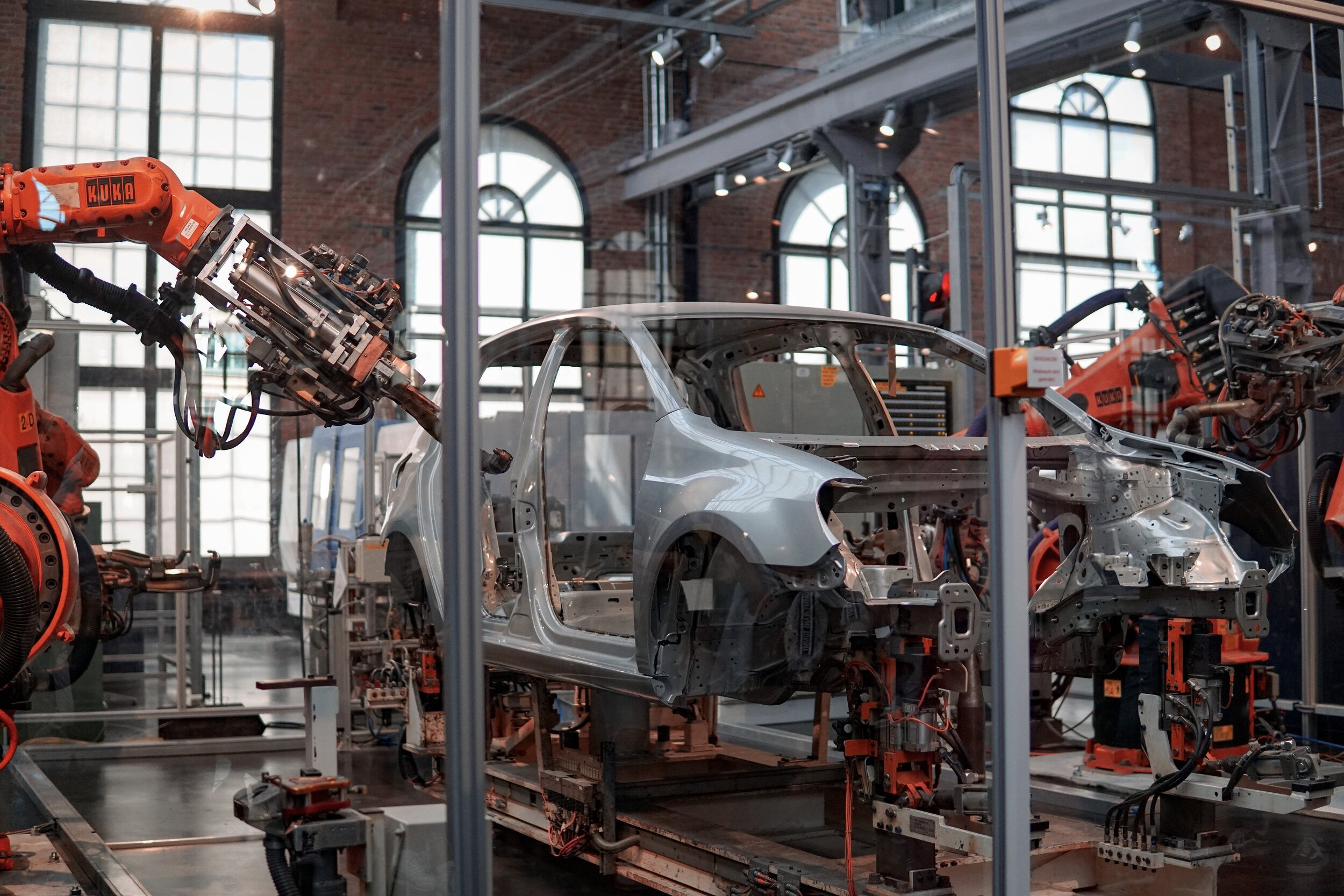
LANGUAGE OF LEAN
Milkrun
The Milkrun is the preset intralogistics concept to bring raw material, semi finished and finished goods to the place they belong at the time they are needed.
The Milkrun is the preset intralogistics concept to bring raw material, semi finished and finished goods to the place they belong at the time they are needed. The Mikrun is implemented based on existing consumption values, an internal supply cycle is defined in which deliveries on fixed routes are installed with specific times.
Based on these current consumption values, a logistic supply cycle is defined wherein raw material, semi and finished goods are delivered and picked up by a fixed route at a specific time. With this you will also optimize your intralogistics concept in general taking on action for a Milkrun concept.
So what is the idea behind the Milkrun concept.
The term Milkrun comes from the traditional milkman that was supplying milk to homes on a fixed route in a specific time. The milk delivery was based on the consumption of the households, by this only the amount of milk needed was delivered. Empty bottles have been picked up at the same time and brought back to the distribution center. So quite simple full bottle(s) delivered, empty bottle(s) picked up.
The cross company Milkrun
Nowadays the material management got a little bit more complex. Speaking in the external way of logistics a Milkrun is a supplier concept where customers ask for one or more shipping companies to manage different suppliers or customers on after the other in the form of a shipping cycle. In this way, goods and empty containers can be delivered and received at the same time without the need of centralization. The main goal is to have as less as possible empty trucks and at the same time being under full control of external material flow. Tours and deadlines are the guard rails on these cycles, reducing storage space is the nice to have side effect.
The benefits of the Milkrun concept
With installing a Milkrun you will be able to reduce shipping times, processing processes and therefore handling costs.
Just in Time and Just in Sequence deliveries are possible
Your planning is more structured as you will have fixed time frames
Less capital needed due to decreasing inventory/stock/WIP
You can integrate waste and empty container management
Increase of sustainability due to ecologically smarter transportation routes
Of course there are also some challenges with the Milkrun concept
Time consuming planning as quantity, duration, replenishment time, etc. needs to be considered
Processes and products need constant supply
Outbound Milkruns can be delayed by traffic or weather conditions
Economically relevant for larger business or higher demands of goods
Reliable supplier for products and transport needed
One last note for the internal Milkrun
Inbound the concept can be used in both ways, intralogistics and manufacturing. E.g. certain raw materials or semi-finished goods can be delivered on a regular basis to predefined workstations where the consumption can simply calculated. And on the fixed route the Mizusumashi can collect empty container and waste from production. This reduces internal ways of operators and guarantees a continuous supply of workstations. The next level would be to interlink all workstations or cells with your internal supply cycles to create an intralogistics flow, reducing the manual replenishment work. To find out what the Mizusumashi is just go here. In short: he/she is the guy who supllies goods on the shop floor in a structured process.
Mentee
The mentee is the student of the mentor.
The mentee is the student of the mentor.
The term mentoring describes the development process in an organization where an experienced person (mentor) passes on his/her knowledge and skills on to a new/unexperienced person (mentee).
The overall aim of a mentoring program is to develop and promote the mentee’s personal and professional growth within or outside your organization.
As described the mentor refers to the role of a personal trainer whose experience supports the development of the mentee. There is also the cross-mentoring approach out there where experienced managers from different departments or companies and their high potentials (mentees) come together for tandems. Cross Mentoring usually is an externally organized program in which the tandems are formed in cross-functional and cross-industry teams.
Minimarket Principle
The minimarket is the smallest version of a supermarket on the shop floor.
The minimarket is the smallest version of a supermarket. The minimarket is typically a small area where operators can take parts from located on the shop floor. Typically C-Parts which are refilled following the Kanban/2-Bin principle. The minimarket is filled by the milkrun which pulls material from the supermarket.
Shop Floor Management
Shop Floor Management supports the consistent development of on-site processes and procedures.
Shop Floor Management (SFM) helps the constant improvement of processes and procedures on the shop floor. The presence of mgmt. level staffing in manufacturing and their recognition on deviations from requirements dramatically hastens decision-making and consequences with inside the on the spot implementation of solutions.
Shop Floor Management really defines control duties and calls for unique modes of conduct. Management is supported via way of means of the utility of unique equipment. Five Shop Floor Management-associated duties are performed on the Shop Floor and are as follows:
Install regular communication
Confirm processes
Empower/Qualify staff
Make it part of the continuous improvement process (CIP)
Conduct problem solving in a structured approach
SFM emphasizes behavior that encourages your staff to resolve issues inside their scope of capabilities and strive for continuous improvement.
For example, management maintains its remarks to a minimum, handiest makes binding commitments, offers however additionally accepts feedback, profits its personal attitude of a situation, lets in errors in mastering situations, does now no longer lay blame and places in vicinity wondering techniques. SFM tools help the effectiveness of SFMgmt. e.g.:
Production diary, KPI charts, hassle-fixing sheet, T-cards
Shopfloor Management
What is Shopfloor Management?
Shopfloor Management
Basic components of shop floor mgmt
Clear management roles and responsibilities
Regular communication (Gemba Walks)
Key Performance Indicators
Problem-solving techniques
Visualization
Some explanation of the basics of operational leadership in shop floor mgmt. you organization will for sure profit from clear leadership roles and tasks. Your employees want near help for independent problem solving. Large control gaps, wherein the direct touch among the supervisor and his personnel and associates is reduced, normally do now no longer show themselves.
The Japanese version of a classical institution leader (Hancho), with a totally small management margin and occasional willpower of the personnel, regularly does now no longer suit into the qualified operator in organizations. The excessive qualification of operators is a vital aggressive thing in industry. In order to make suitable use of those capabilities with inside the processes, disciplinary management has the mission of the use of SMART´en to acquire desires at the same time as keeping room for manoeuvre and keeping a very good stability among needs and help.
Managers at the first mgmt. level do now no longer meet those demanding situations via time control seminars, however via greater practical duties and requirement profiles. Examine whether or not it's far important to introduce extra technical management as an alleviation for the first mgmt. level to your organization (CIP coordinator, Kaizen Manager, Process Champion). This feature can stand up from the present functions.
Jointly have a look at the opportunities of dispensing distinctive information regions (5S, set-up time reduction, CIP etc.) with inside the assembly teams expand collectively with you a brand new blending answer specially appropriate for you.
Regular communication
Regular communication is the structured approach to create a framework on a regular basis for opportunities. In this rhythm issues can be carried out and discussed across the management levels. Regular communication is an integral part of the day to day work of all players in your organization.
This way of communication, no matter if you call it huddles, stand up meetings, shop floor meetings, etc. guarantees a continuous flow of information without loss of information itself as it is fast and recurring. A subject matter-associated exchange takes place where employees are enabled to independently define measures, hassle answers and pointers for development and to remedy conflicts as quick as possible.
The continuous flow of information between the departments throughout the complete organization is guaranteed through these regular and short meetings. One positive side effect is that with regular communication you will also calm down daily operations management by clearly separating the topics (e.g. operative commercial enterprise, 5S, CIP, etc.). It is vital that these regular meetings are performed continuously and adhered to in order that normal communique will become independent.
Key Performance Indicators
Regular communication can only exist if the information inside these meetings are defined and standardized. The standard of these meetings is not only the agenda but more important the Key Performance Indicators (KPI). The target of working with KPIs is to have a framework for employees that provides information on the achievement of objectives. When you want to successfully control your production be aware that KPIs are broken down in such a way that they have a direct connection to the operators or designated workstation. Only then they are becoming a real instrument of control by which teams and departments can be measured. The positive thing about KPIs is that with the continuous improvement process paired with a structured problem solving approach all employees will see the effect of implemented measures on the KPIs. To get the full information on KPIs go here.
Problem Solving
Problem solving isn’t always as simple as it sounds, but it clearly shows the effectiveness of clear shop floor management. There are plenty of problem solving methods out there (Ishikawa, 5 Why, A3, Root Cause Analysis, just to name a few) and lean methods (e.g. 5S, set-up time reduction, Hejunka etc.) are well known in the manufacturing industry. But these methods are there to help your organization to deal with more complex issues, this means that they are not really useful for operators that are dealing with daily production but more for a problem solving team consisting of employees from different departments.
To tackle problem solving the right and sustainable way the role of a Kaizen Manager should be installed in your organization in order to steer the problem solving and continuous improvement process. Kaizen Manager help you to get out of this “fire fighting mode” with a sustainable CIP culture.
Visualization
For a clear visualization of running process in your organization, cleanliness and orderliness is the main part of it. Clarity of your processes on the shop floor is the foundation for all lean manufacturing activities. Having the clarity the implementation and maintaining of visual management methods will guide you to a real state of flow.
There are different ways for visualization out there (find a deeper insight here)
The target with visual management and those methods are all the same:
Create transparency
Visual representation of procedures processes and services
Making problems (or bottlenecks) visible
All documents and information are daily updated and right at the place of action clearly visualized for everybody in the organization (e.g. blackboards, Workflow Boards, Shop Floor Boards, Andon Boards, etc.).
Following the PDCA cycle the status of problem solving activities are recorded and visualized. KPIs on different topics are installed and tracked and so on. Important is only that all this information follows also a clear structure and has its own spot on the shop floor (e.g. a shop floor corner). Visualization starts at the workplace of a operator and ends at the management board of the plant manager or owner of the organization.
But in the end it always supports the Continuous Improvement Process in order to bring your organization the next level or simply to overachieve your customers expectations. To get a full insight in Visual Management, read the full article here.
Sensei
In the lean world a sensei is a lean production expert that transfers his knowledge as mentor on to his mentees.
In the lean world a sensei is a lean production expert that transfers his knowledge as mentor on to his mentees.
To be successful with a Sensei it's been revealed that you need to start at the top and find a sensei to work with in order to engage all employees on the shop floor. As Lean activities reach industrial maturity, the role of the Sensei remains a gray area.
It is obvious that your organization needs a Sensei to adapt and successfully implement Lean principles. Therefore, the Sensei position will be your bottleneck in Lean implementation. In every Lean transformation process, one learns at some point that the success of a company consists in learning to learn.
As a little guide, consider the following three effects:
Learning curve: The learning curve of each department and initiative is tracked by their manager in the organization rather than having to compare it to established best practices across your organization.
Spillover: Effective learning practices are passed through hands-on, experiential learning from person to person within your organization rather than through predetermined processes.
Value-Based: Lean as a whole provides a learning framework that aims to balance customer satisfaction (which leads to organizational success) with employee satisfaction (and personal fulfillment) through a set of principles and tools aimed at discovering how MUDA can be reduced and value can be increased . Adding activities in all areas of the organization.
This approach has both sides of the medal, but the weak and the strength are lying in the learning path of each employee. Following the lean principles, every employee is expected to discover:
What do I need to learn: What is my personal challenge in order to better align my work with customer value and thus sustainable and profitable growth with the satisfaction of all my colleagues to reconcile.
Learning from the shop floor: The learning style is deeply embedded in daily operations. Employees are learning results from their support of learning activities at all levels. Because all employees solve their problems or show initiative, everyone is expected to interpret the conclusions of others and find a way to adopt the solutions to their own work. It is the responsibility of the Sensei to support its learners in this learning phase. Learning by doing is the correct way to describe it.
Create a learning environment for your employees: Learning on the job is never easy, especially in today's business climate. Consequently, one of the key functions of a Sensei in the Lean perspective is to create a visual environment for employees where it is easier to recognize than normal and where opportunities for continuous improvement in small steps (Kaizen in Lean jargon) are clearly visible Everyone. A learning environment also means a stable affective environment where mistakes are not punished but seen as a source of learning.
The Sensei is not a boss at all. He or She has no power and can only suggest. The Sensei's task is to help all employees in your organization to develop their own lean thinking through practical exercises in workshops. The Sensei's job is to convince middle managers that solving today's problems will, in the long run, prevent tomorrow's fires.
The essence of Lean is learning while solving problems. This is a difficult task at the best of times, and indeed every person in your organization must be taught to learn how to learn. In relation to managers, the Sensei has five main roles of support:
Finding problems
Tackling problems
Creating problems
Solving problems
And finally learnings from problems
"If you have no problems, you are dead". is a classic lean principle. Perhaps the most important part of Lean's problem-solving learning approach is the initial problem-finding phase. Lean's approach to business is to capitalize on every problem.
“Sometimes you WIN sometimes you LEARN!”
5M Method
5M Method is an other way of describing an ISHIKAWA Diagram.
5M Method is just an other way of describing an ISHIKAWA Diagram. This diagram is pre-structured with five given categories of potential causes: “Man”, “Machine”, “Material”, “Mileu = Environment” and “Methodology”. In a more detailed form of the environment you can further divide it in “management” and “measurement” which then is considered as 7M methodology.
One Piece Flow
One-piece-flow is a principle to cut production lead times.
The term One-Piece-Flow basically describes the radical reduction of lead times through flow-optimized production. In an ideal state processed parts or components are moved from one process step to the next without any interim storage. The quantity moved consists only of one part or one batch. You will only be able to achieve this when your work systems are closely connected. The transition of a work system to an one-piece-flow oriented system can only succeed if there is a high availability of existing capacities and flexibility.
Getting your production to flow combines increased productivity and increased employee motivation.
As with most of the lean terms the one-piece-flow principle made its way from the Toyota Production System where it is referred as operator centric work flow. Instead of day in and day out performing the same task at a fixed work station the operator moves with the workpiece through the complete process steps, station after station, for which he/she has to be qualified for all process steps. It is quite similar to a Chaku Chaku line, while Chaku Chaku describes a concrete line layout, one-piece-flow is a principle or mindset so to say. The basic idea behind it is to reduce defects through lacks of concentration and increase motivation of operators through variety.
Lean Manufacturing terms might seem complex, but as most of the time, the principle behind is straight forward and quite simple. As they seem to be no brainers they easily get forget about it which will automatically lead to waste. The best example for waste is the so called TIMWOOD(S), where two main drivers are high amount of Work in Progress (WIP) and high inventories.
Now let us have a look how the One-Piece-Flow principle can help.
The principle of One-Piece-Flow is a new form of flow production. In contrast to conventional forms of flow production the worker in the one-piece.flow production does not remain in his place. Generally speaking the operator has no place of his own - he is always moving with the good. This is exactly where the reference to Chaku-Chaku comes from. With the sequence principle, on the other hand, the operator only interacts with the workpiece on one process step.
After on part is finished the operator starts again at the beginning of the line. This procedure comes with certain demands on the assembly line. U-Shape Layout is the most favorite one, as start and end should be as close as possible to each other in order to keep ways short and transition seamless. The U-Shape Layout is also great as raw material and other components are supplied from the outside, what makes the job of the Mizusumashi easier, and the value adding activities are on the inside.
But speaking about the advantages of One-Piece-Flow, the try to make it short:
Arrangement of workstations simplifies the arrangement of operators
If deviations occur, the operator knows exactly where it is coming from
With the CIP the continuous optimization is really driven on a constant basis
Applied correctly, lead times are drastically reduced
Inventory is drastically reduced
Used space on the shop floor can be reduced by 60% compared to conventional production
Motivation of operators raises as they are responsible from start to end and do not have this monotone daily routine of just one work station
In addition, the use of U-Shaped assembly lines, and if they are build up on standard profiles or standard shelvings, it gives you a huge amount of flexibility. Where workstations or the complete line can be easily extended, reduced or adjusted to new needs.
JIDOKA
Jidoka is the Japanese word for automation. It describes a form of automation where machinery stops by itself when defects are detected and notifies humans to clarify what is going wrong.
JIDOKA - the Japanese term meaning automation. In this form of automation the machinery itself is checking the parts produced for defects after processing. With this constant checking of process quality deviations can be directly detected and when defects occur the complete process is automatically stopped until the problem is solved.
You might have come across the word autonomation, which is simply a combination of the words autonomous and automation that describes the automation with still human interactions. JIDOKA has to be seen as a manufacturing principle rather than a methodology. The idea behind JIDOKA is that all machines in the process chain can run without a dedicated operator checking for process stability and quality outcome. If there is a defect or non-conformity of the process, the machine shuts itself down, preventing the defective parts of getting passed on the downstream process steps and for this reason it prevents producing scrap.
In the Toyota Production System, autonomation is one of the main pillar and is also known as intelligent automation as it is firstly focusing on the quality and the ability of a self running system rather than just focusing on the output. You might have also heard the description of automation with a human touch - if a deviation occurs the machine itself will stop the complete manufacturing process and only with the interaction of an operator, after the problem is solved, it can continue production. The upside is pretty clear - you will not produce any defective parts or waste value adding activities on non-conforming components.
With the use of the JIDOKA principle a number of advantages are coming with it:
Processing of non-conforming parts is immediately noticed, so that neither scrap nor rework occurs. Furthermore, no defective parts are passed on to the downstream processes steps
Since the defects are detected automatically, a 100% end of line inspection is no longer needed within the scope of quality assurance
With the help of automatic error detection, operators are no longer needed to monitor machinery, which is no-value adding activity anyway, so it can be declared as waste in the form of waiting time
Operators have now the freedom to perform multiple tasks during the same time or are able to dedicate themselves to new tasks at all
Maintenance activities will also decrease as crashes or malfunction due to the passing on of non-conforming parts is avoided
JIDOKA is the basis of analyzing the root cause of failures and implement sustainable counter measures to avoid these of occurring again
KAIZEN
The mother of all lean terms. The change for good.
KAIZEN the mother of all lean terms.
The word Kaizen is a combination of two Japanese words - KAI meaning change and ZEN meaning good. Kaizen is the epitome of continuous improvement and stands for the “change for the good”. Kaizen for your organization means continuous improvement involving everyone.
All together Kaizen is a collection of simple principles for improving your work but also stands for a management philosophy that has turned manufacturing principles upside down the way organizations think and act. The key of all success is that all employee should constantly critically review their processes and workplaces and improve them every day a little more.
You see Kaizen is a fundamental attitude for all players in your organization that results in high quality processes with zero defects on finished goods. Living Kaizen is the continuous strive to improve, simplify or optimize. This ongoing never ending process is therefore best known as the Continuous Improvement Process (CIP).
You can’t say that Kaizen is a methodology or tool, it is a mindset. I can’t emphasize this enough.
““The message of Kaizen is that no day should go by without any improvement in the company””
Kaizen does not depend on major innovations or fundamental changes, but on the everyday small improvements of your employees. The multiple suggestions for improvements paired with a rapid implementation mentality will show really fast their effect on success. The term of continuous improvement is fairly said just another way of the old fashioned suggestions scheme or idea management, which has a long history in the industry but less successful communicated and accepted.
To make a little list before writing too much I want to make it short. In order to pave the way for Kaizen thinking, a number of principles are linked to it, which should guide the thinking and behavior of all players in your organization.
Daily small improvements in all areas of your organization
Avoid any waste of material, time and money
Consider all downstream process steps as customers and then improve performance and quality
Improvements are always possible, it will never stop
Constant improvements are made on a small scale and step by step
No restrictions in terms of scope; products, services, processes, activities, technology, workplace - everything can be improved
Different methods and tools can be used, the decisive factor is the effect, not the procedure
Workplaces, work areas and the situation are viewed "on site", things are viewed and analyzed live (Gemba Walks)
with constant improvements, higher and higher standards are set and made the rule
Kaizen is a task for all employees in the company
All employees of your organization are directly involved in the Kaizen activities and everyone has to participate. To secure the success of Kaizen each individual should invest an adequate amount of time of their working hours in Kaizen activities and focus on their commitment on improvements. As your organization has different departments and by this different employee groups their Kaizen activities are different as well (e.g.):
Top management has to introduce and promote Kaizen as the fundamental principle and drive and monitor its implementation. It creates the right conditions within your organization
Middle management implements the requirements of top management and ensures that standards are kept. It also promotes the way of thinking by offering appropriate training
Team leaders support employees in developing ideas and implementing them. They are responsible for execution and success confirmation
The operators or administrators at the operational level work out concrete suggestions for improvement and implement them. This can also be done in small groups. Kaizen employees improve their specialist knowledge and experience by participating in further training courses.
To give you an example of daily Kaizen routines 5S seems the all time favorite.
You can read the full article on how to implement 5S here. But I will make a short excursion on 5S just to explain the way of thinking. 5S prescribes:
Seiri: Sort out all unnecessary objects
Seiton: Clean-up and correct arrangement of needed objects
Seiso: Keeping the workplace tidy so as to achieve the already established standards through 5S
Seiketsu: Establishing regulations for work standards
Shitsuke: Adherence to the Work standards and continuous improvement
Kaizen is always and everywhere its right to be applied.
Even when most of the people think that it is originally developed and deployed for the automotive industry (best known as the Toyota Production System) with clear mass manufacturing and assembly processes, there is no organization, yours included, that can not improve its performance and quality in terms of customer satisfaction, services, products and processes.
You see Kaizen has become a general way of thinking in all organizations and industries.
Thinking about organizations without Kaizen, you’ll see employees stick to rules and procedures with a “not my task” mentality. Only a few managers have to come up with fundamental long term changes. Kaizen on the other hand stands for the involvement of all employees and that everybody has to think every day what he/she can improve, simplify or optimize in his/her area of work for the “change for the good” of the complete organization, securing the long term success of your organization
YOKOTEN
Japanese for “across everywhere”.
Japanese term meaning “across everywhere”. With Yokoten the knowledgetransfer is carried out and all activities and countermeasures along the continuous improvement process are communicated organization wide and with other branches of the organization and its affiliates.
Yokoten is not just another Japanese word of the lean world. It might seem fancy to have only Japanese terms on the lean journey but one word isn’t that mainstream and well known but crucial when it comes to lean transformation in your organization. Yokoten describes the process of sharing knowledge across your organization. It includes systematics such as lead plans for copying and improving kaizen activities that work in your complete organization.
Think of Yokoten as horizontal deployment of improvement actions. The Yokoten approach is horizontal and peer-to-peer, with the expectation of Gemba Culture that your people go and see for themselves and learn how other departments or plants in your organization improved their processes. The idea behind is global knowledge transfer of improvement actions as basis for individual local solutions.
It is crucial that it is not a top-down thing where in all plants of your organization everything has to be the exact same. That simply will not work. It is more a benchmark where e.g. one plant in your organization is the champion of one manufacturing process (e.g. injection moulding). Therefore this plant is the “Lead Plant” and by this the benchmark for injection moulding organization wide. All other plants with injection moulding are welcome to the “Lead Plant” to learn from their experience and adopt the Kaizen activities to their own individual needs. With this kind of knowledge transfer a sustainable improvement and collaboration in your organization will be established.
In a nutshell, Yokoten can be understood as internal copy and improve. The role as senior manager is to spread the information and build bridges between the different locations/plants and give the transfer of knowledge a little jump start. Make your organization learn and improve from each other, most of the time there are already good examples out there and just want to be explored and further improved.
The long term success will prove that it is not the processes but the people that are continuously developed, that make the difference between a growing and successful organization or a simple copy cat of Kaizen activities.
The effective Yokoten process is a crucial brick for the foundation of a true learning organization. And no matter where you look at, truly successful organizations have a functioning organization wide knowledge transfer installed.
Supermarket
In the language of Lean the term supermarket describes a ways of an independent production control.
When speaking of a supermarket in lean context we are talking about an independent instrument that is used to control production. In a supermarket raw material and pre-commissioned components can be found in defined areas. The amount is well organized according the replenishment times of each component, in general the inventory is limited and components are refilled as soon as they are used. Following the Pull Principle with the help of the Kanban-System.
Concerning the supermarket we see it as one of the pull strategies that can be implemented as link between two process steps when developing the future value stream. The supermarket is the third option when firstly One-Piece-Flow and secondly FIFO are no options at all.
The supermarket is a great methodology to help your organization to manage a variety of inventory where you don’t need to know in what order the components will be consumed. Through the so called Kanban-Pull-System “internal customers” will take components of the supermarket, which are replenished by the internal logistics following the Kanban-Pull-Principle or in a pre-defined interval. With this integrated pull system of the supermarket as link between logistics and production you can also speak of a general replenishment pull system. But let’s have a look at the supermarket, what it can be used for and how it could look like in your organization.
The supermarket itself is a mix of FIFO lanes for different components stored in Mobile Racks or a typical shelf where components are stored in bins or on pallets. Let’s assume on workstation A 3 different components are assembled, in the supermarket 1 lane would be dedicated to only this component following the FIFO principle. With this explanation you can see why FIFO itself is preferred the supermarket. The supermarket is either steered with two bin principle or kanban cards. According the replenishment time, the replenishment is triggered with the extraction of components and the stock dropping below the minimum quantity.
You see, the key question is when to use a supermarket instead of installing plane FIFO lanes or even follow the One-PIece-Flow.
Here are some examples when this is the case:
Two main material flow streams come together before or are split after the supermarket
Your organization follows the made to stock principle, then the supermarket is at the end of production and stores finished goods
With the help of a supermarket different lead times of suppliers paired with a high variance can be leveled and production can be smoothly supplied
Upstream processes are lacking quality, downstream process steps can easily replace defective parts/components (interim solution until problem is solved)
Different change over times, when a downstream process needs a change over the upstream processes can fill the supermarket as a overflow stock that is drained after change over is done
All of this examples have in common that the final target is to eliminate the supermarket itself and improving the material flow in a way that simple FIFO lanes or a Two-Bin-Principle at workstations can be realized.
The size of a supermarket is always determined by the components and their space needed for storage and their replenishment lead times. So it is a good piece of advice to have a clear overview of your components, their recurring demand including their replenishment times and don’t forget about a little safety stock on top.
As already mentioned there are two principles that are already well-known for implementing and steering a supermarket. The first one we have a look at is the Kanban-Principle and the second the so called Two-Bin-Principle, in which the bins itself trigger the replenishment.
A supermarket running on Kanban Cards can be seen shematically in the picture below. Every component stored in the supermarket is represented by an individual card, on which all required information is listed in order to trigger the replenishment process. The Kanban-Card can be seen as order slip for suppliers. Usually Kanban-Cards are placed on the so called Kanban Board. This kind of a supermarket can be seen most of the time.
The Two-Bin-Principle is a kind of supermarket where the bins itself are utilized the same way the Kanban Cards are used. In this approach all components have e.g. two assigned bins, filled with the dedicated components for this exact bins. The full bins are placed at the workstation, components are used and the empty bins are placed on the empty conveyor, ready to be collected by the Mizusumashi. the Mizusumashi refills the bins with the defined components and brings the full set back to the workstation. This kind of “decentralized” supermarkets are typically used for small and C-parts, which are consumed by not only one but several workstations, e.g. screws, washers, etc. as the financial impact of c-parts are low and the space needed is small.
In the end the supermarket is the last possible way to implement a Pull System after failing on implementing a One-Piece-Flow or FIFO. The target is and always will be to reduce the size of the supermarket by changing it into a FIFO system or change the material flow in to One-Piece-Flow. Therefore the supermarket can be seen as needed but temporary. The size of a supermarket is always defined by the size of the components itself, the replenishment time incl. some safety surcharge and the consumption lead time of the production. By simply removing or adding Kanban Cards or Kanban Bins the level of WIP can be adjusted.
Value Stream
A value stream includes all activities (value adding as well as non-value adding) in your organization that are required to deliver your product or service to the end customer.
A value stream includes all activities (value adding as well as non-value adding) in your organization that are required to deliver your product or service to the end customer.
With the help of the value stream you are able to describe all process steps required for the creation of your product or service, from raw material to the delivery of finished goods. With the Value Stream Map you are able to find potential sources of waste and try to eliminate those by concentrating on the value adding processes. Focus on customer needs and what your customers are willing to pay for. In the ideal state the your production is completely smoothed out and material as well as information stays in a state of continuous flow. Optimization of this state is always driven through productivity. Even when continuous flow is the ideal state, intermediate storages, work in progress or buffers are not evil and even can be a result of optimized material flow.
Push and Pull
To read the full article please go here. Push and Pull is a way in which you can optimize your production and produce according the value stream and flow principle when storages become tight or order books full. Just in time can avoid costly warehousing but gives you also a straight dependency on delivery performance from upstream processes or suppliers.
The pull principle describes the process from the customer's point of view. The order triggered by the customer pulls the components through production. With the push principle, the goods are pushed through production. The pull principle saves the storage of finished goods and thus also transport and search effort.
Production Diary
The production diary, as part of the shop floor management system, defines a shift based weekly forecast incl. upcoming tasks for mgmt., supporting functions and is openly displayed on the shop floor.
With the help of a production diary, based on a pre-defined shift planning all other functions and outcomes are planned and tracked. This includes the mgmt. team as well as all supporting functions. In order that everyone is aware about the upcoming week the production diary is openly displayed on the shop floor. With the production diary and the pre-set structure of daily meetings of the shop floor mgmt. all daily activities are carried out. Best known part is e.g. Gemba Walks and the included problem solving activities e.g. A3 or just confirming that all processes run as planned.
With this big part of shop floor mgmt. it is clear that all regular meetings planned along the production diary are set. All other unplanned activities or extra meetings need to be conducted respecting the fixed schedule of the production diary.
Stay Connected
Ad
We want information fast and in a nutshell. We from OI recommend Blinkist* - because it’s simply the best.
* = Affiliate Link