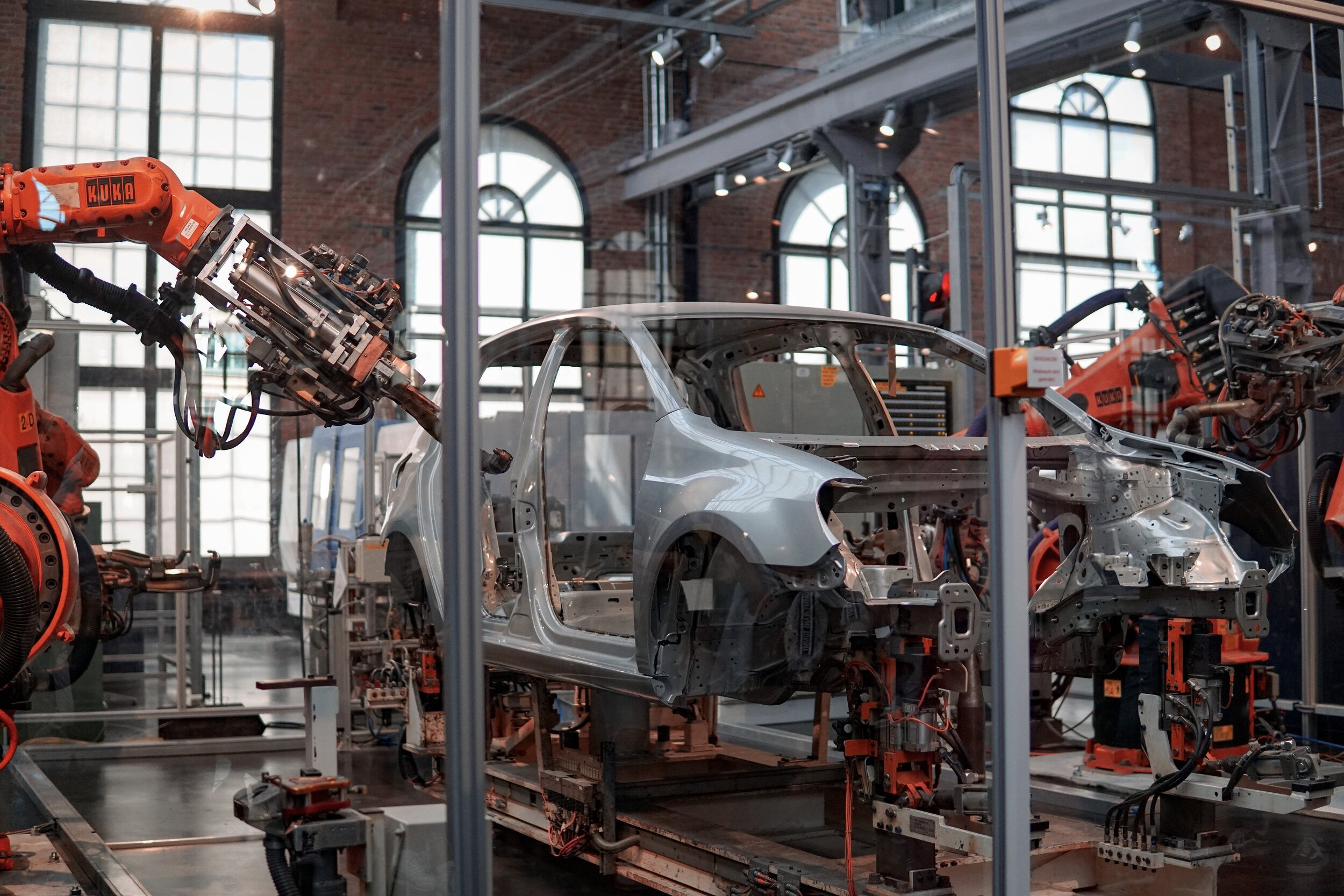
LANGUAGE OF LEAN
Standard Work
Standard work is a fundamental principle of Lean manufacturing, a management philosophy that focuses on the elimination of waste and the continuous improvement of processes in order to increase efficiency, quality, and customer satisfaction.
Standard work is a fundamental principle of Lean manufacturing, a management philosophy that focuses on the elimination of waste and the continuous improvement of processes in order to increase efficiency, quality, and customer satisfaction. From the perspective of a Lean management expert, standard work is an essential tool for achieving operational excellence in the manufacturing industry.
Standard work refers to the detailed documentation of the best way to perform a specific task, taking into account factors such as the skills and experience of the workers, the equipment and materials used, and the desired outcome. This documentation should include step-by-step instructions, visual aids, and clear specifications for each step of the process. The goal of standard work is to ensure that each task is performed consistently and to the highest standard possible, regardless of who is performing it or when it is performed.
There are several key benefits to implementing standard work in manufacturing. Firstly, standard work helps to increase efficiency by eliminating waste and reducing variability in the production process. This leads to shorter lead times, lower costs, and improved quality. Secondly, standard work provides a clear understanding of the expected outcome of each task, making it easier for workers to know what is expected of them and to continuously improve their performance. Thirdly, standard work helps to promote a culture of continuous improvement by empowering workers to identify opportunities for improvement and to suggest changes to the standard work documentation.
To implement standard work effectively, Lean management experts typically follow a five-step process:
Define the task: Clearly define what needs to be accomplished and what the desired outcome is.
Observe and document the current process: Observe the current process, and document each step, including the time taken for each step and any variation in the process.
Determine the standard work: Analyze the data from the observation and determine the best way to perform the task, taking into account the skills and experience of the workers, the equipment and materials used, and the desired outcome.
Train the workers: Train the workers on the standard work and ensure that they understand the expectations and how to perform the task to the standard.
Continuously improve: Regularly review the standard work and identify opportunities for improvement.
In addition to the five-step process, Lean management experts also recommend the following ten tips for a successful implementation of standard work:
Start with a few simple tasks and gradually expand the implementation to other areas of the organization.
Engage the workers in the implementation process and involve them in the development of the standard work.
Focus on standardizing the process, not the workers.
Use visual aids, such as flow charts, to help the workers understand the standard work.
Regularly review and update the standard work to reflect changes in the process, the workers, or the equipment.
Foster a culture of continuous improvement by encouraging workers to suggest changes to the standard work.
Make standard work a part of the performance evaluation process for workers.
Use standard work as a tool for training new workers.
Use standard work to identify opportunities for process improvement.
Regularly communicate the importance of standard work and the benefits of implementing it.
In a nutshell, standard work is a powerful tool for achieving operational excellence in the manufacturing industry. From the perspective of a Lean management expert, standard work helps to increase efficiency, improve quality, and empower workers to continuously improve their performance. By following the five-step process and the ten tips for a successful implementation, organizations can reap the benefits of standard work and achieve their operational excellence goals.
Cell Production
Cell Production focuses on optimizing the flow of work and improving efficiency in manufacturing and operations.
Cell Production focuses on optimizing the flow of work and improving efficiency in manufacturing and operations. It is based on the concept of organizing work into cells, which are self-contained units responsible for performing a specific set of tasks. The goal of cell production is to minimize waste, increase flexibility, and improve overall performance.
The origins of cell production can be traced back to the 1950s and 60s, when Toyota and other Japanese companies were experimenting with new approaches to manufacturing. Over time, the concept of cell production has evolved and been refined, and today it is widely used in a variety of industries, including automotive, electronics, and consumer goods.
In order to implement cell production effectively, there are several key steps that organizations must take. Firstly, it is important to conduct a thorough analysis of the current state of the manufacturing or operations process, in order to identify areas where improvements can be made. This may involve mapping out the flow of work and identifying bottlenecks or other inefficiencies.
Once these areas have been identified, the next step is to reorganize the work into cells, taking into account the specific requirements of each cell and the skills and expertise of the employees who will be working in them. This may involve rearranging physical work spaces, or changing the way that work is assigned and managed.
It is also important to establish clear communication and feedback mechanisms, so that employees and teams can work together effectively. This may involve setting up regular meetings to discuss performance, or implementing systems for tracking and reporting on key metrics.
In order to ensure a successful implementation of cell production, it is also important to provide training and support for employees. This may involve providing training on the new processes and procedures, or offering coaching and mentoring to help employees develop the skills and knowledge they need to be effective.
Another key aspect of cell production is continuous improvement. This involves regularly reviewing performance and making adjustments as needed, in order to optimize efficiency and reduce waste. This may involve experimenting with different approaches, such as implementing new technologies or streamlining processes, in order to find the best solutions.
In conclusion, cell production is a powerful methodology for optimizing performance in operations and manufacturing. By reorganizing work into cells, minimizing waste, and continuously improving performance, organizations can increase efficiency, reduce costs, and improve overall performance. In order to be successful, organizations must take a structured and systematic approach, and be committed to ongoing improvement.
TPM - Total Productive Maintenance
Total Productive Maintenance (TPM) is a maintenance strategy that involves involving all employees in the maintenance process to maximize equipment productivity and minimize downtime.
Total Productive Maintenance (TPM) is a methodology that originated in Japan in the 1970s and has since become a widely recognized and adopted approach to operational excellence in manufacturing and other operations-focused industries. It is a comprehensive approach that seeks to optimize the performance of equipment and processes through a focus on maintaining and improving reliability and efficiency.
The origins of TPM can be traced back to the Japanese auto industry, where manufacturers were seeking ways to increase productivity and competitiveness in the face of increasing global competition. TPM emerged as a response to the need for a more proactive and integrated approach to equipment maintenance, with the goal of improving both productivity and overall equipment effectiveness (OEE).
Over time, TPM has evolved and expanded to encompass a wider range of objectives and activities. Today, it is widely regarded as a best-practice approach to operational excellence, and is widely used in many different industries, including manufacturing, healthcare, and government operations.
One of the key features of TPM is its focus on involving all employees in the maintenance and improvement process. This is achieved through the creation of cross-functional teams and the use of a range of techniques, including root cause analysis, standardization, and continuous improvement.
Another key aspect of TPM is its focus on data-driven decision-making and performance measurement. This involves the collection and analysis of data on equipment and process performance, which is then used to identify areas for improvement and to drive continuous improvement efforts.
When properly implemented, TPM can have a significant impact on organizational performance and competitiveness. This can include improvements in equipment reliability, increased productivity, reduced waste, and improved overall equipment effectiveness (OEE).
To achieve these benefits, it is important to implement TPM in a structured and systematic way, with clear goals and objectives and a strong focus on continuous improvement. This typically involves a multi-phased approach, starting with an assessment of existing processes and equipment, followed by the development of a comprehensive improvement plan and the implementation of specific improvement initiatives.
In a nutshell, TPM is a proven methodology that can help organizations achieve operational excellence by optimizing the performance of their equipment and processes. To achieve success, organizations must approach TPM in a systematic and structured way, with clear goals and objectives, and a strong focus on continuous improvement.
Key points for a successful TPM implementation:
Involve all employees in the process
Focus on data-driven decision-making
Adopt a multi-phased approach
Prioritize continuous improvement
Develop a comprehensive improvement plan.
Bullwhip Effect
The bullwhip effect is a well-known phenomenon in lean management that can have a significant impact on the push and pull principles of supply chain management.
The bullwhip effect is a well-known phenomenon that can have a significant impact on the push and pull principles of supply chain management. The bullwhip effect refers to the amplification of demand fluctuations as they move up the supply chain, leading to increased inventory, increased costs, and decreased customer satisfaction.
The bullwhip effect is caused by a number of factors, including demand forecast errors, order batching, price fluctuations, and the use of incentives that encourage suppliers to order more than they need. These factors can cause suppliers to overreact to demand changes, leading to excessive inventory levels and higher costs.
The impact of the bullwhip effect on the push and pull principles of supply chain management can be significant. The push principle is based on the idea that suppliers produce goods based on demand forecasts, and then push the goods to the customer. The bullwhip effect can cause demand forecasts to become less accurate, leading to increased inventory levels, increased costs, and decreased customer satisfaction.
The pull principle, on the other hand, is based on the idea that suppliers produce goods based on actual customer demand. The bullwhip effect can cause suppliers to overreact to demand changes, leading to increased inventory levels and higher costs. This can result in a situation where suppliers are producing goods that are not actually needed, leading to a decrease in customer satisfaction and increased waste.
To address the bullwhip effect, organizations can implement a number of strategies, including improving demand forecasting accuracy, reducing order batching, reducing price fluctuations, and using incentives that encourage suppliers to order what they need, when they need it.
One approach to reducing the bullwhip effect is to implement a demand-driven supply chain management system. This involves using real-time data to better understand customer demand, and using this information to make informed decisions about inventory levels and production schedules. This can help to reduce the bullwhip effect, leading to more accurate demand forecasts, lower inventory levels, and increased customer satisfaction.
Another strategy to address the bullwhip effect is to implement a lean supply chain management system. This involves reducing waste, streamlining processes, and improving communication and collaboration between suppliers, manufacturers, and customers. This can help to reduce the bullwhip effect, leading to improved supply chain efficiency, lower costs, and increased customer satisfaction.
In a nutshell, the bullwhip effect is a well-known phenomenon in lean management that can have a significant impact on the push and pull principles of supply chain management. To address the bullwhip effect, organizations can implement a number of strategies, including improving demand forecasting accuracy, reducing order batching, reducing price fluctuations, and using incentives that encourage suppliers to order what they need, when they need it. By implementing these strategies, organizations can reduce the bullwhip effect, leading to more accurate demand forecasts, lower inventory levels, and increased customer satisfaction.
Shop Floor Management
Shop Floor Management supports the consistent development of on-site processes and procedures.
Shop Floor Management (SFM) helps the constant improvement of processes and procedures on the shop floor. The presence of mgmt. level staffing in manufacturing and their recognition on deviations from requirements dramatically hastens decision-making and consequences with inside the on the spot implementation of solutions.
Shop Floor Management really defines control duties and calls for unique modes of conduct. Management is supported via way of means of the utility of unique equipment. Five Shop Floor Management-associated duties are performed on the Shop Floor and are as follows:
Install regular communication
Confirm processes
Empower/Qualify staff
Make it part of the continuous improvement process (CIP)
Conduct problem solving in a structured approach
SFM emphasizes behavior that encourages your staff to resolve issues inside their scope of capabilities and strive for continuous improvement.
For example, management maintains its remarks to a minimum, handiest makes binding commitments, offers however additionally accepts feedback, profits its personal attitude of a situation, lets in errors in mastering situations, does now no longer lay blame and places in vicinity wondering techniques. SFM tools help the effectiveness of SFMgmt. e.g.:
Production diary, KPI charts, hassle-fixing sheet, T-cards
Shopfloor Management
What is Shopfloor Management?
Shopfloor Management
Basic components of shop floor mgmt
Clear management roles and responsibilities
Regular communication (Gemba Walks)
Key Performance Indicators
Problem-solving techniques
Visualization
Some explanation of the basics of operational leadership in shop floor mgmt. you organization will for sure profit from clear leadership roles and tasks. Your employees want near help for independent problem solving. Large control gaps, wherein the direct touch among the supervisor and his personnel and associates is reduced, normally do now no longer show themselves.
The Japanese version of a classical institution leader (Hancho), with a totally small management margin and occasional willpower of the personnel, regularly does now no longer suit into the qualified operator in organizations. The excessive qualification of operators is a vital aggressive thing in industry. In order to make suitable use of those capabilities with inside the processes, disciplinary management has the mission of the use of SMART´en to acquire desires at the same time as keeping room for manoeuvre and keeping a very good stability among needs and help.
Managers at the first mgmt. level do now no longer meet those demanding situations via time control seminars, however via greater practical duties and requirement profiles. Examine whether or not it's far important to introduce extra technical management as an alleviation for the first mgmt. level to your organization (CIP coordinator, Kaizen Manager, Process Champion). This feature can stand up from the present functions.
Jointly have a look at the opportunities of dispensing distinctive information regions (5S, set-up time reduction, CIP etc.) with inside the assembly teams expand collectively with you a brand new blending answer specially appropriate for you.
Regular communication
Regular communication is the structured approach to create a framework on a regular basis for opportunities. In this rhythm issues can be carried out and discussed across the management levels. Regular communication is an integral part of the day to day work of all players in your organization.
This way of communication, no matter if you call it huddles, stand up meetings, shop floor meetings, etc. guarantees a continuous flow of information without loss of information itself as it is fast and recurring. A subject matter-associated exchange takes place where employees are enabled to independently define measures, hassle answers and pointers for development and to remedy conflicts as quick as possible.
The continuous flow of information between the departments throughout the complete organization is guaranteed through these regular and short meetings. One positive side effect is that with regular communication you will also calm down daily operations management by clearly separating the topics (e.g. operative commercial enterprise, 5S, CIP, etc.). It is vital that these regular meetings are performed continuously and adhered to in order that normal communique will become independent.
Key Performance Indicators
Regular communication can only exist if the information inside these meetings are defined and standardized. The standard of these meetings is not only the agenda but more important the Key Performance Indicators (KPI). The target of working with KPIs is to have a framework for employees that provides information on the achievement of objectives. When you want to successfully control your production be aware that KPIs are broken down in such a way that they have a direct connection to the operators or designated workstation. Only then they are becoming a real instrument of control by which teams and departments can be measured. The positive thing about KPIs is that with the continuous improvement process paired with a structured problem solving approach all employees will see the effect of implemented measures on the KPIs. To get the full information on KPIs go here.
Problem Solving
Problem solving isn’t always as simple as it sounds, but it clearly shows the effectiveness of clear shop floor management. There are plenty of problem solving methods out there (Ishikawa, 5 Why, A3, Root Cause Analysis, just to name a few) and lean methods (e.g. 5S, set-up time reduction, Hejunka etc.) are well known in the manufacturing industry. But these methods are there to help your organization to deal with more complex issues, this means that they are not really useful for operators that are dealing with daily production but more for a problem solving team consisting of employees from different departments.
To tackle problem solving the right and sustainable way the role of a Kaizen Manager should be installed in your organization in order to steer the problem solving and continuous improvement process. Kaizen Manager help you to get out of this “fire fighting mode” with a sustainable CIP culture.
Visualization
For a clear visualization of running process in your organization, cleanliness and orderliness is the main part of it. Clarity of your processes on the shop floor is the foundation for all lean manufacturing activities. Having the clarity the implementation and maintaining of visual management methods will guide you to a real state of flow.
There are different ways for visualization out there (find a deeper insight here)
The target with visual management and those methods are all the same:
Create transparency
Visual representation of procedures processes and services
Making problems (or bottlenecks) visible
All documents and information are daily updated and right at the place of action clearly visualized for everybody in the organization (e.g. blackboards, Workflow Boards, Shop Floor Boards, Andon Boards, etc.).
Following the PDCA cycle the status of problem solving activities are recorded and visualized. KPIs on different topics are installed and tracked and so on. Important is only that all this information follows also a clear structure and has its own spot on the shop floor (e.g. a shop floor corner). Visualization starts at the workplace of a operator and ends at the management board of the plant manager or owner of the organization.
But in the end it always supports the Continuous Improvement Process in order to bring your organization the next level or simply to overachieve your customers expectations. To get a full insight in Visual Management, read the full article here.
PDCA
The idea behind the PDCA cycle is to empower employees to independently identify and solve problems. It is also a crucial element of the continuous improvement process (CIP).
The idea behind the PDCA cycle is to empower employees to independently identify and solve problems. It is also a crucial element of the continuous improvement process (CIP).
Many projects in which a culture of continuous improvement (CIP) is to be anchored also fail because of the tools required for this. With the A3 Report, for example, there are such tools. Just for clarity upfront, problem solutions, decision bases and strategies are presented on a sheet of paper in DIN A3 format. The A3 Report provides employees with a kind of template for which analysis and action steps must be taken when solving a problem. This process, in turn, is based on a systematic approach: the PDCA cycle.
The four phases of the PDCA cycle
Of all the quality improvement tools, the PDCA cycle is the most important. It describes the basics of an improvement process and divides it into four phases:
Phase 1: Plan
In this phase the problem and the actual state are described, the causes of the problem are analyzed and the target state is defined. In addition, measurements for reaching the target condition is defined.
Phase 2: Do (Implementation)
In the implementation phase, the predefined measures for achieving the target status are fixed.
Phase 3: Check
In the review phase, the experience gained and the results achieved in implementing the measures are reflected and the measures are readjusted if necessary.
Phase 4: Act
In this phase, the experience is gathered and the problem-solving process is evaluated and standards for future action are derived.
PDCA Cylce
Teams always go through this process when they have identified a problem or a relevant opportunity for an improvement. Then a new PDCA cycle is started with the aim of establishing a new standard in the company which serves as a basis for further improvements. The following case study shows how working with the PDCA cycle works.
The PDCA cycle explained using a case study
The management board of an electrical motor manufacturer has adopted a new strategy to further expand the company's quality leadership in electric motor production and increase customer satisfaction. To this end, the management team defined the following so-called breakthrough targets:
The production processes must be state of the art
The work must be based on the zero-defect principle
The striving for continuous improvement (CIP) should be anchored among the employees
These goals have been broken down to all levels. At a meeting, the head of department pointed out to the group leader that the five pressing lines he supervised produce less than the target of 35k motors per day. The consequences: Supply bottlenecks and customer dissatisfaction. The group leader should now solve this problem. In accordance with the PDCA cycle, the following procedure was followed.
This reading pick is from experienced manager and lecturer Ron Basu he lists tools and techniques you can implement to make the best use of Six Sigma and Lean Manufacturing, two major quality-control programs.
Read more here.
PDCA Phase: Plan
The group leader analyzed the production figures of the past weeks. He found that the joining line supervised by the team leader only delivers an average of 32k motors per day instead of 35k. The team leader suspected that this was due to high line rejects. They then took a look at the sorted motors in the quarantine stock. The result: the labelling on almost all rejected motors are displaced or not readable.
The group leader asks the team leader what could be the cause of the problem. His assumption: "The printer is not running perfectly and the application process is not stable. A check of the incoming labels has proven that all material is in specification, so the failure has to be within the printing and application process. The team leader then looked at the scrap figures in the shift reports. It turned out that over 80 percent of the rejected motors are produced during the night shift.
So the group leader and the team leader observed the labelling process in the following night shift. They noticed that the labeling belt occasionally jams in the conveyor belt, which is why the labels are applied offset to the desired location. The team leader suspected that this was due to the fact that the printer mounting and so the printer location was in the wrong position, a further analysis has shown that a new employee has been placed in the night shift and he didn’t understand the correct setting and placement of the printer after exchanging the labeling roll. In addition, it came out that the cartridge has to be replaced after 24 hrs which also was usually coming to the night shift. So the root cause was clear.
The group leader then asked the team leader to formulate a target state for possible countermeasures. He knows through trainings that targets should follow the SMART rule, but on this topic mainly measurable. He wanted to achieve the target by training the new operator. Done deal.
PDCA Phase 2: Do
But the group leader was not satisfied with that. He asked the team leader if he knew exactly how the operator were going to change roles and cartridges if there was a standard operation instruction (SOI) of this process and how to train new operators. The team leader denied this.
In the following night shift, they both watched the change of roles and cartridges by experienced and inexperienced operators. The experienced operators made sure that the labels did not touch the floor during the change and that the printer is in the correct position after replacing the role. The inexperienced, on the other hand, often rubbed the labels on the floor and just pushed the printer in the station without checking the first parts after replacement. Dirt gradually collected in the label dispenser, causing the tape to jam from time to time and the incorrect position of the printer led to misplaced and crushed up labels which in the end of line led to the rejects of the motors.
The group leader asked the team leader and his team to consider possible countermeasures, prioritize them and draw up an action plan. The countermeasures were among others:
5S sessions at the end of each shift to restore cleanliness and order in the line
Installation of training matrix in order to know how is able to follow the process and how is experienced enough to train new operators
Install a Poka Yoke fixture to ensure a process stable positioning of the printer
Install a counter with light indication when the cartridge of the printer needs to be replaced after an evaluated amount of labels printed
Based on the prioritization, the team members drew up an action plan. They also agreed:
The current status of the project is always documented on the cell board of the labelling line for the next three months
The progress figures are reported in the daily shop floor meeting – not the team meeting of the cell. It has mgt. focus.
PDCA Phase 3: Check
In the following weeks, the team leader of the cell reported daily the figures and the impact of the measures on the outcome. They also defined further measures on the basis of their experience to date. For example, the machine is always stopped when the label tape reaches into the light barrier, caused by an air blast. The measure was to install a duct for the carrier tape of the labels into a bin placed under the line, easily accessible for the line clean up at the end of the shift. As a result, the reject rate fell by almost 80 percent after three months. The initially formulated target of 40 percent fewer rejects was achieved.
PDCA Phase 4: Act
After this assessment, the group leader asked the team leader what he wanted to do with regard to standardization. He replied that he would prepare a written description of the optimal process "maintaining the label printer" as well as for training new operators. In addition, from now on he will carry out a daily process control in order to detect target/actual deviations earlier.
The group leader praised the team leader and asked him at the next team leader meeting to inform the team leaders of the four other production lines about the new standard and the findings in the PDCA problem-solving process so that they could learn from the experience. Him himself informed the head of the motor production department that the problem of insufficient motor production had been solved.
MUDA
Read and learn about the 7 kinds of waste.
MUDA – Also see Timwood
In this article we want to talk about MUDA or the 7 kinds of waste known as TIMWOOD.
The seven kinds of waste have to be discovered and eliminated in daily operations. Therefore we will be looking at the 7 kinds of waste and learn how to use appropriate lean tools to reduce these non value-adding activities.
First of all use Gemba Walks to find out more about whats happening on the shop floor. Only through the on-site inspection you can see what is really going on. It is simply not possible to record the types of waste in the conference room at the green table. The CIP Kaizen action on site is always necessary to reduce waste.
When talking about production the ultimate goal is to increase value-creating activities in the complete organization and not to reduce them. Therefore non-value-adding activities are called MUDA - Japanese for wasteful.
Overview of the 7 kinds of waste and the lean approach to avoid these
The individual parts of muda are easily remembered with a simple mnemonic aid called TIMWOOD. TIMWOOD stands for the first letters of the several kinds of waste. Lets have a look at those and some hints what it means:
T = Transport
Material flow
Product-/Value-/Process orientation
Just in Time material supply of workstations
Pull steering of production with the Kanban principle
I = Inventory
Just in Time or Just in Sequence material supply
Pull steering of production with the Kanban principle
Takt time
Linking suppliers
Reduction of batch sizes or production lots
Implementation of One Piece Flow principle
M = Motion
6 S principle
Standardization
Fixed allocated spaces
Shortest ways
W = Waiting
Multi machining
Multi process handling
Material flow in U-shaped manufacturing lines
Implementation of SMED
Installation of Andon Boards
O = Overproduction
Leveling of manufacturing orders
Mixed-Model-Production
One-Piece-Flow
O = Overprocessing/-engineering
Processes are not necessary
Kaizen activities
Quality circle
Idea Management
Reduction of complexity
Reduction of components needed
Reduction of unnecessary process steps
Reduction of hand overs and quality loops
D = Defects
Reduction of scrap rate or rework
Internal customer supplier management
Self-inspection
Poka Yoke principle
Automation
Zero Defects principle
Stop the line authority
5S activities as part of the standard work
Visual Management and visual aids
S = Unutilized Staff
Idea Mgt.
Shop Floor Mgt.
Lean Innovation
Each of the individual elements of the 7 kinds of waste often interact with each other. If you think about your organization as a system, it is necessary to classify not only one characteristics. An approach can only be derived when several classifications of waste have been analyzed.
The 3 MUDA expressions
With the individual process sections and activities and the corresponding 7 kinds of waste, they can be divided into the following activities:
Value Adding Activities
Kanji Muda - Waste in terms of machinery and equipment
Hiragana Muda - Work that needs to be done in order to fulfill the task but not really add value
Katakana Muda - Everything not needed
All this combined is your total workflow
As seen in real life up to 75% of non-optimized processes are non-value-adding activities which means they are pure waste and eat up your resources. Therefore it always makes sense to eliminate each of the 7 kinds of waste in order to increase productivity. To get an idea see the following picture:
Katakana Muda (red - waste that can be eliminated immediately)
Waiting
Searching
Filling
Double work
Stacking of components
Kanji Muda (gray and yellow - waste based on machines and equipment)
Machinery movement without any function
Oversized machines that can produce more than the required parts during the cycle time
Hiragan muda (green - work that is necessary for the provision of services under the current conditions; value-adding process steps)
Return to starting position
Cleaning
Tightening
Manual operation of machines
So how to recognize and eliminate the 7 kinds of waste?
Muda can always only be detected at the place of action. Therefore Gemba Walks are the best way to go on the search. But one thing has to be clear - it does not have to be always big projects to reduce waste. Continuous Improvement is key - recurring CIP or Kaizen activities are very supportive to develop an eye for the 7 kinds of waste. Training makes masters.
Second - it doesn’t has to be expensive. Most actions can be implemented at low cost. E.g. make a spaghetti plot to visualize and recognize obvious unnecessary movements.
Third - always have an eye on the value-adding activities. With a trained eye from GEMBA WALKS you will have improved awareness of waste already in the planing phase of new processes. Use those lessons learned and avoid waste in the beginning.
We don’t want to go into details but there are two other types of losses that can be witnessed in an organization. Mura meaning deviation and muri meaning overload (man, machine, material equally). If you want to read more about these, have a look here.
Let us come to an end - even when it is hard, we could keep going on and on…
But some rules:
No excuses!
Be creative in first place - money always comes second
Never try to explain why something doesn't work, try how it works!
Adjustments kills your time and ambitions. Adjustment means to fight the symptoms not the root cause!
Do not worry about problems that do not yet exist.
Happy Improving!
Stay Connected
Ad
We want information fast and in a nutshell. We from OI recommend Blinkist* - because it’s simply the best.
* = Affiliate Link