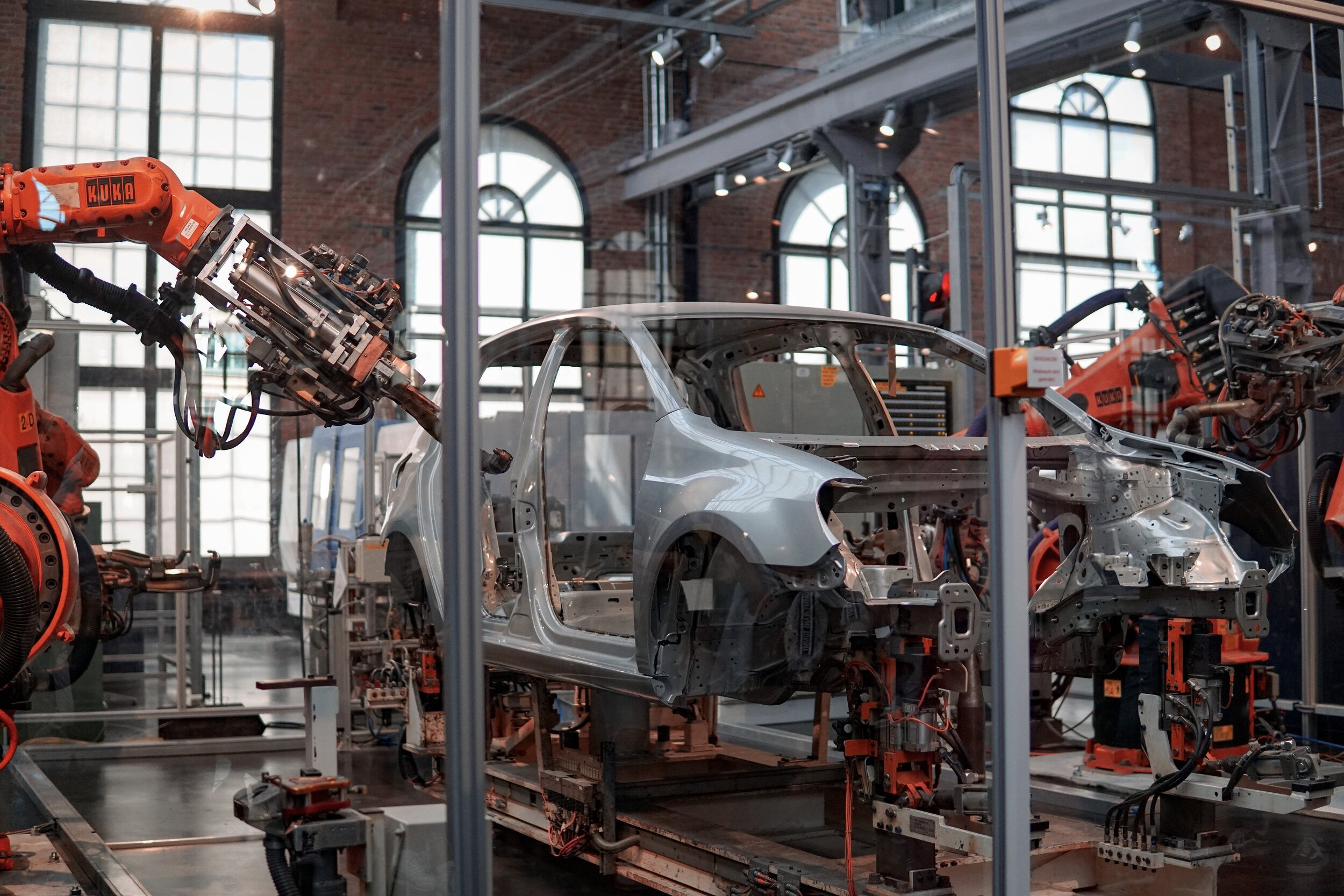
LANGUAGE OF LEAN
Point Of Use
Point of Use (POU) is a key component of Lean initiatives aimed at reducing waste, increasing efficiency, and improving overall production processes.
Point of Use (POU) is a key component of Lean initiatives aimed at reducing waste, increasing efficiency, and improving overall production processes. It is a philosophy that focuses on delivering materials, tools, and equipment directly to the worker at the moment they need them. The goal of POU is to minimize unnecessary movement, handling, and storage of materials, which not only streamlines production but also reduces the risk of damage, loss, and obsolescence.
In traditional manufacturing processes, raw materials and supplies are often stored in central locations, such as inventory rooms, and are retrieved and moved to the production line as needed. This can result in excess inventory, increased lead times, and the need for multiple trips to retrieve materials. Additionally, workers may spend significant amounts of time searching for the tools or materials they need, which reduces productivity and increases the risk of mistakes.
Point of Use aims to eliminate these inefficiencies by bringing materials and supplies directly to the worker at the point of need. This reduces the need for workers to search for materials and increases the speed and accuracy of the production process. POU also reduces the amount of inventory that needs to be stored and managed, which helps to reduce the risk of damage, loss, and obsolescence.
There are several different approaches to implementing POU, each with its own set of benefits and challenges. One approach is to use kanban systems, which are visual signals that tell workers when it’s time to replenish materials or supplies. Another approach is to use automated systems, such as conveyors or robots, which move materials and supplies directly to the production line as needed.
Regardless of the approach used, POU requires careful planning and coordination between all departments involved in the production process. It also requires regular monitoring and adjustments to ensure that the system is working as intended. This can include tracking key performance indicators (KPIs) such as inventory levels, production lead times, and worker productivity.
One of the benefits of POU is that it helps to improve worker morale and job satisfaction. When workers have access to the materials and supplies they need exactly when they need them, they are able to focus on their work without worrying about finding the right tools or supplies. Additionally, POU helps to eliminate the frustration that workers may feel when they are unable to find the materials they need, which can lead to decreased job satisfaction and even burnout.
Another benefit of POU is that it helps to reduce the risk of mistakes and increase quality. When workers have everything they need at their fingertips, they are able to focus on their work without worrying about searching for materials or supplies. This reduces the risk of errors, which in turn helps to improve overall quality and reduce the need for rework.
In a nutshell, Point of Use is an important concept in Lean Manufacturing that aims to reduce waste, increase efficiency, and improve overall production processes. By bringing materials and supplies directly to the worker at the point of need, POU streamlines production, reduces the risk of damage, loss, and obsolescence, and improves worker morale and job satisfaction. To be successful, POU requires careful planning, coordination, and monitoring, as well as a focus on continuous improvement. By implementing POU and other Lean principles, manufacturers can reduce costs, increase efficiency, and improve overall production outcomes.
Cell Production
Cell Production focuses on optimizing the flow of work and improving efficiency in manufacturing and operations.
Cell Production focuses on optimizing the flow of work and improving efficiency in manufacturing and operations. It is based on the concept of organizing work into cells, which are self-contained units responsible for performing a specific set of tasks. The goal of cell production is to minimize waste, increase flexibility, and improve overall performance.
The origins of cell production can be traced back to the 1950s and 60s, when Toyota and other Japanese companies were experimenting with new approaches to manufacturing. Over time, the concept of cell production has evolved and been refined, and today it is widely used in a variety of industries, including automotive, electronics, and consumer goods.
In order to implement cell production effectively, there are several key steps that organizations must take. Firstly, it is important to conduct a thorough analysis of the current state of the manufacturing or operations process, in order to identify areas where improvements can be made. This may involve mapping out the flow of work and identifying bottlenecks or other inefficiencies.
Once these areas have been identified, the next step is to reorganize the work into cells, taking into account the specific requirements of each cell and the skills and expertise of the employees who will be working in them. This may involve rearranging physical work spaces, or changing the way that work is assigned and managed.
It is also important to establish clear communication and feedback mechanisms, so that employees and teams can work together effectively. This may involve setting up regular meetings to discuss performance, or implementing systems for tracking and reporting on key metrics.
In order to ensure a successful implementation of cell production, it is also important to provide training and support for employees. This may involve providing training on the new processes and procedures, or offering coaching and mentoring to help employees develop the skills and knowledge they need to be effective.
Another key aspect of cell production is continuous improvement. This involves regularly reviewing performance and making adjustments as needed, in order to optimize efficiency and reduce waste. This may involve experimenting with different approaches, such as implementing new technologies or streamlining processes, in order to find the best solutions.
In conclusion, cell production is a powerful methodology for optimizing performance in operations and manufacturing. By reorganizing work into cells, minimizing waste, and continuously improving performance, organizations can increase efficiency, reduce costs, and improve overall performance. In order to be successful, organizations must take a structured and systematic approach, and be committed to ongoing improvement.
Cellularization
Cellularization is a lean manufacturing methodology that aims to optimize the flow of materials, information, and people within a manufacturing or production environment.
Cellularization is a lean manufacturing methodology that aims to optimize the flow of materials, information, and people within a manufacturing or production environment. Its goal is to create a more efficient, flexible, and responsive production system that can quickly adapt to changing customer demands and market conditions.
The origin of cellularization can be traced back to the early days of the Toyota Production System (TPS), which was developed in the 1950s and 60s. TPS was based on the principles of Just-In-Time (JIT) production and was designed to reduce waste, improve quality, and increase productivity. The concept of cellularization emerged as a way to create small, self-contained production cells that were optimized for specific product families or types of work.
The core idea behind cellularization is to create a flow of work that is highly synchronized and integrated, with minimal inventory and waste. This is achieved by organizing the production environment into cells that are designed to handle specific product families or product types. Each cell is equipped with the necessary tools, equipment, and materials to complete the work in a continuous flow, without the need for batch processing or work-in-progress storage.
Cellularization also requires a cross-functional team approach, where workers from different areas of the organization come together to work on a specific product family or type of work. This team-based approach helps to ensure that everyone has a clear understanding of the work, and it encourages collaboration and communication between different departments.
One of the key benefits of cellularization is that it enables organizations to respond quickly to changes in customer demand and market conditions. For example, if a new product is introduced, the production cell for that product can be quickly reconfigured to accommodate the new work. This agility is a critical advantage in today's fast-paced and highly competitive market.
Another benefit of cellularization is that it promotes continuous improvement. The small, self-contained nature of the cells allows for close observation and monitoring of the work, which in turn enables quick and effective identification and elimination of waste. The cross-functional teams are also empowered to identify and implement improvements that can be made to the production process.
To effectively implement cellularization, organizations need to carefully consider the following factors:
Work flow design: The first step in implementing cellularization is to carefully design the work flow to ensure that it is optimized for the specific product family or type of work being performed.
Equipment selection: The right tools and equipment are critical to the success of cellularization. Organizations need to carefully select the tools and equipment that will be used in each cell, and ensure that they are properly maintained and calibrated.
Cross-functional teams: Teams of workers from different departments must be assembled to work together in each cell. These teams need to be trained on the new work processes, and encouraged to collaborate and communicate effectively.
Lean leadership: Leaders at all levels of the organization need to embrace the principles of lean manufacturing and support the implementation of cellularization. This includes providing the resources, training, and coaching that teams need to succeed.
In a nutshell, cellularization is a powerful and effective methodology for optimizing the flow of materials, information, and people within a manufacturing or production environment. Its success depends on careful design of the work flow, selection of the right tools and equipment, and the development of cross-functional teams. With the right leadership and support, cellularization can help organizations to achieve greater efficiency, flexibility, and responsiveness, and to remain competitive in today's fast-paced and dynamic market
MTM
MTM (Methods Time Measurement) is a systematic method for analyzing and optimizing work processes that is widely used in the field of Lean Management.
MTM (Methods Time Measurement) is a systematic method for analyzing and optimizing work processes that is widely used in the field of Lean Management. MTM is based on the idea of breaking down work into small, easily analyzed and optimized tasks, and is therefore an important tool for improving efficiency and productivity in operations.
The origin of MTM can be traced back to the early 20th century, when industrial engineers in Europe and the United States first began to develop time-and-motion studies. These early studies sought to identify the most efficient ways to perform tasks and reduce waste in manufacturing operations. Over time, MTM evolved into a standardized methodology, with clear guidelines and tools for process analysis and improvement.
One of the key features of MTM is its focus on standardizing work processes. This is accomplished by breaking down each task into its component parts and then determining the most efficient way to perform each part. The result of this analysis is a set of standardized work methods that can be used to train workers and ensure consistency in operations.
Another important aspect of MTM is its focus on continuous improvement. The MTM methodology includes regular reviews of work processes and the use of data and analysis to identify areas for improvement. This approach helps organizations to continuously improve their operations and remain competitive over time.
One of the best ways to utilize MTM is in the context of Lean management. In Lean, the focus is on identifying and eliminating waste in all aspects of operations. By applying the MTM methodology to work processes, organizations can identify inefficiencies and then work to eliminate them. This helps to create a more streamlined, efficient, and productive work environment.
Another important application of MTM is in the context of training and development. By using MTM to analyze and standardize work processes, organizations can provide clear and consistent training to workers. This helps to ensure that all workers are performing their tasks in the most efficient way, which leads to improved productivity and reduced waste.
Finally, MTM can also be used in the context of project management. By analyzing work processes in advance of a project, organizations can ensure that they have the resources and capabilities needed to complete the project on time and within budget.
In a nutshell, MTM is a powerful tool for improving efficiency and productivity in operations. Its focus on standardizing work processes and its emphasis on continuous improvement make it an ideal methodology for Lean management and for organizations looking to improve their operations over time.
Ergonomic Workplace
A work place that takes into consideration most of the ergonomic aspects such as the operator’s height, range and reach.
An ergonomic workplace is a work system that considers the ergonomic aspects of an operation and the operator such as the operator’s hight, range and reach with the goal that the operator does not need to bend or turn.
The ergonomic workplace goes hand in hand with the work improvement.
Definition and purpose
Reveal waste increasing cost and not adding value.
Find waste in the movement of workers, eliminate/improve, pursue net work adding value.
Worker Movement
Lean Manufacturing and Ergonomics may have different roots and directions but together they can complement each other and define a more efficient and safer workplace.
One of the best person known for focusing on productivity and efficiency in manufacturing processes was Henry Ford with the invention of the modern assembly line. Ford really was focusing on eliminating waste and to cut down unnecessary costs in relation to the manufacturing of his cars.
Toyota is one of the best known companies that has stretched to the maximum the idea of Lean Manufacturing and is now holding the pole position when it comes to the reputation according the elimination of “waste”.
By looking at the Lean Model as well as Work Ergonomics, you clearly see the necessity of both practices in the industrial workplace, as well as observe that both can complement each other.
The 7 types of waste to eliminate include:
Transport
Inventory
Motion/Movement
Waiting
Overproduction
Overprocessing
Defects
The list of TIMWOOD is what Toyota has defined as the seven major types of wastes or non-value-adding activities. The seven wastes do not add any value to the product and the customer in the end is not willing to pay for it. Therefore it is essential to remove as much waste as possible which will have also an effect on the ergonomic workplace and furthermore on the health of the operators.
Some of these things like transport, waiting or unnecessary movement can be reduced to a limit what the operator still needs because as human being the operator is limited by his body.
The Lean Manufacturing initiatives and workplace ergonomics stepped into the manufacturing world at different times and therefore are not fully integrated. But you are perfectly advised by combining the principles of Workplace Ergonomics with Lean Manufacturing initiatives. Through a cooperative assessment and teamwork you have the chance to complement each other in making the workplace more efficient and a safer place.
Stay Connected
Ad
We want information fast and in a nutshell. We from OI recommend Blinkist* - because it’s simply the best.
* = Affiliate Link