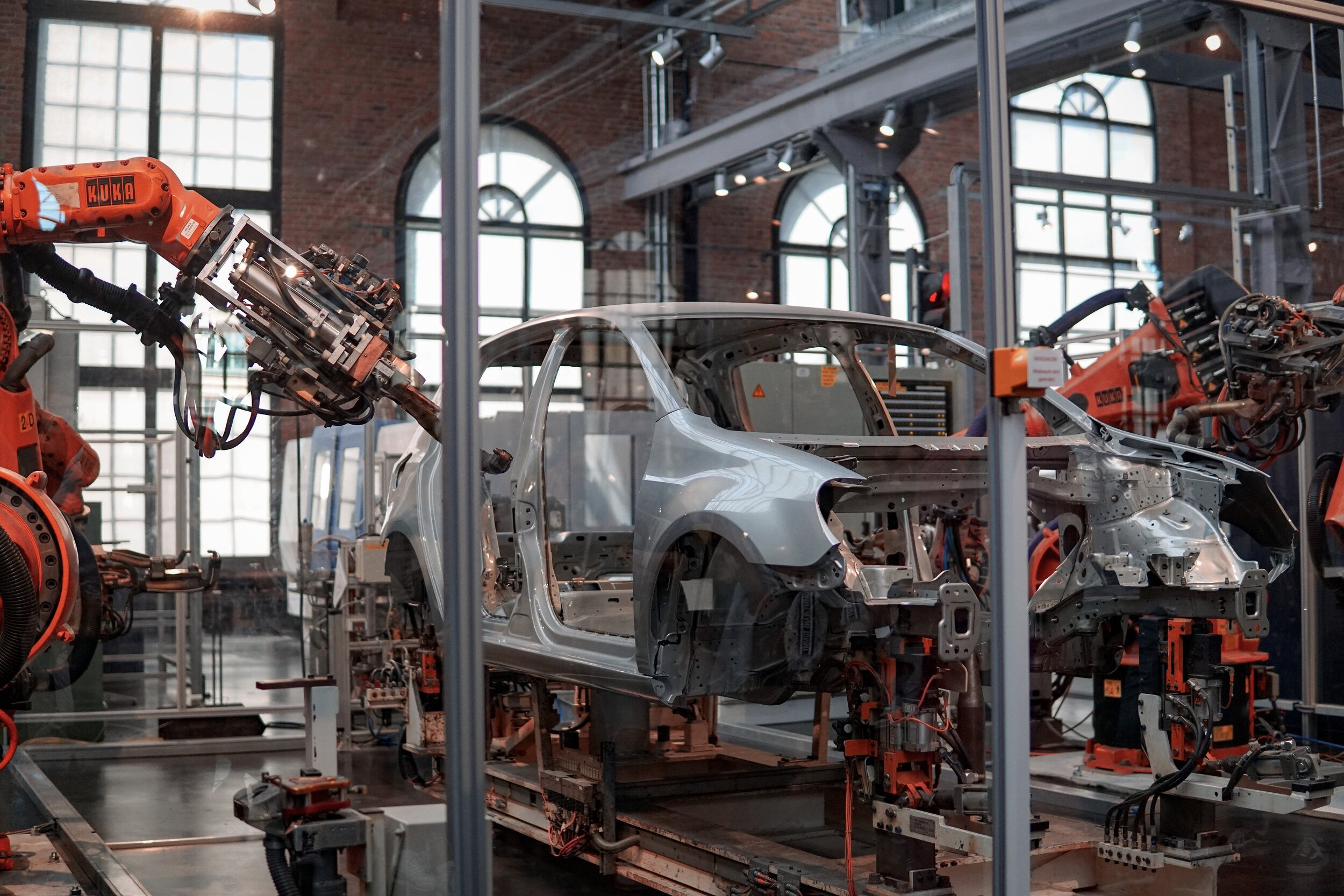
LANGUAGE OF LEAN
FLOW
Flow is one of the key principles of Lean, and it refers to the smooth, uninterrupted progression of work from one step to the next.
Flow is an essential aspect of Lean Management and is closely tied to the value stream of an organization. Lean is a management philosophy that emphasizes the elimination of waste and the creation of value in all areas of a business, from the production floor to the office. Flow is one of the key principles of Lean, and it refers to the smooth, uninterrupted progression of work from one step to the next.
The value stream is the series of activities that a company performs to deliver its products or services to customers. It includes everything from the design and development of a product to the delivery of that product to the customer. The goal of Lean is to optimize the value stream, eliminating waste and ensuring that the flow of work is as efficient as possible.
To achieve flow, Lean experts focus on creating a smooth and continuous flow of work, from the initial stages of design and development to the final stages of delivery and customer service. This requires a deep understanding of the value stream and the identification of any bottlenecks, or areas where work is slowing down or coming to a stop. By removing bottlenecks, Lean experts can increase the speed of work and improve overall efficiency.
One of the key tools used in Lean for optimizing flow is Value Stream Mapping (VSM). VSM is a visual representation of the value stream, showing the flow of work from start to finish, including all the steps involved and the time required for each step. With VSM, Lean experts can identify areas of waste and inefficiency, such as excessive inventory, overprocessing, and wait times.
Another important tool for optimizing flow is Just-In-Time (JIT) manufacturing. JIT is a Lean method that emphasizes the need for production to occur only when it is needed, and no earlier. This helps to eliminate inventory waste and reduces the amount of time spent waiting for parts or materials. JIT also helps to minimize the risks associated with inventory, such as obsolescence, damage, and theft.
Another aspect of flow in Lean is the concept of "pull" production. This means that production should be driven by the demand from customers, rather than by forecasting and forecasting-based production schedules. Pull production helps to ensure that work is only done when it is needed, eliminating the waste associated with overproduction and reducing the risk of obsolescence.
Finally, it's important to understand that flow is not just about efficiency and productivity. It is also about creating a culture of continuous improvement and empowering employees to identify and eliminate waste in their own work. This can be achieved through the use of tools such as Kaizen, a Lean method that encourages employees to identify and suggest improvements to the value stream.
In a nutshell, flow is a critical aspect of Lean Management and is closely tied to the value stream of an organization. By focusing on creating a smooth and continuous flow of work, Lean experts can optimize the value stream, eliminate waste, and improve overall efficiency. Whether through the use of tools such as VSM and JIT, or through a focus on continuous improvement and employee empowerment, flow is a key part of the Lean philosophy and is essential for success in the modern business environment.
One Point Lesson
One Point Lesson (OPL) is a method used in the manufacturing industry that can greatly improve operational efficiency and overall quality.
One Point Lesson (OPL) is a method used in the manufacturing industry that can greatly improve operational efficiency and overall quality. This method is often used within the context of Lean Management, which is a strategy that focuses on maximizing value while minimizing waste. As a Lean Management Expert, I will be discussing how OPL can be used to improve operations in the manufacturing industry.
OPL is a simple but effective tool that helps to standardize and spread best practices across an organization. It is a one-page document that summarizes a lesson learned from a problem or improvement opportunity. This document is designed to be easy to understand and share, so that others can learn from the lesson and apply it in their own work. The purpose of OPL is to promote continuous improvement by capturing and sharing knowledge that can be used to prevent similar problems from happening again in the future.
One of the key benefits of using OPL is that it allows for quick and easy dissemination of knowledge and best practices. The one-page format makes it easy for employees to understand and remember the information, and the lessons learned can be quickly spread throughout the organization. This can lead to significant improvements in the quality of products and services, as well as increased efficiency in operations.
OPL can also help organizations to identify and eliminate non-value-adding activities. This is because the lessons learned can be used to identify areas where improvements can be made, and then the appropriate changes can be implemented. For example, if a problem occurs during the production process, an OPL can be created to document the cause of the problem and how it was resolved. This information can then be used to make changes that will prevent the problem from happening again in the future.
In addition to improving quality and efficiency, OPL can also help organizations to foster a culture of continuous improvement. By capturing and sharing knowledge, employees are encouraged to look for ways to improve processes and to find solutions to problems. This leads to a more engaged workforce, as employees feel that their ideas and contributions are valued.
In order to successfully implement OPL in the manufacturing industry, there are a few key steps that organizations should follow. Firstly, it is important to have a clear understanding of what information should be included in each OPL. This includes the problem or opportunity that was identified, the cause of the problem, the solution that was implemented, and the results of the solution.
Secondly, organizations should develop a system for sharing OPLs throughout the organization. This could be done through regular meetings, email, or an online platform. The key is to make sure that the information is easily accessible and can be quickly shared with others.
Finally, organizations should ensure that they have the resources in place to support the implementation of OPL. This includes providing training to employees on how to create and use OPLs, as well as having dedicated staff to manage the process.
In a nutshell, One Point Lesson (OPL) is a powerful tool that can help organizations in the manufacturing industry to improve quality, efficiency, and overall operations. By standardizing and spreading best practices, organizations can foster a culture of continuous improvement and identify and eliminate non-value-adding activities. To successfully implement OPL, organizations should follow a few key steps, including having a clear understanding of what information should be included in each OPL, developing a system for sharing OPLs, and ensuring that they have the resources in place to support the implementation.
Perfection
Perfection is a goal that many organizations strive for, and it is no different in the manufacturing industry.
Perfection is a goal that many organizations strive for, and it is no different in the manufacturing industry. By striving for perfection, manufacturers can improve the quality of their products, reduce waste, and increase efficiency. But how exactly can perfection be achieved in the manufacturing industry?
One of the key components of achieving perfection is through the implementation of a continuous improvement mindset. This involves constantly looking for ways to improve processes, systems, and products. This could include implementing new technology, streamlining processes, or making changes based on customer feedback. By continuously seeking out ways to improve, manufacturers are able to stay ahead of the curve and remain competitive in an ever-evolving industry.
Another critical component of achieving perfection in the manufacturing industry is through effective communication. Communication is key when it comes to identifying and addressing areas for improvement. Whether it is between departments, between management and employees, or between a manufacturer and its customers, effective communication is essential to achieving perfection.
Another way to achieve perfection in the manufacturing industry is through standardization. By establishing and following standardized processes, manufacturers are able to reduce waste, improve quality, and increase efficiency. This could involve standardizing equipment, tools, and work processes, or even creating a standard operating procedure manual that outlines the steps involved in a particular process. By having standardized procedures in place, manufacturers are able to ensure that their products are of the highest quality and that their processes are as efficient as possible.
Quality control is another critical component of achieving perfection in the manufacturing industry. This involves inspecting products and processes to ensure that they meet the standards set by the manufacturer. Quality control processes could include regular inspections, audits, and testing of products, as well as processes such as supplier selection and product design. By implementing a robust quality control system, manufacturers are able to identify and address any issues before they become major problems.
Investing in training and development is another important step in achieving perfection in the manufacturing industry. By providing employees with the training and resources they need to succeed, manufacturers are able to improve the skills and knowledge of their workforce. This could include providing employees with training on new technologies, new processes, or even soft skills such as effective communication and teamwork. By investing in their employees, manufacturers are able to improve their overall operations and move closer to their goal of perfection.
In a nutshell, achieving perfection in the manufacturing industry is a goal that can be achieved through a combination of continuous improvement, effective communication, standardization, quality control, and employee training and development. By striving for excellence in all areas of their operations, manufacturers are able to remain competitive, improve the quality of their products, and provide customers with the best possible experience.
Product Machine Matrix
The Product Machine Matrix is a methodology that can be used in the manufacturing industry to improve production processes and achieve operational excellence.
The Product Machine Matrix is a methodology that can be used in the manufacturing industry to improve production processes and achieve operational excellence. The idea behind this approach is to create a matrix that matches the type of product being produced with the appropriate machine for that product.
The first step in implementing the Product Machine Matrix is to analyze the current production process and identify areas where improvements can be made. This can be done through the use of data and performance measurement tools, as well as by observing the process and gathering feedback from employees.
Once the areas for improvement have been identified, the next step is to determine the optimal machine for each type of product. This involves considering factors such as the complexity of the product, the volume of production, and the skill level of the operator. It may also be necessary to make changes to the existing machines or to purchase new equipment in order to meet the needs of the production process.
The Product Machine Matrix also requires the establishment of standard work procedures for each machine and product type. This helps to ensure that the production process is consistent and efficient, and it also provides a roadmap for continuous improvement. Standard work procedures should be regularly reviewed and updated based on performance data and feedback from employees.
Another important aspect of the Product Machine Matrix is the need for visual management. This involves creating clear and easy-to-understand visual aids, such as work instructions and flow charts, that help to guide employees through the production process. This helps to prevent errors and improve productivity, as well as making it easier for employees to quickly identify and resolve any issues that may arise.
To be effective, the Product Machine Matrix must be integrated into the overall culture of the organization. This requires the commitment and engagement of employees at all levels, as well as a focus on continuous improvement and a willingness to embrace change. Regular training and communication is also key to the success of the methodology, as it helps to build the necessary skills and knowledge, and ensures that everyone is working towards a common goal.
In a nutshell, the Product Machine Matrix is a powerful methodology that can be used to improve production processes in the manufacturing industry. By carefully matching the type of product with the appropriate machine, and by establishing standard work procedures and utilizing visual management techniques, organizations can achieve operational excellence and drive continuous improvement. With the right approach and commitment, this methodology can deliver significant benefits to any organization looking to optimize its production processes.
Regular Communication
Regular communication refers to the continuous exchange of information between different departments and individuals within an organization.
Regular communication refers to the continuous exchange of information between different departments and individuals within an organization. The aim of this communication is to ensure that everyone is on the same page, working towards the same goals, and that any problems or obstacles are addressed promptly. In this article, we will explore the positives aspects of using regular communication in manufacturing and how it supports shop floor management in three steps.
Improves Collaboration and Cooperation
Regular communication plays an important role in improving collaboration and cooperation within an organization. When everyone is kept informed about the latest developments, it becomes easier for employees to work together effectively. They can share ideas and best practices, identify areas for improvement, and help each other overcome challenges. As a result, teamwork becomes more efficient, and everyone is able to contribute to the success of the organization.
Facilitates Problem Solving
Problems and obstacles are a natural part of any manufacturing process. However, if they are not addressed promptly, they can quickly escalate into bigger issues. Regular communication helps to ensure that problems are identified and addressed in a timely manner. When employees are able to openly communicate with each other, they can work together to find solutions and prevent problems from getting worse. This helps to minimize the impact of any issues on production and ensures that the organization is able to maintain its competitiveness.
Supports Shop Floor Management
Regular communication is also an important aspect of shop floor management. Shop floor management refers to the process of managing the day-to-day operations of a manufacturing facility. Regular communication helps to ensure that everyone is aware of their responsibilities and is able to perform their duties effectively. It also helps to identify areas for improvement and makes it easier for managers to provide feedback and guidance. In addition, regular communication helps to create a culture of continuous improvement, where everyone is encouraged to take an active role in driving progress and improving performance.
In a nutshell, regular communication is a crucial aspect of Lean management in manufacturing. It plays an important role in improving collaboration and cooperation, facilitating problem solving, and supporting shop floor management. By incorporating regular communication into their operations, organizations can ensure that everyone is working together effectively, that problems are addressed promptly, and that the organization is able to maintain its competitiveness.
Cell Production
Cell Production focuses on optimizing the flow of work and improving efficiency in manufacturing and operations.
Cell Production focuses on optimizing the flow of work and improving efficiency in manufacturing and operations. It is based on the concept of organizing work into cells, which are self-contained units responsible for performing a specific set of tasks. The goal of cell production is to minimize waste, increase flexibility, and improve overall performance.
The origins of cell production can be traced back to the 1950s and 60s, when Toyota and other Japanese companies were experimenting with new approaches to manufacturing. Over time, the concept of cell production has evolved and been refined, and today it is widely used in a variety of industries, including automotive, electronics, and consumer goods.
In order to implement cell production effectively, there are several key steps that organizations must take. Firstly, it is important to conduct a thorough analysis of the current state of the manufacturing or operations process, in order to identify areas where improvements can be made. This may involve mapping out the flow of work and identifying bottlenecks or other inefficiencies.
Once these areas have been identified, the next step is to reorganize the work into cells, taking into account the specific requirements of each cell and the skills and expertise of the employees who will be working in them. This may involve rearranging physical work spaces, or changing the way that work is assigned and managed.
It is also important to establish clear communication and feedback mechanisms, so that employees and teams can work together effectively. This may involve setting up regular meetings to discuss performance, or implementing systems for tracking and reporting on key metrics.
In order to ensure a successful implementation of cell production, it is also important to provide training and support for employees. This may involve providing training on the new processes and procedures, or offering coaching and mentoring to help employees develop the skills and knowledge they need to be effective.
Another key aspect of cell production is continuous improvement. This involves regularly reviewing performance and making adjustments as needed, in order to optimize efficiency and reduce waste. This may involve experimenting with different approaches, such as implementing new technologies or streamlining processes, in order to find the best solutions.
In conclusion, cell production is a powerful methodology for optimizing performance in operations and manufacturing. By reorganizing work into cells, minimizing waste, and continuously improving performance, organizations can increase efficiency, reduce costs, and improve overall performance. In order to be successful, organizations must take a structured and systematic approach, and be committed to ongoing improvement.
TPM - Total Productive Maintenance
Total Productive Maintenance (TPM) is a maintenance strategy that involves involving all employees in the maintenance process to maximize equipment productivity and minimize downtime.
Total Productive Maintenance (TPM) is a methodology that originated in Japan in the 1970s and has since become a widely recognized and adopted approach to operational excellence in manufacturing and other operations-focused industries. It is a comprehensive approach that seeks to optimize the performance of equipment and processes through a focus on maintaining and improving reliability and efficiency.
The origins of TPM can be traced back to the Japanese auto industry, where manufacturers were seeking ways to increase productivity and competitiveness in the face of increasing global competition. TPM emerged as a response to the need for a more proactive and integrated approach to equipment maintenance, with the goal of improving both productivity and overall equipment effectiveness (OEE).
Over time, TPM has evolved and expanded to encompass a wider range of objectives and activities. Today, it is widely regarded as a best-practice approach to operational excellence, and is widely used in many different industries, including manufacturing, healthcare, and government operations.
One of the key features of TPM is its focus on involving all employees in the maintenance and improvement process. This is achieved through the creation of cross-functional teams and the use of a range of techniques, including root cause analysis, standardization, and continuous improvement.
Another key aspect of TPM is its focus on data-driven decision-making and performance measurement. This involves the collection and analysis of data on equipment and process performance, which is then used to identify areas for improvement and to drive continuous improvement efforts.
When properly implemented, TPM can have a significant impact on organizational performance and competitiveness. This can include improvements in equipment reliability, increased productivity, reduced waste, and improved overall equipment effectiveness (OEE).
To achieve these benefits, it is important to implement TPM in a structured and systematic way, with clear goals and objectives and a strong focus on continuous improvement. This typically involves a multi-phased approach, starting with an assessment of existing processes and equipment, followed by the development of a comprehensive improvement plan and the implementation of specific improvement initiatives.
In a nutshell, TPM is a proven methodology that can help organizations achieve operational excellence by optimizing the performance of their equipment and processes. To achieve success, organizations must approach TPM in a systematic and structured way, with clear goals and objectives, and a strong focus on continuous improvement.
Key points for a successful TPM implementation:
Involve all employees in the process
Focus on data-driven decision-making
Adopt a multi-phased approach
Prioritize continuous improvement
Develop a comprehensive improvement plan.
Blue Sky Workshop
A Blue Sky Workshop is a process that is often used in organizational change management and is designed to promote creative thinking and help organizations to think beyond the boundaries of their current systems and practices.
A Blue Sky Workshop is a process that is often used in organizational change management and is designed to promote creative thinking and help organizations to think beyond the boundaries of their current systems and practices. The origin of Blue Sky Workshops can be traced back to Japan, where they were first developed by a group of industrial engineers as a way to encourage free thinking and help organizations to achieve their full potential.
The purpose of a Blue Sky Workshop is to provide a structured process that allows an organization to step outside of its normal routines and think creatively about the future. This process involves bringing together a group of stakeholders, including senior executives, managers, and employees, to brainstorm and imagine new and innovative ways of working. The workshop is designed to provide a safe and supportive environment where people can let their imaginations run wild and come up with ideas that may not be possible within the constraints of the current organizational structure.
To conduct a Blue Sky Workshop, it is essential to create an atmosphere of openness and collaboration. The facilitator should encourage participants to think outside the box and challenge their existing assumptions about what is possible. It is also important to provide participants with the necessary tools and resources to help them come up with innovative ideas, such as whiteboards, sticky notes, and brainstorming software.
The first step in conducting a Blue Sky Workshop is to establish the objective of the workshop. This should be a specific, measurable, and achievable goal that the participants are trying to achieve. For example, the objective might be to develop a new product, improve customer satisfaction, or reduce costs.
Once the objective has been established, the facilitator should begin by encouraging participants to think about their ideal future. They should ask participants to imagine what their organization would look like if they could achieve their goal, and what challenges they might face along the way. This exercise helps participants to think creatively and generate new ideas that they may not have considered before.
After the initial brainstorming session, the facilitator should then encourage participants to refine their ideas and develop them further. This may involve breaking down the ideas into smaller sub-goals, or exploring the feasibility of different approaches.
Once the ideas have been refined, the facilitator should then help participants to prioritize their ideas based on their potential impact, feasibility, and potential risks. Participants should then be encouraged to develop action plans that outline the steps they will take to achieve their goals.
The final step in the Blue Sky Workshop process is to review and evaluate the progress made. This may involve regular check-ins, progress reports, or other methods of monitoring progress.
In conclusion, the Blue Sky Workshop is a powerful tool for organizations that want to think creatively about the future and develop new and innovative solutions to their problems. By encouraging participants to think beyond their current systems and practices, organizations can achieve their full potential and create a brighter future for themselves and their stakeholders.
Mura
A traditional general Japanese term for unevenness. It is the waste of variation in the production process.
Mura, one of the three types of waste in the Toyota Production System, translates to "unevenness" or "inconsistency" in English. It refers to the irregularity in the flow of work, causing fluctuations in capacity and production. Identifying and removing Mura is essential for creating a steady work pace and optimizing resources.
One of the main causes of Mura is multitasking. When team members are constantly switching between tasks, they often lose focus and efficiency, leading to unevenness in the workflow. This results in longer lead times, increased inventory, and higher costs.
Another cause of Mura is overproduction. Producing more than what is needed, whether it's goods or services, creates an imbalance in the system and results in unnecessary inventory. This not only ties up valuable resources but also increases the risk of defects and rework.
To handle Mura, one must first understand the root cause of the unevenness. This can be done through value stream mapping, a tool that visually represents the flow of work and helps identify areas of waste. By analyzing the current state of the process, one can identify the steps that are causing Mura and implement solutions to eliminate them.
One effective solution is to implement a pull system, also known as "kanban" in Japanese. This system ensures that work is only produced when it is needed, eliminating overproduction and promoting a steady flow of work.
Another solution is to implement standard work. By standardizing the work process, team members are able to work consistently and efficiently, resulting in less Mura. This also helps in identifying and addressing any abnormalities that may occur in the process.
Additionally, involving the team members in problem-solving and continuous improvement activities can lead to increased ownership and accountability, leading to a reduction in Mura.
Implementing a pull system, standard work and involving team members in problem-solving and continuous improvement activities can help organizations to create a steady flow of work and optimize resources.
It's important to note that Mura is not a problem that can be solved once and for all. It's a continuous effort and requires constant monitoring and improvement. Regularly conducting value stream mapping and Gemba walks, where one goes to the place where the work is done to observe and understand the process, can help in identifying and addressing Mura.
In conclusion, Mura is a key concept in lean management and must be addressed to ensure a steady work pace and optimize resources. By understanding the root cause of Mura and implementing solutions such as pull systems, standard work, and involving team members in problem-solving and continuous improvement activities, organizations can achieve the goal of smooth and well-organized workflow.
Stay Connected
Ad
We want information fast and in a nutshell. We from OI recommend Blinkist* - because it’s simply the best.
* = Affiliate Link