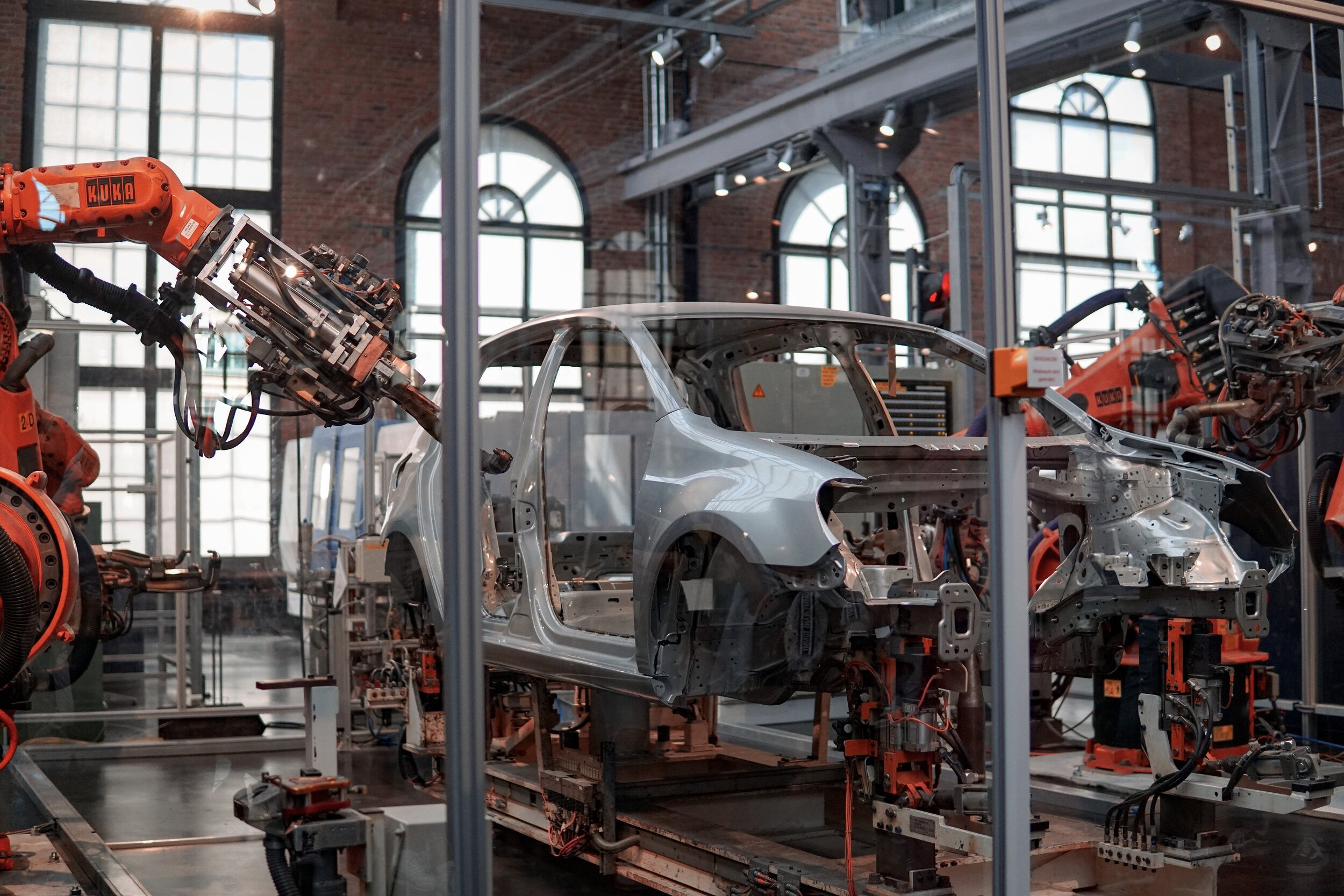
LANGUAGE OF LEAN
Mixed Model Production
We believe that MMP has the potential to bring significant benefits to a production line by increasing efficiency, reducing waste, and improving customer satisfaction.
Mixed Model Production (MMP) is a flexible production strategy that is gaining popularity in the manufacturing industry. We believe that MMP has the potential to bring significant benefits to a production line by increasing efficiency, reducing waste, and improving customer satisfaction.
Mixed Model Production is characterized by the simultaneous production of different models and variations of a product on the same production line. This approach is in contrast to the traditional practice of having a dedicated production line for each product type. In MMP, production is optimized by using a mix of products, models, and variations that can be produced on the same equipment, thereby reducing the need for changeovers, equipment downtime, and material waste.
One of the key benefits of MMP is increased production efficiency. By producing multiple products on the same production line, changeovers and downtime are minimized, reducing the time it takes to produce each product. This increased efficiency results in improved productivity, lower production costs, and higher customer satisfaction.
Another advantage of MMP is reduced waste. The production of multiple products on the same line results in a better utilization of resources and raw materials. This, in turn, reduces the amount of waste generated and the costs associated with waste disposal. Additionally, the reduced downtime results in less energy consumption and a more sustainable production process.
In MMP, the key to success is the ability to schedule production effectively. This requires a deep understanding of the production process, the equipment, and the capabilities of the workforce. A well-designed MMP strategy should be based on a detailed analysis of the production line and a comprehensive understanding of the production process.
The first step in implementing MMP is to identify the different products, models, and variations that can be produced on the same production line. This requires a thorough analysis of the production process and the equipment used. Once the different products have been identified, the next step is to determine the most efficient scheduling of production. This requires a detailed understanding of the production process and the equipment used, as well as the capabilities of the workforce.
The implementation of MMP requires a cross-functional approach that involves teams from different areas of the organization, including production, engineering, and logistics. The success of MMP depends on the collaboration and cooperation of these teams, as well as the effective communication of the MMP strategy to all stakeholders.
In a nutshell, Mixed Model Production is a flexible production strategy that has the potential to bring significant benefits to the manufacturing industry. As a Lean Management and Operational Excellence expert, I believe that MMP has the potential to increase production efficiency, reduce waste, and improve customer satisfaction. However, the success of MMP depends on a detailed understanding of the production process, the equipment, and the workforce, as well as a cross-functional approach that involves teams from different areas of the organization.
Point Of Use
Point of Use (POU) is a key component of Lean initiatives aimed at reducing waste, increasing efficiency, and improving overall production processes.
Point of Use (POU) is a key component of Lean initiatives aimed at reducing waste, increasing efficiency, and improving overall production processes. It is a philosophy that focuses on delivering materials, tools, and equipment directly to the worker at the moment they need them. The goal of POU is to minimize unnecessary movement, handling, and storage of materials, which not only streamlines production but also reduces the risk of damage, loss, and obsolescence.
In traditional manufacturing processes, raw materials and supplies are often stored in central locations, such as inventory rooms, and are retrieved and moved to the production line as needed. This can result in excess inventory, increased lead times, and the need for multiple trips to retrieve materials. Additionally, workers may spend significant amounts of time searching for the tools or materials they need, which reduces productivity and increases the risk of mistakes.
Point of Use aims to eliminate these inefficiencies by bringing materials and supplies directly to the worker at the point of need. This reduces the need for workers to search for materials and increases the speed and accuracy of the production process. POU also reduces the amount of inventory that needs to be stored and managed, which helps to reduce the risk of damage, loss, and obsolescence.
There are several different approaches to implementing POU, each with its own set of benefits and challenges. One approach is to use kanban systems, which are visual signals that tell workers when it’s time to replenish materials or supplies. Another approach is to use automated systems, such as conveyors or robots, which move materials and supplies directly to the production line as needed.
Regardless of the approach used, POU requires careful planning and coordination between all departments involved in the production process. It also requires regular monitoring and adjustments to ensure that the system is working as intended. This can include tracking key performance indicators (KPIs) such as inventory levels, production lead times, and worker productivity.
One of the benefits of POU is that it helps to improve worker morale and job satisfaction. When workers have access to the materials and supplies they need exactly when they need them, they are able to focus on their work without worrying about finding the right tools or supplies. Additionally, POU helps to eliminate the frustration that workers may feel when they are unable to find the materials they need, which can lead to decreased job satisfaction and even burnout.
Another benefit of POU is that it helps to reduce the risk of mistakes and increase quality. When workers have everything they need at their fingertips, they are able to focus on their work without worrying about searching for materials or supplies. This reduces the risk of errors, which in turn helps to improve overall quality and reduce the need for rework.
In a nutshell, Point of Use is an important concept in Lean Manufacturing that aims to reduce waste, increase efficiency, and improve overall production processes. By bringing materials and supplies directly to the worker at the point of need, POU streamlines production, reduces the risk of damage, loss, and obsolescence, and improves worker morale and job satisfaction. To be successful, POU requires careful planning, coordination, and monitoring, as well as a focus on continuous improvement. By implementing POU and other Lean principles, manufacturers can reduce costs, increase efficiency, and improve overall production outcomes.
Production Smoothing (Heijunka)
Production smoothing, also known as Heijunka, is a key aspect of modern operations management. It refers to the leveling of production to match customer demand, while maximizing efficiency and minimizing waste.
Production smoothing, also known as Heijunka, is a key aspect of modern operations management. It refers to the leveling of production to match customer demand, while maximizing efficiency and minimizing waste. This technique has been proven to be an effective way to manage production processes and increase competitiveness in the marketplace.
The objective of production smoothing is to create a steady flow of products and services, reducing the variability and fluctuations in the production process. This helps to minimize the waste and resources associated with overproduction, excess inventory, and bottlenecks in the production line. By leveling production, companies can better predict customer demand and adjust their production processes accordingly.
One of the primary benefits of production smoothing is the reduction of waste in the production process. By leveling production, it minimizes the need for excess inventory and eliminates the waste associated with overproduction. This helps to minimize the costs associated with storage, handling, and transportation of excess inventory, while improving overall efficiency.
Another advantage of production smoothing is the improvement of customer satisfaction. By better predicting and matching customer demand, companies can ensure that they have the right products and services available at the right time. This helps to build stronger relationships with customers and improves the overall perception of the company.
To implement production smoothing, companies must first understand their customer demand patterns and the production processes that support them. This requires a thorough analysis of the production line, including the identification of bottlenecks and areas of waste. The company should then develop a production plan that balances customer demand with the production processes to create a steady flow of goods and services.
The company should also implement effective communication and collaboration between all departments, including sales, marketing, engineering, and production. This helps to ensure that all processes are aligned and working together towards the common goal of production smoothing. The company should also consider the use of technology and equipment to automate the production process and improve efficiency.
It is also important to engage employees in the production smoothing process. By involving employees in the implementation and ongoing management of production smoothing, companies can tap into their expertise and insights, and build a culture of continuous improvement. Employees should also receive training and development opportunities to enhance their skills and knowledge in production smoothing techniques.
In a nutshell, production smoothing is an effective way to manage production processes and increase competitiveness in the marketplace. By reducing waste, improving customer satisfaction, and engaging employees, companies can create a steady flow of goods and services, and improve their overall production efficiency. By embracing this technique, companies can achieve operational excellence and maintain their competitive edge in the marketplace.
Cellularization
Cellularization is a lean manufacturing methodology that aims to optimize the flow of materials, information, and people within a manufacturing or production environment.
Cellularization is a lean manufacturing methodology that aims to optimize the flow of materials, information, and people within a manufacturing or production environment. Its goal is to create a more efficient, flexible, and responsive production system that can quickly adapt to changing customer demands and market conditions.
The origin of cellularization can be traced back to the early days of the Toyota Production System (TPS), which was developed in the 1950s and 60s. TPS was based on the principles of Just-In-Time (JIT) production and was designed to reduce waste, improve quality, and increase productivity. The concept of cellularization emerged as a way to create small, self-contained production cells that were optimized for specific product families or types of work.
The core idea behind cellularization is to create a flow of work that is highly synchronized and integrated, with minimal inventory and waste. This is achieved by organizing the production environment into cells that are designed to handle specific product families or product types. Each cell is equipped with the necessary tools, equipment, and materials to complete the work in a continuous flow, without the need for batch processing or work-in-progress storage.
Cellularization also requires a cross-functional team approach, where workers from different areas of the organization come together to work on a specific product family or type of work. This team-based approach helps to ensure that everyone has a clear understanding of the work, and it encourages collaboration and communication between different departments.
One of the key benefits of cellularization is that it enables organizations to respond quickly to changes in customer demand and market conditions. For example, if a new product is introduced, the production cell for that product can be quickly reconfigured to accommodate the new work. This agility is a critical advantage in today's fast-paced and highly competitive market.
Another benefit of cellularization is that it promotes continuous improvement. The small, self-contained nature of the cells allows for close observation and monitoring of the work, which in turn enables quick and effective identification and elimination of waste. The cross-functional teams are also empowered to identify and implement improvements that can be made to the production process.
To effectively implement cellularization, organizations need to carefully consider the following factors:
Work flow design: The first step in implementing cellularization is to carefully design the work flow to ensure that it is optimized for the specific product family or type of work being performed.
Equipment selection: The right tools and equipment are critical to the success of cellularization. Organizations need to carefully select the tools and equipment that will be used in each cell, and ensure that they are properly maintained and calibrated.
Cross-functional teams: Teams of workers from different departments must be assembled to work together in each cell. These teams need to be trained on the new work processes, and encouraged to collaborate and communicate effectively.
Lean leadership: Leaders at all levels of the organization need to embrace the principles of lean manufacturing and support the implementation of cellularization. This includes providing the resources, training, and coaching that teams need to succeed.
In a nutshell, cellularization is a powerful and effective methodology for optimizing the flow of materials, information, and people within a manufacturing or production environment. Its success depends on careful design of the work flow, selection of the right tools and equipment, and the development of cross-functional teams. With the right leadership and support, cellularization can help organizations to achieve greater efficiency, flexibility, and responsiveness, and to remain competitive in today's fast-paced and dynamic market
Stay Connected
Ad
We want information fast and in a nutshell. We from OI recommend Blinkist* - because it’s simply the best.
* = Affiliate Link