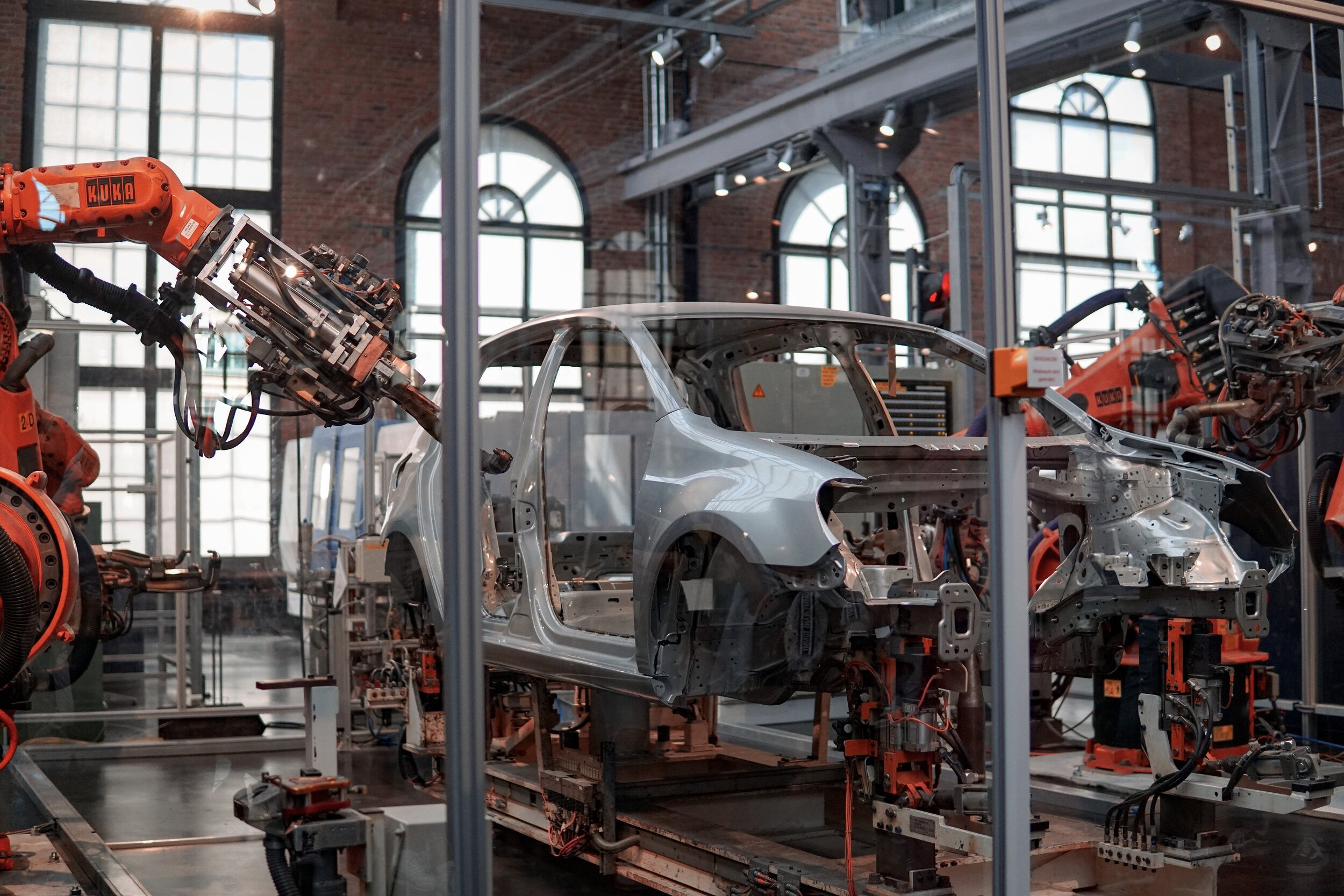
LANGUAGE OF LEAN
Turtle Analysis
“Turtle Diagrams” are an effective tool to understand the processes from both a managerial and workforce perspective.
Turtle Diagrams are an effective method to understand the processes from both a managerial and workforce perspective. These diagrams can also be used to identify gaps in the organizations structure and further develop organizational procedures. From these activities further measures can also be developed for efficiency improvement.
How to use Turtle Diagrams
We will go through the diagram step by step:
INPUT:
Enter details of actual process inputs such as raw material, requirements, information, documents, etc.
PROCESS:
Enter your management process.
OUTPUTS:
Enter your expected or defined output of your process. This can be finished goods, products, records, documentation, etc.
CONGARTS you already described your main process. Now we will complete it with details.
WITH WHAT:
This is asking for materials and equipment. Enter details of materials, components, machinery, test equipment, software, etc. all you use in the process.
WITH WHO:
Resources and competencies. Enter human resources requirements, including qualification, competencies and training requirements or restrictions.
HOW:
The how goes for the supportive processes, procedures and methods. Write down linked processes, pre-processes, supportive processes, instructions, procedures, standard work described, etc.
WHAT FOR:
Key Performance Indicators. Enter the targets, KPIs, performance measures, etc. to measure effectiveness and efficiencies.
Example of a Turtle Diagram
How to use the Turtle Diagram for auditing
When running an internal audit, you can use the Turtle Diagram to understand the relation between input and output for the audited process or activity. In order to get full advantage of the audit, the auditor needs to assess not only the process itself but also the complete surrounding such as the process owner, stakeholders of the process, standard work procedures, training and qualification matrix of persons involved, as well as linked processes. Based on the Turtle Diagram Layout the auditor has a guide to follow through the process audit.
Running the Turtle Analysis
When talking about quality management, process analysis is a key part of daily business. With the Turtle Analysis and the resulting Turtle Diagram you will have the chance to describe processes in a simple and clear one pager. The summary of this one pager is the description of the most important process characteristics. This overview can then be taken to identify risks and weaknesses of the process and build the framework for upcoming quality audits.
The Turtle Diagram gives a clear picture of the links between two process steps or different processes. As usual in manufacturing environment the output of one process step is the input of the other. This can be made visible with the the Turtle Analysis. You starting point is then when interfaces do not run smooth or e.g. important information is lost during hand over phase.
In addition after a Turtle Analysis or audit with the diagram and identified risks and weaknesses you can define specific objectives to be addressed. As mentioned above you can steer and control your improvement actions with pre-defined KPIs, this helps you to visualize deviations from the set course easier.
If you think you need a deep dive on one specific topic found during the Turtle Analysis, we recommend the ISHIKAWA or the 5Why methodology.
Makigami
With the help of a Makigami - administrative processes are recorded and redesigned.
The Japanese term Makigami is developed out of two. First the MAKI (yeah like the Sushi) meaning roll or rolled and KAMI meaning paper. Before you go wild, in the word combination you write kami with “g”. So the question that rises is: What you do with a rolled paper? You use the Makigami to draw and redesign administrative processes. Like with all Lean or Opex activities, once the process is visualized with the help of a Makigami “value-adding” and “non-value adding” activities are marked. On the bottom of the Makigami you will find a time axis which shows the operating time and the pure value adding time.
With the help of the Makigami process analysis, the process is always viewed from the perspective of the process itself, never from the perspective of the employees. This has to be clear also for the waste attack activities in the process. With the Mantra of OPEX: the central question that must be brutaly honest answered: Is the customer willing to pay for this process step/activity? Is this what you are doing adding value to the final product or service?
After you recorded the current state of your process you start to redesign it by asking yourself permanent the following question:
What should the ideal process look like?
Take your planned future development and corporate vision into account to make sure you are not running in the wrong direction.
Stay Connected
Ad
We want information fast and in a nutshell. We from OI recommend Blinkist* - because it’s simply the best.
* = Affiliate Link