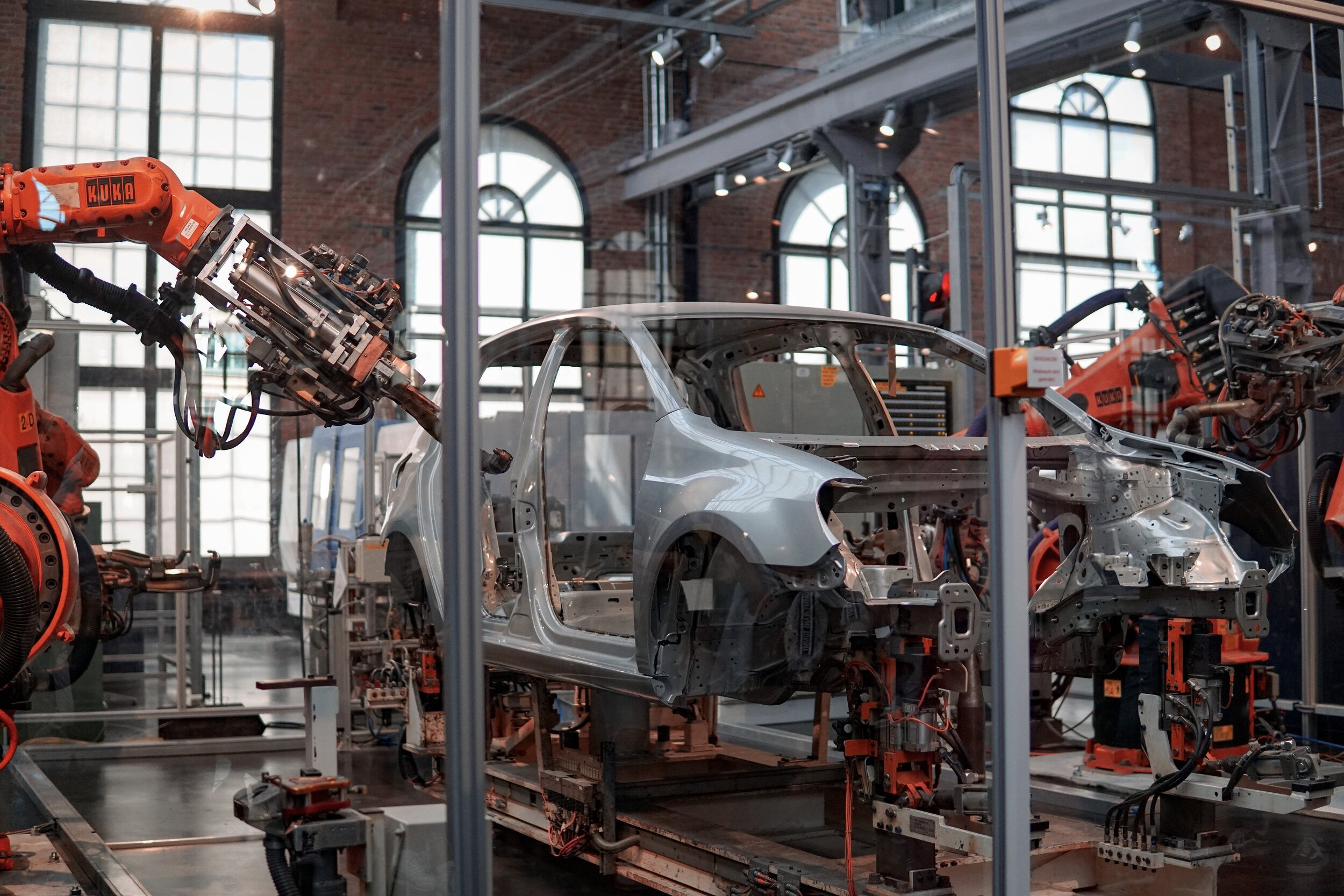
LANGUAGE OF LEAN
ABC Analysis
ABC Analysis is a method used in the manufacturing industry to categorize inventory based on its value and usage.
ABC Analysis is a method used in the manufacturing industry to categorize inventory based on its value and usage. The goal of this analysis is to prioritize items for better inventory management and streamline production processes.
In ABC Analysis, items are divided into three categories: A, B, and C. A items are the most valuable and frequently used, B items are less valuable but still used regularly, and C items are the least valuable and used infrequently. This categorization helps identify areas where improvements can be made to reduce inventory costs and increase efficiency.
To implement ABC Analysis, it is necessary to first gather data on the value and usage of each item in the inventory. This can be done by tracking the usage frequency, cost, and demand of each item. Once the data is collected, the items can be divided into the three categories based on their value and usage.
Once the items are categorized, the focus can be placed on the A items. These items should be closely managed and monitored to ensure they are always in stock and available for production. This may involve implementing a just-in-time (JIT) system for these items, which reduces the amount of inventory that needs to be kept on hand.
B items can also be managed, but to a lesser extent. These items may not be as critical to production, but they still need to be available when needed. Inventory levels for B items should be managed to minimize excess inventory, but not at the cost of stockouts.
C items are typically low-cost items that are not used frequently. The focus for these items should be on reducing the amount of inventory that is kept on hand. This can be done by reducing the order frequency or implementing a safety stock system to ensure that the item is available when needed.
In a nutshell, ABC Analysis is a simple and effective method to prioritize inventory and streamline production processes. By categorizing inventory based on its value and usage, it is possible to focus on the most important items and reduce the amount of inventory that is kept on hand. This leads to cost savings, increased efficiency, and improved production processes.
Just in Sequence - JIS
Just in Sequence (JIS) is a lean manufacturing principle that emphasizes the importance of delivering components to the production line at the exact moment they are needed.
Just in Sequence (JIS) is a lean manufacturing principle that emphasizes the importance of delivering components to the production line at the exact moment they are needed. The goal of JIS is to minimize waste and improve efficiency by avoiding overproduction and reducing the amount of inventory in the production process.
In traditional manufacturing processes, components are often delivered to the production line well in advance of when they are needed, leading to large amounts of inventory and unnecessary waste. With JIS, components are delivered to the production line just in time, reducing the amount of inventory and freeing up valuable storage space.
JIS also helps to minimize the risk of stock obsolescence, as inventory is not kept for long periods of time. In addition, JIS reduces the risk of quality problems and defects, as components are delivered only when they are needed and there is less chance for them to become damaged or lost.
Implementing JIS in a manufacturing facility requires a high level of coordination and communication between suppliers, manufacturers, and logistics providers. A just-in-sequence system should be carefully planned and implemented to ensure that components are delivered exactly when they are needed, without any delays or interruptions.
One of the key components of a successful JIS system is a strong logistics network that can ensure timely and accurate delivery of components. This may involve using advanced technologies such as real-time tracking and data analysis to monitor the delivery of components and identify potential issues before they become problems.
Another critical aspect of JIS is the need for clear and accurate communication between suppliers and manufacturers. This can include the use of automated systems and data sharing to ensure that all parties are aware of the status of deliveries and can take the necessary actions to resolve any issues.
In a nutshell, the Just in Sequence (JIS) principle is an important component of lean manufacturing, as it helps to minimize waste, reduce inventory, and improve efficiency. To fully realize the benefits of JIS, manufacturers must implement it as part of a comprehensive lean manufacturing program that includes strong logistics, clear communication, and the use of advanced technologies. With the right approach, JIS can help manufacturers to achieve significant improvements in their operations, leading to increased competitiveness and profitability.
Standardization
Standardization is a vital aspect of a successful lean management strategy and can be defined as the process of establishing and maintaining common procedures and processes throughout the manufacturing organization.
Standardization is a key principle in lean manufacturing, which is focused on maximizing efficiency, minimizing waste, and continuously improving processes. It is a vital aspect of a successful lean management strategy and can be defined as the process of establishing and maintaining common procedures and processes throughout the manufacturing organization. This principle is based on the idea that standardization leads to improved productivity and a higher level of consistency in the production process.
A lean manufacturing expert knows the importance of standardization, as it helps to reduce variation and streamline processes, resulting in increased efficiency and improved quality. This is because standardization helps to eliminate inefficiencies, errors, and inconsistencies in the production process, allowing employees to focus on the tasks that are most important. This in turn leads to improved cycle times, reduced lead times, and increased customer satisfaction.
Standardization also helps to eliminate confusion and misunderstandings, as all employees are following the same procedures and processes. This makes it easier for employees to work together, as everyone is working from the same set of guidelines. This also makes it easier for management to train new employees, as they can be taught the standard procedures from the outset.
Standardization also helps to facilitate continuous improvement. By standardizing processes, it is easier to identify areas where improvement is needed, and changes can be made more easily. This is because employees are all working from the same set of guidelines, making it easier to see where improvements can be made and implement changes.
In order to effectively implement standardization in manufacturing, a Lean Management Expert would typically follow three steps:
Process Mapping: The first step is to map out the processes and procedures used in the manufacturing organization. This helps to identify areas where standardization can be implemented, and where improvements can be made.
Standardization: The second step is to develop and implement standardized procedures and processes. This involves working with employees to ensure that everyone is following the same procedures, and that they are understood by all.
Continuous Improvement: The final step is to continuously monitor and improve the standardization process. This involves regularly reviewing the procedures and processes to identify areas for improvement, and making changes as necessary to ensure that the standardization process remains effective.
In a nutshell, standardization is a key principle in lean manufacturing, and is essential for maximizing efficiency, minimizing waste, and continuously improving processes. By following the three steps outlined above, a Lean Management Expert can effectively implement standardization in their organization, leading to improved productivity, higher levels of consistency, and increased customer satisfaction.
Bowling Chart
The bowling chart is a visual representation used in the manufacturing industry to track and monitor key performance indicators (KPIs)
The bowling chart is a visual representation used in the manufacturing industry to track and monitor key performance indicators (KPIs). Its origins can be traced back to the Toyota Production System, where it was used as a simple and effective tool to measure and improve the performance of the production line.
The basic concept of a bowling chart is to provide a visual representation of the performance of a particular KPI over time. The chart takes the form of a bowling pin, with each pin representing a performance target. The height of the pin corresponds to the actual performance achieved for that period, with higher pins indicating better performance.
One of the main benefits of using a bowling chart is that it provides a simple and intuitive way to track progress towards performance targets. The visual representation allows stakeholders to quickly understand the current state of the performance and identify areas where improvement is needed.
In the manufacturing industry, bowling charts are often used in combination with other KPIs to provide a comprehensive view of the performance of the production line. For example, a bowling chart could be used to track the number of defects produced in a particular production run, while another KPI might track the overall cycle time for the production line.
To get the most out of a bowling chart, it is important to ensure that the KPIs being tracked are relevant to the performance of the production line. This requires a clear understanding of the goals and objectives of the production process and the factors that influence performance.
Once the appropriate KPIs have been identified, the next step is to establish performance targets for each KPI. These targets should be based on historical data, industry benchmarks, and the overall goals and objectives of the production line.
Once the performance targets have been established, the bowling chart can be populated with data on a regular basis, such as weekly or monthly. This data can then be analyzed to identify areas where performance is exceeding expectations and areas where improvement is needed.
In conclusion, the bowling chart is a simple and effective tool for tracking and monitoring KPIs in the manufacturing industry. When used in combination with other KPIs and as part of a systematic approach to performance improvement, it can provide valuable insights into the performance of the production line and help drive continuous improvement.
Cardboard Engineering
Cardboard engineering, also known as corrugated cardboard engineering, is a concept that is gaining popularity in the world of manufacturing.
Cardboard engineering, also known as corrugated cardboard engineering, is a concept that is gaining popularity in the world of manufacturing. This approach is based on the use of cardboard mock-ups, prototypes, and models to visualize, test, and improve manufacturing processes and product design.
We would like to provide an overview of cardboard engineering and its application in a manufacturing setting.
Cardboard engineering is a low-cost, fast, and efficient method for testing and refining manufacturing processes and product design. The approach is based on the use of cardboard prototypes and models to simulate the manufacturing process and identify potential challenges and limitations. This allows manufacturers to quickly test and refine their processes and products without incurring the costs and delays associated with traditional prototyping methods.
The use of cardboard engineering has several benefits in a manufacturing setting. Some of these benefits include:
Low cost: Cardboard engineering is a low-cost method for testing and refining manufacturing processes and product design. This makes it accessible to a wide range of manufacturers, regardless of size or budget.
Fast: Cardboard engineering allows manufacturers to quickly test and refine their processes and products, reducing the time required to bring new products to market.
Improved design: By using cardboard prototypes and models, manufacturers can quickly identify potential challenges and limitations in their product design and make improvements accordingly.
Improved efficiency: Cardboard engineering helps manufacturers to optimize their processes and products, leading to improved efficiency and reduced waste.
Increased collaboration: The use of cardboard prototypes and models promotes collaboration and communication between departments, improving the overall efficiency of the manufacturing process.
In order to implement cardboard engineering in a manufacturing setting, it is important to follow a structured approach. This may include the following steps:
Identify the problem: Identify the challenges and limitations in the manufacturing process or product design that need to be addressed.
Create a cardboard prototype: Create a cardboard prototype or model that simulates the manufacturing process or product design.
Test and refine: Test the cardboard prototype or model and refine the process or product design as needed.
Implement changes: Implement any changes identified during the testing and refinement process.
Continuous improvement: Continuously monitor the manufacturing process and make improvements as needed to optimize efficiency and reduce waste.
In a nutshell, cardboard engineering is a valuable tool for manufacturers looking to improve their processes and products. By using cardboard prototypes and models, manufacturers can quickly test and refine their processes and products, leading to improved efficiency, reduced waste, and increased collaboration. By following a structured approach and continuously monitoring their processes, manufacturers can ensure that they are always working to improve their operations and products
Line Balancing
Line balancing is a critical component of lean manufacturing and is a key tool for improving efficiency, reducing waste, and increasing productivity.
Line balancing is a critical component of lean manufacturing and is a key tool for improving efficiency, reducing waste, and increasing productivity. The principle of line balancing is to ensure that every workstation on a production line is working at optimal capacity and that the overall line is balanced in terms of the workload and resources available.
We would like to provide an overview of the line balancing principle and its application in a manufacturing setting.
Line balancing is a process that involves analyzing the production line and determining the ideal workload for each workstation. This is done by breaking down the tasks involved in producing a product into individual steps, and then determining the time required to complete each step. Once this has been done, the steps are assigned to workstations, taking into account the workload and resources available.
The goal of line balancing is to ensure that each workstation is working at optimal capacity, with no workstation being overworked or underutilized. This results in a more efficient production line, with less waste and reduced lead times.
There are several benefits to line balancing in a manufacturing setting. Some of these benefits include:
Increased efficiency: Line balancing helps to ensure that each workstation is working at optimal capacity, which leads to increased efficiency and reduced waste.
Reduced lead times: By ensuring that each workstation is working efficiently, line balancing can help to reduce lead times and improve delivery times.
Improved quality: Line balancing helps to ensure that each workstation is working at the appropriate pace, which can help to improve quality and reduce the risk of defects.
Increased productivity: Line balancing helps to optimize the use of resources, which can lead to increased productivity and reduced costs.
Improved work environment: Line balancing helps to create a more balanced and less stressful work environment, which can improve employee morale and reduce turnover.
In order to implement line balancing in a manufacturing setting, it is important to follow a structured approach. This may include the following steps:
Define the production line: Define the production line and identify the workstations involved in the process.
Break down the process: Break down the process into individual steps and determine the time required to complete each step.
Assign tasks to workstations: Assign tasks to workstations based on the workload and resources available.
Monitor performance: Continuously monitor performance and make adjustments as necessary to ensure that the line is balanced and working at optimal capacity.
In a nutshell, line balancing is a key tool for improving efficiency and reducing waste in a manufacturing setting. By following a structured approach and continuously monitoring performance, manufacturers can ensure that their production lines are working at optimal capacity, leading to improved efficiency, reduced lead times, and increased productivity.
Overproduction
Overproduction is one of the seven kinds of wastes in the Lean Manufacturing methodology and refers to the production of goods in excess of what is immediately required by the customer. Operations Insider - connecting the dots.
Overproduction is one of the seven kinds of wastes in the Lean Manufacturing methodology and refers to the production of goods in excess of what is immediately required by the customer. This type of waste can have a significant impact on the efficiency and profitability of a manufacturing operation, and as a Lean Management Expert, I would like to provide an overview of the negative effects of overproduction.
One of the main negative effects of overproduction is increased inventory costs. When a manufacturer produces more goods than are immediately required by the customer, the excess inventory takes up valuable space in the warehouse and incurs additional costs for storage and handling. This inventory also ties up capital that could be used elsewhere in the business, reducing the overall financial performance of the company.
Another negative effect of overproduction is increased lead time. When a manufacturer produces goods in excess of what is immediately required, the production line may become congested, leading to delays and increased lead time. This can negatively impact customer satisfaction and reduce the competitiveness of the manufacturer.
Overproduction can also lead to increased defects and decreased quality. When a manufacturer produces more goods than are immediately required, the pressure to maintain production speed and volume can lead to shortcuts being taken and decreased attention to detail. This can result in an increase in defects and a decrease in overall product quality, leading to customer complaints and reduced customer loyalty.
Finally, overproduction can contribute to a lack of flexibility and responsiveness. When a manufacturer produces more goods than are immediately required, they may not be able to respond quickly to changes in customer demand, leading to increased lead time and decreased customer satisfaction. This can also result in increased costs due to the need to adjust production processes and manage excess inventory.
In a nutshell, overproduction is a significant waste in the manufacturing process and can have a negative impact on efficiency, profitability, and customer satisfaction. By focusing on reducing overproduction and improving production processes, manufacturers can increase their competitiveness and improve their overall performance. We recommend that manufacturers continuously monitor their production processes and work to reduce overproduction and improve the overall efficiency of their operations
Process Chain
The manufacturing industry is a complex system of processes, with each stage relying on the success of the previous one to achieve the final product.
The manufacturing industry is a complex system of processes, with each stage relying on the success of the previous one to achieve the final product. The process chain is the backbone of this system, connecting each stage together to ensure a seamless flow of goods and services.
To achieve the highest level of efficiency in the production process, it is important to understand the process chain and how it serves the production processes. This includes identifying the inputs, outputs, and key activities of each stage, as well as the flow of goods, services, and information throughout the chain.
One of the first steps in optimizing the process chain is to establish clear and standardized procedures for each stage. This includes defining the roles and responsibilities of each team member, as well as establishing a clear communication plan to ensure that everyone is aware of the status of each stage.
Another important factor in optimizing the process chain is to reduce waste and increase efficiency. This can be achieved through continuous improvement efforts, such as streamlining processes, reducing inventory, and minimizing lead times. Lean tools, such as value stream mapping, can be used to identify areas of waste and opportunities for improvement.
Additionally, investing in new technology and equipment can also help to improve the process chain. Automation and digitalization of the production process can lead to faster and more accurate production, as well as reduced labor costs and increased productivity.
Furthermore, involving employees in the continuous improvement process is crucial in achieving the best results. Encouraging their input and ideas can lead to new solutions and creative thinking that can drive process improvement. Employee training and development programs can also help to enhance the skills and knowledge of the workforce, leading to increased efficiency and effectiveness.
Another important aspect of the process chain is supplier selection and management. Careful selection of suppliers can ensure that high-quality inputs are used in the production process, reducing the likelihood of defects and increasing efficiency. Effective supplier management can also ensure timely delivery of goods and services, reducing lead times and minimizing the impact of supply chain disruptions.
In a nutshell, the process chain is a critical component of the manufacturing industry, serving as the foundation for the production processes. By establishing clear procedures, reducing waste and increasing efficiency, investing in new technology, involving employees, and carefully selecting and managing suppliers, manufacturers can optimize the process chain and achieve operational excellence
Pacemaker
"Pacemaker" is a term commonly used in the manufacturing industry to describe a production process that sets the pace for the rest of the production line. Sometimes also considered as bottleneck station.
"Pacemaker" is a term commonly used in the manufacturing industry to describe a production process that sets the pace for the rest of the production line. A pacemaker process is the one that determines the speed and flow of the entire production process, and therefore has a significant impact on the efficiency and productivity of the manufacturing operation. As a Lean Management Expert, it is important to understand the role and significance of a pacemaker in manufacturing, and how to effectively implement this principle for maximum efficiency and profitability.
The concept of a pacemaker process has its roots in the Toyota Production System (TPS), which is the foundation of the Lean Manufacturing philosophy. TPS emphasizes the importance of flow and standardization in manufacturing, and the pacemaker process is a key component in achieving these goals. The pacemaker process is the first step in the production line and sets the standard for the rest of the processes to follow. This means that the pace, efficiency, and quality of the pacemaker process have a direct impact on the entire production line.
In order to effectively implement the pacemaker principle, it is important to carefully select the appropriate process to serve as the pacemaker. This process should be stable, consistent, and capable of producing high-quality products in a timely manner. It is also important to standardize the pacemaker process to ensure that it runs smoothly and consistently, and that the production line can respond to changes in demand or other factors.
Once the pacemaker process has been established, it is important to monitor and measure its performance regularly. This can be done through the use of Key Performance Indicators (KPIs), such as cycle time, quality rate, and productivity. By monitoring these KPIs, it is possible to identify areas for improvement and to make changes to the pacemaker process or the rest of the production line to improve overall efficiency.
In addition to setting the pace for the production line, a pacemaker process can also have a positive impact on the morale of the manufacturing workforce. When employees see that their efforts are making a significant impact on the overall efficiency and success of the operation, they are more likely to be motivated and engaged in their work.
In a nutshell, the pacemaker principle is a key component of the Lean Manufacturing philosophy, and a valuable tool for Lean Management Experts looking to improve the efficiency and profitability of their manufacturing operations. By carefully selecting the pacemaker process, standardizing its performance, monitoring its performance regularly, and using KPIs to track progress, it is possible to achieve maximum efficiency and profitability in the manufacturing industry.
Building Information Modeling (BIM)
Building Information Modeling (BIM) is a method to optimally plan, develop and manage buildings using software.
Building Information Modeling (BIM) is a process of creating digital representations of physical and functional characteristics of buildings and structures. It has been widely adopted in the construction industry and has been found to be extremely effective in streamlining the construction process. This principle of BIM is not just limited to construction and has been successfully implemented in the manufacturing industry as well. A Lean Management Expert will tell you that the principles of BIM can be applied to the manufacturing industry in a number of ways to create a more efficient and effective production process.
One of the key benefits of BIM in manufacturing is that it allows for a more accurate and detailed representation of the manufacturing process. This helps to identify bottlenecks, potential inefficiencies and other areas that may be hindering production. By creating a detailed digital representation of the production process, manufacturers can better understand the flow of materials, resources and labor. This leads to more informed decisions regarding production planning and scheduling, as well as more accurate forecasting of production costs.
Another benefit of BIM in manufacturing is that it enables more effective collaboration between different departments and functions within a company. By having a centralized platform where all stakeholders can access and update information, teams can work together more effectively and avoid any potential miscommunication or misunderstandings. This increased collaboration leads to better decision-making, improved project management and more efficient use of resources.
A Lean Management Expert will tell you that the implementation of BIM in manufacturing is a three-step process. The first step is to create a digital representation of the production process. This includes creating a detailed model of all equipment, machinery, facilities and processes. This model can be used to identify areas where improvements can be made, as well as areas that may be hindering production.
The second step is to use the digital representation to optimize the production process. This involves using the model to evaluate different production scenarios and identify the most efficient and effective approach. This includes the use of data analysis, simulations and other tools to help identify areas for improvement.
The final step is to implement the improvements identified in the second step. This can include changes to the production process, the introduction of new equipment and machinery, and other initiatives aimed at streamlining the production process.
In a nutshell, the implementation of BIM in the manufacturing industry can bring numerous benefits to organizations. By creating a detailed digital representation of the production process, manufacturers can better understand their operations and identify areas for improvement. This leads to a more efficient production process, improved collaboration between departments and functions, and more informed decision-making. A Lean Management Expert will tell you that the principles of BIM can be a valuable tool in helping organizations achieve their operational excellence goals.
Zero Defects
Zero Defects, also known as "Zero Quality Control" or "ZQC," is a quality improvement philosophy that seeks to eliminate defects in the production process.
In other projects we have witnessed the significant impact that Zero Defects programs can have on a manufacturing organization. Zero Defects, also known as "Zero Quality Control" or "ZQC," is a quality improvement philosophy that seeks to eliminate defects in the production process. This philosophy has its roots in the Total Quality Management (TQM) movement and has been widely adopted by many manufacturing organizations.
The Zero Defects philosophy is based on the belief that quality should be built into every product, from start to finish. The goal is to eliminate defects and ensure that products are produced to the highest standard, meeting or exceeding customer expectations. This approach to quality focuses on the entire production process, from raw materials to finished goods, and encourages all employees to be actively involved in the quest for zero defects.
One of the key benefits of a Zero Defects program is that it helps to create a culture of continuous improvement. Employees are encouraged to identify areas where defects are occurring, and to work together to eliminate these issues. This creates a sense of ownership and engagement among employees, which in turn drives improved performance and results.
Another key benefit of Zero Defects is that it reduces the costs associated with rework and product defects. Defects in the production process can lead to increased costs, such as scrap, waste, and retooling. By reducing or eliminating these costs, organizations can improve their bottom line and remain competitive in their industry.
The key to success with Zero Defects is to have a well-defined process in place. This process should start with defining the standards for each product and then identifying the critical-to-quality characteristics that must be met. From there, a detailed process map should be created that outlines the steps involved in the production process, from raw materials to finished goods. This process map should also identify the potential sources of defects and highlight the steps that need to be taken to eliminate these defects.
Once the process map is in place, the next step is to implement the Zero Defects program. This involves training employees on the Zero Defects philosophy, as well as the process map and the critical-to-quality characteristics. It is also important to provide employees with the necessary tools and resources to identify and eliminate defects. This may include things like checklists, forms, and software programs.
In addition to training and tools, it is also important to have a robust feedback and continuous improvement process in place. This can include regular quality audits, customer feedback, and employee suggestion programs. The goal of these programs is to identify areas where defects are occurring, and to work together to eliminate these issues.
Finally, it is important to track progress and measure success. This can be done by tracking key performance indicators (KPIs), such as the number of defects, scrap rates, and customer satisfaction levels. By tracking these KPIs, organizations can determine whether their Zero Defects program is having a positive impact and make adjustments as needed.
In conclusion, Zero Defects is a powerful tool for organizations looking to improve the quality of their products and processes. By eliminating defects, organizations can improve customer satisfaction, reduce costs, and remain competitive in their industry. The key to success with Zero Defects is to have a well-defined process in place, and to actively involve employees in the quest for zero defects. By doing so, organizations can achieve operational excellence and realize their full potential.
Six Sigma
Six Sigma is a highly structured and data-driven methodology used in the manufacturing industry to improve quality and efficiency. Six Sigma offers a powerful toolset to help organizations achieve operational excellence and continuous improvement.
Six Sigma is a highly structured and data-driven methodology used in the manufacturing industry to improve quality and efficiency. Six Sigma offers a powerful toolset to help organizations achieve operational excellence and continuous improvement.
The primary goal of Six Sigma is to eliminate defects and minimize variability in processes, leading to improved customer satisfaction, reduced costs, and increased profitability. This is achieved through a combination of data analysis, statistical methods, and team-based problem-solving.
One of the key elements of Six Sigma is the DMAIC process, which stands for Define, Measure, Analyze, Improve, and Control. This process provides a systematic approach to solving problems and improving processes, starting with a clear definition of the problem, followed by the collection and analysis of data, and ending with the implementation of sustainable solutions.
Another key aspect of Six Sigma is the use of statistical tools and techniques to measure and improve process performance. This includes process mapping, hypothesis testing, design of experiments, and control charts, among others. Six Sigma also relies on a highly-skilled workforce, with individuals trained in statistical analysis and problem-solving techniques.
One of the key benefits of Six Sigma is its ability to drive continuous improvement. This is achieved through regular monitoring and measurement of processes, coupled with ongoing analysis and improvement efforts. Six Sigma provides organizations with a roadmap for sustained, data-driven improvement, helping to ensure that performance gains are maintained over the long-term.
In a nutshell, Six Sigma is a powerful tool in the arsenal of any Lean Management Expert. It provides organizations with a systematic approach to improving quality and efficiency, while also driving continuous improvement and driving long-term success. Whether you are looking to optimize a specific process, or seeking to drive broader organizational change, Six Sigma provides the methodology and tools to help you achieve your goals.
Regular Communication
Regular communication refers to the continuous exchange of information between different departments and individuals within an organization.
Regular communication refers to the continuous exchange of information between different departments and individuals within an organization. The aim of this communication is to ensure that everyone is on the same page, working towards the same goals, and that any problems or obstacles are addressed promptly. In this article, we will explore the positives aspects of using regular communication in manufacturing and how it supports shop floor management in three steps.
Improves Collaboration and Cooperation
Regular communication plays an important role in improving collaboration and cooperation within an organization. When everyone is kept informed about the latest developments, it becomes easier for employees to work together effectively. They can share ideas and best practices, identify areas for improvement, and help each other overcome challenges. As a result, teamwork becomes more efficient, and everyone is able to contribute to the success of the organization.
Facilitates Problem Solving
Problems and obstacles are a natural part of any manufacturing process. However, if they are not addressed promptly, they can quickly escalate into bigger issues. Regular communication helps to ensure that problems are identified and addressed in a timely manner. When employees are able to openly communicate with each other, they can work together to find solutions and prevent problems from getting worse. This helps to minimize the impact of any issues on production and ensures that the organization is able to maintain its competitiveness.
Supports Shop Floor Management
Regular communication is also an important aspect of shop floor management. Shop floor management refers to the process of managing the day-to-day operations of a manufacturing facility. Regular communication helps to ensure that everyone is aware of their responsibilities and is able to perform their duties effectively. It also helps to identify areas for improvement and makes it easier for managers to provide feedback and guidance. In addition, regular communication helps to create a culture of continuous improvement, where everyone is encouraged to take an active role in driving progress and improving performance.
In a nutshell, regular communication is a crucial aspect of Lean management in manufacturing. It plays an important role in improving collaboration and cooperation, facilitating problem solving, and supporting shop floor management. By incorporating regular communication into their operations, organizations can ensure that everyone is working together effectively, that problems are addressed promptly, and that the organization is able to maintain its competitiveness.
Change Over
Change overs refer to the process of switching a production line from producing one product to producing another.
Change overs refer to the process of switching a production line from producing one product to producing another. This process can have a significant impact on the efficiency and profitability of a manufacturing operation, and as a Lean Management Expert, I would like to provide an overview of change overs and how they can be improved with SMED (Single Minute Exchange of Dies) Workshops.
One of the main challenges with change overs is the time it takes to complete the process. In many cases, change overs can take several hours or even days, which can result in decreased production and increased costs. This can be a significant issue for manufacturers who need to be able to switch between products quickly and efficiently to meet customer demand.
Another challenge with change overs is the potential for mistakes and errors during the process. When a production line is being changed over, there is an increased risk of mistakes being made, such as incorrect parts being installed or procedures being skipped. This can result in decreased production quality, increased defects, and increased lead time.
In order to improve change overs, manufacturers can implement SMED Workshops. SMED Workshops are designed to streamline the change over process and reduce the time it takes to switch between products. This is achieved by identifying and eliminating non-value-added activities, such as time spent waiting for equipment to cool down or procedures that can be done in parallel. By eliminating these activities, SMED Workshops can significantly reduce the time it takes to complete change overs, allowing manufacturers to increase production efficiency and responsiveness.
SMED Workshops also help to reduce the potential for mistakes and errors during change overs by standardizing the process and reducing the number of activities that need to be performed. This can improve overall production quality, reduce defects, and increase customer satisfaction.
In nutshell, change overs can have a significant impact on the efficiency and profitability of a manufacturing operation. By implementing SMED Workshops, manufacturers can streamline the change over process, reduce the time it takes to switch between products, and improve production quality and customer satisfaction. As a Lean Management Expert, I recommend that manufacturers consider implementing SMED Workshops as a means of improving their overall production efficiency and competitiveness.
Audit
Audits are a critical component of any lean manufacturing program, as they provide a structured and systematic approach for evaluating the effectiveness of the processes and procedures in place.
Audits are a critical component of any lean manufacturing program, as they provide a structured and systematic approach for evaluating the effectiveness of the processes and procedures in place. Audits help to identify areas for improvement, track progress, and ensure that best practices are being followed.
We would like to outline the 5 steps in order to prepare and conduct a successful audit in a manufacturing setting. These steps are as follows:
Define the audit scope: Determine what areas of the manufacturing process will be evaluated during the audit. This may include areas such as production line processes, inventory management, and quality control procedures.
Gather data: Collect relevant data and information that will be used during the audit. This may include data on production volumes, inventory levels, and quality control data.
Prepare audit checklists: Develop a detailed set of checklists that will be used to evaluate the different areas of the manufacturing process. These checklists should be comprehensive and include questions about process flow, standard operating procedures, and key performance indicators.
Conduct the audit: Conduct the audit using the checklists developed in step 3. This should be done by a team of experts who have a thorough understanding of the manufacturing process and best practices.
Analyze the results: After the audit is complete, analyze the results to identify areas for improvement. This may include the development of action plans to address any areas of weakness or non-compliance.
In order to ensure a successful audit, it is important to follow a set of best practices. Here are 10 tips for a successful audit in a manufacturing setting:
Be well-prepared: Ensure that you have a thorough understanding of the manufacturing process and the areas that will be evaluated during the audit.
Use a team approach: Conduct the audit as a team to ensure that all areas are thoroughly evaluated and that all perspectives are taken into account.
Follow a structured approach: Use a structured approach and follow the audit checklists developed in step 3 to ensure a consistent and systematic evaluation of the manufacturing process.
Be objective: Maintain objectivity throughout the audit and avoid making assumptions about the manufacturing process or the results.
Focus on best practices: Evaluate the manufacturing process against best practices and ensure that these are being followed.
Be open-minded: Be open-minded and willing to consider alternative approaches and new ideas for improvement.
Be transparent: Be transparent about the audit process and the results, and communicate openly with all stakeholders.
Follow-up on action plans: Ensure that action plans are developed to address any areas of weakness or non-compliance identified during the audit.
Continuously monitor progress: Continuously monitor progress and track progress against the action plans to ensure that improvements are being made.
Encourage continuous improvement: Encourage continuous improvement and encourage all stakeholders to be involved in the audit process and to contribute to the improvement of the manufacturing process.
In a nutshell, audits are an essential component of a successful lean manufacturing program. By following the 5 steps and the 10 tips outlined above, manufacturers can ensure that they are conducting effective and successful audits that lead to continuous improvement and enhanced competitiveness.
Annual Objectives
The use of annual objectives with 3 to 5 years breakthrough objectives is a crucial aspect of policy development in an organization.
The use of annual objectives with 3 to 5 years breakthrough objectives is a crucial aspect of policy development in an organization. This approach to setting goals allows an organization to balance both short-term and long-term objectives, ensuring that progress is being made towards both immediate and ultimate goals. In this article, an operational excellence expert will discuss the importance of this approach and the steps organizations can take to implement it effectively.
The first step in setting annual objectives with 3 to 5 years breakthrough objectives is to define the long-term vision of the organization. This vision should reflect the organization's ultimate goals and should be ambitious yet achievable. It should also align with the organization's mission and values, as well as the larger goals of the industry or sector in which it operates.
Once the long-term vision has been defined, the organization can begin setting its annual objectives. These objectives should be specific, measurable, achievable, relevant, and time-bound (SMART). They should also align with the long-term vision of the organization. For example, if the long-term vision is to become the leader in a particular market, an annual objective might be to increase market share by a certain percentage each year.
The next step is to set the 3 to 5 years breakthrough objectives. These objectives should be significant milestones that are critical to achieving the long-term vision. They should also be challenging, yet achievable, and should align with the annual objectives. For example, if the long-term vision is to become the leader in a particular market, a 3 to 5 years breakthrough objective might be to become the market leader in a particular geographic region.
Once the objectives have been set, the organization can develop a policy to support their achievement. This policy should include specific strategies and initiatives that will help the organization achieve its objectives. For example, the policy might include initiatives to improve product quality, increase customer satisfaction, reduce costs, or increase market share.
In order to effectively implement the policy, the organization must allocate resources appropriately. This includes allocating both financial and human resources, as well as the time and energy of key stakeholders. The organization must also establish a process for monitoring progress towards the objectives and for making adjustments as needed.
The use of annual objectives with 3 to 5 years breakthrough objectives can be a powerful tool for organizations that are seeking to improve their performance and achieve their goals. However, it is important to remember that this approach requires a significant investment of time and resources, as well as a commitment to ongoing improvement. Organizations that are willing to make this investment will be well-positioned to achieve their goals and create a bright future for themselves and their stakeholders.
In a nutshell, the use of annual objectives with 3 to 5 years breakthrough objectives is a crucial aspect of policy development in an organization. It allows organizations to balance both short-term and long-term objectives, ensuring that progress is being made towards both immediate and ultimate goals. By following the steps outlined in this article, organizations can effectively implement this approach and achieve their goals.
Cell Production
Cell Production focuses on optimizing the flow of work and improving efficiency in manufacturing and operations.
Cell Production focuses on optimizing the flow of work and improving efficiency in manufacturing and operations. It is based on the concept of organizing work into cells, which are self-contained units responsible for performing a specific set of tasks. The goal of cell production is to minimize waste, increase flexibility, and improve overall performance.
The origins of cell production can be traced back to the 1950s and 60s, when Toyota and other Japanese companies were experimenting with new approaches to manufacturing. Over time, the concept of cell production has evolved and been refined, and today it is widely used in a variety of industries, including automotive, electronics, and consumer goods.
In order to implement cell production effectively, there are several key steps that organizations must take. Firstly, it is important to conduct a thorough analysis of the current state of the manufacturing or operations process, in order to identify areas where improvements can be made. This may involve mapping out the flow of work and identifying bottlenecks or other inefficiencies.
Once these areas have been identified, the next step is to reorganize the work into cells, taking into account the specific requirements of each cell and the skills and expertise of the employees who will be working in them. This may involve rearranging physical work spaces, or changing the way that work is assigned and managed.
It is also important to establish clear communication and feedback mechanisms, so that employees and teams can work together effectively. This may involve setting up regular meetings to discuss performance, or implementing systems for tracking and reporting on key metrics.
In order to ensure a successful implementation of cell production, it is also important to provide training and support for employees. This may involve providing training on the new processes and procedures, or offering coaching and mentoring to help employees develop the skills and knowledge they need to be effective.
Another key aspect of cell production is continuous improvement. This involves regularly reviewing performance and making adjustments as needed, in order to optimize efficiency and reduce waste. This may involve experimenting with different approaches, such as implementing new technologies or streamlining processes, in order to find the best solutions.
In conclusion, cell production is a powerful methodology for optimizing performance in operations and manufacturing. By reorganizing work into cells, minimizing waste, and continuously improving performance, organizations can increase efficiency, reduce costs, and improve overall performance. In order to be successful, organizations must take a structured and systematic approach, and be committed to ongoing improvement.
TPM - Total Productive Maintenance
Total Productive Maintenance (TPM) is a maintenance strategy that involves involving all employees in the maintenance process to maximize equipment productivity and minimize downtime.
Total Productive Maintenance (TPM) is a methodology that originated in Japan in the 1970s and has since become a widely recognized and adopted approach to operational excellence in manufacturing and other operations-focused industries. It is a comprehensive approach that seeks to optimize the performance of equipment and processes through a focus on maintaining and improving reliability and efficiency.
The origins of TPM can be traced back to the Japanese auto industry, where manufacturers were seeking ways to increase productivity and competitiveness in the face of increasing global competition. TPM emerged as a response to the need for a more proactive and integrated approach to equipment maintenance, with the goal of improving both productivity and overall equipment effectiveness (OEE).
Over time, TPM has evolved and expanded to encompass a wider range of objectives and activities. Today, it is widely regarded as a best-practice approach to operational excellence, and is widely used in many different industries, including manufacturing, healthcare, and government operations.
One of the key features of TPM is its focus on involving all employees in the maintenance and improvement process. This is achieved through the creation of cross-functional teams and the use of a range of techniques, including root cause analysis, standardization, and continuous improvement.
Another key aspect of TPM is its focus on data-driven decision-making and performance measurement. This involves the collection and analysis of data on equipment and process performance, which is then used to identify areas for improvement and to drive continuous improvement efforts.
When properly implemented, TPM can have a significant impact on organizational performance and competitiveness. This can include improvements in equipment reliability, increased productivity, reduced waste, and improved overall equipment effectiveness (OEE).
To achieve these benefits, it is important to implement TPM in a structured and systematic way, with clear goals and objectives and a strong focus on continuous improvement. This typically involves a multi-phased approach, starting with an assessment of existing processes and equipment, followed by the development of a comprehensive improvement plan and the implementation of specific improvement initiatives.
In a nutshell, TPM is a proven methodology that can help organizations achieve operational excellence by optimizing the performance of their equipment and processes. To achieve success, organizations must approach TPM in a systematic and structured way, with clear goals and objectives, and a strong focus on continuous improvement.
Key points for a successful TPM implementation:
Involve all employees in the process
Focus on data-driven decision-making
Adopt a multi-phased approach
Prioritize continuous improvement
Develop a comprehensive improvement plan.
Cellularization
Cellularization is a lean manufacturing methodology that aims to optimize the flow of materials, information, and people within a manufacturing or production environment.
Cellularization is a lean manufacturing methodology that aims to optimize the flow of materials, information, and people within a manufacturing or production environment. Its goal is to create a more efficient, flexible, and responsive production system that can quickly adapt to changing customer demands and market conditions.
The origin of cellularization can be traced back to the early days of the Toyota Production System (TPS), which was developed in the 1950s and 60s. TPS was based on the principles of Just-In-Time (JIT) production and was designed to reduce waste, improve quality, and increase productivity. The concept of cellularization emerged as a way to create small, self-contained production cells that were optimized for specific product families or types of work.
The core idea behind cellularization is to create a flow of work that is highly synchronized and integrated, with minimal inventory and waste. This is achieved by organizing the production environment into cells that are designed to handle specific product families or product types. Each cell is equipped with the necessary tools, equipment, and materials to complete the work in a continuous flow, without the need for batch processing or work-in-progress storage.
Cellularization also requires a cross-functional team approach, where workers from different areas of the organization come together to work on a specific product family or type of work. This team-based approach helps to ensure that everyone has a clear understanding of the work, and it encourages collaboration and communication between different departments.
One of the key benefits of cellularization is that it enables organizations to respond quickly to changes in customer demand and market conditions. For example, if a new product is introduced, the production cell for that product can be quickly reconfigured to accommodate the new work. This agility is a critical advantage in today's fast-paced and highly competitive market.
Another benefit of cellularization is that it promotes continuous improvement. The small, self-contained nature of the cells allows for close observation and monitoring of the work, which in turn enables quick and effective identification and elimination of waste. The cross-functional teams are also empowered to identify and implement improvements that can be made to the production process.
To effectively implement cellularization, organizations need to carefully consider the following factors:
Work flow design: The first step in implementing cellularization is to carefully design the work flow to ensure that it is optimized for the specific product family or type of work being performed.
Equipment selection: The right tools and equipment are critical to the success of cellularization. Organizations need to carefully select the tools and equipment that will be used in each cell, and ensure that they are properly maintained and calibrated.
Cross-functional teams: Teams of workers from different departments must be assembled to work together in each cell. These teams need to be trained on the new work processes, and encouraged to collaborate and communicate effectively.
Lean leadership: Leaders at all levels of the organization need to embrace the principles of lean manufacturing and support the implementation of cellularization. This includes providing the resources, training, and coaching that teams need to succeed.
In a nutshell, cellularization is a powerful and effective methodology for optimizing the flow of materials, information, and people within a manufacturing or production environment. Its success depends on careful design of the work flow, selection of the right tools and equipment, and the development of cross-functional teams. With the right leadership and support, cellularization can help organizations to achieve greater efficiency, flexibility, and responsiveness, and to remain competitive in today's fast-paced and dynamic market
MTM
MTM (Methods Time Measurement) is a systematic method for analyzing and optimizing work processes that is widely used in the field of Lean Management.
MTM (Methods Time Measurement) is a systematic method for analyzing and optimizing work processes that is widely used in the field of Lean Management. MTM is based on the idea of breaking down work into small, easily analyzed and optimized tasks, and is therefore an important tool for improving efficiency and productivity in operations.
The origin of MTM can be traced back to the early 20th century, when industrial engineers in Europe and the United States first began to develop time-and-motion studies. These early studies sought to identify the most efficient ways to perform tasks and reduce waste in manufacturing operations. Over time, MTM evolved into a standardized methodology, with clear guidelines and tools for process analysis and improvement.
One of the key features of MTM is its focus on standardizing work processes. This is accomplished by breaking down each task into its component parts and then determining the most efficient way to perform each part. The result of this analysis is a set of standardized work methods that can be used to train workers and ensure consistency in operations.
Another important aspect of MTM is its focus on continuous improvement. The MTM methodology includes regular reviews of work processes and the use of data and analysis to identify areas for improvement. This approach helps organizations to continuously improve their operations and remain competitive over time.
One of the best ways to utilize MTM is in the context of Lean management. In Lean, the focus is on identifying and eliminating waste in all aspects of operations. By applying the MTM methodology to work processes, organizations can identify inefficiencies and then work to eliminate them. This helps to create a more streamlined, efficient, and productive work environment.
Another important application of MTM is in the context of training and development. By using MTM to analyze and standardize work processes, organizations can provide clear and consistent training to workers. This helps to ensure that all workers are performing their tasks in the most efficient way, which leads to improved productivity and reduced waste.
Finally, MTM can also be used in the context of project management. By analyzing work processes in advance of a project, organizations can ensure that they have the resources and capabilities needed to complete the project on time and within budget.
In a nutshell, MTM is a powerful tool for improving efficiency and productivity in operations. Its focus on standardizing work processes and its emphasis on continuous improvement make it an ideal methodology for Lean management and for organizations looking to improve their operations over time.
Stay Connected
Ad
We want information fast and in a nutshell. We from OI recommend Blinkist* - because it’s simply the best.
* = Affiliate Link