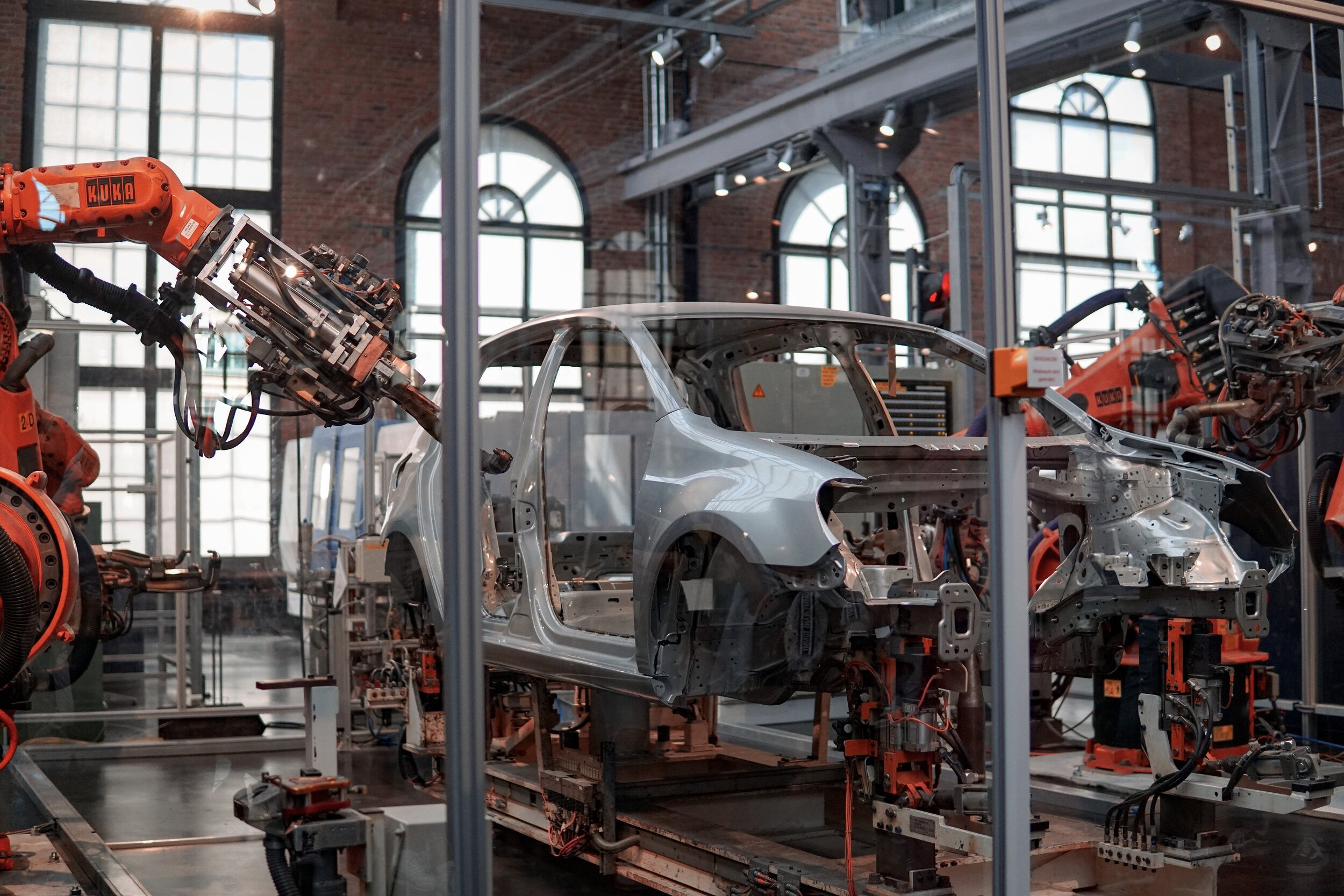
LANGUAGE OF LEAN
Standard Work
Standard work is a fundamental principle of Lean manufacturing, a management philosophy that focuses on the elimination of waste and the continuous improvement of processes in order to increase efficiency, quality, and customer satisfaction.
Standard work is a fundamental principle of Lean manufacturing, a management philosophy that focuses on the elimination of waste and the continuous improvement of processes in order to increase efficiency, quality, and customer satisfaction. From the perspective of a Lean management expert, standard work is an essential tool for achieving operational excellence in the manufacturing industry.
Standard work refers to the detailed documentation of the best way to perform a specific task, taking into account factors such as the skills and experience of the workers, the equipment and materials used, and the desired outcome. This documentation should include step-by-step instructions, visual aids, and clear specifications for each step of the process. The goal of standard work is to ensure that each task is performed consistently and to the highest standard possible, regardless of who is performing it or when it is performed.
There are several key benefits to implementing standard work in manufacturing. Firstly, standard work helps to increase efficiency by eliminating waste and reducing variability in the production process. This leads to shorter lead times, lower costs, and improved quality. Secondly, standard work provides a clear understanding of the expected outcome of each task, making it easier for workers to know what is expected of them and to continuously improve their performance. Thirdly, standard work helps to promote a culture of continuous improvement by empowering workers to identify opportunities for improvement and to suggest changes to the standard work documentation.
To implement standard work effectively, Lean management experts typically follow a five-step process:
Define the task: Clearly define what needs to be accomplished and what the desired outcome is.
Observe and document the current process: Observe the current process, and document each step, including the time taken for each step and any variation in the process.
Determine the standard work: Analyze the data from the observation and determine the best way to perform the task, taking into account the skills and experience of the workers, the equipment and materials used, and the desired outcome.
Train the workers: Train the workers on the standard work and ensure that they understand the expectations and how to perform the task to the standard.
Continuously improve: Regularly review the standard work and identify opportunities for improvement.
In addition to the five-step process, Lean management experts also recommend the following ten tips for a successful implementation of standard work:
Start with a few simple tasks and gradually expand the implementation to other areas of the organization.
Engage the workers in the implementation process and involve them in the development of the standard work.
Focus on standardizing the process, not the workers.
Use visual aids, such as flow charts, to help the workers understand the standard work.
Regularly review and update the standard work to reflect changes in the process, the workers, or the equipment.
Foster a culture of continuous improvement by encouraging workers to suggest changes to the standard work.
Make standard work a part of the performance evaluation process for workers.
Use standard work as a tool for training new workers.
Use standard work to identify opportunities for process improvement.
Regularly communicate the importance of standard work and the benefits of implementing it.
In a nutshell, standard work is a powerful tool for achieving operational excellence in the manufacturing industry. From the perspective of a Lean management expert, standard work helps to increase efficiency, improve quality, and empower workers to continuously improve their performance. By following the five-step process and the ten tips for a successful implementation, organizations can reap the benefits of standard work and achieve their operational excellence goals.
Standard Work Combination Sheet
In lean management, a standard work combination sheet is a document that displays the process steps for one or several employees. It is used to show the optimal combination of human and machine work.
In lean management, a standard work combination sheet is a document that displays the process steps for one or several employees. It is used to show the optimal combination of human and machine work. The sheet includes information on the timing values between different steps of the process, including manual work time, walk time, and machine processing time. The data recorded on the sheet is analyzed to identify any significant waste or delays in the process, and can be used to help determine the direction the company needs to take to address these issues. The sheet can also be used to evaluate the performance of individual employees, such as identifying if someone is overburdened with tasks or underutilized. Let’s go in a little bit detail in the following.
Standardized Work Combination Sheet
A Standardized Work Combination Sheet is a document that provides an overview of the interactions and timing between different parts of the work process. It displays how the various timing values such as manual work time, walk time, and machine processing time, combine and interact with each other. The sheet is designed to capture key data that is relevant to the understanding of the workflow and timing of the process.
What you should record
The data for each individual operator working on the floor is recorded in the Combination Sheet, and then analyzed using various forms of analysis. This sheet is useful for identifying any significant waste in delays between separate process steps, and can provide a clear indication of the direction the company needs to take to address these issues.
The most important points recorded in the sheet are the time required for human and machine movement, all based on the Takt Time. The sheet can help the company quantitatively evaluate an individual worker's performance and identify if they are overburdened by their current tasks.
Additionally, it can also reveal if a particular employee could be utilized more effectively. Often, companies may not realize that one of their workers is underutilized, spending less time performing actual work than expected. By properly recording and analyzing data using relevant tools to standardize the working environment, all the information will be easily accessible.
Eliminate waste
The Combination Sheet can help identify and eliminate waste in the production process by observing data recorded on the sheet, such as the time operators spend waiting for machines to complete tasks, waiting for input from other machines, or waiting for other operators to perform their tasks.
While some waiting may be necessary and an inherent part of the work process, it can be challenging to distinguish between necessary and unnecessary downtime. The Combination Sheet provides a comprehensive understanding of the current state of the production process and an objective view of each individual's involvement.
The data collected from the sheet is well-suited for graphical representation and can be easily analyzed using visualization tools. It may be incorporated into the sheet itself or handled by another department. The most crucial aspect is that the data is collected and organized correctly, as it can always be processed later.
How accurate should it be
The level of precision required for timing measurements can vary depending on the nature of your organizations processes. In some cases, it may not be necessary to record times down to the last second, such as when processes typically take over ten minutes. On the other hand, if the organization relies on many small and fast-paced processes, it may be necessary to use external devices to measure time as it would be difficult for a human operator to keep up.
It is essential to ensure that all data is measured consistently, as this is what establishes the validity of the data for later analysis. It is not advisable to round off one part of the data set while keeping another precise as it can lead to statistical deviations that are challenging to explain.
So what does it mean?
Employees may initially be uncertain about their new responsibilities related to completing the Combination Sheet, but taking the time to provide guidance and training can lead to significant improvements in the overall efficiency of the organization. Standard work can bring about significant changes in a company, but it is important to be patient and provide clear instructions during the initial implementation process. It can be a challenging transition, which is why it is essential to be well-versed in all the tools and techniques involved.
Andon
Andon is a crucial part of visual management on the shop floor that gives a signal that indicates if and where there is a problem.
Andon is a crucial part for the visual management on the shop floor that gives a signal that indicates if and where there is a problem. Typically indicated with a traffic light signal red = failure mode, yellow = non-conforming performance and green = normal operation mode.
The methodology of Andon as part of the shop floor management, is to show the current operating status of a machine or a production line in a way that everyone can see and understand it immediately. As typically in Lean Terms Andon comes from the Japanese language and means paper lamp or just lamp.
Going along the Andon-Systematic there is to mention the Andon-Cords. The cords are used by operators to activate the lamps by either tear the cord or more likely nowadays pressing the corresponding buttons, which are attached above the production line and are easily accessible for the operators hanging downwards or as button attached at the work station.
If a non-conforming condition occurs, the yellow Andon signal initiates the support so that the problem that has occurred can be remedied immediately with additional supportive functions, such as maintenance. In worst case it is also possible to stop the complete production (red signal) until the problem has been solved or at least suitable countermeasures are in place.
An Andon has three main functions:
Visualization of the operating status of a machine/assembly line
Possibility for the operator to report an non-conforming condition and escalate it using a defined escalation process
Production or belt stop, so that no non-conforming products or components are passed on to the next process step
Old fashion Andon Board
The clear display of the operating states of several workstations was used quite early in the development of the Andon systems. The godfather of the TPS, Taiichi Ohno once described it as followed: "When one looks up, the andon (the line stop indication board) comes into view, showing the location and nature of trouble situations at a glance."
In the course of time, the Andon board has increasingly developed into an information board for all employees involved in the process. They display status information regarding the current situation in production, such as the number of units produced per day or per hour, the degree of delivery reliability to the customer or the cumulated amount of backlog. In this way, all process participants are aware of the current situation and can act accordingly.
Andon Boards nowadays
KATA
The term Kata is borrowed from Japanese martial arts and describes a series of movements following the flow of a fight.
The term Kata is borrowed from Japanese martial arts and describes a series of movements (routines) following the flow of a fight. It can be seen as choreography without an enemy. Translated in operations we are talking about implementing routines to achieve continuous improvements. In the lean world the term KATA is well promoted by Mike Rother - therefore customer satisfaction and personal development is improved using improvement and mentoring routines.
The improvement routine consists of four steps
Determine a clear target state > vision statement
Determine the current state
Define the next target condition
Get into action following the PDCA methodology
The goal is to start building a habit of continuous improvement by the application of the principles of Kata. Following Mike Rother - The Kata Story Board demonstrates the basics of the Toyota Kata methodology. This means nothing less than taking step by step towards continuous improvements in your organization towards the targeted state.
Using the Kata methodology gives you the advantage of defining a clear structure and clarity to the improvement process itself. The guideline is clear and easy to adapt:
Remove emotions and options
Create small, fast and effective PDCA cycles
Stop the trial and error > deploy a clear approach with small steps
Build habits that sustainably support your long-term goals
Following the Story Board
With the help of the Kata methodology you will start to build up new habits through continuous training and practicing your routines. With new habits you will reach new skills that might change your own mindest on how to look at things when focusing on continuous improvements. Therefore Kata is a universal methodology that can be utilized in any field, it will not only help you in your professional life but can also be adapted in your private life.
See one example of a KATA Story board below. You can also download a free example here.
An effective way to introduce a lasting change is to establish the routine of continuous improvement habits that strive for excellence. For your organization that should mean to work with a KATA Coach who supports you by installing regular meetings (stand ups/huddles or however you want to call it) and go through the five questions of Coaching Kata and repetitively goes through the four steps of Improvement Kata.
Therefore the five questions of Coaching Kata are:
What is your targeted condition?
What is the actual condition?
What road blockers are in your way that prevent you or your organization from reaching your target condition?
What will you do/try next to come closer to your target condition?
What have you learned from previous steps?
Coaching Kata strives for a long lasting change and you can start small instead of creating a huge mountain to climb in first place. Coaching Kata is empowering everybody involved in your organization, from the shop floor up to the C-level. Kata enables people to participate and contribute to the organizations success through their own actions. In addition Kata will support you on your continuous improvement process and methodologies.
The Kata methodology can be seen as a toolkit helping you to gain a better understanding of how Kata can support you on:
Developing a standardized method on how to improve solution oriented processes
Training managers to see themselves as mentors, coaches and role models
Implementing a problem solving routine that supports on daily basis the continuous improvement process
Developing a framework for a living PDCA cycle that underlines the value of small steps to the all over defined target state
No matter what phase your in - whether you are a one person startup or multi-billion organization Kata provides a methodology that can be used to solve problems and brings you faster to the stage you want to be. The systematic approach can be implemented at all levels of CIP and all fields of industry.
Stay Connected
Ad
We want information fast and in a nutshell. We from OI recommend Blinkist* - because it’s simply the best.
* = Affiliate Link