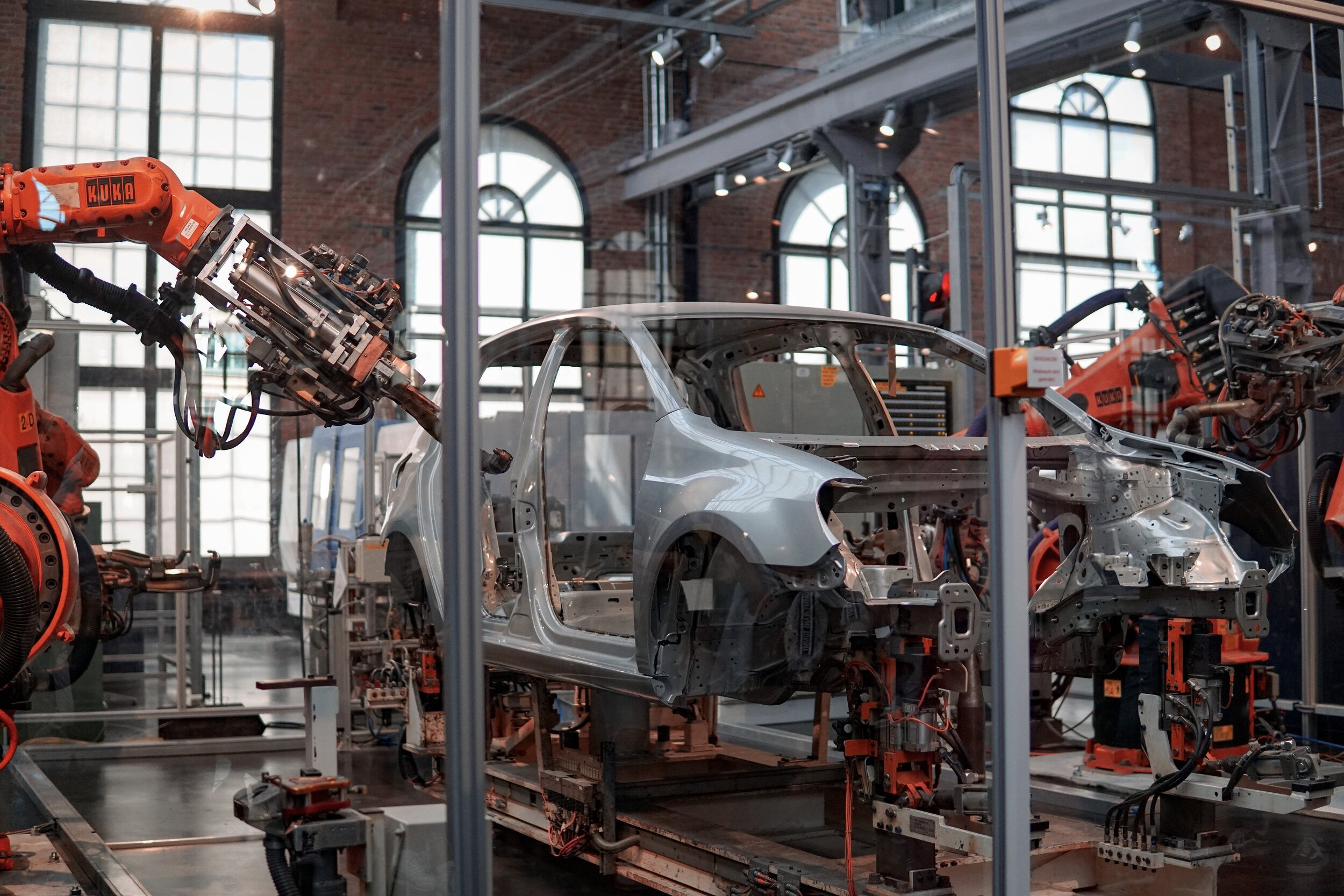
LANGUAGE OF LEAN
Process Chain
The manufacturing industry is a complex system of processes, with each stage relying on the success of the previous one to achieve the final product.
The manufacturing industry is a complex system of processes, with each stage relying on the success of the previous one to achieve the final product. The process chain is the backbone of this system, connecting each stage together to ensure a seamless flow of goods and services.
To achieve the highest level of efficiency in the production process, it is important to understand the process chain and how it serves the production processes. This includes identifying the inputs, outputs, and key activities of each stage, as well as the flow of goods, services, and information throughout the chain.
One of the first steps in optimizing the process chain is to establish clear and standardized procedures for each stage. This includes defining the roles and responsibilities of each team member, as well as establishing a clear communication plan to ensure that everyone is aware of the status of each stage.
Another important factor in optimizing the process chain is to reduce waste and increase efficiency. This can be achieved through continuous improvement efforts, such as streamlining processes, reducing inventory, and minimizing lead times. Lean tools, such as value stream mapping, can be used to identify areas of waste and opportunities for improvement.
Additionally, investing in new technology and equipment can also help to improve the process chain. Automation and digitalization of the production process can lead to faster and more accurate production, as well as reduced labor costs and increased productivity.
Furthermore, involving employees in the continuous improvement process is crucial in achieving the best results. Encouraging their input and ideas can lead to new solutions and creative thinking that can drive process improvement. Employee training and development programs can also help to enhance the skills and knowledge of the workforce, leading to increased efficiency and effectiveness.
Another important aspect of the process chain is supplier selection and management. Careful selection of suppliers can ensure that high-quality inputs are used in the production process, reducing the likelihood of defects and increasing efficiency. Effective supplier management can also ensure timely delivery of goods and services, reducing lead times and minimizing the impact of supply chain disruptions.
In a nutshell, the process chain is a critical component of the manufacturing industry, serving as the foundation for the production processes. By establishing clear procedures, reducing waste and increasing efficiency, investing in new technology, involving employees, and carefully selecting and managing suppliers, manufacturers can optimize the process chain and achieve operational excellence
JIT
Just-in-Time (JIT) is a manufacturing and inventory control system in which raw materials, components, and finished products are delivered to the production line exactly when they are needed.
Just-in-Time (JIT) is a manufacturing and inventory control system in which raw materials, components, and finished products are delivered to the production line exactly when they are needed. The goal of JIT is to minimize inventory levels and reduce lead times, while maintaining high levels of production efficiency.
JIT is a pull-based system, which means that production is driven by customer demand rather than by a production schedule. This is achieved by using Kanban, a signaling system that alerts the supplier to send more materials or components when the inventory level of a specific item reaches a predetermined minimum level.
The origins of JIT can be traced back to the manufacturing practices of the Toyota Motor Company in the 1950s. It was developed by Taiichi Ohno, an engineer at Toyota, as a response to the inefficiencies he observed in the company's production processes. Ohno recognized that by reducing the amount of inventory and increasing the flow of materials, Toyota could improve its production efficiency and responsiveness to customer demand.
One of the key principles of JIT is the elimination of waste, or "muda" in Japanese. Ohno identified seven types of waste in manufacturing: overproduction, waiting, unnecessary motion, overprocessing, defects, excess inventory, and unused human potential. JIT aims to eliminate these forms of waste by creating a smooth and efficient flow of materials and products through the production process.
JIT also relies on the concept of "one piece flow", which is the production of one item at a time, rather than producing large batches of items. This allows for better control of the production process, as well as the ability to quickly identify and correct any problems that may arise.
Another important aspect of JIT is the use of visual management tools, such as Andon boards and Kanban boards. These tools allow for real-time monitoring of the production process, and can alert workers to potential problems before they become major issues.
JIT also requires a high level of collaboration and communication between suppliers, manufacturers, and customers. This is necessary to ensure that materials and components are delivered to the production line exactly when they are needed, and that finished products are delivered to customers in a timely manner.
JIT has a number of benefits for manufacturers. One of the most significant is that it can help to reduce inventory levels, which can free up valuable floor space, reduce storage costs, and minimize the risk of stockouts. JIT can also help to improve production efficiency by reducing lead times and minimizing downtime caused by waiting for materials or components.
JIT can also help to improve product quality by reducing defects, and increasing the ability to quickly identify and correct any problems that may arise in the production process.
JIT also helps companies to be more responsive to customer demand by reducing lead times and increasing the speed of delivery. This can help to improve customer satisfaction, and increase the chances of repeat business.
JIT also helps companies to be more flexible and adaptable to changes in customer demand. It allows companies to more easily shift production to different products or product lines, which can help to maintain profitability during periods of slow sales.
However, it's worth noting that JIT is not suitable for all industries and companies, it's best applied in companies where the production process is well-defined, the demand is stable and predictable, and the lead times are short. Implementing JIT can also be challenging and requires a significant investment of time and resources to establish an effective system.
Additionally, JIT requires a high level of coordination and communication with suppliers and customers, which can be difficult to achieve. This is particularly true for companies that have a large number of suppliers or customers, or those that operate in
Stay Connected
Ad
We want information fast and in a nutshell. We from OI recommend Blinkist* - because it’s simply the best.
* = Affiliate Link