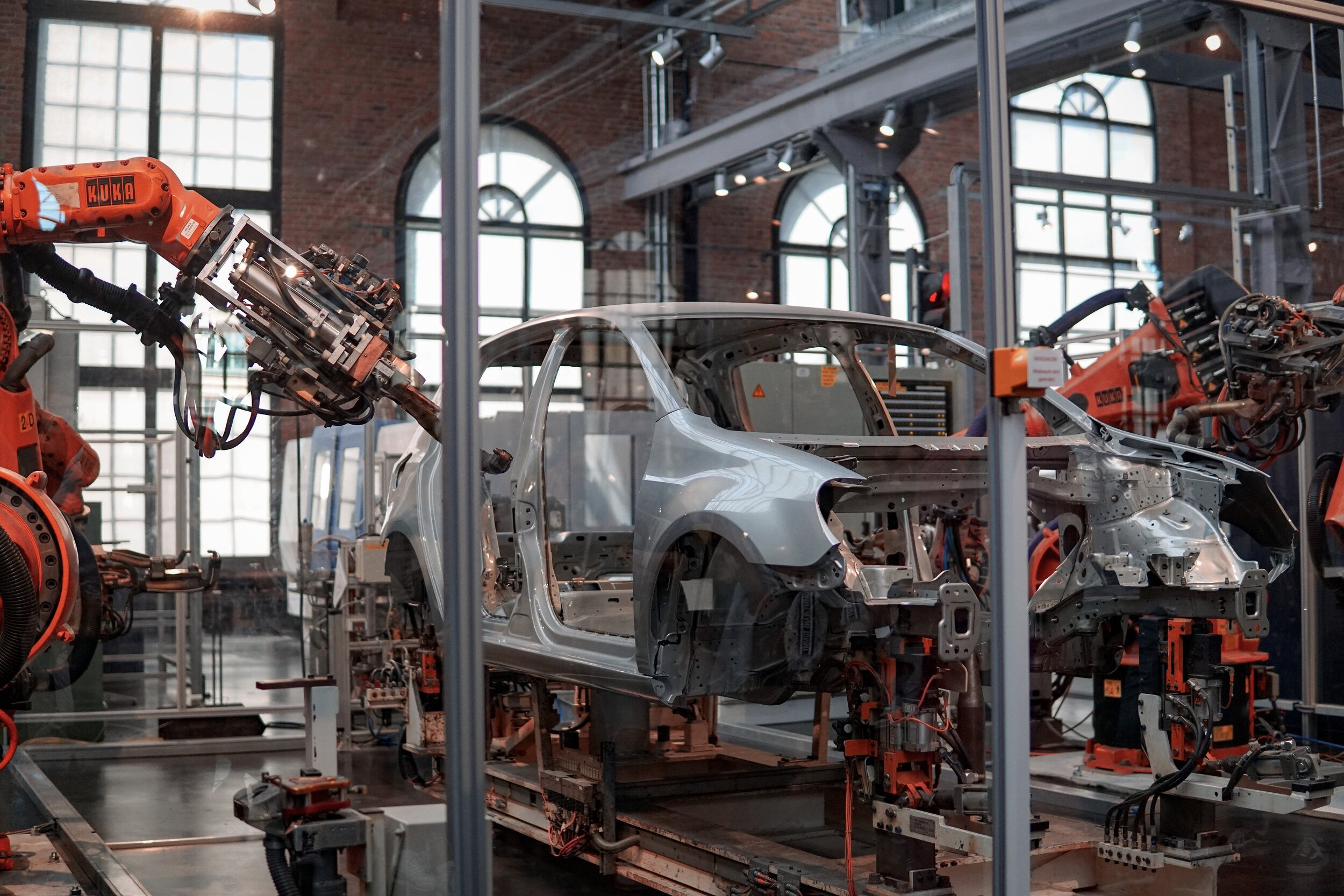
LANGUAGE OF LEAN
Makigami
With the help of a Makigami - administrative processes are recorded and redesigned.
The Japanese term Makigami is developed out of two. First the MAKI (yeah like the Sushi) meaning roll or rolled and KAMI meaning paper. Before you go wild, in the word combination you write kami with “g”. So the question that rises is: What you do with a rolled paper? You use the Makigami to draw and redesign administrative processes. Like with all Lean or Opex activities, once the process is visualized with the help of a Makigami “value-adding” and “non-value adding” activities are marked. On the bottom of the Makigami you will find a time axis which shows the operating time and the pure value adding time.
With the help of the Makigami process analysis, the process is always viewed from the perspective of the process itself, never from the perspective of the employees. This has to be clear also for the waste attack activities in the process. With the Mantra of OPEX: the central question that must be brutaly honest answered: Is the customer willing to pay for this process step/activity? Is this what you are doing adding value to the final product or service?
After you recorded the current state of your process you start to redesign it by asking yourself permanent the following question:
What should the ideal process look like?
Take your planned future development and corporate vision into account to make sure you are not running in the wrong direction.
Andon
Andon is a crucial part of visual management on the shop floor that gives a signal that indicates if and where there is a problem.
Andon is a crucial part for the visual management on the shop floor that gives a signal that indicates if and where there is a problem. Typically indicated with a traffic light signal red = failure mode, yellow = non-conforming performance and green = normal operation mode.
The methodology of Andon as part of the shop floor management, is to show the current operating status of a machine or a production line in a way that everyone can see and understand it immediately. As typically in Lean Terms Andon comes from the Japanese language and means paper lamp or just lamp.
Going along the Andon-Systematic there is to mention the Andon-Cords. The cords are used by operators to activate the lamps by either tear the cord or more likely nowadays pressing the corresponding buttons, which are attached above the production line and are easily accessible for the operators hanging downwards or as button attached at the work station.
If a non-conforming condition occurs, the yellow Andon signal initiates the support so that the problem that has occurred can be remedied immediately with additional supportive functions, such as maintenance. In worst case it is also possible to stop the complete production (red signal) until the problem has been solved or at least suitable countermeasures are in place.
An Andon has three main functions:
Visualization of the operating status of a machine/assembly line
Possibility for the operator to report an non-conforming condition and escalate it using a defined escalation process
Production or belt stop, so that no non-conforming products or components are passed on to the next process step
Old fashion Andon Board
The clear display of the operating states of several workstations was used quite early in the development of the Andon systems. The godfather of the TPS, Taiichi Ohno once described it as followed: "When one looks up, the andon (the line stop indication board) comes into view, showing the location and nature of trouble situations at a glance."
In the course of time, the Andon board has increasingly developed into an information board for all employees involved in the process. They display status information regarding the current situation in production, such as the number of units produced per day or per hour, the degree of delivery reliability to the customer or the cumulated amount of backlog. In this way, all process participants are aware of the current situation and can act accordingly.
Andon Boards nowadays
OCT
The Operator Cycle Time is the time an operator needs to fulfill a dedicated process step, including loading and unloading but excluding waiting time.
The Operator Cycle Time is the time an operator needs to fulfill a dedicated process step, including loading and unloading but excluding waiting time.
The Operator Cycle Time is measured from when the operator starts his/her process and is stopped when he/she is ready for the next workpiece (no matter if it’s there or not). Yes I said that the OCT is exclusive waiting time, but not exclusive the waiting time within the process itself. That means if the operator is waiting for a machine, he/she loaded, to finish the operation and unload the workpiece, this waiting time will be included in the OCT.
Most of the time OCT can be seen as the same as “cycle time”. The main difference comes from the waiting time an operator has, while a machine is running a process and the operator him-/herself would be ready for the next piece. This means in the end the OCT is always shorter as the CT. Going even further this means that the OCT can be shortened when installing a HANEDASHI device that autounloads the workpiece after the operation.
As with all lean management activities and targeted increase on productivity and flexibility time is on focus. But make sure to understand the process first, before running improvement actions you have to know what to improve.
Production Diary
The production diary, as part of the shop floor management system, defines a shift based weekly forecast incl. upcoming tasks for mgmt., supporting functions and is openly displayed on the shop floor.
With the help of a production diary, based on a pre-defined shift planning all other functions and outcomes are planned and tracked. This includes the mgmt. team as well as all supporting functions. In order that everyone is aware about the upcoming week the production diary is openly displayed on the shop floor. With the production diary and the pre-set structure of daily meetings of the shop floor mgmt. all daily activities are carried out. Best known part is e.g. Gemba Walks and the included problem solving activities e.g. A3 or just confirming that all processes run as planned.
With this big part of shop floor mgmt. it is clear that all regular meetings planned along the production diary are set. All other unplanned activities or extra meetings need to be conducted respecting the fixed schedule of the production diary.
SIPOC
SIPOC can be used to clearly define process steps within a process chain.
SIPOC is a > Six Sigma tool that summarizes an entire process at the start of an improvement project. SIPOC can be used to clearly identify process steps within a process chain. A SIPOC diagram is only a snapshot of a process. Each of the letters in SIPOC represent the names of the columns in the table:
S – Supplier, I – Inputs, P – Process, O – Output, C – Customer.
The SIPOC method has its origins in Six-Sigma and is used there in the definition phase of a project. To have it summarized see the following Infographic:
By applying this method, it is possible to quickly gain an overview of all the main elements of a process to be examined, even before more in-depth details are worked out.
SIPOC is a very simple and at the same time very effective method that can also be used in various situations in the lean management context.
Possible applications of a SIPOC can be:
Starting a KAIZEN workshop in order to create a common basic understanding.
To achieve a quick overview (top level) for subsequent process optimization
Simple type of documentation for existing processes
Identification of important process participants (who must attend the KAIZEN workshop)
Definition of the process steps to be investigated within a process chain
How to use SIPOC:
The SIPOC method can be used in many different forms, such as Excel spreadsheets, handwritten tables on flip charts or brownpaper versions using cards or post-it notes.
The easiest way is to start by listing the process steps. No more than 5-7 process steps should be listed, since the SIPOC method is not about carrying out a detailed process analysis, but only about gaining a rough overview.
It often makes sense to note down on the process card those departments or persons who carry out the process for the respective process steps, so that it can be recognized immediately who is responsible for the process.
Input: which input factors are necessary to perform the process step? This could be material, information, machines or a service.
Supplier: who provides these input factors? Do they come from an external supplier or from an internal supplier - perhaps as the output of a previous process step in the process chain?
Output: what is produced as a result in the respective process step. These can be material things such as components, assemblies or finished products, or intangible things such as processed information in the form of a document - e.g. a static calculation or an order confirmation.
Customer: for whom the result was actually produced. Make a distinction between external and internal customers. If no customer is found for the output size, it must be checked whether the process step makes sense at all.
Stay Connected
Ad
We want information fast and in a nutshell. We from OI recommend Blinkist* - because it’s simply the best.
* = Affiliate Link