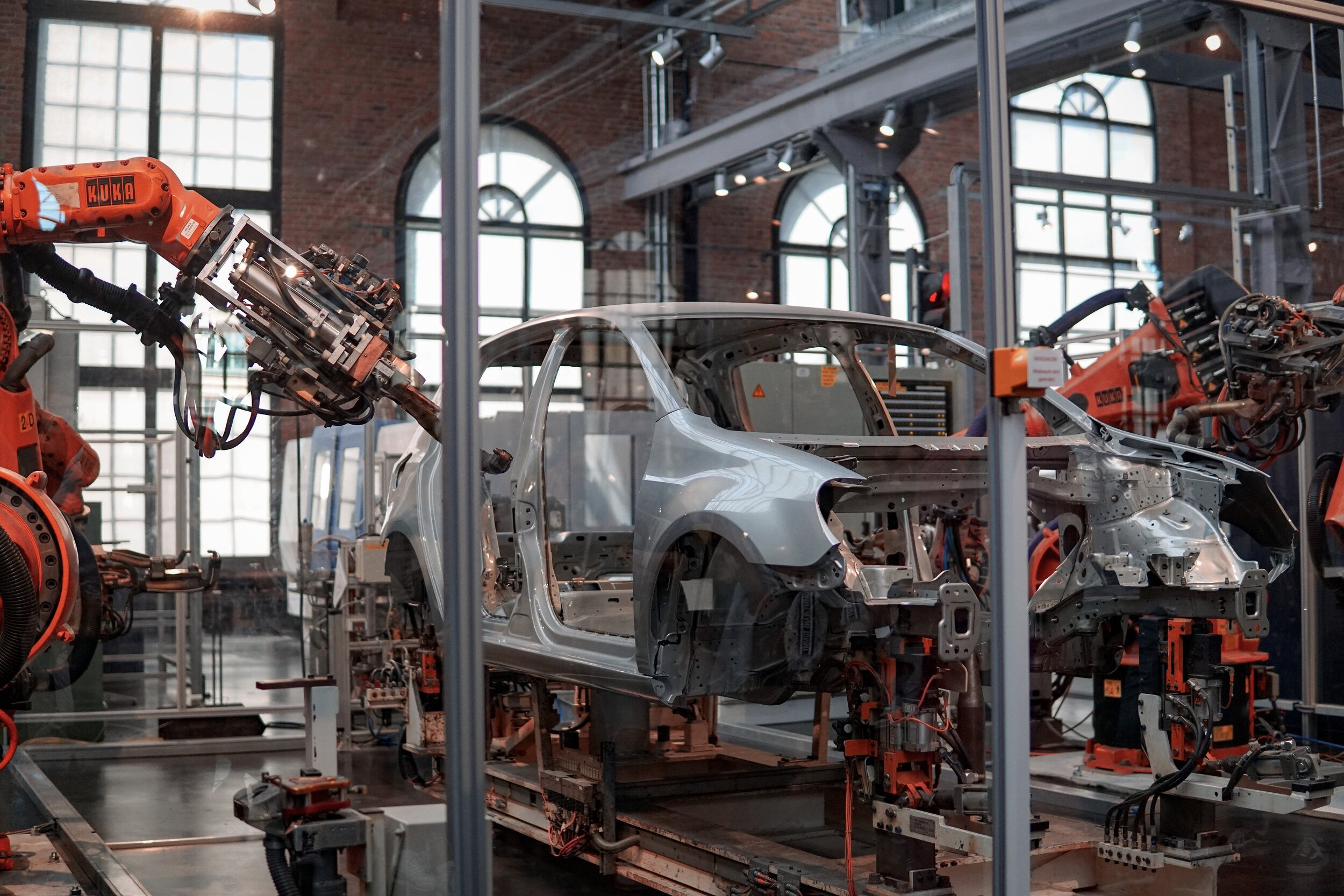
LANGUAGE OF LEAN
Order and Cleanliness
Order and cleanliness are two critical components of a successful and efficient work environment.
Order and cleanliness are two critical components of a successful and efficient work environment. By creating an organized and tidy workspace, employees are able to work more effectively, reduce waste, and increase productivity. One proven method for achieving order and cleanliness is through the use of the 5S Method.
The 5S Method is a system that originated in Japan and focuses on five key principles: Sort, Simplify, Sweep, Standardize, and Sustain. By following these five principles, organizations are able to create a work environment that is efficient, safe, and conducive to high performance.
The first step of the 5S Method is "Sort." This principle involves eliminating items that are no longer necessary or used. This could include outdated equipment, supplies that have been discontinued, or items that have simply outlived their usefulness. By sorting through items and getting rid of what is not needed, organizations are able to free up valuable space and resources.
The second principle of the 5S Method is "Simplify." This step involves organizing the items that remain after the sorting process and finding ways to make the workplace more efficient. This could mean moving items to more accessible locations, labeling items clearly, or rearranging the workspace to make it more user-friendly.
The third step is "Sweep." This principle involves cleaning the workspace and ensuring that it is free of debris and clutter. This not only helps to create a cleaner and more inviting work environment, but it also helps to prevent accidents and injuries.
The fourth step of the 5S Method is "Standardize." This principle involves establishing procedures and processes that ensure the workplace remains organized and clean. This could include regular cleaning schedules, procedures for storing items, and guidelines for maintaining a tidy workspace. By establishing these standards, organizations are able to ensure that the benefits of the 5S Method are sustained over time.
The final step of the 5S Method is "Sustain." This principle involves continuously monitoring and improving the work environment. This could involve regular audits, updating procedures, or incorporating feedback from employees. By continuously improving, organizations are able to maintain the benefits of the 5S Method and ensure that they remain at the forefront of efficiency and productivity.
In a nutshell order and cleanliness are critical components of a successful and efficient work environment. By following the 5S Method, organizations are able to create a work environment that is safe, efficient, and conducive to high performance. Whether you are an office worker or a factory worker, the 5S Method can help you achieve a more productive and effective work environment.
Set up time
The term "set up time" refers to the amount of time it takes to transition a manufacturing process or production line from producing one product to another.
The term "set up time" refers to the amount of time it takes to transition a manufacturing process or production line from producing one product to another. This time includes all the tasks and activities that must be performed in order to prepare the line for the new product, such as cleaning and changing tools, adjusting machinery, and organizing raw materials and supplies.
Set up time has its origins in the field of manufacturing, where reducing the time required to change over from one product to another has been a critical factor in improving efficiency and productivity. The idea behind reducing set up time is that the less time a production line is idle, the more products can be produced, and the more efficiently the production process can run.
To improve set up time, organizations can use a variety of methods and techniques. One approach is to standardize set up procedures, so that the same steps are followed every time a change over is performed. This standardization helps to eliminate waste, reduce the risk of errors, and speed up the process.
Another approach is to use technology to automate and streamline set up procedures. For example, a company might use barcode scanning to quickly and accurately identify the right tools and supplies for a particular change over, or use robotic arms to change tools and adjust machinery, reducing the amount of manual labor required.
Organizations can also make use of visual aids, such as standard work instructions, to help workers understand the set up process and complete it more quickly. These instructions can be displayed in the form of checklists, posters, or other visual aids that are easy to understand and follow.
In addition, organizations can work to minimize the number of set ups required by batching products or running them in a continuous flow, which reduces the need to change over production lines as frequently.
Finally, it is also important to involve workers in the process of improving set up time. By engaging workers in the process and soliciting their input and suggestions, organizations can gain valuable insights into how the process can be improved and find new and innovative ways to reduce set up time.
In conclusion, improving set up time is critical for organizations that want to optimize their production processes and improve efficiency. By using a combination of standardization, technology, visual aids, continuous flow, and worker involvement, organizations can reduce set up time, minimize waste, and improve productivity
Stay Connected
Ad
We want information fast and in a nutshell. We from OI recommend Blinkist* - because it’s simply the best.
* = Affiliate Link