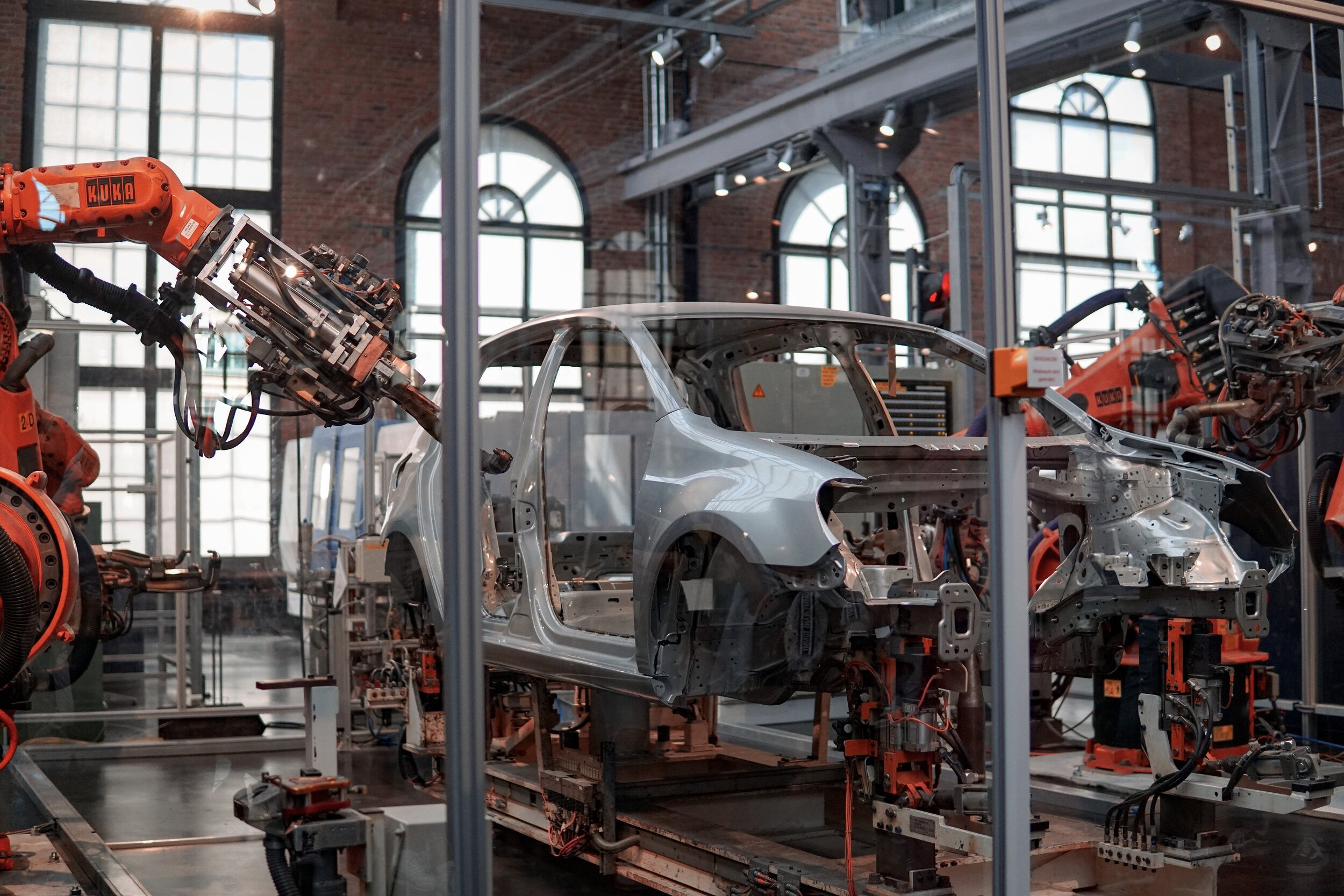
LANGUAGE OF LEAN
Bottleneck
Bottlenecks are the pacemaker of your process chain.
Bottlenecks in your process are the pacemakers of existing processes. These means if you tackle your bottlenecks in your process chain, it will have a direct impact on your cash flow.
A Bottleneck in a process chain requires the longest lead time of operations, A typical indicator for a bottleneck station is a upstream increased inventory or Work in Progress. The bottleneck is therefore the weakest link in the chain.
If you are running improvement or KAIZEN Workshops on your bottleneck station the upstream or downstream process steps will never be above 100% of performance. If so the bottleneck station changed to a different process step.
Bottlenecks are great to improve!
The potential of removing bottlenecks is unbelievable high, if you miss the chance to tackle the potential of bottlenecks in order to increase your throughput you are missing the chance to increase your performance and exceed customer demand/expectations. It is quite simple – the cost per hour of a bottleneck station can be seen as the loss of one hour of your complete process chain (e.g. production line) incl. the loss of parts not produced.
The whole deal is about increasing the throughput of your assembly line, to use machines efficiently combined with optimized operator working steps to increase the profitability of the assembly in total. Don’t make the mistake and focus only on the cost reduction part of it think and don’t be fooled by thinking in partial optimization.
To bring it to the point: In manufacturing, bottlenecks are continuously slowing down the whole assembly line. Focusing on permanent existing bottlenecks will sustainable improve the performance of the whole process chain and effect even other areas.
Cycle Time
In order-oriented production, the cycle time specifies the time from the start to the completion of the process steps.
Cycle Time = Takt Time > that upfront.
In order-oriented production, the cycle time specifies the time from the start of the first operation to the completion of the last operation for an order backlog.
Cycle time is the time your organization needs to carry out a work process, no matter what kind of process. For an optimum production cycle proper balancing needs to be done on both sides, the operators work and the machine cycles to meet the customer takt.
The period of time from the pickup of the work piece or process to be machined to the pickup of the next part. The pure machining time (added value) can differ from the cycle time, for example in the case of long paths or movements to pick up and transfer the individual work piece.
We will go in more detail on machine time and customer takt as well in upcoming articles.
Pareto Chart
A Pareto Chart is used to help determine the waste characteristics of a product.
A pareto chart is used in order to determine the waste characteristics of a product/good but also of processes. They are sorted onto a cart so that the most frequent defects can be visualized and stand at first place.
Today, I am writing this blog post after discussing several times with colleagues who want to understand the Pareto chart (or Pareto diagram) more deeply.
The Pareto chart is one of the basic tools of quality management. Usually, this chart consists of a combined bar and line graph. The vertical bars are representing the quantity of defects, and the line represents a cumulative percentage of the defects.
The descending order of bars is from left to right. The bar on the left will have the highest value, and the bar on the right side will have the lowest value.
Let’s discuss this in detail.
Pareto Chart
Sometimes, it is challenging for you to understand the problems and their causes. Instead of focusing on the root cause, you spend your time, solving problems, which were influencing the project least.
The Pareto diagram can help you overcome this situation. The Pareto diagram can help you segregate the defects and their cause. Once you get this info, you can focus on the cause which is generating the most defects.
The Pareto diagram is based on the Pareto Principle, which was developed by an Italian economist named Vilfredo Pareto. He found out that 80% of the wealth was spread to 20% of the population. Therefore, pareto is also known as the 80/20 rule.
We could now list several examples where this rule is confirmed such as
80% of the defects are coming from 20% of the process
or
80% of customer complaints are coming from 20% of all defects detected
or
20% of the defects are causing 80% of the problems…
The list can go on and on.
In general, this phenomenon can be interpreted as follows: Roughly 80% of the problems will be due to 20% of the causes, or the majority of issues will be due to a small number of causes.
However, keep in mind that the above rule is a general rule and the ratio is not absolute.
The Pareto chart is mainly used in quality management or Six Sigma approaches. This chart helps you to find the majority of the problems and their root causes. You then should focus on tackling those causes and therefor solve the majority of the problems.
How to Draw a Pareto Chart
Drawing a Pareto chart is very simple. The most important step is to collect the correct data.
The steps to drawing a Pareto chart are as follows:
Categorize your potential causes
Specify the measure, e.g. quantity, costs per failure, downtime, etc.
Set a time frame you measure, e.g. per shift, per week, etc.
Measure Measure Measure (If you can’t measure you can’t control)
Separate the data based on the categories
Draw a bar chart with causes on horizontal axis and number of occurrences on the vertical axis (Excel gives you predefined templates)
The category with the lowest quantity will be at the right and the highest quantity on the left
If you don’t have the histogram preset chart in excel - define a second row with the percentage value. Accumulated up to 100%. This will be your secondary axis. The values in percent will form the curve of distribution.
.To make it short - it should look like this:
Pareto Chart
Now, you can focus on the causes generating the majority of problems, analyze them, find their real root cause(s), and start to get rid of the issues one by one.
This chart can help everybody to identify causes of the most common problems. It also supports on prioritizing tasks and activities for KAIZEN Workshops or simply fire fighting. Having some Excel skills, it is very easy to create a Pareto and also often helpful communicating your actions to the upper management - you can bring it to the point.
This reading pick is not focusing on the professional approach of the Pareto (meaning quality matters in manufacturing) but more looking at the personal usage of the 80/20 Rule. We love it as it shows you how to focus on what really matters in live.
Read more in our reading picks here.
5S
The 5S Method is a five-level system for the provision of safety, cleanliness and orderliness on the workplace.
The 5S Method is a five-level system for the provision of safety, cleanliness and orderliness at the workplace. The term „5S“ is coming from 5 Japanese words that begin with the letter „S“.
These 5 words describe the 5 principles for the organization of the workplace:
1S – SEIRI
Cleaning: Sorting-out and get rid of all unwanted objects.
2S – SEITON
Orderliness: Clean-up and proper arrange tools needed.
3S – SEISO
Cleanliness: Maintain cleanliness at the workplace and keep the standards established through 5S workshops.
4S – SEIKETSU
Standardization: Establishing work standards developed by 5S sessions.
5S – SHITSU
Discipline: Observing compliance of new work standards and drive for continuous improvement.
Why do we need 5S?
Goals of the 5S during the implementation:
Safety
Flexibility
Quality
Costs
Ergonomics
How can you implement 5S at your organization?
How to implement 5S
The 5 steps of the 5S-Method:
Sorting out all unnecessary objects at your workplace
All needed objects have to be arranged in a proper way
Keep your workplace clean
Standardize the steps 1 to 3
Keep your new standard or improve it even more
5S is a continuous process!
The 5S checklist
In order to maintain the 5S procedure and standard you should be implementing a routine of a so called 5S audit. The 5S audit is an instrument of sustainable implementation of the five step system for safety, cleanliness and order at your workplace.
Therefore 5S is relevant in all areas of your company, no matter if you are working in a office or your focus is on the shop floor. To maintain the 5S implementation and the ongoing improvement of all 5 steps. The audit can support you on identifying deviation and to improve.
So why do you need the 5S Method?
It supports you on
Reduction of uncleanliness and its causes in the company
Reduction of latent waste in the company (e.g. untidiness, unneeded objects)
Reduction of defective equipment and tooling
Reduction of deviations from standardized manufacturing procedures due to unnecessary objects and frequent searches for misplaced objects
Increasing the awareness of the employees about tidiness, cleanliness, waste and deviations from standardized manufacturing procedures
Enhancing the positive impression of the company towards the customer
So what are the goals when you implement 5S in your company?
1 Increase safety at the workplace
Everything lies in its right place and employees receive a standardized and up-to-date description of their workplace
The employees know where to find everything needed in the case of an emergency
Markings on the floor are used as a visual control aid to help the employees to stay clear of any dangerous situations
2 Increased capability to react
Expeditious reaction to the requests of the customer and expediting the manufacturing process
By involving all employees, the internal flow of communication is enhanced along with the identification and removal of mistakes
It supports the expeditious preparation of e.g. work procedures, replacement of tools, increased flexibility of the employees, streamlines the work processes, increases the general economy by making the work procedures more effective; and expedites the continuous process of enhancement
Mistakes and deviations from the standardized work procedures become an exception and can be quickly eliminated
This reading pick will show you the methodology as well as real doing and conducting of 5S Sessions. It is a great guidance and a step by step instruction with lots of advice and practical tools that will allow you to conduct your 5S project from A-Z.
Read more in our reading picks here.
3 Enhanced quality
The proper arrangement of material and equipment decreases the amount of defective products and improves the repeatability of the work process
Enables the employees to determine at first glance what is needed to do to ensure quality
Makes the problems more perceivable and thus enables their solution
4 Cost reduction
Shortens unnecessary searches and reduces the time needed to find objects
Shortening time for exchange of tools > SMED
Creating new areas
Eliminating all unnecessary objects
Too excessive or insufficient supplies are discovered and are made visible
Expedient realization of counter-measures
5S designates the 5 basic principles for creating a clean, well-arranged and effective workplace with competent employees – the basis is orderliness = 5S.
5 Developing a “Visual Workplace”
In the case of a visually created workplace the work procedures are adjusted to enable all employees to have the possibility to observe the actual work process
Visualization:
Organization of the workplace
Manufacturing process
Distractions, such as defective objects, sources of danger etc.
Production indicators (plan, overproduction, or as the case may be, underproduction)
How can a 5S Audit support you?
The 5S Method makes sure that each workplace, in the production or office, is organized according to the principles of cleanliness, orderliness and safety
To secure the permanence and the continuity of adherence to the defined 5S standards it is necessary to regularly conduct 5S Audits
For the different areas of Production or Administration and others, specific questionnaires are prepared, on basis of which the obvious deviations from the defined planned state can be detected
The 5S questionnaires are combined with a list of counter-measures necessary to rectify the situation along with the names of responsible persons
Lead time
Lead times is based on the time that a component needs to get from the raw material stage to the customer.
Lead time – throughput time
In lean philosophy, lead time is seen as the key indicator. Lead time is proportional to the level of
> excess production and
> inventory in the value stream.
It is based on the time that a component needs to get from the raw material stage to the customer.
To calculate lead time in ...
... Batch production:
processing time + transport time + idle time
... Single-piece production:
Time from order input to operation
The total time it takes for a process to convert a raw
material to a finished quality part
The competitiveness of companies depends on whether products and services meet market requirements in terms of time, cost and quality. As the dynamics of the market increase, the importance of the time dimension increases. This means that products have to be developed, manufactured and made available to customers ever faster. The same applies to services of all kinds. The decisive factor here is the so-called lead time, which should be as short as possible.
What is the lead time?
The lead time (DLZ) describes the time span for processing orders or for the course of processes between and within companies. According to REFA, the lead time in a work system is referred to as time type TD. You
may include scheduled and additional stages and times,
is an important parameter for assessing the quality and performance of processes and work systems,
can be used in a variety of ways, especially to generate key figures,
is determined at REFA for orders (order lead time), process chains and processes (process lead time) and for individual work systems (work system lead time).
What are the components of the lead time?
The lead time in production plants consists of the following components (partly optional):
Execution time: Sum of the times of all process segments for carrying out task or order processing in the work system.
Additional time: Sum of the times of all process segments that can occur in addition to the scheduled execution of tasks. If additional times occur regularly, this is an indication of potential for improvement.
Transport time: Sum of the times of all process stages that are used to transfer the order to the following work system, for example, transport time of finished parts from assembly into the warehouse.
Waiting time: Sum of the times of all process sections in which the order waits between two work systems for its further execution, e.g. finished individual parts wait for assembly to the finished product.
Storage time: Sum of the times of all process stages in which parts, semi-finished and finished products of an order are stored in storage areas before, between, or after execution.
How can the lead time be shortened?
Approaches to shorten the lead time are:
technical or technological improvements
Avoidance of disturbances
Improvement of workflow and information flow - Process optimization
Balancing the capacities of the resources used and the employees deployed
Information and qualification of the employees involved
Push vs Pull Principle
One of the four building blocks of lean production. Push vs Pull production.
The pull principle is one of the main blocks in lean manufacturing > pull manufacturing. The customer demand determines which good will be produced and in which quantity. Max/Min inventory levels are agreed with suppliers and customers. This gives you the opportunity to limit overproduction.
In a pull process a workstation or process step is only being triggered when the downstream processes are free to take the output. This means that only when the customer initiates a need the value adding is started. By this a customer can be seen as internal as well as external one. This is lovely as you make sure that only what you will sell will be produced.
Pull is always to prefer against push. As it allows you to manage the WIP and inventories in between workstations which has a straight impact on your lead time. To successfully install a Pull System you have three choices, it is either the well known continuous flow installed, sequential pull or the replenishment pull.
All three types of connection will help you to achieve different levels of Pull in your environment.
No matter what it always comes down to three factors in your system:
Having max one piece of inventory between two process steps
Having a fix production sequence
and having a max number of parts waiting
Thinking about the three types of a Pull System, the continuous flow system has the highest level of Pull, as all three factors are highly involved. Only One Piece at the time and in between two process steps which means a fixed sequence as well as max one part waiting for the next process step.
If you have several workstation linked in one main manufacturing process working on one final product you have a work cell or simply a production line, depending on the shape you can call it e.g. U-cell.
With the sequential pull system you will have the second best choice of a pull manufacturing. It will have a fixed quantity, the sequence of production is defined but with a max number of WIP allowed between process steps. Basically you will allow buffers in your manufacturing. This can typically be seen in FiFo lines (First in First out).
Last but not least we have a look on the Replenishment Pull. This is in other words your supermarket in the production and your third and last option of implementing pull. The supermarket has a maximum number of components, parts or products waiting to be worked or processed on. But it is not known which one will be next. This type of inventory is usually steered or controlled using the Kanban systematic.
To put it in a nutshell - the following table should be fine to give you an overview:
Autounloading
In the lean world “auto unloading” means that every machine is automatically unloading the processed part or component, so that the operators’ task is reduced to only loading the machine.
In the lean world “auto unloading” means that every machine is automatically unloading the processed part or component, so that the operator’s task is reduced to only loading the machine. This also refers to the chaku chaku principle. The correct lean term of autounloading is the Hanedashi Principle which is explained here.
Ishikawa (Fishbone Diagram)
An ISHIKAWA is a chart that resembles a fish skeleton, with a main spine and branches (bones) drawn at a slant off the spine; used for quality control in two main ways.
If you are running problem-solving you will come across the so called ISHIKA (or Fishbone) diagram. An ISHIKAWA is a chart that resembles a fish skeleton, with a spine and bones drawn slanting off the spine; used for quality control in two main ways:
As a cause-and-effect diagram, where the spine leads to an effect (head of the fish) and the “bones” are cause factors
As a subdivision of quality requirements, where the spine represents a quality objective and the bones describe subsidiary traits or measurements that are important but are not the end in themselves. (Sometimes referred to as a Reverse Fishbone)
The fishbone diagram is simple to use and allows a quick and effective root cause analysis and to understand what corrective actions can be taken to have fast success. It is used for brainstorming and often in conjunction with the 5 Why Methodology.
In a ISHIKAWA, the various causes are grouped into categories and the causes cascade from the main categories, flowing towards the effect, forming what resembles a fishbone appearance.
The first step is to brainstorm all possibilities that could cause the problem and then drill it down to the factors that are causing the effect. Once found it is the task to eliminate them. It enables the team to focus on why the problem occurs and not the history of symptoms of the problem. It also displays a real time snap shot of the collected inputs of a team as it is updated.
How to Conduct a Fishbone Diagram
Draw the box on the right of a flip chart, large brown paper or white board, and write the problem statement (effect) in the box. Be as clear and specific as you can about the problem.
Now draw the line going from left to right as the ‘spine’, connecting to the problem statement.
Draw the ‘fishbones’ emanating from the spine. These represent the main cause categories.
Now label each Fishbone category. There are two options here. You can use the generic cause categories of Environment, Machine, Man, Material Methodology, which is easier to use for a team that is relatively new to this method but, but you can also use the brainstorming in the group to define the major categories related to the specific problem.
Now brainstorm all the causes to the problem. You could use the approach of writing each cause on a sticky note, going around the group asking each person for one cause. Continue going through the rounds, getting more causes, until all ideas are on the board.
For each cause, agree in the group which category the issue should fall in. (An issue can be addressed in several categories) and continue this process until the group have run out of ideas and all potential causes are at least placed under one category.
Next, get each team member a marker or sticker dots to mark the top three causes they think have the highest effect on the issue.
Not always mentioned but for us very important – also differentiate between the factors in three sectors
Factor of non conformity (process, drawing, etc.)
Factor for non detection
Simple cause
Once completed, the facilitator adds up all the markings for each cause and selects the top three with the highest scores. These three issues will now form the basis of additional investigation in order to find the root cause. The team may then investigate these causes further and use problem-solving techniques like 5 Whys to eliminate their occurrences.
An example Fishbone Diagram
A typical use case in industry is that a production facility has a too high scrap rate. Manager comes in and says “solve it”. As mentioned above the cross functional team gathered all data and ideas during a brainstorming session and listed all possible causes into the main categories.
The next step would be to pick the top three causes and delve deeper to find the true root causes.
Example of an Ishikawa Diagram
Some hints:
Remember, as with any task-based activity, always close a problem solving session with actions, clearly assigned owners and due dates – “Who is doing what by when?” This is important, as it keeps the teams focused on the project. Do not end up with an excel LOP use the Workflow Board instead to steer and assign tasks. This is great way to have transparency on task tracking and assignment
Don’t assign huge tasks which require several weeks to fulfill. Cut the elephant in pieces. Set up a regular meeting twice or at least once a week.
Hold people accountable and summarize the session, including the actions and deliverables
Have regular reviews with the team in between, therefore use a stand up meeting to gather the team and check for status against the actions planned. (Workflow Board)
Make every tasks as clear and simple as possible, so everybody of the team understands what is expected.
Besides ISHIKAWA you can also use, as part of Visual Management, the so called KAIZEN Board. It is a great opportunity to tackle issues before they become big problems. Also here it is a must to run it with discipline and continuity. It will support you on systematically embed problem solving behavior and continuous improvement culture in you company.
If you want to go deeper in the Ishikawa problem solving I recommend the book from Mickael Réquillard.
In this book, you will discover what an ISHIKAWA diagram is, its different representations and use cases, how to create one and how to effectively exploit the information gathered.
Read more about the book here or get it straight from amazon.
Stay Connected
Ad
We want information fast and in a nutshell. We from OI recommend Blinkist* - because it’s simply the best.
* = Affiliate Link