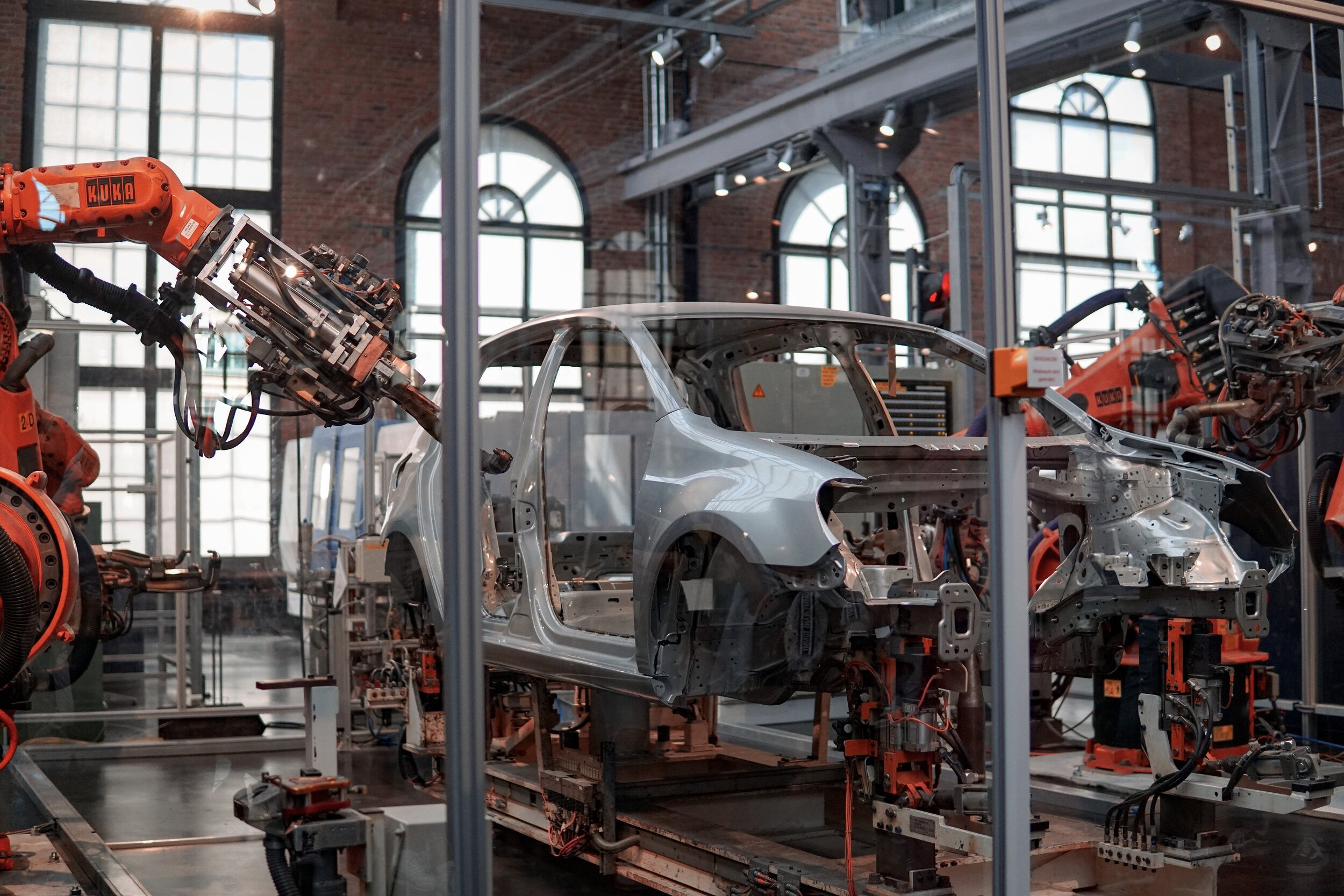
LANGUAGE OF LEAN
Production Smoothing (Heijunka)
Production smoothing, also known as Heijunka, is a key aspect of modern operations management. It refers to the leveling of production to match customer demand, while maximizing efficiency and minimizing waste.
Production smoothing, also known as Heijunka, is a key aspect of modern operations management. It refers to the leveling of production to match customer demand, while maximizing efficiency and minimizing waste. This technique has been proven to be an effective way to manage production processes and increase competitiveness in the marketplace.
The objective of production smoothing is to create a steady flow of products and services, reducing the variability and fluctuations in the production process. This helps to minimize the waste and resources associated with overproduction, excess inventory, and bottlenecks in the production line. By leveling production, companies can better predict customer demand and adjust their production processes accordingly.
One of the primary benefits of production smoothing is the reduction of waste in the production process. By leveling production, it minimizes the need for excess inventory and eliminates the waste associated with overproduction. This helps to minimize the costs associated with storage, handling, and transportation of excess inventory, while improving overall efficiency.
Another advantage of production smoothing is the improvement of customer satisfaction. By better predicting and matching customer demand, companies can ensure that they have the right products and services available at the right time. This helps to build stronger relationships with customers and improves the overall perception of the company.
To implement production smoothing, companies must first understand their customer demand patterns and the production processes that support them. This requires a thorough analysis of the production line, including the identification of bottlenecks and areas of waste. The company should then develop a production plan that balances customer demand with the production processes to create a steady flow of goods and services.
The company should also implement effective communication and collaboration between all departments, including sales, marketing, engineering, and production. This helps to ensure that all processes are aligned and working together towards the common goal of production smoothing. The company should also consider the use of technology and equipment to automate the production process and improve efficiency.
It is also important to engage employees in the production smoothing process. By involving employees in the implementation and ongoing management of production smoothing, companies can tap into their expertise and insights, and build a culture of continuous improvement. Employees should also receive training and development opportunities to enhance their skills and knowledge in production smoothing techniques.
In a nutshell, production smoothing is an effective way to manage production processes and increase competitiveness in the marketplace. By reducing waste, improving customer satisfaction, and engaging employees, companies can create a steady flow of goods and services, and improve their overall production efficiency. By embracing this technique, companies can achieve operational excellence and maintain their competitive edge in the marketplace.
Standard Work
Standard work is a fundamental principle of Lean manufacturing, a management philosophy that focuses on the elimination of waste and the continuous improvement of processes in order to increase efficiency, quality, and customer satisfaction.
Standard work is a fundamental principle of Lean manufacturing, a management philosophy that focuses on the elimination of waste and the continuous improvement of processes in order to increase efficiency, quality, and customer satisfaction. From the perspective of a Lean management expert, standard work is an essential tool for achieving operational excellence in the manufacturing industry.
Standard work refers to the detailed documentation of the best way to perform a specific task, taking into account factors such as the skills and experience of the workers, the equipment and materials used, and the desired outcome. This documentation should include step-by-step instructions, visual aids, and clear specifications for each step of the process. The goal of standard work is to ensure that each task is performed consistently and to the highest standard possible, regardless of who is performing it or when it is performed.
There are several key benefits to implementing standard work in manufacturing. Firstly, standard work helps to increase efficiency by eliminating waste and reducing variability in the production process. This leads to shorter lead times, lower costs, and improved quality. Secondly, standard work provides a clear understanding of the expected outcome of each task, making it easier for workers to know what is expected of them and to continuously improve their performance. Thirdly, standard work helps to promote a culture of continuous improvement by empowering workers to identify opportunities for improvement and to suggest changes to the standard work documentation.
To implement standard work effectively, Lean management experts typically follow a five-step process:
Define the task: Clearly define what needs to be accomplished and what the desired outcome is.
Observe and document the current process: Observe the current process, and document each step, including the time taken for each step and any variation in the process.
Determine the standard work: Analyze the data from the observation and determine the best way to perform the task, taking into account the skills and experience of the workers, the equipment and materials used, and the desired outcome.
Train the workers: Train the workers on the standard work and ensure that they understand the expectations and how to perform the task to the standard.
Continuously improve: Regularly review the standard work and identify opportunities for improvement.
In addition to the five-step process, Lean management experts also recommend the following ten tips for a successful implementation of standard work:
Start with a few simple tasks and gradually expand the implementation to other areas of the organization.
Engage the workers in the implementation process and involve them in the development of the standard work.
Focus on standardizing the process, not the workers.
Use visual aids, such as flow charts, to help the workers understand the standard work.
Regularly review and update the standard work to reflect changes in the process, the workers, or the equipment.
Foster a culture of continuous improvement by encouraging workers to suggest changes to the standard work.
Make standard work a part of the performance evaluation process for workers.
Use standard work as a tool for training new workers.
Use standard work to identify opportunities for process improvement.
Regularly communicate the importance of standard work and the benefits of implementing it.
In a nutshell, standard work is a powerful tool for achieving operational excellence in the manufacturing industry. From the perspective of a Lean management expert, standard work helps to increase efficiency, improve quality, and empower workers to continuously improve their performance. By following the five-step process and the ten tips for a successful implementation, organizations can reap the benefits of standard work and achieve their operational excellence goals.
Mura
A traditional general Japanese term for unevenness. It is the waste of variation in the production process.
Mura, one of the three types of waste in the Toyota Production System, translates to "unevenness" or "inconsistency" in English. It refers to the irregularity in the flow of work, causing fluctuations in capacity and production. Identifying and removing Mura is essential for creating a steady work pace and optimizing resources.
One of the main causes of Mura is multitasking. When team members are constantly switching between tasks, they often lose focus and efficiency, leading to unevenness in the workflow. This results in longer lead times, increased inventory, and higher costs.
Another cause of Mura is overproduction. Producing more than what is needed, whether it's goods or services, creates an imbalance in the system and results in unnecessary inventory. This not only ties up valuable resources but also increases the risk of defects and rework.
To handle Mura, one must first understand the root cause of the unevenness. This can be done through value stream mapping, a tool that visually represents the flow of work and helps identify areas of waste. By analyzing the current state of the process, one can identify the steps that are causing Mura and implement solutions to eliminate them.
One effective solution is to implement a pull system, also known as "kanban" in Japanese. This system ensures that work is only produced when it is needed, eliminating overproduction and promoting a steady flow of work.
Another solution is to implement standard work. By standardizing the work process, team members are able to work consistently and efficiently, resulting in less Mura. This also helps in identifying and addressing any abnormalities that may occur in the process.
Additionally, involving the team members in problem-solving and continuous improvement activities can lead to increased ownership and accountability, leading to a reduction in Mura.
Implementing a pull system, standard work and involving team members in problem-solving and continuous improvement activities can help organizations to create a steady flow of work and optimize resources.
It's important to note that Mura is not a problem that can be solved once and for all. It's a continuous effort and requires constant monitoring and improvement. Regularly conducting value stream mapping and Gemba walks, where one goes to the place where the work is done to observe and understand the process, can help in identifying and addressing Mura.
In conclusion, Mura is a key concept in lean management and must be addressed to ensure a steady work pace and optimize resources. By understanding the root cause of Mura and implementing solutions such as pull systems, standard work, and involving team members in problem-solving and continuous improvement activities, organizations can achieve the goal of smooth and well-organized workflow.
Standard WIP (SWIP)
The minimum amount of material or a given product, which must be in process at any time to ensure proper flow of the operation.
The minimum amount of material or product that must be in the process at all times to ensure smooth operation.
Standard Work is a little underrated concept in Lean Manufacturing. It is not simply standardization or work standards.
Standard Work is composed of three elements: Takt time, Work sequence and Standard Work in Process (SWIP). Takt Time is a fundamental concept of Lean Manufacturing, and Work Sequence is relatively intuitive. SWIP, however, is a bit more complex.
SWIP refers to the minimum necessary in-process inventory (work in process or WIP) to maintain Standard Work. It is not more or less than what is needed. To calculate the appropriate quantity for SWIP, one must ask a number of questions.
While a rough estimate of SWIP can be obtained by using the equation SWIP = Sum of Cycle Times / Takt Time, it is still necessary to determine where exactly this SWIP should be applied. The following steps provide a guide for determining the appropriate quantity of SWIP:
what’S the team size?
Standard Work is the most efficient combination of manpower, material, and machine, and is based on takt, work sequence, and Standard Work in Process (SWIP). By definition, it should include manual work. If a process is fully automated, it is not considered Standard Work. Instead, it is likely an NC program.
To determine the appropriate team size, the sum of manual cycle time is divided by Takt Time. Therefore, one piece of SWIP per person is required. The equation for manual SWIP would than be:
SWIP(manual) = Team member x (1 piece = person)
When determining the amount of SWIP, there should be no rounding, unless there is less than a full person. In that case, round up to the nearest whole number.
process steps as automatic one-piece cycle machines
Standard Work assumes the use of multiple processes or machines, and separates human and machine tasks as much as possible.
When using an automatic cycle, the worker will only be responsible for loading and unloading, and will not be present during the actual cycle. The automatic cycle time must also be shorter than the Takt Time, ensuring that there is always at least one piece in the machine during each cycle.
This is known as SWIP (single piece auto), and is calculated as the number of single-piece automatic cycle machines multiplied by one piece per machine. There is no rounding necessary as it is not possible to have less than a full machine. However, this only applies to single-piece automatic cycles, and calculations for batch processes or cycles with longer lead times may differ.
process steps as a single-piece non-machine automatic cycle
The term "non-machine automatic cycle" refers to process steps such as the drying time for paint, curing time for epoxy, and cooling time for hot parts.
These process steps may not involve machines, but they do require a certain amount of time for completion. The ratio of this time to the Takt Time is known as the Single-Piece Non-Machine Automatic (SWIP) cycle.
It is important to note that this value should always be rounded up to the nearest whole number. In some cases, equipment like turn tables or FIFO racks may be used to manage the curing process, ensuring that a finished product is available for each takt, and a new one is added for curing.
Process steps with a batch automatic cycle
Batch processes refer to situations in which equipment is designed to unload and load multiple pieces at a time, rather than one piece at a time.
A common example is heat treatment processes where a vacuum must be maintained and the door cannot be opened for hours. In such cases, a batch of parts is removed and then another batch is loaded. The cycle time per piece may be less than the Takt Time, but the overall automatic Cycle Time is greater than the Takt Time.
The Single-Piece Non-Machine Automatic (SWIP) cycle in this case is calculated as (Automatic time / Takt Time) x 2. The reason for this is that in batch processes, which do not allow for the addition or removal of individual pieces during the Takt, an extra quantity of complete parts is required. This concept can be compared to the idea of a pulley and bucket system used to retrieve water from a well, where one bucket is at the bottom of the well, full of water and another bucket is at the top, full of water, and during Takt, you empty out the bucket one by one and fill it back up one by one.
It's worth noting that in formulas 2, 3 and 4, manual cycle time is not included in the calculation because rule #1 takes care of that. This is because every manual Cycle Time must be within Takt by definition of Standard Work and since the unload/load time will involve one piece, there is no need to add manual time back into the calculation (in most of the cases).
Stay Connected
Ad
We want information fast and in a nutshell. We from OI recommend Blinkist* - because it’s simply the best.
* = Affiliate Link