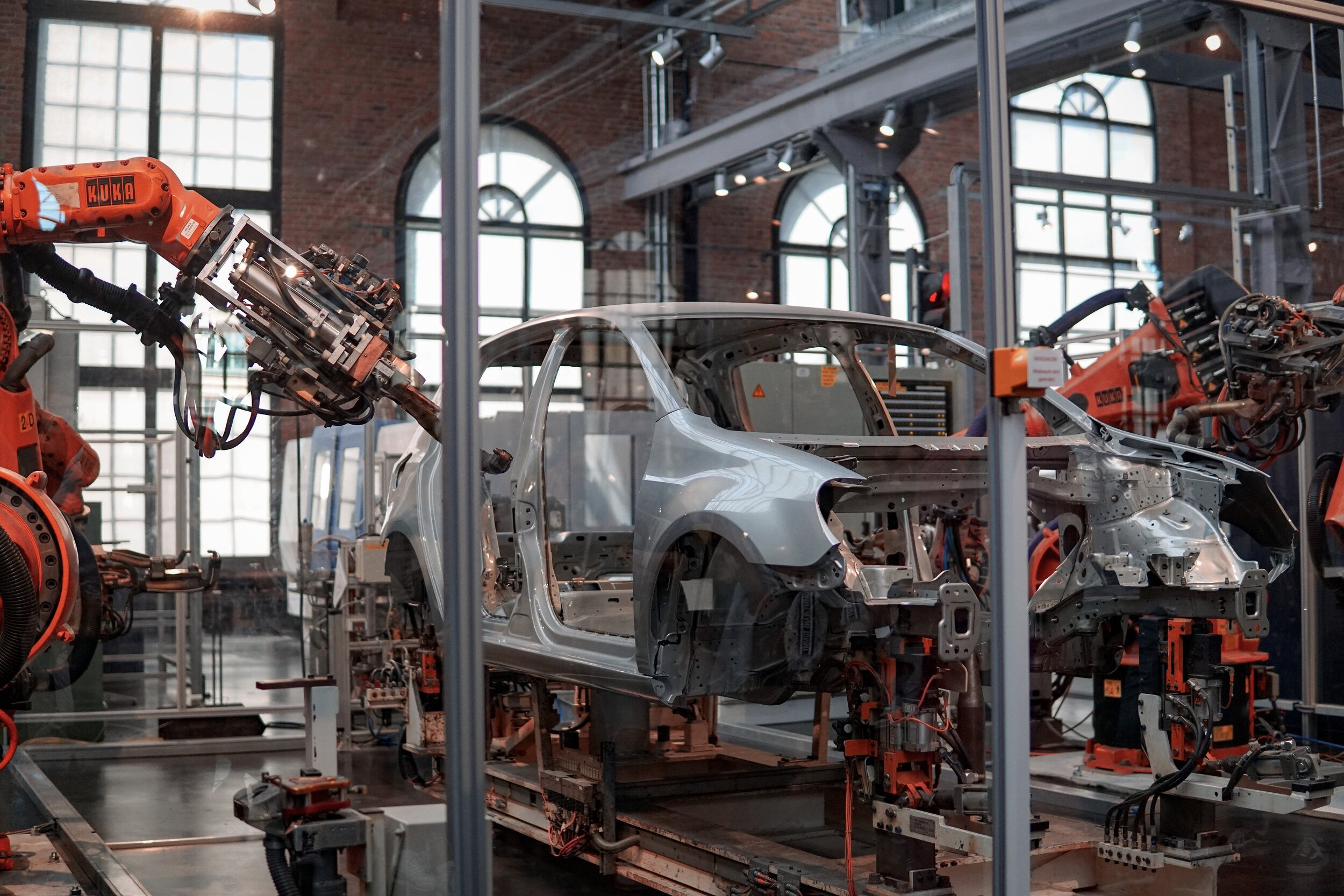
LANGUAGE OF LEAN
Perfection
Perfection is a goal that many organizations strive for, and it is no different in the manufacturing industry.
Perfection is a goal that many organizations strive for, and it is no different in the manufacturing industry. By striving for perfection, manufacturers can improve the quality of their products, reduce waste, and increase efficiency. But how exactly can perfection be achieved in the manufacturing industry?
One of the key components of achieving perfection is through the implementation of a continuous improvement mindset. This involves constantly looking for ways to improve processes, systems, and products. This could include implementing new technology, streamlining processes, or making changes based on customer feedback. By continuously seeking out ways to improve, manufacturers are able to stay ahead of the curve and remain competitive in an ever-evolving industry.
Another critical component of achieving perfection in the manufacturing industry is through effective communication. Communication is key when it comes to identifying and addressing areas for improvement. Whether it is between departments, between management and employees, or between a manufacturer and its customers, effective communication is essential to achieving perfection.
Another way to achieve perfection in the manufacturing industry is through standardization. By establishing and following standardized processes, manufacturers are able to reduce waste, improve quality, and increase efficiency. This could involve standardizing equipment, tools, and work processes, or even creating a standard operating procedure manual that outlines the steps involved in a particular process. By having standardized procedures in place, manufacturers are able to ensure that their products are of the highest quality and that their processes are as efficient as possible.
Quality control is another critical component of achieving perfection in the manufacturing industry. This involves inspecting products and processes to ensure that they meet the standards set by the manufacturer. Quality control processes could include regular inspections, audits, and testing of products, as well as processes such as supplier selection and product design. By implementing a robust quality control system, manufacturers are able to identify and address any issues before they become major problems.
Investing in training and development is another important step in achieving perfection in the manufacturing industry. By providing employees with the training and resources they need to succeed, manufacturers are able to improve the skills and knowledge of their workforce. This could include providing employees with training on new technologies, new processes, or even soft skills such as effective communication and teamwork. By investing in their employees, manufacturers are able to improve their overall operations and move closer to their goal of perfection.
In a nutshell, achieving perfection in the manufacturing industry is a goal that can be achieved through a combination of continuous improvement, effective communication, standardization, quality control, and employee training and development. By striving for excellence in all areas of their operations, manufacturers are able to remain competitive, improve the quality of their products, and provide customers with the best possible experience.
Push Principle
The Push Principle Concept/Term refers to a production system where material and products are manufactured and moved along the production line based on a predicted demand, rather than actual demand.
The Push Principle Concept/Term refers to a production system where material and products are manufactured and moved along the production line based on a predicted demand, rather than actual demand. This system operates under the assumption that the customer demand can be accurately forecasted and the production line can be appropriately scheduled to meet that demand.
However, the Push Principle often leads to negative impacts on operations. One of the main problems with this system is the assumption of accurate demand forecasting. In reality, customer demand is highly unpredictable and can fluctuate rapidly, leading to overproduction and inventory buildup. This excess inventory creates significant problems such as storage and handling costs, obsolescence, and potential quality issues.
Additionally, the Push Principle often results in an inefficient utilization of resources. The production line is designed to produce a set amount of product, regardless of actual demand. This can lead to idle time and equipment, increased energy costs, and reduced production capacity. The production process is also disrupted by production line breakdowns, worker absences, and equipment failures, resulting in increased downtime and decreased efficiency.
Another negative impact of the Push Principle is that it can lead to a lack of focus on customer needs. The emphasis is on meeting a predetermined production schedule, rather than meeting the actual needs of the customer. This can result in an overproduction of products that are not needed, as well as a lack of flexibility to adapt to changing customer demand.
To mitigate these negative impacts, Lean Management experts advocate for the implementation of the Pull Principle. The Pull Principle is a system where production is based on actual customer demand, rather than a predicted demand. This system allows for a more flexible and efficient utilization of resources, as well as a greater focus on meeting the actual needs of the customer.
In a nutshell, the Push Principle can lead to negative impacts on operations such as inventory buildup, resource inefficiency, and a lack of focus on customer needs. Lean Management experts recommend the implementation of the Pull Principle as a more efficient and effective alternative. By focusing on actual customer demand, organizations can achieve greater operational efficiency and meet the needs of their customers.
KOSU
KOSU, short for "Key Operating System Units", is a method used in Lean management and operational excellence to identify and measure the critical units of a process that are essential for the overall performance and success of the operation.
KOSU, short for "Key Operating System Units", is a method used in Lean management and operational excellence to identify and measure the critical units of a process that are essential for the overall performance and success of the operation. By identifying these key units, organizations can focus their improvement efforts on the areas that will have the greatest impact on performance.
The basic idea behind KOSU is to identify the critical units of a process that are essential for the overall performance and success of the operation. This can include things like machines, equipment, personnel, and processes. By identifying these key units, organizations can focus their improvement efforts on the areas that will have the greatest impact on performance.
One of the key benefits of using KOSU is that it helps organizations to identify and prioritize the areas of the process that are most critical to performance. By identifying the key units of a process, organizations can focus their improvement efforts on those areas that will have the greatest impact on performance. This allows them to make the most of their resources and achieve the greatest return on investment.
Another benefit of using KOSU is that it helps organizations to identify and eliminate bottlenecks in the process. By identifying the key units of a process, organizations can identify which units are causing delays and bottlenecks in the process, and then take action to eliminate those bottlenecks. This can include things like improving machine maintenance, optimizing production processes, or identifying areas where automation can be used to improve efficiency.
Using KOSU also helps organizations to identify areas where standardization can be used to improve a process. By identifying the key units of a process, organizations can identify which units are taking longer than they should, and then take action to standardize those processes. This can include things like implementing best practices, developing standard operating procedures, or identifying areas where automation can be used to improve efficiency.
In addition, KOSU can be used to identify areas where automation can be used to improve efficiency. By identifying the key units of a process, organizations can identify which units are taking longer than they should, and then take action to automate those processes. This can include things like using robotics, using automated inspection systems, or using artificial intelligence to optimize production processes.
KOSU also plays a critical role in analyzing machine’s capacity. By identifying the key units of a process, organizations can identify which units are operating at full capacity, and which ones have room for improvement. This can help organizations to optimize their production processes, and ultimately, increase their overall production capacity.
In a nutshell, KOSU is a powerful method for organizations that are committed to operational excellence and continuous improvement. By identifying the key units of a process, organizations can focus their improvement efforts on the areas that will have the greatest impact on performance, eliminate bottlenecks in the process, use standardization to improve a process, use automation to improve efficiency and increase their overall production capacity.
Machine Cycle Time
Machine cycle time is a term used to describe the amount of time it takes for a machine to complete one full cycle of operation.
Machine Cycle Time is a term used to describe the amount of time it takes for a machine to complete one full cycle of operation. In the context of Lean management and operational excellence, machine cycle time is a critical metric that can be used to measure the efficiency and effectiveness of a manufacturing or production process.
The basic idea behind machine cycle time is that it measures the amount of time it takes for a machine to complete a specific task or series of tasks. This can include things like setting up a machine, loading raw materials, running a production process, and unloading finished products. By measuring the amount of time it takes for a machine to complete a full cycle of operation, organizations can gain insight into how efficiently the machine is running and identify areas for improvement.
One of the key benefits of measuring machine cycle time is that it can help organizations to identify bottlenecks and delays in the production process. By measuring the amount of time it takes for a machine to complete a full cycle of operation, organizations can identify which machines or processes are taking longer than they should, and then take action to address these bottlenecks. This can include things like improving machine maintenance, optimizing production processes, or identifying areas where automation can be used to improve efficiency.
Another benefit of measuring machine cycle time is that it can help organizations to identify areas where standardization can be used to improve a process. By measuring the amount of time it takes for a machine to complete a full cycle of operation, organizations can identify which machines or processes are taking longer than they should, and then take action to standardize those processes. This can include things like implementing best practices, developing standard operating procedures, or identifying areas where automation can be used to improve efficiency.
Measuring machine cycle time can also help organizations to identify areas where automation can be used to improve efficiency. By measuring the amount of time it takes for a machine to complete a full cycle of operation, organizations can identify which machines or processes are taking longer than they should, and then take action to automate those processes. This can include things like using robotics, using automated inspection systems, or using artificial intelligence to optimize production processes.
Machine cycle time also plays a critical role in analyzing machine’s capacity. By measuring the amount of time it takes for a machine to complete a full cycle of operation, organizations can identify which machines are operating at full capacity, and which ones have room for improvement. This can help organizations to optimize their production processes, and ultimately, increase their overall production capacity.
In conclusion, machine cycle time is a critical metric that can be used to measure the efficiency and effectiveness of a manufacturing or production process. By measuring the amount of time it takes for a machine to complete a full cycle of operation, organizations can gain insight into how efficiently the machine is running, identify bottlenecks and delays in the production process, identify areas where standardization can be used to improve a process, and identify areas where automation can be used to improve efficiency. Ultimately, measuring machine cycle time is a powerful tool for organizations that are committed to operational excellence and continuous improvement.
Stay Connected
Ad
We want information fast and in a nutshell. We from OI recommend Blinkist* - because it’s simply the best.
* = Affiliate Link