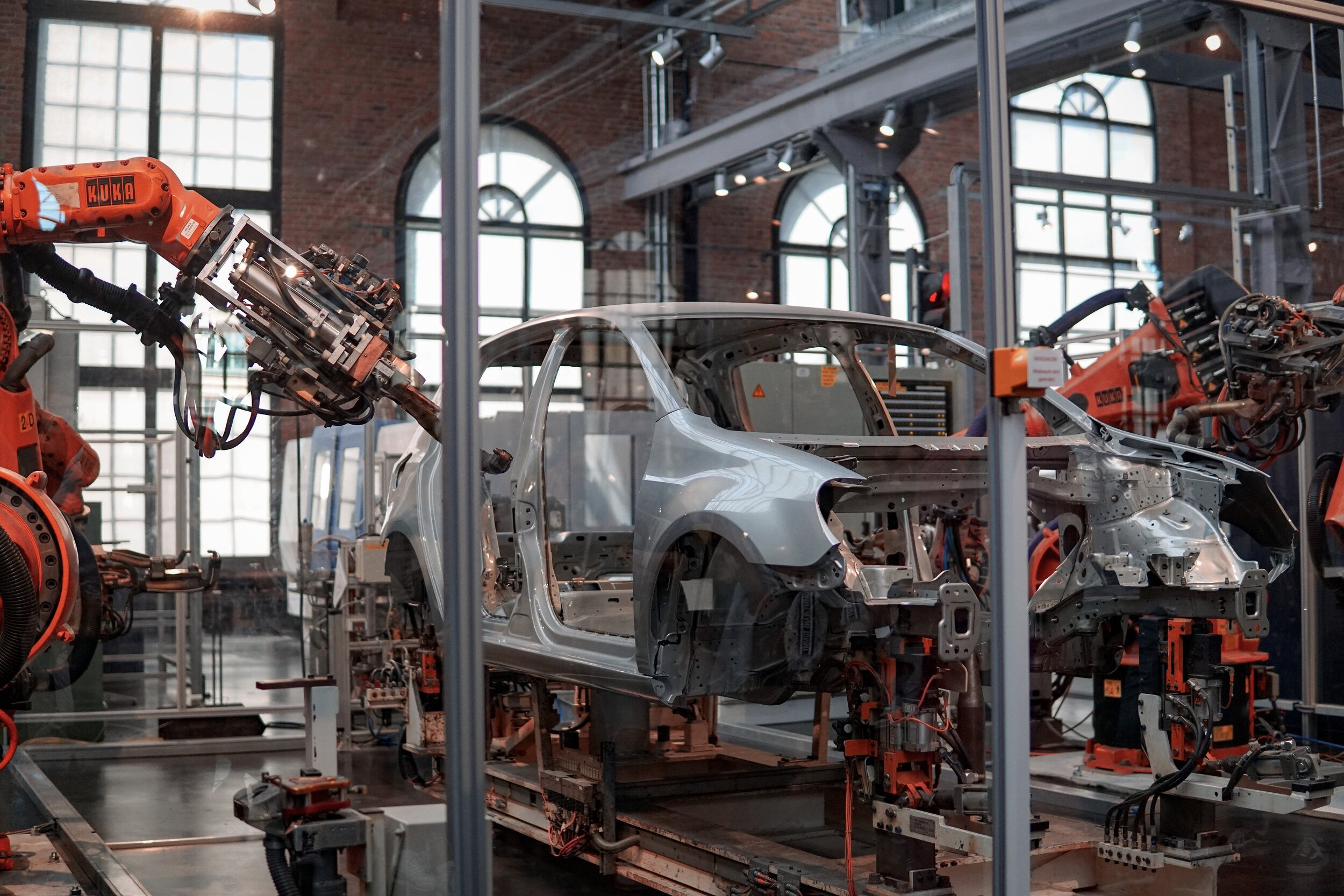
LANGUAGE OF LEAN
CHAKU CHAKU
The term Chaku Chaku comes from the Japanese and can be translated with "load load”. Also in general it has become a term for variant of a flow or series production, and the work in it.
The term Chaku-Chaku comes from the Japanese and can be translated with "load load”. Also in general it has become a term for variant of a flow or series production, and the work in it, naturalized, at of all the workplaces involved in the production of a product following each other so that the shortest possible distances between them are possible. Since there must also be space for transport, this is usually a u-shaped or omega-shaped formation.
The basis is multi-machine work: one operator works on several process steps. It is usually his task to load and unload the material. The stations work independently without the intervention of the operator, often simple tasks are taken over by the operators in order to save on machine purchases. In practice, the operators only take over the transport from station to station, sometimes there are “mini” buffers provided at the stations, in which a machined work piece can wait for a short time.
Through the Chaku Chaku production system, also known as flow production, can be different depending on the complexity of the parts to be produced also refrain from purchasing machinery or even dismantling machines. These machine systems are then replaced by mostly simple manual workstations.
In a Chaku Chaku line the operator primarily performs the loading and starting of the stations through. The material is supplied from outside, safety measures to the employees and the ejection of machined parts are automated. The capacity of the line is mostly determined by work distributions of one to three operators flexibly. The advantage of this system is that:
thus the usually high acquisition costs for complex interlinking machines
and the training time of the workers employed is usually shorter, since the
activities are often of a simple nature, and therefore don’t require extensive instructions and
there is no training on complex machines.
Also, with the Chaku Chaku principle, the cycle time can be controlled individually, for example, if the pre- and downstream machines run at different speeds, this will be controlled by the operators.
The structure of a Chaku Chaku Line is based on the simplest production principle in which manual labour is the most important factor.
The operator has to fulfill transport, quality control and process monitoring for this. In the manufacturing process, the principle applies that the machine is maintained and not man. Expensive technologies require a high occupancy of machines, are less flexible for fluctuations.
In the simple Chaku Chaku Line it is easy to achieve the required number of units through the design of flexible deployment of operators.
EMIPS Method
EMIPS stands for eliminate, minimize, integrate, parallelize, synchronize.
EMIPS stands for eliminate, minimize, integrate, parallelize, synchronize. The EMIPS method is a process improvement principle. It is implemented to undergo a structured assessment of processes or individual process steps with the goal of optimizing the approach of improvement itself.
Hancho
Read how a Hancho will support your organization as the first management level on the shop floor.
A Hancho is the first management level in a lean organization. A hancho is the technical manager or team leader (speaker - Japanese chô) in one part of the process or a small group (Japanese han) and typically consists of 6 to 10 employees. A Hancho masters all processes in his /her area, receives a slightly higher wage (5-10 %) than normal operators and is selected and appointed by the company. The hancho’s responsibilities include reacting to abnormalities and promoting standardized work and the process of continuous improvement.
In order to increase productivity the Hancho is the key player in his role as a team leader. Above the Hancho level your organization, depending on size, has the group leaders which are having a larger number of employees underneath them.
In order to implement the role of a Hancho you need define several aspects upfront. Just answer some questions to yourself:
How many Hanchos do we need?
What will be their daily tasks?
Which qualifications are a necessity?
Which employees are suitable for this role?
Does the employee have the right professional and social qualifications?
At Toyta e.g. the Hancho has following tasks:
You see that most of the time is used for problem solving and the dealing with absence. In best case the Hancho is dedicated to only this tasks, because he contributes the most for a successful continuous improvement management on the shop floor.
Heijunka
How to level production with the help of Heijunka.
Heijunka is a tool in the lean world that is striving for a leveled and smoothed dispatching of manufacturing demands which therefore leads to a reduction of waste. The meaning of levelling is to transform irregular incoming orders into uniform production batches. The target is to bring all demands on the smallest batch size possible based on a leveled production pattern. The Heijunka Board visualizes the predefined production plan for the production process. The beauty of it is that it enables you with little effort of control to implement a steady and synchronous flow of production.
If you are in a leading manufacturing position you already know how painful it can be to maintain a steady flow of work.
Customer demands are typically not perfectly leveled and this fluctuation needs to be translated into a defined takt that is given by your production process. To keep up with the incoming stream of orders and to avoid overproduction and therefore tied up cash, Heijunka can help you lowering the peaks and smoothing out production.
Heijunka is a well-known lean method for smoothing and reduce the over stressing of a production process. Heijunka is Japanese and means roughly translated levelling. The main reason for implementing Heijunka is a faster reaction time on fluctuating demands and improving the utilization of installed capacity.
With the help of Heijunka you minimize the sizes of batches to smallest size possible and start processing customer orders based on demand. This will support you on reducing your inventory as you will stop producing based on utilization of line capacity and then pile up finished goods without being sold.
At the bottom, Heijunka allows you to produce and deliver value to your customer at a steady pace and gives you the chance to react faster on deviations, while not overstressing the process. Therefore this method gives you always two options for levelling your production: By type or by quantity.
Balancing by type:
Go through your portfolio and define the average demand of each product. Based on the average demand the production is smoothed out to meet it. The target is to level the capacity of our line. Use Heijunka to keep up with the demands of each product of your portfolio and use it to visualize the production plan.
Balancing by quantity:
The main road blocker to establish a smooth and continuous production flow is producing in batches. The target is clear: produce only what is ordered. Therefore, Heijunka enables you to level your production by the average volume you get. By levelling your production this way, you will be able to achieve all demand by the end of the week. With the help of Heijunka you will keep your processes running without overburden it when unplanned peaks are coming in.
The Heijunka Box is a tool implemented on the shop floor in order to visualize the workload that needs to be fulfilled in order to meet the average demand. Simply spoken it has cards spread over the week for each product in a logical sequence to reach optimal flow.
The Heijunka Board
Usually the Heijunka box is set up in a matrix with the first column separated by product type for each line, the following columns are the workdays of the week. Therefore your Matrix defines Product type and the quantity that needs to be produced on a specific day. Two ways are most common, either as boxes where cards are placed in or as a board with magnetic cards that stick on it.
Depending on your installed capacity and the team size you want to cover with Heijunka you might need multiple Heijunka boards. Typically the cards you use are having the format of Kanban cards, that are following the process of the processed good until the end and then are placed back to the collection box for new planning.
Heijunka is a great lean method that allows you to organize your workflow around average customer demand. You protect your processes and employees from over stressing due to uneven production and quantity sizes. Furthermore, it supports you on realizing a complete pull system throughout production.
FiFo
FIFO is a warehousing-related principle. The parts that were stored first are picked first.
FIFO – First in First out
FiFo is a warehousing-related principle. The parts that were loaded in first are the once next in line to get picked.
Most commonly known as FiFo is that a shelf system is filled on one side with goods, which are later removed on the other side: The (strict) FiFo principle (First in - First out) works according to this method.
The FiFo storage principle is recommended when you have components of only one type in one line stored and it has to be ensured that the oldest loaded unit is set first so it will be always removed first. It is suitable for the optimized provision of goods in production and assembly and in industries in which the consideration of factors such as the best-before date of foodstuff is essential.
FiFo - First in First out
In accordance with the strict FiFo principle, the provision of the stored goods takes place purely under the aspect of access sequence, as it is automatically the case with a flow rack, without any further precautions being required. In the moderated FiFo principle, groups of loading units are considered to be the same (e.g. all articles with the same minimum best-before range) or criteria such as shorter withdrawal distances are used as a basis.
Voice of the customer
When talking about voice of the customer (VoC) we think about the customers’ expectations which are driving product development, services and improvement of daily business..
When talking about voice of the customer (VoC) we think about the customers’ expectations which are driving product development, services and improvement of daily business.
The VoC method is there to identify and transforming customer wishes, expressed or unspoken, into a quantified and structured customer requirement catalogue. It therefore is typically used at the beginning of new product definition, it pre-defines features and functions for the further development process.
Voice of the Customer
Also important for customer service, whenever customer service is needed. As an example for use cases think about sales process or even management process. But to simplify we talk about products.
VoC unfolds his full potential in the product definition phase in combination with Six Sigma. When Quality Function Deployment (QFD) is performed, VoC delivers valuable input.
VoC makes it possible to define the design of a product in the product development process in such a way that the customer’s expectations are fulfilled or even exceeded. The product definition starts with customer needs and not with technical product features (think about Timwood > Over Engineering). By keeping this in mind you will have a higher level of customer orientation.
A separate analysis of requirements and technical solutions will increase your flexibility on both sides, with VoC you are creating a comprehensive understanding of the market demands and the products you are offering.
When we have a look at highly innovative products VoC might not be the right choice > when the potential customers don’t know about > how can they have expectations. This gives you a large uncertainty using VoC.
So, what is the expected outcome of VoC > it will give you a complete, structured list of weighted and non-overlapping customer requirements that can be directly used for the product development process. One way to bring it in format is a so called VoC table.
This reading pick is awesome when you need a kick in the butt to turn outside-in. The focus is on the so called “reverse value chain”. Everything starts with customer wishes and based on those you develop innovative products or services.
No matter if you are a business student or manager and have to develop a company strategy, this book is just right. Not always easy to read but in summary it is all about connecting, converting and collaborating with your customers.
Read more in our reading picks here.
What needs to be done before:
You will need a defined customer target group! If you don’t know your target group or segment a VoC will never deliver meaningful results.
Before you start with a VoC Project a project team needs to be defined, it should include at the least the core product development team. In this way you will be able to bring in the knowledge of marketing, sales, product development and management, quality and production as well as other departments of your organization. If you want to go for the complete thing, think about even getting in key customers as a temporary team extension.
Like in most cases, a VoC Project-Team is a cross functional and cross departmental group of people. Therefore, you have to have a neutral moderator. It is the moderator’s job to ensure that these different interests do not lead to any falsification while collecting customer expectations and formulation towards requirements
Finally, as it will be a project, it needs management support. The Management has three main tasks:
Ensure that people involved are set free of other tasks to give their full resources to the project
To approve resources
Approve further development of the outcome of a VoC project
Bottleneck
Bottlenecks are the pacemaker of your process chain.
Bottlenecks in your process are the pacemakers of existing processes. These means if you tackle your bottlenecks in your process chain, it will have a direct impact on your cash flow.
A Bottleneck in a process chain requires the longest lead time of operations, A typical indicator for a bottleneck station is a upstream increased inventory or Work in Progress. The bottleneck is therefore the weakest link in the chain.
If you are running improvement or KAIZEN Workshops on your bottleneck station the upstream or downstream process steps will never be above 100% of performance. If so the bottleneck station changed to a different process step.
Bottlenecks are great to improve!
The potential of removing bottlenecks is unbelievable high, if you miss the chance to tackle the potential of bottlenecks in order to increase your throughput you are missing the chance to increase your performance and exceed customer demand/expectations. It is quite simple – the cost per hour of a bottleneck station can be seen as the loss of one hour of your complete process chain (e.g. production line) incl. the loss of parts not produced.
The whole deal is about increasing the throughput of your assembly line, to use machines efficiently combined with optimized operator working steps to increase the profitability of the assembly in total. Don’t make the mistake and focus only on the cost reduction part of it think and don’t be fooled by thinking in partial optimization.
To bring it to the point: In manufacturing, bottlenecks are continuously slowing down the whole assembly line. Focusing on permanent existing bottlenecks will sustainable improve the performance of the whole process chain and effect even other areas.
Cycle Time
In order-oriented production, the cycle time specifies the time from the start to the completion of the process steps.
Cycle Time = Takt Time > that upfront.
In order-oriented production, the cycle time specifies the time from the start of the first operation to the completion of the last operation for an order backlog.
Cycle time is the time your organization needs to carry out a work process, no matter what kind of process. For an optimum production cycle proper balancing needs to be done on both sides, the operators work and the machine cycles to meet the customer takt.
The period of time from the pickup of the work piece or process to be machined to the pickup of the next part. The pure machining time (added value) can differ from the cycle time, for example in the case of long paths or movements to pick up and transfer the individual work piece.
We will go in more detail on machine time and customer takt as well in upcoming articles.
Pareto Chart
A Pareto Chart is used to help determine the waste characteristics of a product.
A pareto chart is used in order to determine the waste characteristics of a product/good but also of processes. They are sorted onto a cart so that the most frequent defects can be visualized and stand at first place.
Today, I am writing this blog post after discussing several times with colleagues who want to understand the Pareto chart (or Pareto diagram) more deeply.
The Pareto chart is one of the basic tools of quality management. Usually, this chart consists of a combined bar and line graph. The vertical bars are representing the quantity of defects, and the line represents a cumulative percentage of the defects.
The descending order of bars is from left to right. The bar on the left will have the highest value, and the bar on the right side will have the lowest value.
Let’s discuss this in detail.
Pareto Chart
Sometimes, it is challenging for you to understand the problems and their causes. Instead of focusing on the root cause, you spend your time, solving problems, which were influencing the project least.
The Pareto diagram can help you overcome this situation. The Pareto diagram can help you segregate the defects and their cause. Once you get this info, you can focus on the cause which is generating the most defects.
The Pareto diagram is based on the Pareto Principle, which was developed by an Italian economist named Vilfredo Pareto. He found out that 80% of the wealth was spread to 20% of the population. Therefore, pareto is also known as the 80/20 rule.
We could now list several examples where this rule is confirmed such as
80% of the defects are coming from 20% of the process
or
80% of customer complaints are coming from 20% of all defects detected
or
20% of the defects are causing 80% of the problems…
The list can go on and on.
In general, this phenomenon can be interpreted as follows: Roughly 80% of the problems will be due to 20% of the causes, or the majority of issues will be due to a small number of causes.
However, keep in mind that the above rule is a general rule and the ratio is not absolute.
The Pareto chart is mainly used in quality management or Six Sigma approaches. This chart helps you to find the majority of the problems and their root causes. You then should focus on tackling those causes and therefor solve the majority of the problems.
How to Draw a Pareto Chart
Drawing a Pareto chart is very simple. The most important step is to collect the correct data.
The steps to drawing a Pareto chart are as follows:
Categorize your potential causes
Specify the measure, e.g. quantity, costs per failure, downtime, etc.
Set a time frame you measure, e.g. per shift, per week, etc.
Measure Measure Measure (If you can’t measure you can’t control)
Separate the data based on the categories
Draw a bar chart with causes on horizontal axis and number of occurrences on the vertical axis (Excel gives you predefined templates)
The category with the lowest quantity will be at the right and the highest quantity on the left
If you don’t have the histogram preset chart in excel - define a second row with the percentage value. Accumulated up to 100%. This will be your secondary axis. The values in percent will form the curve of distribution.
.To make it short - it should look like this:
Pareto Chart
Now, you can focus on the causes generating the majority of problems, analyze them, find their real root cause(s), and start to get rid of the issues one by one.
This chart can help everybody to identify causes of the most common problems. It also supports on prioritizing tasks and activities for KAIZEN Workshops or simply fire fighting. Having some Excel skills, it is very easy to create a Pareto and also often helpful communicating your actions to the upper management - you can bring it to the point.
This reading pick is not focusing on the professional approach of the Pareto (meaning quality matters in manufacturing) but more looking at the personal usage of the 80/20 Rule. We love it as it shows you how to focus on what really matters in live.
Read more in our reading picks here.
5S
The 5S Method is a five-level system for the provision of safety, cleanliness and orderliness on the workplace.
The 5S Method is a five-level system for the provision of safety, cleanliness and orderliness at the workplace. The term „5S“ is coming from 5 Japanese words that begin with the letter „S“.
These 5 words describe the 5 principles for the organization of the workplace:
1S – SEIRI
Cleaning: Sorting-out and get rid of all unwanted objects.
2S – SEITON
Orderliness: Clean-up and proper arrange tools needed.
3S – SEISO
Cleanliness: Maintain cleanliness at the workplace and keep the standards established through 5S workshops.
4S – SEIKETSU
Standardization: Establishing work standards developed by 5S sessions.
5S – SHITSU
Discipline: Observing compliance of new work standards and drive for continuous improvement.
Why do we need 5S?
Goals of the 5S during the implementation:
Safety
Flexibility
Quality
Costs
Ergonomics
How can you implement 5S at your organization?
How to implement 5S
The 5 steps of the 5S-Method:
Sorting out all unnecessary objects at your workplace
All needed objects have to be arranged in a proper way
Keep your workplace clean
Standardize the steps 1 to 3
Keep your new standard or improve it even more
5S is a continuous process!
The 5S checklist
In order to maintain the 5S procedure and standard you should be implementing a routine of a so called 5S audit. The 5S audit is an instrument of sustainable implementation of the five step system for safety, cleanliness and order at your workplace.
Therefore 5S is relevant in all areas of your company, no matter if you are working in a office or your focus is on the shop floor. To maintain the 5S implementation and the ongoing improvement of all 5 steps. The audit can support you on identifying deviation and to improve.
So why do you need the 5S Method?
It supports you on
Reduction of uncleanliness and its causes in the company
Reduction of latent waste in the company (e.g. untidiness, unneeded objects)
Reduction of defective equipment and tooling
Reduction of deviations from standardized manufacturing procedures due to unnecessary objects and frequent searches for misplaced objects
Increasing the awareness of the employees about tidiness, cleanliness, waste and deviations from standardized manufacturing procedures
Enhancing the positive impression of the company towards the customer
So what are the goals when you implement 5S in your company?
1 Increase safety at the workplace
Everything lies in its right place and employees receive a standardized and up-to-date description of their workplace
The employees know where to find everything needed in the case of an emergency
Markings on the floor are used as a visual control aid to help the employees to stay clear of any dangerous situations
2 Increased capability to react
Expeditious reaction to the requests of the customer and expediting the manufacturing process
By involving all employees, the internal flow of communication is enhanced along with the identification and removal of mistakes
It supports the expeditious preparation of e.g. work procedures, replacement of tools, increased flexibility of the employees, streamlines the work processes, increases the general economy by making the work procedures more effective; and expedites the continuous process of enhancement
Mistakes and deviations from the standardized work procedures become an exception and can be quickly eliminated
This reading pick will show you the methodology as well as real doing and conducting of 5S Sessions. It is a great guidance and a step by step instruction with lots of advice and practical tools that will allow you to conduct your 5S project from A-Z.
Read more in our reading picks here.
3 Enhanced quality
The proper arrangement of material and equipment decreases the amount of defective products and improves the repeatability of the work process
Enables the employees to determine at first glance what is needed to do to ensure quality
Makes the problems more perceivable and thus enables their solution
4 Cost reduction
Shortens unnecessary searches and reduces the time needed to find objects
Shortening time for exchange of tools > SMED
Creating new areas
Eliminating all unnecessary objects
Too excessive or insufficient supplies are discovered and are made visible
Expedient realization of counter-measures
5S designates the 5 basic principles for creating a clean, well-arranged and effective workplace with competent employees – the basis is orderliness = 5S.
5 Developing a “Visual Workplace”
In the case of a visually created workplace the work procedures are adjusted to enable all employees to have the possibility to observe the actual work process
Visualization:
Organization of the workplace
Manufacturing process
Distractions, such as defective objects, sources of danger etc.
Production indicators (plan, overproduction, or as the case may be, underproduction)
How can a 5S Audit support you?
The 5S Method makes sure that each workplace, in the production or office, is organized according to the principles of cleanliness, orderliness and safety
To secure the permanence and the continuity of adherence to the defined 5S standards it is necessary to regularly conduct 5S Audits
For the different areas of Production or Administration and others, specific questionnaires are prepared, on basis of which the obvious deviations from the defined planned state can be detected
The 5S questionnaires are combined with a list of counter-measures necessary to rectify the situation along with the names of responsible persons
Stay Connected
Ad
We want information fast and in a nutshell. We from OI recommend Blinkist* - because it’s simply the best.
* = Affiliate Link