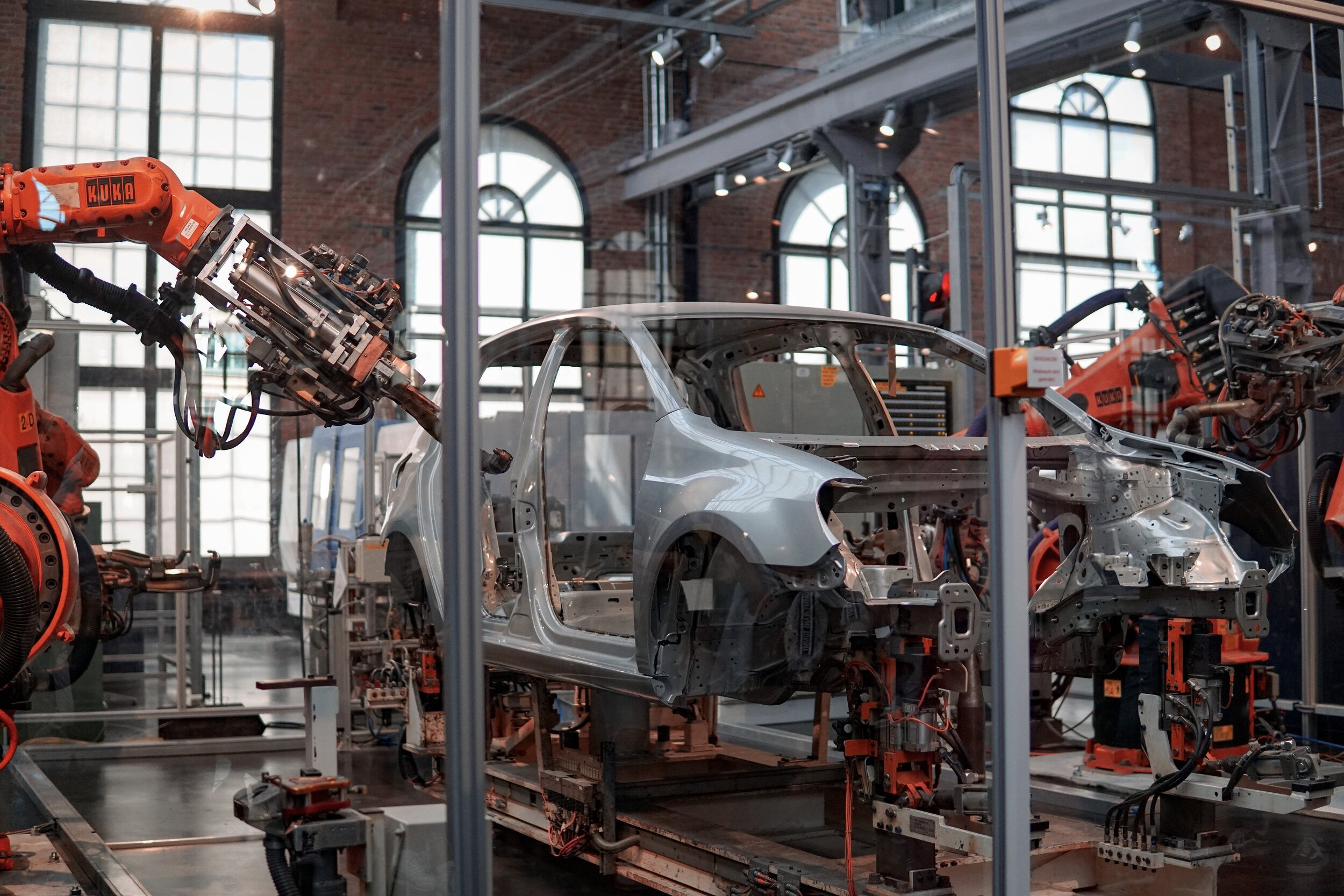
LANGUAGE OF LEAN
Standard WIP (SWIP)
The minimum amount of material or a given product, which must be in process at any time to ensure proper flow of the operation.
The minimum amount of material or product that must be in the process at all times to ensure smooth operation.
Standard Work is a little underrated concept in Lean Manufacturing. It is not simply standardization or work standards.
Standard Work is composed of three elements: Takt time, Work sequence and Standard Work in Process (SWIP). Takt Time is a fundamental concept of Lean Manufacturing, and Work Sequence is relatively intuitive. SWIP, however, is a bit more complex.
SWIP refers to the minimum necessary in-process inventory (work in process or WIP) to maintain Standard Work. It is not more or less than what is needed. To calculate the appropriate quantity for SWIP, one must ask a number of questions.
While a rough estimate of SWIP can be obtained by using the equation SWIP = Sum of Cycle Times / Takt Time, it is still necessary to determine where exactly this SWIP should be applied. The following steps provide a guide for determining the appropriate quantity of SWIP:
what’S the team size?
Standard Work is the most efficient combination of manpower, material, and machine, and is based on takt, work sequence, and Standard Work in Process (SWIP). By definition, it should include manual work. If a process is fully automated, it is not considered Standard Work. Instead, it is likely an NC program.
To determine the appropriate team size, the sum of manual cycle time is divided by Takt Time. Therefore, one piece of SWIP per person is required. The equation for manual SWIP would than be:
SWIP(manual) = Team member x (1 piece = person)
When determining the amount of SWIP, there should be no rounding, unless there is less than a full person. In that case, round up to the nearest whole number.
process steps as automatic one-piece cycle machines
Standard Work assumes the use of multiple processes or machines, and separates human and machine tasks as much as possible.
When using an automatic cycle, the worker will only be responsible for loading and unloading, and will not be present during the actual cycle. The automatic cycle time must also be shorter than the Takt Time, ensuring that there is always at least one piece in the machine during each cycle.
This is known as SWIP (single piece auto), and is calculated as the number of single-piece automatic cycle machines multiplied by one piece per machine. There is no rounding necessary as it is not possible to have less than a full machine. However, this only applies to single-piece automatic cycles, and calculations for batch processes or cycles with longer lead times may differ.
process steps as a single-piece non-machine automatic cycle
The term "non-machine automatic cycle" refers to process steps such as the drying time for paint, curing time for epoxy, and cooling time for hot parts.
These process steps may not involve machines, but they do require a certain amount of time for completion. The ratio of this time to the Takt Time is known as the Single-Piece Non-Machine Automatic (SWIP) cycle.
It is important to note that this value should always be rounded up to the nearest whole number. In some cases, equipment like turn tables or FIFO racks may be used to manage the curing process, ensuring that a finished product is available for each takt, and a new one is added for curing.
Process steps with a batch automatic cycle
Batch processes refer to situations in which equipment is designed to unload and load multiple pieces at a time, rather than one piece at a time.
A common example is heat treatment processes where a vacuum must be maintained and the door cannot be opened for hours. In such cases, a batch of parts is removed and then another batch is loaded. The cycle time per piece may be less than the Takt Time, but the overall automatic Cycle Time is greater than the Takt Time.
The Single-Piece Non-Machine Automatic (SWIP) cycle in this case is calculated as (Automatic time / Takt Time) x 2. The reason for this is that in batch processes, which do not allow for the addition or removal of individual pieces during the Takt, an extra quantity of complete parts is required. This concept can be compared to the idea of a pulley and bucket system used to retrieve water from a well, where one bucket is at the bottom of the well, full of water and another bucket is at the top, full of water, and during Takt, you empty out the bucket one by one and fill it back up one by one.
It's worth noting that in formulas 2, 3 and 4, manual cycle time is not included in the calculation because rule #1 takes care of that. This is because every manual Cycle Time must be within Takt by definition of Standard Work and since the unload/load time will involve one piece, there is no need to add manual time back into the calculation (in most of the cases).
Muri
Muri, a Japanese term meaning "unreasonable, impossible, or overburdened," refers to the excessive demands placed on resources, such as equipment and operators, which can lead to wear and production downtime.
Muri, a Japanese term meaning "unreasonable, impossible, or overburdened," refers to the excessive demands placed on resources, such as equipment and operators, which can lead to wear and production downtime. This traditional Japanese concept is often associated with overburden, unreasonableness, and absurdity. However, it can be eliminated through the implementation of standard work practices.
INTRODUCTION
Lean management aims to optimize resources and eliminate wasteful activities in the production process. However, many lean practitioners often focus solely on identifying and eliminating the 7 wastes, known as Muda, neglecting the importance of the other two M's: Mura and Muri.
Identifying and addressing Mura (unevenness) is essential for creating a steady work pace, but it is equally important to identify and address Muri, which is the overburden of resources in the organization's work system. By identifying Muri, organizations can analyze and optimize the capacity of their workforce.
Let's dive deeper into understanding what Muri is and its significance.
What does Muri stand for?
As a lean expert, it's important to understand the concept of Muri, which is a Japanese term meaning "overburden or unreasonable." It is one of the three types of waste (Muda, Mura, Muri) and a key element in the Toyota Production System.
Muri occurs when demands placed on a team exceed their capacity, leading to stress and decreased productivity and efficiency. This can also result in extra working hours and occupational burnouts, negatively impacting team morale and the overall health of the work process.
To avoid this, it's important to be mindful of the workload and to strive for balance at the optimal capacity, where all parts of the system are able to deliver results without the need for extra work. It's also essential to understand the root causes of Muri in order to effectively address it.
What can Muri cause?
It's important to be aware that overburdening teams can occur without conscious intent. Setting unrealistic deadlines, for example, can lead team members to rush their work and result in poor quality and decreased customer satisfaction.
For instance, if a designer is asked to create twice the number of images they are capable of producing within a certain timeframe, it's likely that the final output will not be of the highest quality.
This analogy can be applied to an assembly line as well, where rushing the process can increase the likelihood of low-quality products being delivered to customers. There are various reasons that can contribute to creating Muri and it's important to identify and address them to maintain a smooth and efficient workflow.
Over-demanding
One of the most apparent causes of Muri is over-demanding, where higher management places excessive workloads on teams with the belief that more inputs will result in more outputs.
However, this often leads to a rising number of pending tasks and can cause chaos and burnouts among the team members. This over-demanding behavior is commonly seen in the contemporary business world, it is important for management to be aware of the consequences of overburdening the team, and to instead aim for a balance between inputs and outputs.
Lack of training
The lack of proper training can lead to inefficiencies and the prolonging of tasks. For example, if a team member is not properly trained for a specific task, they may take longer to complete it than necessary.
For instance, if an individual is trained as a copywriter but is assigned tasks of a designer, they may require twice as much time to produce high-quality images as compared to a regular designer who is properly trained for that role.
This highlights the importance of providing proper training and ensuring team members are equipped with the necessary skills to perform their roles effectively, which can help prevent Muri and optimize the workflow.
Lack of communication
Effective communication is crucial for the success of any team. To avoid overburdening, it is essential to establish clear communication channels and practices.
For example, if a meeting with team members is held and a decision is made to create 10 new landing pages for a website, it is important that all team members are informed and aware of the project, including the expected deadline.
Failure to do so, such as in the scenario where a designer is not informed until the last day before the deadline, can lead to overburdening and negative consequences of Muri due to miscommunication. Clear communication can prevent such situations and help teams work efficiently and effectively.
Lack of proper tools and equipment
When the necessary tools and resources are absent, the occurrence of Muri becomes evident and unavoidable. For example, if certain developers are given new computers while others are still using outdated equipment, the latter group will experience overburdening as they will require more time to complete their tasks.
Muri can be caused by various factors, it's important to keep in mind that managing and addressing all of them is crucial in order to maintain a stable and efficient workflow.
To effectively deal with Muri, it's important to identify and understand the root causes, and develop strategies to address them. This may include providing proper tools and resources, implementing clear communication channels, and providing adequate training to ensure that teams have the necessary skills to perform their roles effectively.
Different ways to deal with Muri
Lean management offers various techniques and strategies that can assist in minimizing the negative impact of overburdening or eliminating it altogether.
Map your team’s workflow
A useful starting point in identifying and addressing Muri is to map out your team's workflow. One tool that can aid in this process is a Kanban board, which visually displays the various stages of the workflow and allows for an understanding of your team's capacity and where value is added.
Next, implementing work-in-progress limits for each stage of the workflow can ensure that team members are not juggling multiple tasks at once, but are focusing on completing one task before moving on to the next. This helps to create an efficient pull system, which leads to better organization and prevents overburdening.
When dealing with multiple teams whose work is interdependent, it is important to also implement WIP limits on a global level. For example, if team A is responsible for developing new features for a software service and team B is responsible for deploying those features, but team A is delivering new features faster than team B can deploy them, team B will be constantly overburdened. To avoid this, team A must ensure that team B has the capacity to handle new features before starting work on them. This may mean that team A may have to wait, but it is better to have one team blocked than have the entire company impacted.
Standardize your process
Another approach to addressing Muri is through the implementation of standardization. By documenting all processes and providing thorough training to team members, you can ensure that everyone is equipped to complete their tasks in an efficient and effective manner. This promotes clear communication and helps to eliminate misunderstandings, which can contribute to overburden.
Practice Jidoka
Another Lean management technique that can be used to address Muri is Jidoka. This practice empowers team members to halt the work process if an issue arises, and requires the problem to be resolved before the process can continue. This helps to establish built-in quality standards and prevent the need for rework.
Furthermore, regularly conducting Gemba walks, which involve physically going to the work area to observe and understand what is happening, can also provide insight into where Muri is occurring and how it can be addressed.
In a nutshell
Many businesses unknowingly put excessive demands on their staff, known as Muri in Japanese. This can lead to decreased efficiency and wasted resources, impacting profitability. To address Muri, it is important to:
Provide proper training and necessary tools and equipment to teams
Establish clear communication channels and protocols
Implement standard procedures within the organization
Stay Connected
Ad
We want information fast and in a nutshell. We from OI recommend Blinkist* - because it’s simply the best.
* = Affiliate Link