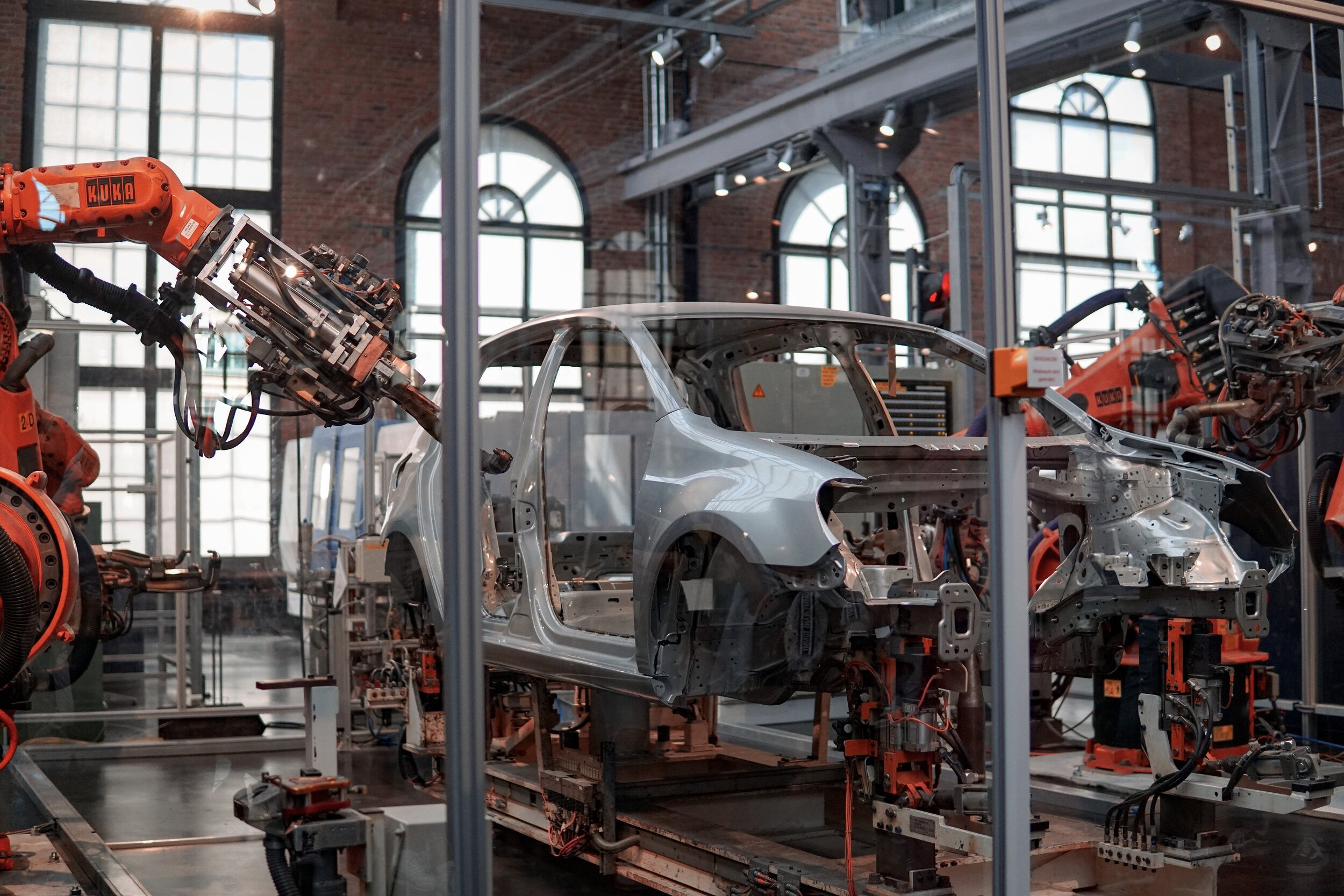
LANGUAGE OF LEAN
Set up time
The term "set up time" refers to the amount of time it takes to transition a manufacturing process or production line from producing one product to another.
The term "set up time" refers to the amount of time it takes to transition a manufacturing process or production line from producing one product to another. This time includes all the tasks and activities that must be performed in order to prepare the line for the new product, such as cleaning and changing tools, adjusting machinery, and organizing raw materials and supplies.
Set up time has its origins in the field of manufacturing, where reducing the time required to change over from one product to another has been a critical factor in improving efficiency and productivity. The idea behind reducing set up time is that the less time a production line is idle, the more products can be produced, and the more efficiently the production process can run.
To improve set up time, organizations can use a variety of methods and techniques. One approach is to standardize set up procedures, so that the same steps are followed every time a change over is performed. This standardization helps to eliminate waste, reduce the risk of errors, and speed up the process.
Another approach is to use technology to automate and streamline set up procedures. For example, a company might use barcode scanning to quickly and accurately identify the right tools and supplies for a particular change over, or use robotic arms to change tools and adjust machinery, reducing the amount of manual labor required.
Organizations can also make use of visual aids, such as standard work instructions, to help workers understand the set up process and complete it more quickly. These instructions can be displayed in the form of checklists, posters, or other visual aids that are easy to understand and follow.
In addition, organizations can work to minimize the number of set ups required by batching products or running them in a continuous flow, which reduces the need to change over production lines as frequently.
Finally, it is also important to involve workers in the process of improving set up time. By engaging workers in the process and soliciting their input and suggestions, organizations can gain valuable insights into how the process can be improved and find new and innovative ways to reduce set up time.
In conclusion, improving set up time is critical for organizations that want to optimize their production processes and improve efficiency. By using a combination of standardization, technology, visual aids, continuous flow, and worker involvement, organizations can reduce set up time, minimize waste, and improve productivity
Set up time reduction
Set up time reduction. Nice and simple.
First things first. In order to reduce set-up time the set-up process itself must be observed and analyzed (e.g. by using the EMIPS - eliminate, minimize, integrate, parallelize or synchronize - methodology).
After you have analyzed the process make sure you write down all identified kinds of waste. Try to define the ideal state of the new procedure. Only after verification through testing of the new procedure make it a standard and implement it in your TPM framework. By doing so your operators are now responsible for the new set-up procedure, assumed that your operators are properly trained.
The whole focus on set-up time reduction comes from the customer requirements to manufacture a higher variety of goods in smaller batches. In order to meet those requirements set-up or change over must be kept as short as possible.
But let us go a little bit more into the details.
The pure set-up time is defined as the time needed to change from the last part of a batch to the first part of the following batch.
The set-up includes all activities needed, preparation, action on side and adjustments needed. By doing this you automatically differentiate between so called “external” and “internal” activities.
The following steps should help you to make it easier to reduce set-up times
1 Classify each part of the set-up process to either internal or external. Internal steps are those that only can be done while the production is or has to be inactive. External steps are done without interrupting production.
2 Convert internal steps to external ones. The whole idea is to minimize the time needed shutting down operations. This is why we want to take internal steps out as much as possible.
3 Reduce the time needed for the remaining internal steps. There are for sure some steps you can not take out, for those the manufacturing has to be stopped. The whole focus is now on this internal steps and how to reduce them to an absolute minimum. Here the SMED methodology (Single Minute Exchange of a Die) can help. Too find out more you can read here.
4 Eliminate adjustments. Last but not least try to get stable process parameters. With effective process control in place you can get rid off adjustment activities.
A Pareto Diagram can be useful to prioritize the setup time reduction activities. Don’t start everywhere at the same time! Start with the biggest loss and you will see over the time how it will change. It also gives you a great opportunity to see the progress that you are making on set-up time reduction.
Stay Connected
Ad
We want information fast and in a nutshell. We from OI recommend Blinkist* - because it’s simply the best.
* = Affiliate Link