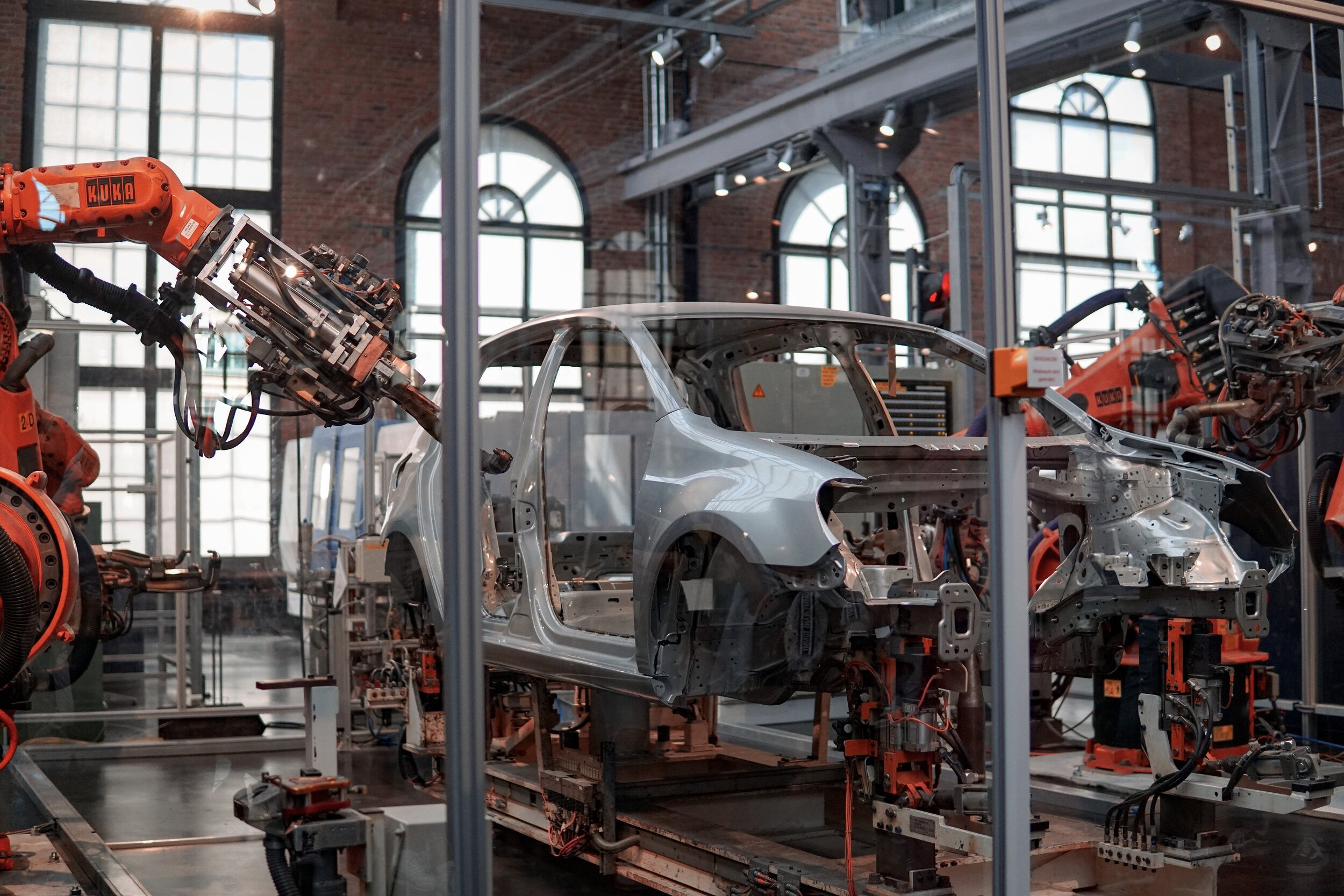
LANGUAGE OF LEAN
FLOW
Flow is one of the key principles of Lean, and it refers to the smooth, uninterrupted progression of work from one step to the next.
Flow is an essential aspect of Lean Management and is closely tied to the value stream of an organization. Lean is a management philosophy that emphasizes the elimination of waste and the creation of value in all areas of a business, from the production floor to the office. Flow is one of the key principles of Lean, and it refers to the smooth, uninterrupted progression of work from one step to the next.
The value stream is the series of activities that a company performs to deliver its products or services to customers. It includes everything from the design and development of a product to the delivery of that product to the customer. The goal of Lean is to optimize the value stream, eliminating waste and ensuring that the flow of work is as efficient as possible.
To achieve flow, Lean experts focus on creating a smooth and continuous flow of work, from the initial stages of design and development to the final stages of delivery and customer service. This requires a deep understanding of the value stream and the identification of any bottlenecks, or areas where work is slowing down or coming to a stop. By removing bottlenecks, Lean experts can increase the speed of work and improve overall efficiency.
One of the key tools used in Lean for optimizing flow is Value Stream Mapping (VSM). VSM is a visual representation of the value stream, showing the flow of work from start to finish, including all the steps involved and the time required for each step. With VSM, Lean experts can identify areas of waste and inefficiency, such as excessive inventory, overprocessing, and wait times.
Another important tool for optimizing flow is Just-In-Time (JIT) manufacturing. JIT is a Lean method that emphasizes the need for production to occur only when it is needed, and no earlier. This helps to eliminate inventory waste and reduces the amount of time spent waiting for parts or materials. JIT also helps to minimize the risks associated with inventory, such as obsolescence, damage, and theft.
Another aspect of flow in Lean is the concept of "pull" production. This means that production should be driven by the demand from customers, rather than by forecasting and forecasting-based production schedules. Pull production helps to ensure that work is only done when it is needed, eliminating the waste associated with overproduction and reducing the risk of obsolescence.
Finally, it's important to understand that flow is not just about efficiency and productivity. It is also about creating a culture of continuous improvement and empowering employees to identify and eliminate waste in their own work. This can be achieved through the use of tools such as Kaizen, a Lean method that encourages employees to identify and suggest improvements to the value stream.
In a nutshell, flow is a critical aspect of Lean Management and is closely tied to the value stream of an organization. By focusing on creating a smooth and continuous flow of work, Lean experts can optimize the value stream, eliminate waste, and improve overall efficiency. Whether through the use of tools such as VSM and JIT, or through a focus on continuous improvement and employee empowerment, flow is a key part of the Lean philosophy and is essential for success in the modern business environment.
Mixed Model Production
We believe that MMP has the potential to bring significant benefits to a production line by increasing efficiency, reducing waste, and improving customer satisfaction.
Mixed Model Production (MMP) is a flexible production strategy that is gaining popularity in the manufacturing industry. We believe that MMP has the potential to bring significant benefits to a production line by increasing efficiency, reducing waste, and improving customer satisfaction.
Mixed Model Production is characterized by the simultaneous production of different models and variations of a product on the same production line. This approach is in contrast to the traditional practice of having a dedicated production line for each product type. In MMP, production is optimized by using a mix of products, models, and variations that can be produced on the same equipment, thereby reducing the need for changeovers, equipment downtime, and material waste.
One of the key benefits of MMP is increased production efficiency. By producing multiple products on the same production line, changeovers and downtime are minimized, reducing the time it takes to produce each product. This increased efficiency results in improved productivity, lower production costs, and higher customer satisfaction.
Another advantage of MMP is reduced waste. The production of multiple products on the same line results in a better utilization of resources and raw materials. This, in turn, reduces the amount of waste generated and the costs associated with waste disposal. Additionally, the reduced downtime results in less energy consumption and a more sustainable production process.
In MMP, the key to success is the ability to schedule production effectively. This requires a deep understanding of the production process, the equipment, and the capabilities of the workforce. A well-designed MMP strategy should be based on a detailed analysis of the production line and a comprehensive understanding of the production process.
The first step in implementing MMP is to identify the different products, models, and variations that can be produced on the same production line. This requires a thorough analysis of the production process and the equipment used. Once the different products have been identified, the next step is to determine the most efficient scheduling of production. This requires a detailed understanding of the production process and the equipment used, as well as the capabilities of the workforce.
The implementation of MMP requires a cross-functional approach that involves teams from different areas of the organization, including production, engineering, and logistics. The success of MMP depends on the collaboration and cooperation of these teams, as well as the effective communication of the MMP strategy to all stakeholders.
In a nutshell, Mixed Model Production is a flexible production strategy that has the potential to bring significant benefits to the manufacturing industry. As a Lean Management and Operational Excellence expert, I believe that MMP has the potential to increase production efficiency, reduce waste, and improve customer satisfaction. However, the success of MMP depends on a detailed understanding of the production process, the equipment, and the workforce, as well as a cross-functional approach that involves teams from different areas of the organization.
One Point Lesson
One Point Lesson (OPL) is a method used in the manufacturing industry that can greatly improve operational efficiency and overall quality.
One Point Lesson (OPL) is a method used in the manufacturing industry that can greatly improve operational efficiency and overall quality. This method is often used within the context of Lean Management, which is a strategy that focuses on maximizing value while minimizing waste. As a Lean Management Expert, I will be discussing how OPL can be used to improve operations in the manufacturing industry.
OPL is a simple but effective tool that helps to standardize and spread best practices across an organization. It is a one-page document that summarizes a lesson learned from a problem or improvement opportunity. This document is designed to be easy to understand and share, so that others can learn from the lesson and apply it in their own work. The purpose of OPL is to promote continuous improvement by capturing and sharing knowledge that can be used to prevent similar problems from happening again in the future.
One of the key benefits of using OPL is that it allows for quick and easy dissemination of knowledge and best practices. The one-page format makes it easy for employees to understand and remember the information, and the lessons learned can be quickly spread throughout the organization. This can lead to significant improvements in the quality of products and services, as well as increased efficiency in operations.
OPL can also help organizations to identify and eliminate non-value-adding activities. This is because the lessons learned can be used to identify areas where improvements can be made, and then the appropriate changes can be implemented. For example, if a problem occurs during the production process, an OPL can be created to document the cause of the problem and how it was resolved. This information can then be used to make changes that will prevent the problem from happening again in the future.
In addition to improving quality and efficiency, OPL can also help organizations to foster a culture of continuous improvement. By capturing and sharing knowledge, employees are encouraged to look for ways to improve processes and to find solutions to problems. This leads to a more engaged workforce, as employees feel that their ideas and contributions are valued.
In order to successfully implement OPL in the manufacturing industry, there are a few key steps that organizations should follow. Firstly, it is important to have a clear understanding of what information should be included in each OPL. This includes the problem or opportunity that was identified, the cause of the problem, the solution that was implemented, and the results of the solution.
Secondly, organizations should develop a system for sharing OPLs throughout the organization. This could be done through regular meetings, email, or an online platform. The key is to make sure that the information is easily accessible and can be quickly shared with others.
Finally, organizations should ensure that they have the resources in place to support the implementation of OPL. This includes providing training to employees on how to create and use OPLs, as well as having dedicated staff to manage the process.
In a nutshell, One Point Lesson (OPL) is a powerful tool that can help organizations in the manufacturing industry to improve quality, efficiency, and overall operations. By standardizing and spreading best practices, organizations can foster a culture of continuous improvement and identify and eliminate non-value-adding activities. To successfully implement OPL, organizations should follow a few key steps, including having a clear understanding of what information should be included in each OPL, developing a system for sharing OPLs, and ensuring that they have the resources in place to support the implementation.
Perfection
Perfection is a goal that many organizations strive for, and it is no different in the manufacturing industry.
Perfection is a goal that many organizations strive for, and it is no different in the manufacturing industry. By striving for perfection, manufacturers can improve the quality of their products, reduce waste, and increase efficiency. But how exactly can perfection be achieved in the manufacturing industry?
One of the key components of achieving perfection is through the implementation of a continuous improvement mindset. This involves constantly looking for ways to improve processes, systems, and products. This could include implementing new technology, streamlining processes, or making changes based on customer feedback. By continuously seeking out ways to improve, manufacturers are able to stay ahead of the curve and remain competitive in an ever-evolving industry.
Another critical component of achieving perfection in the manufacturing industry is through effective communication. Communication is key when it comes to identifying and addressing areas for improvement. Whether it is between departments, between management and employees, or between a manufacturer and its customers, effective communication is essential to achieving perfection.
Another way to achieve perfection in the manufacturing industry is through standardization. By establishing and following standardized processes, manufacturers are able to reduce waste, improve quality, and increase efficiency. This could involve standardizing equipment, tools, and work processes, or even creating a standard operating procedure manual that outlines the steps involved in a particular process. By having standardized procedures in place, manufacturers are able to ensure that their products are of the highest quality and that their processes are as efficient as possible.
Quality control is another critical component of achieving perfection in the manufacturing industry. This involves inspecting products and processes to ensure that they meet the standards set by the manufacturer. Quality control processes could include regular inspections, audits, and testing of products, as well as processes such as supplier selection and product design. By implementing a robust quality control system, manufacturers are able to identify and address any issues before they become major problems.
Investing in training and development is another important step in achieving perfection in the manufacturing industry. By providing employees with the training and resources they need to succeed, manufacturers are able to improve the skills and knowledge of their workforce. This could include providing employees with training on new technologies, new processes, or even soft skills such as effective communication and teamwork. By investing in their employees, manufacturers are able to improve their overall operations and move closer to their goal of perfection.
In a nutshell, achieving perfection in the manufacturing industry is a goal that can be achieved through a combination of continuous improvement, effective communication, standardization, quality control, and employee training and development. By striving for excellence in all areas of their operations, manufacturers are able to remain competitive, improve the quality of their products, and provide customers with the best possible experience.
Production Smoothing (Heijunka)
Production smoothing, also known as Heijunka, is a key aspect of modern operations management. It refers to the leveling of production to match customer demand, while maximizing efficiency and minimizing waste.
Production smoothing, also known as Heijunka, is a key aspect of modern operations management. It refers to the leveling of production to match customer demand, while maximizing efficiency and minimizing waste. This technique has been proven to be an effective way to manage production processes and increase competitiveness in the marketplace.
The objective of production smoothing is to create a steady flow of products and services, reducing the variability and fluctuations in the production process. This helps to minimize the waste and resources associated with overproduction, excess inventory, and bottlenecks in the production line. By leveling production, companies can better predict customer demand and adjust their production processes accordingly.
One of the primary benefits of production smoothing is the reduction of waste in the production process. By leveling production, it minimizes the need for excess inventory and eliminates the waste associated with overproduction. This helps to minimize the costs associated with storage, handling, and transportation of excess inventory, while improving overall efficiency.
Another advantage of production smoothing is the improvement of customer satisfaction. By better predicting and matching customer demand, companies can ensure that they have the right products and services available at the right time. This helps to build stronger relationships with customers and improves the overall perception of the company.
To implement production smoothing, companies must first understand their customer demand patterns and the production processes that support them. This requires a thorough analysis of the production line, including the identification of bottlenecks and areas of waste. The company should then develop a production plan that balances customer demand with the production processes to create a steady flow of goods and services.
The company should also implement effective communication and collaboration between all departments, including sales, marketing, engineering, and production. This helps to ensure that all processes are aligned and working together towards the common goal of production smoothing. The company should also consider the use of technology and equipment to automate the production process and improve efficiency.
It is also important to engage employees in the production smoothing process. By involving employees in the implementation and ongoing management of production smoothing, companies can tap into their expertise and insights, and build a culture of continuous improvement. Employees should also receive training and development opportunities to enhance their skills and knowledge in production smoothing techniques.
In a nutshell, production smoothing is an effective way to manage production processes and increase competitiveness in the marketplace. By reducing waste, improving customer satisfaction, and engaging employees, companies can create a steady flow of goods and services, and improve their overall production efficiency. By embracing this technique, companies can achieve operational excellence and maintain their competitive edge in the marketplace.
Standard Work
Standard work is a fundamental principle of Lean manufacturing, a management philosophy that focuses on the elimination of waste and the continuous improvement of processes in order to increase efficiency, quality, and customer satisfaction.
Standard work is a fundamental principle of Lean manufacturing, a management philosophy that focuses on the elimination of waste and the continuous improvement of processes in order to increase efficiency, quality, and customer satisfaction. From the perspective of a Lean management expert, standard work is an essential tool for achieving operational excellence in the manufacturing industry.
Standard work refers to the detailed documentation of the best way to perform a specific task, taking into account factors such as the skills and experience of the workers, the equipment and materials used, and the desired outcome. This documentation should include step-by-step instructions, visual aids, and clear specifications for each step of the process. The goal of standard work is to ensure that each task is performed consistently and to the highest standard possible, regardless of who is performing it or when it is performed.
There are several key benefits to implementing standard work in manufacturing. Firstly, standard work helps to increase efficiency by eliminating waste and reducing variability in the production process. This leads to shorter lead times, lower costs, and improved quality. Secondly, standard work provides a clear understanding of the expected outcome of each task, making it easier for workers to know what is expected of them and to continuously improve their performance. Thirdly, standard work helps to promote a culture of continuous improvement by empowering workers to identify opportunities for improvement and to suggest changes to the standard work documentation.
To implement standard work effectively, Lean management experts typically follow a five-step process:
Define the task: Clearly define what needs to be accomplished and what the desired outcome is.
Observe and document the current process: Observe the current process, and document each step, including the time taken for each step and any variation in the process.
Determine the standard work: Analyze the data from the observation and determine the best way to perform the task, taking into account the skills and experience of the workers, the equipment and materials used, and the desired outcome.
Train the workers: Train the workers on the standard work and ensure that they understand the expectations and how to perform the task to the standard.
Continuously improve: Regularly review the standard work and identify opportunities for improvement.
In addition to the five-step process, Lean management experts also recommend the following ten tips for a successful implementation of standard work:
Start with a few simple tasks and gradually expand the implementation to other areas of the organization.
Engage the workers in the implementation process and involve them in the development of the standard work.
Focus on standardizing the process, not the workers.
Use visual aids, such as flow charts, to help the workers understand the standard work.
Regularly review and update the standard work to reflect changes in the process, the workers, or the equipment.
Foster a culture of continuous improvement by encouraging workers to suggest changes to the standard work.
Make standard work a part of the performance evaluation process for workers.
Use standard work as a tool for training new workers.
Use standard work to identify opportunities for process improvement.
Regularly communicate the importance of standard work and the benefits of implementing it.
In a nutshell, standard work is a powerful tool for achieving operational excellence in the manufacturing industry. From the perspective of a Lean management expert, standard work helps to increase efficiency, improve quality, and empower workers to continuously improve their performance. By following the five-step process and the ten tips for a successful implementation, organizations can reap the benefits of standard work and achieve their operational excellence goals.
Cellularization
Cellularization is a lean manufacturing methodology that aims to optimize the flow of materials, information, and people within a manufacturing or production environment.
Cellularization is a lean manufacturing methodology that aims to optimize the flow of materials, information, and people within a manufacturing or production environment. Its goal is to create a more efficient, flexible, and responsive production system that can quickly adapt to changing customer demands and market conditions.
The origin of cellularization can be traced back to the early days of the Toyota Production System (TPS), which was developed in the 1950s and 60s. TPS was based on the principles of Just-In-Time (JIT) production and was designed to reduce waste, improve quality, and increase productivity. The concept of cellularization emerged as a way to create small, self-contained production cells that were optimized for specific product families or types of work.
The core idea behind cellularization is to create a flow of work that is highly synchronized and integrated, with minimal inventory and waste. This is achieved by organizing the production environment into cells that are designed to handle specific product families or product types. Each cell is equipped with the necessary tools, equipment, and materials to complete the work in a continuous flow, without the need for batch processing or work-in-progress storage.
Cellularization also requires a cross-functional team approach, where workers from different areas of the organization come together to work on a specific product family or type of work. This team-based approach helps to ensure that everyone has a clear understanding of the work, and it encourages collaboration and communication between different departments.
One of the key benefits of cellularization is that it enables organizations to respond quickly to changes in customer demand and market conditions. For example, if a new product is introduced, the production cell for that product can be quickly reconfigured to accommodate the new work. This agility is a critical advantage in today's fast-paced and highly competitive market.
Another benefit of cellularization is that it promotes continuous improvement. The small, self-contained nature of the cells allows for close observation and monitoring of the work, which in turn enables quick and effective identification and elimination of waste. The cross-functional teams are also empowered to identify and implement improvements that can be made to the production process.
To effectively implement cellularization, organizations need to carefully consider the following factors:
Work flow design: The first step in implementing cellularization is to carefully design the work flow to ensure that it is optimized for the specific product family or type of work being performed.
Equipment selection: The right tools and equipment are critical to the success of cellularization. Organizations need to carefully select the tools and equipment that will be used in each cell, and ensure that they are properly maintained and calibrated.
Cross-functional teams: Teams of workers from different departments must be assembled to work together in each cell. These teams need to be trained on the new work processes, and encouraged to collaborate and communicate effectively.
Lean leadership: Leaders at all levels of the organization need to embrace the principles of lean manufacturing and support the implementation of cellularization. This includes providing the resources, training, and coaching that teams need to succeed.
In a nutshell, cellularization is a powerful and effective methodology for optimizing the flow of materials, information, and people within a manufacturing or production environment. Its success depends on careful design of the work flow, selection of the right tools and equipment, and the development of cross-functional teams. With the right leadership and support, cellularization can help organizations to achieve greater efficiency, flexibility, and responsiveness, and to remain competitive in today's fast-paced and dynamic market
Push Principle
The Push Principle Concept/Term refers to a production system where material and products are manufactured and moved along the production line based on a predicted demand, rather than actual demand.
The Push Principle Concept/Term refers to a production system where material and products are manufactured and moved along the production line based on a predicted demand, rather than actual demand. This system operates under the assumption that the customer demand can be accurately forecasted and the production line can be appropriately scheduled to meet that demand.
However, the Push Principle often leads to negative impacts on operations. One of the main problems with this system is the assumption of accurate demand forecasting. In reality, customer demand is highly unpredictable and can fluctuate rapidly, leading to overproduction and inventory buildup. This excess inventory creates significant problems such as storage and handling costs, obsolescence, and potential quality issues.
Additionally, the Push Principle often results in an inefficient utilization of resources. The production line is designed to produce a set amount of product, regardless of actual demand. This can lead to idle time and equipment, increased energy costs, and reduced production capacity. The production process is also disrupted by production line breakdowns, worker absences, and equipment failures, resulting in increased downtime and decreased efficiency.
Another negative impact of the Push Principle is that it can lead to a lack of focus on customer needs. The emphasis is on meeting a predetermined production schedule, rather than meeting the actual needs of the customer. This can result in an overproduction of products that are not needed, as well as a lack of flexibility to adapt to changing customer demand.
To mitigate these negative impacts, Lean Management experts advocate for the implementation of the Pull Principle. The Pull Principle is a system where production is based on actual customer demand, rather than a predicted demand. This system allows for a more flexible and efficient utilization of resources, as well as a greater focus on meeting the actual needs of the customer.
In a nutshell, the Push Principle can lead to negative impacts on operations such as inventory buildup, resource inefficiency, and a lack of focus on customer needs. Lean Management experts recommend the implementation of the Pull Principle as a more efficient and effective alternative. By focusing on actual customer demand, organizations can achieve greater operational efficiency and meet the needs of their customers.
Stay Connected
Ad
We want information fast and in a nutshell. We from OI recommend Blinkist* - because it’s simply the best.
* = Affiliate Link