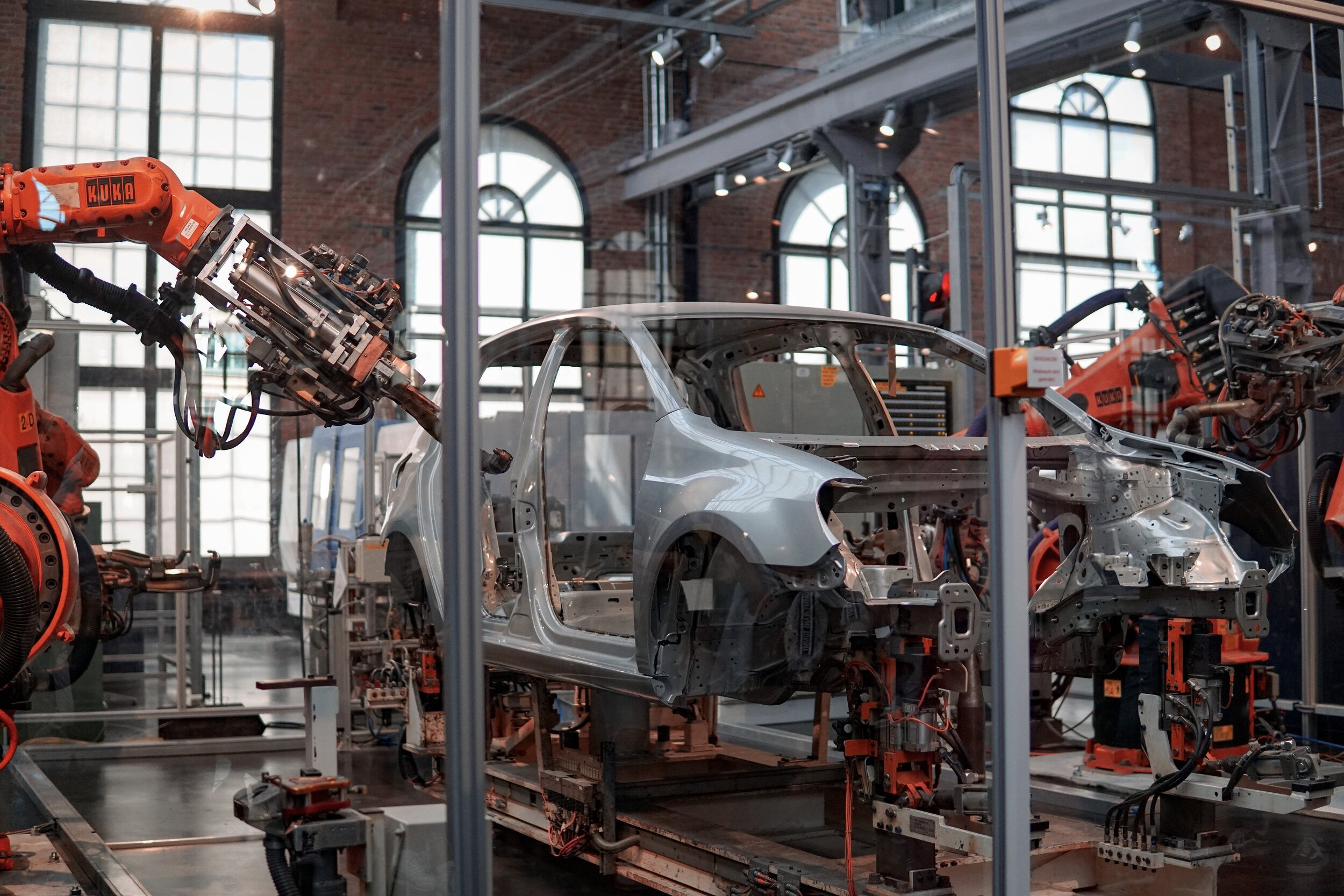
LANGUAGE OF LEAN
FLOW
Flow is one of the key principles of Lean, and it refers to the smooth, uninterrupted progression of work from one step to the next.
Flow is an essential aspect of Lean Management and is closely tied to the value stream of an organization. Lean is a management philosophy that emphasizes the elimination of waste and the creation of value in all areas of a business, from the production floor to the office. Flow is one of the key principles of Lean, and it refers to the smooth, uninterrupted progression of work from one step to the next.
The value stream is the series of activities that a company performs to deliver its products or services to customers. It includes everything from the design and development of a product to the delivery of that product to the customer. The goal of Lean is to optimize the value stream, eliminating waste and ensuring that the flow of work is as efficient as possible.
To achieve flow, Lean experts focus on creating a smooth and continuous flow of work, from the initial stages of design and development to the final stages of delivery and customer service. This requires a deep understanding of the value stream and the identification of any bottlenecks, or areas where work is slowing down or coming to a stop. By removing bottlenecks, Lean experts can increase the speed of work and improve overall efficiency.
One of the key tools used in Lean for optimizing flow is Value Stream Mapping (VSM). VSM is a visual representation of the value stream, showing the flow of work from start to finish, including all the steps involved and the time required for each step. With VSM, Lean experts can identify areas of waste and inefficiency, such as excessive inventory, overprocessing, and wait times.
Another important tool for optimizing flow is Just-In-Time (JIT) manufacturing. JIT is a Lean method that emphasizes the need for production to occur only when it is needed, and no earlier. This helps to eliminate inventory waste and reduces the amount of time spent waiting for parts or materials. JIT also helps to minimize the risks associated with inventory, such as obsolescence, damage, and theft.
Another aspect of flow in Lean is the concept of "pull" production. This means that production should be driven by the demand from customers, rather than by forecasting and forecasting-based production schedules. Pull production helps to ensure that work is only done when it is needed, eliminating the waste associated with overproduction and reducing the risk of obsolescence.
Finally, it's important to understand that flow is not just about efficiency and productivity. It is also about creating a culture of continuous improvement and empowering employees to identify and eliminate waste in their own work. This can be achieved through the use of tools such as Kaizen, a Lean method that encourages employees to identify and suggest improvements to the value stream.
In a nutshell, flow is a critical aspect of Lean Management and is closely tied to the value stream of an organization. By focusing on creating a smooth and continuous flow of work, Lean experts can optimize the value stream, eliminate waste, and improve overall efficiency. Whether through the use of tools such as VSM and JIT, or through a focus on continuous improvement and employee empowerment, flow is a key part of the Lean philosophy and is essential for success in the modern business environment.
One Point Lesson
One Point Lesson (OPL) is a method used in the manufacturing industry that can greatly improve operational efficiency and overall quality.
One Point Lesson (OPL) is a method used in the manufacturing industry that can greatly improve operational efficiency and overall quality. This method is often used within the context of Lean Management, which is a strategy that focuses on maximizing value while minimizing waste. As a Lean Management Expert, I will be discussing how OPL can be used to improve operations in the manufacturing industry.
OPL is a simple but effective tool that helps to standardize and spread best practices across an organization. It is a one-page document that summarizes a lesson learned from a problem or improvement opportunity. This document is designed to be easy to understand and share, so that others can learn from the lesson and apply it in their own work. The purpose of OPL is to promote continuous improvement by capturing and sharing knowledge that can be used to prevent similar problems from happening again in the future.
One of the key benefits of using OPL is that it allows for quick and easy dissemination of knowledge and best practices. The one-page format makes it easy for employees to understand and remember the information, and the lessons learned can be quickly spread throughout the organization. This can lead to significant improvements in the quality of products and services, as well as increased efficiency in operations.
OPL can also help organizations to identify and eliminate non-value-adding activities. This is because the lessons learned can be used to identify areas where improvements can be made, and then the appropriate changes can be implemented. For example, if a problem occurs during the production process, an OPL can be created to document the cause of the problem and how it was resolved. This information can then be used to make changes that will prevent the problem from happening again in the future.
In addition to improving quality and efficiency, OPL can also help organizations to foster a culture of continuous improvement. By capturing and sharing knowledge, employees are encouraged to look for ways to improve processes and to find solutions to problems. This leads to a more engaged workforce, as employees feel that their ideas and contributions are valued.
In order to successfully implement OPL in the manufacturing industry, there are a few key steps that organizations should follow. Firstly, it is important to have a clear understanding of what information should be included in each OPL. This includes the problem or opportunity that was identified, the cause of the problem, the solution that was implemented, and the results of the solution.
Secondly, organizations should develop a system for sharing OPLs throughout the organization. This could be done through regular meetings, email, or an online platform. The key is to make sure that the information is easily accessible and can be quickly shared with others.
Finally, organizations should ensure that they have the resources in place to support the implementation of OPL. This includes providing training to employees on how to create and use OPLs, as well as having dedicated staff to manage the process.
In a nutshell, One Point Lesson (OPL) is a powerful tool that can help organizations in the manufacturing industry to improve quality, efficiency, and overall operations. By standardizing and spreading best practices, organizations can foster a culture of continuous improvement and identify and eliminate non-value-adding activities. To successfully implement OPL, organizations should follow a few key steps, including having a clear understanding of what information should be included in each OPL, developing a system for sharing OPLs, and ensuring that they have the resources in place to support the implementation.
Order and Cleanliness
Order and cleanliness are two critical components of a successful and efficient work environment.
Order and cleanliness are two critical components of a successful and efficient work environment. By creating an organized and tidy workspace, employees are able to work more effectively, reduce waste, and increase productivity. One proven method for achieving order and cleanliness is through the use of the 5S Method.
The 5S Method is a system that originated in Japan and focuses on five key principles: Sort, Simplify, Sweep, Standardize, and Sustain. By following these five principles, organizations are able to create a work environment that is efficient, safe, and conducive to high performance.
The first step of the 5S Method is "Sort." This principle involves eliminating items that are no longer necessary or used. This could include outdated equipment, supplies that have been discontinued, or items that have simply outlived their usefulness. By sorting through items and getting rid of what is not needed, organizations are able to free up valuable space and resources.
The second principle of the 5S Method is "Simplify." This step involves organizing the items that remain after the sorting process and finding ways to make the workplace more efficient. This could mean moving items to more accessible locations, labeling items clearly, or rearranging the workspace to make it more user-friendly.
The third step is "Sweep." This principle involves cleaning the workspace and ensuring that it is free of debris and clutter. This not only helps to create a cleaner and more inviting work environment, but it also helps to prevent accidents and injuries.
The fourth step of the 5S Method is "Standardize." This principle involves establishing procedures and processes that ensure the workplace remains organized and clean. This could include regular cleaning schedules, procedures for storing items, and guidelines for maintaining a tidy workspace. By establishing these standards, organizations are able to ensure that the benefits of the 5S Method are sustained over time.
The final step of the 5S Method is "Sustain." This principle involves continuously monitoring and improving the work environment. This could involve regular audits, updating procedures, or incorporating feedback from employees. By continuously improving, organizations are able to maintain the benefits of the 5S Method and ensure that they remain at the forefront of efficiency and productivity.
In a nutshell order and cleanliness are critical components of a successful and efficient work environment. By following the 5S Method, organizations are able to create a work environment that is safe, efficient, and conducive to high performance. Whether you are an office worker or a factory worker, the 5S Method can help you achieve a more productive and effective work environment.
Standard Work
Standard work is a fundamental principle of Lean manufacturing, a management philosophy that focuses on the elimination of waste and the continuous improvement of processes in order to increase efficiency, quality, and customer satisfaction.
Standard work is a fundamental principle of Lean manufacturing, a management philosophy that focuses on the elimination of waste and the continuous improvement of processes in order to increase efficiency, quality, and customer satisfaction. From the perspective of a Lean management expert, standard work is an essential tool for achieving operational excellence in the manufacturing industry.
Standard work refers to the detailed documentation of the best way to perform a specific task, taking into account factors such as the skills and experience of the workers, the equipment and materials used, and the desired outcome. This documentation should include step-by-step instructions, visual aids, and clear specifications for each step of the process. The goal of standard work is to ensure that each task is performed consistently and to the highest standard possible, regardless of who is performing it or when it is performed.
There are several key benefits to implementing standard work in manufacturing. Firstly, standard work helps to increase efficiency by eliminating waste and reducing variability in the production process. This leads to shorter lead times, lower costs, and improved quality. Secondly, standard work provides a clear understanding of the expected outcome of each task, making it easier for workers to know what is expected of them and to continuously improve their performance. Thirdly, standard work helps to promote a culture of continuous improvement by empowering workers to identify opportunities for improvement and to suggest changes to the standard work documentation.
To implement standard work effectively, Lean management experts typically follow a five-step process:
Define the task: Clearly define what needs to be accomplished and what the desired outcome is.
Observe and document the current process: Observe the current process, and document each step, including the time taken for each step and any variation in the process.
Determine the standard work: Analyze the data from the observation and determine the best way to perform the task, taking into account the skills and experience of the workers, the equipment and materials used, and the desired outcome.
Train the workers: Train the workers on the standard work and ensure that they understand the expectations and how to perform the task to the standard.
Continuously improve: Regularly review the standard work and identify opportunities for improvement.
In addition to the five-step process, Lean management experts also recommend the following ten tips for a successful implementation of standard work:
Start with a few simple tasks and gradually expand the implementation to other areas of the organization.
Engage the workers in the implementation process and involve them in the development of the standard work.
Focus on standardizing the process, not the workers.
Use visual aids, such as flow charts, to help the workers understand the standard work.
Regularly review and update the standard work to reflect changes in the process, the workers, or the equipment.
Foster a culture of continuous improvement by encouraging workers to suggest changes to the standard work.
Make standard work a part of the performance evaluation process for workers.
Use standard work as a tool for training new workers.
Use standard work to identify opportunities for process improvement.
Regularly communicate the importance of standard work and the benefits of implementing it.
In a nutshell, standard work is a powerful tool for achieving operational excellence in the manufacturing industry. From the perspective of a Lean management expert, standard work helps to increase efficiency, improve quality, and empower workers to continuously improve their performance. By following the five-step process and the ten tips for a successful implementation, organizations can reap the benefits of standard work and achieve their operational excellence goals.
Process Chain
The manufacturing industry is a complex system of processes, with each stage relying on the success of the previous one to achieve the final product.
The manufacturing industry is a complex system of processes, with each stage relying on the success of the previous one to achieve the final product. The process chain is the backbone of this system, connecting each stage together to ensure a seamless flow of goods and services.
To achieve the highest level of efficiency in the production process, it is important to understand the process chain and how it serves the production processes. This includes identifying the inputs, outputs, and key activities of each stage, as well as the flow of goods, services, and information throughout the chain.
One of the first steps in optimizing the process chain is to establish clear and standardized procedures for each stage. This includes defining the roles and responsibilities of each team member, as well as establishing a clear communication plan to ensure that everyone is aware of the status of each stage.
Another important factor in optimizing the process chain is to reduce waste and increase efficiency. This can be achieved through continuous improvement efforts, such as streamlining processes, reducing inventory, and minimizing lead times. Lean tools, such as value stream mapping, can be used to identify areas of waste and opportunities for improvement.
Additionally, investing in new technology and equipment can also help to improve the process chain. Automation and digitalization of the production process can lead to faster and more accurate production, as well as reduced labor costs and increased productivity.
Furthermore, involving employees in the continuous improvement process is crucial in achieving the best results. Encouraging their input and ideas can lead to new solutions and creative thinking that can drive process improvement. Employee training and development programs can also help to enhance the skills and knowledge of the workforce, leading to increased efficiency and effectiveness.
Another important aspect of the process chain is supplier selection and management. Careful selection of suppliers can ensure that high-quality inputs are used in the production process, reducing the likelihood of defects and increasing efficiency. Effective supplier management can also ensure timely delivery of goods and services, reducing lead times and minimizing the impact of supply chain disruptions.
In a nutshell, the process chain is a critical component of the manufacturing industry, serving as the foundation for the production processes. By establishing clear procedures, reducing waste and increasing efficiency, investing in new technology, involving employees, and carefully selecting and managing suppliers, manufacturers can optimize the process chain and achieve operational excellence
Pacemaker
"Pacemaker" is a term commonly used in the manufacturing industry to describe a production process that sets the pace for the rest of the production line. Sometimes also considered as bottleneck station.
"Pacemaker" is a term commonly used in the manufacturing industry to describe a production process that sets the pace for the rest of the production line. A pacemaker process is the one that determines the speed and flow of the entire production process, and therefore has a significant impact on the efficiency and productivity of the manufacturing operation. As a Lean Management Expert, it is important to understand the role and significance of a pacemaker in manufacturing, and how to effectively implement this principle for maximum efficiency and profitability.
The concept of a pacemaker process has its roots in the Toyota Production System (TPS), which is the foundation of the Lean Manufacturing philosophy. TPS emphasizes the importance of flow and standardization in manufacturing, and the pacemaker process is a key component in achieving these goals. The pacemaker process is the first step in the production line and sets the standard for the rest of the processes to follow. This means that the pace, efficiency, and quality of the pacemaker process have a direct impact on the entire production line.
In order to effectively implement the pacemaker principle, it is important to carefully select the appropriate process to serve as the pacemaker. This process should be stable, consistent, and capable of producing high-quality products in a timely manner. It is also important to standardize the pacemaker process to ensure that it runs smoothly and consistently, and that the production line can respond to changes in demand or other factors.
Once the pacemaker process has been established, it is important to monitor and measure its performance regularly. This can be done through the use of Key Performance Indicators (KPIs), such as cycle time, quality rate, and productivity. By monitoring these KPIs, it is possible to identify areas for improvement and to make changes to the pacemaker process or the rest of the production line to improve overall efficiency.
In addition to setting the pace for the production line, a pacemaker process can also have a positive impact on the morale of the manufacturing workforce. When employees see that their efforts are making a significant impact on the overall efficiency and success of the operation, they are more likely to be motivated and engaged in their work.
In a nutshell, the pacemaker principle is a key component of the Lean Manufacturing philosophy, and a valuable tool for Lean Management Experts looking to improve the efficiency and profitability of their manufacturing operations. By carefully selecting the pacemaker process, standardizing its performance, monitoring its performance regularly, and using KPIs to track progress, it is possible to achieve maximum efficiency and profitability in the manufacturing industry.
Cell Production
Cell Production focuses on optimizing the flow of work and improving efficiency in manufacturing and operations.
Cell Production focuses on optimizing the flow of work and improving efficiency in manufacturing and operations. It is based on the concept of organizing work into cells, which are self-contained units responsible for performing a specific set of tasks. The goal of cell production is to minimize waste, increase flexibility, and improve overall performance.
The origins of cell production can be traced back to the 1950s and 60s, when Toyota and other Japanese companies were experimenting with new approaches to manufacturing. Over time, the concept of cell production has evolved and been refined, and today it is widely used in a variety of industries, including automotive, electronics, and consumer goods.
In order to implement cell production effectively, there are several key steps that organizations must take. Firstly, it is important to conduct a thorough analysis of the current state of the manufacturing or operations process, in order to identify areas where improvements can be made. This may involve mapping out the flow of work and identifying bottlenecks or other inefficiencies.
Once these areas have been identified, the next step is to reorganize the work into cells, taking into account the specific requirements of each cell and the skills and expertise of the employees who will be working in them. This may involve rearranging physical work spaces, or changing the way that work is assigned and managed.
It is also important to establish clear communication and feedback mechanisms, so that employees and teams can work together effectively. This may involve setting up regular meetings to discuss performance, or implementing systems for tracking and reporting on key metrics.
In order to ensure a successful implementation of cell production, it is also important to provide training and support for employees. This may involve providing training on the new processes and procedures, or offering coaching and mentoring to help employees develop the skills and knowledge they need to be effective.
Another key aspect of cell production is continuous improvement. This involves regularly reviewing performance and making adjustments as needed, in order to optimize efficiency and reduce waste. This may involve experimenting with different approaches, such as implementing new technologies or streamlining processes, in order to find the best solutions.
In conclusion, cell production is a powerful methodology for optimizing performance in operations and manufacturing. By reorganizing work into cells, minimizing waste, and continuously improving performance, organizations can increase efficiency, reduce costs, and improve overall performance. In order to be successful, organizations must take a structured and systematic approach, and be committed to ongoing improvement.
TPM - Total Productive Maintenance
Total Productive Maintenance (TPM) is a maintenance strategy that involves involving all employees in the maintenance process to maximize equipment productivity and minimize downtime.
Total Productive Maintenance (TPM) is a methodology that originated in Japan in the 1970s and has since become a widely recognized and adopted approach to operational excellence in manufacturing and other operations-focused industries. It is a comprehensive approach that seeks to optimize the performance of equipment and processes through a focus on maintaining and improving reliability and efficiency.
The origins of TPM can be traced back to the Japanese auto industry, where manufacturers were seeking ways to increase productivity and competitiveness in the face of increasing global competition. TPM emerged as a response to the need for a more proactive and integrated approach to equipment maintenance, with the goal of improving both productivity and overall equipment effectiveness (OEE).
Over time, TPM has evolved and expanded to encompass a wider range of objectives and activities. Today, it is widely regarded as a best-practice approach to operational excellence, and is widely used in many different industries, including manufacturing, healthcare, and government operations.
One of the key features of TPM is its focus on involving all employees in the maintenance and improvement process. This is achieved through the creation of cross-functional teams and the use of a range of techniques, including root cause analysis, standardization, and continuous improvement.
Another key aspect of TPM is its focus on data-driven decision-making and performance measurement. This involves the collection and analysis of data on equipment and process performance, which is then used to identify areas for improvement and to drive continuous improvement efforts.
When properly implemented, TPM can have a significant impact on organizational performance and competitiveness. This can include improvements in equipment reliability, increased productivity, reduced waste, and improved overall equipment effectiveness (OEE).
To achieve these benefits, it is important to implement TPM in a structured and systematic way, with clear goals and objectives and a strong focus on continuous improvement. This typically involves a multi-phased approach, starting with an assessment of existing processes and equipment, followed by the development of a comprehensive improvement plan and the implementation of specific improvement initiatives.
In a nutshell, TPM is a proven methodology that can help organizations achieve operational excellence by optimizing the performance of their equipment and processes. To achieve success, organizations must approach TPM in a systematic and structured way, with clear goals and objectives, and a strong focus on continuous improvement.
Key points for a successful TPM implementation:
Involve all employees in the process
Focus on data-driven decision-making
Adopt a multi-phased approach
Prioritize continuous improvement
Develop a comprehensive improvement plan.
MTM
MTM (Methods Time Measurement) is a systematic method for analyzing and optimizing work processes that is widely used in the field of Lean Management.
MTM (Methods Time Measurement) is a systematic method for analyzing and optimizing work processes that is widely used in the field of Lean Management. MTM is based on the idea of breaking down work into small, easily analyzed and optimized tasks, and is therefore an important tool for improving efficiency and productivity in operations.
The origin of MTM can be traced back to the early 20th century, when industrial engineers in Europe and the United States first began to develop time-and-motion studies. These early studies sought to identify the most efficient ways to perform tasks and reduce waste in manufacturing operations. Over time, MTM evolved into a standardized methodology, with clear guidelines and tools for process analysis and improvement.
One of the key features of MTM is its focus on standardizing work processes. This is accomplished by breaking down each task into its component parts and then determining the most efficient way to perform each part. The result of this analysis is a set of standardized work methods that can be used to train workers and ensure consistency in operations.
Another important aspect of MTM is its focus on continuous improvement. The MTM methodology includes regular reviews of work processes and the use of data and analysis to identify areas for improvement. This approach helps organizations to continuously improve their operations and remain competitive over time.
One of the best ways to utilize MTM is in the context of Lean management. In Lean, the focus is on identifying and eliminating waste in all aspects of operations. By applying the MTM methodology to work processes, organizations can identify inefficiencies and then work to eliminate them. This helps to create a more streamlined, efficient, and productive work environment.
Another important application of MTM is in the context of training and development. By using MTM to analyze and standardize work processes, organizations can provide clear and consistent training to workers. This helps to ensure that all workers are performing their tasks in the most efficient way, which leads to improved productivity and reduced waste.
Finally, MTM can also be used in the context of project management. By analyzing work processes in advance of a project, organizations can ensure that they have the resources and capabilities needed to complete the project on time and within budget.
In a nutshell, MTM is a powerful tool for improving efficiency and productivity in operations. Its focus on standardizing work processes and its emphasis on continuous improvement make it an ideal methodology for Lean management and for organizations looking to improve their operations over time.
Set up time
The term "set up time" refers to the amount of time it takes to transition a manufacturing process or production line from producing one product to another.
The term "set up time" refers to the amount of time it takes to transition a manufacturing process or production line from producing one product to another. This time includes all the tasks and activities that must be performed in order to prepare the line for the new product, such as cleaning and changing tools, adjusting machinery, and organizing raw materials and supplies.
Set up time has its origins in the field of manufacturing, where reducing the time required to change over from one product to another has been a critical factor in improving efficiency and productivity. The idea behind reducing set up time is that the less time a production line is idle, the more products can be produced, and the more efficiently the production process can run.
To improve set up time, organizations can use a variety of methods and techniques. One approach is to standardize set up procedures, so that the same steps are followed every time a change over is performed. This standardization helps to eliminate waste, reduce the risk of errors, and speed up the process.
Another approach is to use technology to automate and streamline set up procedures. For example, a company might use barcode scanning to quickly and accurately identify the right tools and supplies for a particular change over, or use robotic arms to change tools and adjust machinery, reducing the amount of manual labor required.
Organizations can also make use of visual aids, such as standard work instructions, to help workers understand the set up process and complete it more quickly. These instructions can be displayed in the form of checklists, posters, or other visual aids that are easy to understand and follow.
In addition, organizations can work to minimize the number of set ups required by batching products or running them in a continuous flow, which reduces the need to change over production lines as frequently.
Finally, it is also important to involve workers in the process of improving set up time. By engaging workers in the process and soliciting their input and suggestions, organizations can gain valuable insights into how the process can be improved and find new and innovative ways to reduce set up time.
In conclusion, improving set up time is critical for organizations that want to optimize their production processes and improve efficiency. By using a combination of standardization, technology, visual aids, continuous flow, and worker involvement, organizations can reduce set up time, minimize waste, and improve productivity
Mura
A traditional general Japanese term for unevenness. It is the waste of variation in the production process.
Mura, one of the three types of waste in the Toyota Production System, translates to "unevenness" or "inconsistency" in English. It refers to the irregularity in the flow of work, causing fluctuations in capacity and production. Identifying and removing Mura is essential for creating a steady work pace and optimizing resources.
One of the main causes of Mura is multitasking. When team members are constantly switching between tasks, they often lose focus and efficiency, leading to unevenness in the workflow. This results in longer lead times, increased inventory, and higher costs.
Another cause of Mura is overproduction. Producing more than what is needed, whether it's goods or services, creates an imbalance in the system and results in unnecessary inventory. This not only ties up valuable resources but also increases the risk of defects and rework.
To handle Mura, one must first understand the root cause of the unevenness. This can be done through value stream mapping, a tool that visually represents the flow of work and helps identify areas of waste. By analyzing the current state of the process, one can identify the steps that are causing Mura and implement solutions to eliminate them.
One effective solution is to implement a pull system, also known as "kanban" in Japanese. This system ensures that work is only produced when it is needed, eliminating overproduction and promoting a steady flow of work.
Another solution is to implement standard work. By standardizing the work process, team members are able to work consistently and efficiently, resulting in less Mura. This also helps in identifying and addressing any abnormalities that may occur in the process.
Additionally, involving the team members in problem-solving and continuous improvement activities can lead to increased ownership and accountability, leading to a reduction in Mura.
Implementing a pull system, standard work and involving team members in problem-solving and continuous improvement activities can help organizations to create a steady flow of work and optimize resources.
It's important to note that Mura is not a problem that can be solved once and for all. It's a continuous effort and requires constant monitoring and improvement. Regularly conducting value stream mapping and Gemba walks, where one goes to the place where the work is done to observe and understand the process, can help in identifying and addressing Mura.
In conclusion, Mura is a key concept in lean management and must be addressed to ensure a steady work pace and optimize resources. By understanding the root cause of Mura and implementing solutions such as pull systems, standard work, and involving team members in problem-solving and continuous improvement activities, organizations can achieve the goal of smooth and well-organized workflow.
Standard WIP (SWIP)
The minimum amount of material or a given product, which must be in process at any time to ensure proper flow of the operation.
The minimum amount of material or product that must be in the process at all times to ensure smooth operation.
Standard Work is a little underrated concept in Lean Manufacturing. It is not simply standardization or work standards.
Standard Work is composed of three elements: Takt time, Work sequence and Standard Work in Process (SWIP). Takt Time is a fundamental concept of Lean Manufacturing, and Work Sequence is relatively intuitive. SWIP, however, is a bit more complex.
SWIP refers to the minimum necessary in-process inventory (work in process or WIP) to maintain Standard Work. It is not more or less than what is needed. To calculate the appropriate quantity for SWIP, one must ask a number of questions.
While a rough estimate of SWIP can be obtained by using the equation SWIP = Sum of Cycle Times / Takt Time, it is still necessary to determine where exactly this SWIP should be applied. The following steps provide a guide for determining the appropriate quantity of SWIP:
what’S the team size?
Standard Work is the most efficient combination of manpower, material, and machine, and is based on takt, work sequence, and Standard Work in Process (SWIP). By definition, it should include manual work. If a process is fully automated, it is not considered Standard Work. Instead, it is likely an NC program.
To determine the appropriate team size, the sum of manual cycle time is divided by Takt Time. Therefore, one piece of SWIP per person is required. The equation for manual SWIP would than be:
SWIP(manual) = Team member x (1 piece = person)
When determining the amount of SWIP, there should be no rounding, unless there is less than a full person. In that case, round up to the nearest whole number.
process steps as automatic one-piece cycle machines
Standard Work assumes the use of multiple processes or machines, and separates human and machine tasks as much as possible.
When using an automatic cycle, the worker will only be responsible for loading and unloading, and will not be present during the actual cycle. The automatic cycle time must also be shorter than the Takt Time, ensuring that there is always at least one piece in the machine during each cycle.
This is known as SWIP (single piece auto), and is calculated as the number of single-piece automatic cycle machines multiplied by one piece per machine. There is no rounding necessary as it is not possible to have less than a full machine. However, this only applies to single-piece automatic cycles, and calculations for batch processes or cycles with longer lead times may differ.
process steps as a single-piece non-machine automatic cycle
The term "non-machine automatic cycle" refers to process steps such as the drying time for paint, curing time for epoxy, and cooling time for hot parts.
These process steps may not involve machines, but they do require a certain amount of time for completion. The ratio of this time to the Takt Time is known as the Single-Piece Non-Machine Automatic (SWIP) cycle.
It is important to note that this value should always be rounded up to the nearest whole number. In some cases, equipment like turn tables or FIFO racks may be used to manage the curing process, ensuring that a finished product is available for each takt, and a new one is added for curing.
Process steps with a batch automatic cycle
Batch processes refer to situations in which equipment is designed to unload and load multiple pieces at a time, rather than one piece at a time.
A common example is heat treatment processes where a vacuum must be maintained and the door cannot be opened for hours. In such cases, a batch of parts is removed and then another batch is loaded. The cycle time per piece may be less than the Takt Time, but the overall automatic Cycle Time is greater than the Takt Time.
The Single-Piece Non-Machine Automatic (SWIP) cycle in this case is calculated as (Automatic time / Takt Time) x 2. The reason for this is that in batch processes, which do not allow for the addition or removal of individual pieces during the Takt, an extra quantity of complete parts is required. This concept can be compared to the idea of a pulley and bucket system used to retrieve water from a well, where one bucket is at the bottom of the well, full of water and another bucket is at the top, full of water, and during Takt, you empty out the bucket one by one and fill it back up one by one.
It's worth noting that in formulas 2, 3 and 4, manual cycle time is not included in the calculation because rule #1 takes care of that. This is because every manual Cycle Time must be within Takt by definition of Standard Work and since the unload/load time will involve one piece, there is no need to add manual time back into the calculation (in most of the cases).
Muri
Muri, a Japanese term meaning "unreasonable, impossible, or overburdened," refers to the excessive demands placed on resources, such as equipment and operators, which can lead to wear and production downtime.
Muri, a Japanese term meaning "unreasonable, impossible, or overburdened," refers to the excessive demands placed on resources, such as equipment and operators, which can lead to wear and production downtime. This traditional Japanese concept is often associated with overburden, unreasonableness, and absurdity. However, it can be eliminated through the implementation of standard work practices.
INTRODUCTION
Lean management aims to optimize resources and eliminate wasteful activities in the production process. However, many lean practitioners often focus solely on identifying and eliminating the 7 wastes, known as Muda, neglecting the importance of the other two M's: Mura and Muri.
Identifying and addressing Mura (unevenness) is essential for creating a steady work pace, but it is equally important to identify and address Muri, which is the overburden of resources in the organization's work system. By identifying Muri, organizations can analyze and optimize the capacity of their workforce.
Let's dive deeper into understanding what Muri is and its significance.
What does Muri stand for?
As a lean expert, it's important to understand the concept of Muri, which is a Japanese term meaning "overburden or unreasonable." It is one of the three types of waste (Muda, Mura, Muri) and a key element in the Toyota Production System.
Muri occurs when demands placed on a team exceed their capacity, leading to stress and decreased productivity and efficiency. This can also result in extra working hours and occupational burnouts, negatively impacting team morale and the overall health of the work process.
To avoid this, it's important to be mindful of the workload and to strive for balance at the optimal capacity, where all parts of the system are able to deliver results without the need for extra work. It's also essential to understand the root causes of Muri in order to effectively address it.
What can Muri cause?
It's important to be aware that overburdening teams can occur without conscious intent. Setting unrealistic deadlines, for example, can lead team members to rush their work and result in poor quality and decreased customer satisfaction.
For instance, if a designer is asked to create twice the number of images they are capable of producing within a certain timeframe, it's likely that the final output will not be of the highest quality.
This analogy can be applied to an assembly line as well, where rushing the process can increase the likelihood of low-quality products being delivered to customers. There are various reasons that can contribute to creating Muri and it's important to identify and address them to maintain a smooth and efficient workflow.
Over-demanding
One of the most apparent causes of Muri is over-demanding, where higher management places excessive workloads on teams with the belief that more inputs will result in more outputs.
However, this often leads to a rising number of pending tasks and can cause chaos and burnouts among the team members. This over-demanding behavior is commonly seen in the contemporary business world, it is important for management to be aware of the consequences of overburdening the team, and to instead aim for a balance between inputs and outputs.
Lack of training
The lack of proper training can lead to inefficiencies and the prolonging of tasks. For example, if a team member is not properly trained for a specific task, they may take longer to complete it than necessary.
For instance, if an individual is trained as a copywriter but is assigned tasks of a designer, they may require twice as much time to produce high-quality images as compared to a regular designer who is properly trained for that role.
This highlights the importance of providing proper training and ensuring team members are equipped with the necessary skills to perform their roles effectively, which can help prevent Muri and optimize the workflow.
Lack of communication
Effective communication is crucial for the success of any team. To avoid overburdening, it is essential to establish clear communication channels and practices.
For example, if a meeting with team members is held and a decision is made to create 10 new landing pages for a website, it is important that all team members are informed and aware of the project, including the expected deadline.
Failure to do so, such as in the scenario where a designer is not informed until the last day before the deadline, can lead to overburdening and negative consequences of Muri due to miscommunication. Clear communication can prevent such situations and help teams work efficiently and effectively.
Lack of proper tools and equipment
When the necessary tools and resources are absent, the occurrence of Muri becomes evident and unavoidable. For example, if certain developers are given new computers while others are still using outdated equipment, the latter group will experience overburdening as they will require more time to complete their tasks.
Muri can be caused by various factors, it's important to keep in mind that managing and addressing all of them is crucial in order to maintain a stable and efficient workflow.
To effectively deal with Muri, it's important to identify and understand the root causes, and develop strategies to address them. This may include providing proper tools and resources, implementing clear communication channels, and providing adequate training to ensure that teams have the necessary skills to perform their roles effectively.
Different ways to deal with Muri
Lean management offers various techniques and strategies that can assist in minimizing the negative impact of overburdening or eliminating it altogether.
Map your team’s workflow
A useful starting point in identifying and addressing Muri is to map out your team's workflow. One tool that can aid in this process is a Kanban board, which visually displays the various stages of the workflow and allows for an understanding of your team's capacity and where value is added.
Next, implementing work-in-progress limits for each stage of the workflow can ensure that team members are not juggling multiple tasks at once, but are focusing on completing one task before moving on to the next. This helps to create an efficient pull system, which leads to better organization and prevents overburdening.
When dealing with multiple teams whose work is interdependent, it is important to also implement WIP limits on a global level. For example, if team A is responsible for developing new features for a software service and team B is responsible for deploying those features, but team A is delivering new features faster than team B can deploy them, team B will be constantly overburdened. To avoid this, team A must ensure that team B has the capacity to handle new features before starting work on them. This may mean that team A may have to wait, but it is better to have one team blocked than have the entire company impacted.
Standardize your process
Another approach to addressing Muri is through the implementation of standardization. By documenting all processes and providing thorough training to team members, you can ensure that everyone is equipped to complete their tasks in an efficient and effective manner. This promotes clear communication and helps to eliminate misunderstandings, which can contribute to overburden.
Practice Jidoka
Another Lean management technique that can be used to address Muri is Jidoka. This practice empowers team members to halt the work process if an issue arises, and requires the problem to be resolved before the process can continue. This helps to establish built-in quality standards and prevent the need for rework.
Furthermore, regularly conducting Gemba walks, which involve physically going to the work area to observe and understand what is happening, can also provide insight into where Muri is occurring and how it can be addressed.
In a nutshell
Many businesses unknowingly put excessive demands on their staff, known as Muri in Japanese. This can lead to decreased efficiency and wasted resources, impacting profitability. To address Muri, it is important to:
Provide proper training and necessary tools and equipment to teams
Establish clear communication channels and protocols
Implement standard procedures within the organization
Stay Connected
Ad
We want information fast and in a nutshell. We from OI recommend Blinkist* - because it’s simply the best.
* = Affiliate Link