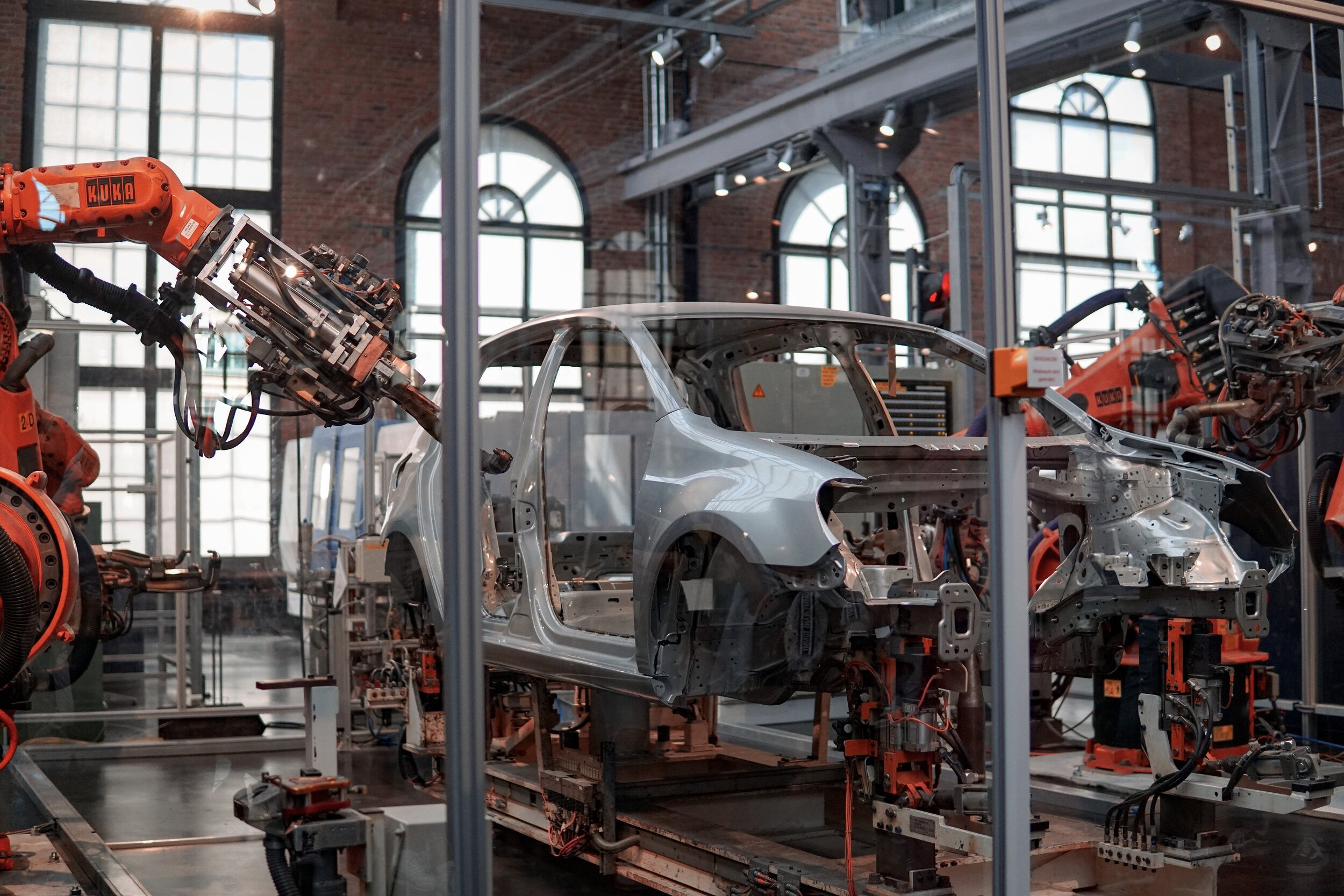
LANGUAGE OF LEAN
Production Smoothing (Heijunka)
Production smoothing, also known as Heijunka, is a key aspect of modern operations management. It refers to the leveling of production to match customer demand, while maximizing efficiency and minimizing waste.
Production smoothing, also known as Heijunka, is a key aspect of modern operations management. It refers to the leveling of production to match customer demand, while maximizing efficiency and minimizing waste. This technique has been proven to be an effective way to manage production processes and increase competitiveness in the marketplace.
The objective of production smoothing is to create a steady flow of products and services, reducing the variability and fluctuations in the production process. This helps to minimize the waste and resources associated with overproduction, excess inventory, and bottlenecks in the production line. By leveling production, companies can better predict customer demand and adjust their production processes accordingly.
One of the primary benefits of production smoothing is the reduction of waste in the production process. By leveling production, it minimizes the need for excess inventory and eliminates the waste associated with overproduction. This helps to minimize the costs associated with storage, handling, and transportation of excess inventory, while improving overall efficiency.
Another advantage of production smoothing is the improvement of customer satisfaction. By better predicting and matching customer demand, companies can ensure that they have the right products and services available at the right time. This helps to build stronger relationships with customers and improves the overall perception of the company.
To implement production smoothing, companies must first understand their customer demand patterns and the production processes that support them. This requires a thorough analysis of the production line, including the identification of bottlenecks and areas of waste. The company should then develop a production plan that balances customer demand with the production processes to create a steady flow of goods and services.
The company should also implement effective communication and collaboration between all departments, including sales, marketing, engineering, and production. This helps to ensure that all processes are aligned and working together towards the common goal of production smoothing. The company should also consider the use of technology and equipment to automate the production process and improve efficiency.
It is also important to engage employees in the production smoothing process. By involving employees in the implementation and ongoing management of production smoothing, companies can tap into their expertise and insights, and build a culture of continuous improvement. Employees should also receive training and development opportunities to enhance their skills and knowledge in production smoothing techniques.
In a nutshell, production smoothing is an effective way to manage production processes and increase competitiveness in the marketplace. By reducing waste, improving customer satisfaction, and engaging employees, companies can create a steady flow of goods and services, and improve their overall production efficiency. By embracing this technique, companies can achieve operational excellence and maintain their competitive edge in the marketplace.
Inventory
Inventory is often viewed as a necessary evil, as it provides a safety net to ensure that products are available to meet customer demand.
Inventory is often viewed as a necessary evil, as it provides a safety net to ensure that products are available to meet customer demand. However, from the perspective of Lean Management, inventory can also be seen as a type of waste.
In Lean, waste is defined as anything that does not add value to the customer. From this perspective, inventory can be considered waste because it ties up valuable resources such as space, money, and time without providing any immediate value to the customer. This is because inventory requires storage, which takes up valuable space, and also requires investment in the products themselves. In addition, inventory can lead to obsolescence, as products may become outdated or go out of fashion before they can be sold. Furthermore, inventory can lead to inefficiencies in the supply chain, as products may sit on shelves for extended periods of time before they are sold, adding unnecessary time to the overall lead time.
Despite these challenges, inventory is also an essential component of most businesses. Inventory provides a safety net, ensuring that there are products available to meet customer demand even when there are disruptions in the supply chain. It also allows businesses to take advantage of bulk purchasing discounts, and to manage seasonal variations in demand.
So, how can Lean Management help businesses to steer inventory in the best direction? There are several key steps that can be taken to minimize the waste associated with inventory while still ensuring that the business has the products it needs to meet customer demand.
The first step is to implement a Lean production system. This involves using the principles of Lean Management to streamline production processes and reduce waste in all areas of the business, including inventory management. By reducing waste in the production process, it is possible to minimize the amount of inventory that is required, freeing up valuable resources for other areas of the business.
The second step is to implement a pull-based production system. This involves using customer demand as the driving force behind production, rather than using forecasted demand to determine production schedules. This can help to minimize inventory waste by ensuring that products are only produced when there is a genuine demand for them.
The third step is to implement just-in-time (JIT) inventory management. JIT is a Lean approach to inventory management that involves only ordering the products that are required to meet customer demand, and no more. This can help to minimize inventory waste by reducing the amount of product that is held in reserve, freeing up valuable resources such as space and money.
The fourth step is to implement a continuous improvement program. This involves regularly reviewing inventory levels and processes, and making changes where necessary to reduce waste and increase efficiency. This can help to ensure that inventory management processes are constantly evolving, and that the business is always adapting to changing customer demand.
In a nutshell, inventory management is an important aspect of any business, as it helps to ensure that the right products are available at the right time to meet customer demand. However, from the perspective of Lean Management, inventory can also be seen as a type of waste. By implementing a Lean production system, a pull-based production system, JIT inventory management, and a continuous improvement program, businesses can minimize the waste associated with inventory while still ensuring that they have the products they need to meet customer demand. By adopting these principles, businesses can increase efficiency, reduce costs, and improve overall customer satisfaction.
Kanban
The material in the Kanban System is exclusively oriented to the consumption of your production process.
In this article we want to talk about another classic from Lean Management Kanban or the so called Pull System.
The word Kanban itself has its roots in the Chinese Japanese language and means card, label or sticker. In industrial manufacturing planning systems or general in logistics control Kanban describes a replenishment system for consumed parts according to the amount used steered by cards that give the signal following the Pull Principle.
The material in the Kanban System is exclusively oriented to the consumption of your production process. The cards are a key element of this kind of control system and provide proper information transfer. Kanban control loops from the work station of flexible production control and serves to smooth material flow through your inbound or even outbound logistics. In addition Kanban serves you to implement a sustainable reduction of material stocks, increases the ability to deliver and saves you pure cash.
In an ideal world Kanban would control your entire value chain from the supplier to the end customer. In this way you would have installed an complete smooth supply chain with almost no chance of interruption and massive stocks. And now comes the but – to steer production with Kanban – a continuous monitoring is required for a smooth material supply. To make it short: it requires discipline from all involved parties along the supply chain.
Lets have a look to the development of Kanban.
The first Kanban System was developed by none other than Taiici Ohno (of course) at Toyota Motor in the 1940s. One of the main reasons for the implementation of Kanban was the low productivity and efficiency of Toyota compared to western competitors. With the Kanban System, Toyota achieved a significant change towards flexible and efficient production control that had a massive impact on productions output while at the same time reducing the costs for inventory in raw material, work in progress (WIP) and finished goods.
To give the complete picture it wasn’t implementing the Kanban system itself to drive the success of Toyota, there are other key factors that together where making the difference. Just to name Just in time as an example of key elements of the Toyota Production System. It is and always will be a combination of different methods and philosophy that brings you forward.
In the 1970s the Kanban Concept was adapted in the industry in the USA and Germany. As they haven’t known better, they pretty much copied the complete Toyota Production System (TPS) in order to get the principles running.
Pull or Kanban System
Either way you call it, the material flow is controlled by boxes or cards. Kanban Cards serving in a simple way all information needed to identify what parts are needed in what quantity at what place. The amount typically is defined by the replenishment time at the work station. With the so called two box principle you make sure that the operator never runs short on components. Nowadays there are also digital version of it called eKanban, but the principle behind is the same. The trigger of supply is the Kanban Card starting of the pull chain of material.
To use Kanban efficient, it is not suitable for all parts. Kanban is perfect for small parts with a small amount of variants and a consistent demand. For this reason, you’ll see Kanban Systems in the industry mostly used for C-Parts management. The rest of the components are steered with the support of MRP. Only in rare cases you find that even the supply of big components are controlled with the Kanban methodology.
One nice side effect with Kanban, you can set up the way you can steer your bottleneck. That means, when you have done a proper value stream analysis you know the capacity for your bottleneck and will only order what this process step can handle.
Milkrun
The Milkrun is the preset intralogistics concept to bring raw material, semi finished and finished goods to the place they belong at the time they are needed.
The Milkrun is the preset intralogistics concept to bring raw material, semi finished and finished goods to the place they belong at the time they are needed. The Mikrun is implemented based on existing consumption values, an internal supply cycle is defined in which deliveries on fixed routes are installed with specific times.
Based on these current consumption values, a logistic supply cycle is defined wherein raw material, semi and finished goods are delivered and picked up by a fixed route at a specific time. With this you will also optimize your intralogistics concept in general taking on action for a Milkrun concept.
So what is the idea behind the Milkrun concept.
The term Milkrun comes from the traditional milkman that was supplying milk to homes on a fixed route in a specific time. The milk delivery was based on the consumption of the households, by this only the amount of milk needed was delivered. Empty bottles have been picked up at the same time and brought back to the distribution center. So quite simple full bottle(s) delivered, empty bottle(s) picked up.
The cross company Milkrun
Nowadays the material management got a little bit more complex. Speaking in the external way of logistics a Milkrun is a supplier concept where customers ask for one or more shipping companies to manage different suppliers or customers on after the other in the form of a shipping cycle. In this way, goods and empty containers can be delivered and received at the same time without the need of centralization. The main goal is to have as less as possible empty trucks and at the same time being under full control of external material flow. Tours and deadlines are the guard rails on these cycles, reducing storage space is the nice to have side effect.
The benefits of the Milkrun concept
With installing a Milkrun you will be able to reduce shipping times, processing processes and therefore handling costs.
Just in Time and Just in Sequence deliveries are possible
Your planning is more structured as you will have fixed time frames
Less capital needed due to decreasing inventory/stock/WIP
You can integrate waste and empty container management
Increase of sustainability due to ecologically smarter transportation routes
Of course there are also some challenges with the Milkrun concept
Time consuming planning as quantity, duration, replenishment time, etc. needs to be considered
Processes and products need constant supply
Outbound Milkruns can be delayed by traffic or weather conditions
Economically relevant for larger business or higher demands of goods
Reliable supplier for products and transport needed
One last note for the internal Milkrun
Inbound the concept can be used in both ways, intralogistics and manufacturing. E.g. certain raw materials or semi-finished goods can be delivered on a regular basis to predefined workstations where the consumption can simply calculated. And on the fixed route the Mizusumashi can collect empty container and waste from production. This reduces internal ways of operators and guarantees a continuous supply of workstations. The next level would be to interlink all workstations or cells with your internal supply cycles to create an intralogistics flow, reducing the manual replenishment work. To find out what the Mizusumashi is just go here. In short: he/she is the guy who supllies goods on the shop floor in a structured process.
Supermarket
In the language of Lean the term supermarket describes a ways of an independent production control.
When speaking of a supermarket in lean context we are talking about an independent instrument that is used to control production. In a supermarket raw material and pre-commissioned components can be found in defined areas. The amount is well organized according the replenishment times of each component, in general the inventory is limited and components are refilled as soon as they are used. Following the Pull Principle with the help of the Kanban-System.
Concerning the supermarket we see it as one of the pull strategies that can be implemented as link between two process steps when developing the future value stream. The supermarket is the third option when firstly One-Piece-Flow and secondly FIFO are no options at all.
The supermarket is a great methodology to help your organization to manage a variety of inventory where you don’t need to know in what order the components will be consumed. Through the so called Kanban-Pull-System “internal customers” will take components of the supermarket, which are replenished by the internal logistics following the Kanban-Pull-Principle or in a pre-defined interval. With this integrated pull system of the supermarket as link between logistics and production you can also speak of a general replenishment pull system. But let’s have a look at the supermarket, what it can be used for and how it could look like in your organization.
The supermarket itself is a mix of FIFO lanes for different components stored in Mobile Racks or a typical shelf where components are stored in bins or on pallets. Let’s assume on workstation A 3 different components are assembled, in the supermarket 1 lane would be dedicated to only this component following the FIFO principle. With this explanation you can see why FIFO itself is preferred the supermarket. The supermarket is either steered with two bin principle or kanban cards. According the replenishment time, the replenishment is triggered with the extraction of components and the stock dropping below the minimum quantity.
You see, the key question is when to use a supermarket instead of installing plane FIFO lanes or even follow the One-PIece-Flow.
Here are some examples when this is the case:
Two main material flow streams come together before or are split after the supermarket
Your organization follows the made to stock principle, then the supermarket is at the end of production and stores finished goods
With the help of a supermarket different lead times of suppliers paired with a high variance can be leveled and production can be smoothly supplied
Upstream processes are lacking quality, downstream process steps can easily replace defective parts/components (interim solution until problem is solved)
Different change over times, when a downstream process needs a change over the upstream processes can fill the supermarket as a overflow stock that is drained after change over is done
All of this examples have in common that the final target is to eliminate the supermarket itself and improving the material flow in a way that simple FIFO lanes or a Two-Bin-Principle at workstations can be realized.
The size of a supermarket is always determined by the components and their space needed for storage and their replenishment lead times. So it is a good piece of advice to have a clear overview of your components, their recurring demand including their replenishment times and don’t forget about a little safety stock on top.
As already mentioned there are two principles that are already well-known for implementing and steering a supermarket. The first one we have a look at is the Kanban-Principle and the second the so called Two-Bin-Principle, in which the bins itself trigger the replenishment.
A supermarket running on Kanban Cards can be seen shematically in the picture below. Every component stored in the supermarket is represented by an individual card, on which all required information is listed in order to trigger the replenishment process. The Kanban-Card can be seen as order slip for suppliers. Usually Kanban-Cards are placed on the so called Kanban Board. This kind of a supermarket can be seen most of the time.
The Two-Bin-Principle is a kind of supermarket where the bins itself are utilized the same way the Kanban Cards are used. In this approach all components have e.g. two assigned bins, filled with the dedicated components for this exact bins. The full bins are placed at the workstation, components are used and the empty bins are placed on the empty conveyor, ready to be collected by the Mizusumashi. the Mizusumashi refills the bins with the defined components and brings the full set back to the workstation. This kind of “decentralized” supermarkets are typically used for small and C-parts, which are consumed by not only one but several workstations, e.g. screws, washers, etc. as the financial impact of c-parts are low and the space needed is small.
In the end the supermarket is the last possible way to implement a Pull System after failing on implementing a One-Piece-Flow or FIFO. The target is and always will be to reduce the size of the supermarket by changing it into a FIFO system or change the material flow in to One-Piece-Flow. Therefore the supermarket can be seen as needed but temporary. The size of a supermarket is always defined by the size of the components itself, the replenishment time incl. some safety surcharge and the consumption lead time of the production. By simply removing or adding Kanban Cards or Kanban Bins the level of WIP can be adjusted.
Smoothed Production
Smoothed production is integral for customer satisfaction as it is a part of the ordering and complete fulfillment process. It makes sure that the supply chain capabilities are enough for stable production.
The topic of discussion today will be the so-called smoothed production. It is integral for customer satisfaction as it is a part of the ordering and complete fulfillment process. It makes sure that the supply chain capabilities are enough for stable production.
Smooth production benefits you by having a proper influence on your workplace configuration. It does this by helping to create a stable output with optimized inventory via a pre-condition. This presupposition/pre-condition simplifies your workplace based on the following conditions:
Standardized work processes
One-Piece Flow within the workstation
Complete processing
Stabile customer TAKT TIME
Minimal TAKT TIME loss
Maximum Output
Flexible deployment of workers
Quicker material change
Two-Bin-Principle
The smooth production is structured in the following:
Planning Strategy
Constant lot sizes
Stabile material needs
Fixed production times
Flexible inventories
Fixed timelines
Higher delivery dependability
It is implemented by:
Material flow
Scheduling methods
No part shortages
Pull-principle
Supermarket
Route traffic
Small containers
Warehouse Organization
Full transparency
Minimal warehouse levels
Set assembly
Bar codes and Data Matrix Codes
You may be asking the question, “but why do we need smooth production?”
It is a well-known fact that smooth production has many veritable advantages. With that said, there are also some potential drawbacks, but those can be eliminated or at the very least mitigated in the implementation phase.
Here are some of the benefits and drawbacks of smooth production:
The next question you might be asking is, “how does one implement smooth production?”.
Following are some of the requirements for smooth production:
Variable worker allocations should be the basis for the production power of the system. The variable shift models are first optimized for maximum output and then implemented specifically.
Two factors determine the minimum inventory of safety stock for a part number. The first is the variability in customer ordering habits. The second factor is the degree to which the program is successful in the production line. To hit the right spot between these two factors will require systematic optimization with the help of a mathematical model.
To determine what the maximum inventory of each part number should be, we should look at the delivery cycle of that said part number. This is essential for weekly pick-ups or delivery.
The production equipment inventory should be in accordance with necessary tool changes and set-up times.
The weekly production plan should be consistently released to the concerned parties once the production macro planning has been finished.
An information board at the assembly areas will contain all the planned orders.
The material requirement determination should solely be on the basis of the production plan.
Assembly areas should be designated for the online measurement of production units. A data matrix system should be implemented for reducing errors in the documentation process.
The ability to control production is a must if there are any noticeable short-term reactions arising due to discrepancies between the expected outcome and the actual outcome of the production plan.
Any daily deviations must be dealt with proper countermeasures. The production plan must be flexible enough to allow time to deal with backlogs. Meeting shipping deadlines is the primary goal.
A time-saving approach must be implemented in moving full racks from assembly areas to warehousing.
The requirements of the long-term sales plan should be integrated into the production plan so that production capacities and worker allocation are determined.
It is imperative that order calling and Just-In-Time delivery schedule data be automatically transferred to the resource planing system so that production planning can be done.
The production planning for the system will determine the specific production calendars with your organizations shift models.
All underlying data in the system must contain related shipping dates or the dates can be transferred from the demand data as well.
To control the complete system, the updated inventory trend with planned shipping dates, for example, weekly and monthly, should be represented graphically.
All possible scenarios should be simulated, because it is important to determine optimum capacities, performance, etc. for universal or shared production areas.
So, what factors make smooth production successful?
The two factors are planned output realization and controlling of supply
Production plan fulfillment as a part of planned output realization (source: Information board at production area as part of shop floor mgt)
Performance grading of workers in the production area that is done on the basis of the number of Dollars created in exchange for optimal material usability and worker effort (whether overtime or temporary workers)
Material usability of purchased parts, WIP, and raw materials when assembly time bears the cost or parts become short (Source: Information board at production area as part of shop floor mgt)
Special trips for the respective assembly area as a truthful Dollar figure
Supply capabilities and service grade for finished goods are measured using the number of delivered parts and the number of delivery dates met as a result of customer requests when demand data is transferred. (Source: Information board at production area as part of shop floor mgt)
Alternative measures for the success of smooth production:
Usage of constant customer feedback to determine customer satisfaction as used by companies e.g. from the automotive industry
Iterative comparison of customer feedback with important shipping and delivery figures
Target values of no customer feedback are used to get parameters to measure with
With the help of Kaizen workshops in conjunction with the introduction and implementation are used to create optimal basic parameters of success:
The finished goods inventory levels are available transparently to be used as an early warning signal
A minimal failure rate is strived for in the overall process of making sure of data from the production and logistics division
Over-production of products is reduced by ensuring that upstream assemblies are only producing the right amount of product to be used by the downstream processes
With the implementation of workshops, the set-up time can be reduced drastically
Constant reduction of purchase parts does not diminish the availability of the material in the production line while also reducing downtime
Optimal balance is achieved for assembly lines and areas and the requirements are met for variable worker allocation
The specifications of operator qualification shall determine how the qualification and training of workers should be conducted
There has been evidence of improvement in production flexibility in comparison to the past
Demings 14 Points
The 14 principles of good mgmt. described by Deming in his book "Out of the Crisis" can be seen as crucial factors for successful corporate transformation.
In this article we introduce you to Deming's 14 management principles and how they have impacted the Lean Management System.
The person Deming
William Edward Deming was an American professor, engineer, and consultant who studied electrical engineering and mathematical physics before becoming a consultant. He participated in a variety of topics, including statistical process control, systems thinking, and the human psyche. His work as a quality management consultant for Japanese firms was possibly his most well-known accomplishment. As a result, the Deming Prize has been given out to this day.
Nowadays the PDCA-Cycle is well known globally (or Deming Circle). But fun fact – it initially was called the Shewart-Cycle based on his cooperation with Dr. Walter Shewart.
Deming’s 14 POINTS OF GOOD MANAGEMENT
Deming offers 14 principles that he has identified as success elements for effective organizational transformation in his book "Out of the Crisis." Here they come:
To be competitive, set an unchanging business aim of consistent product and service improvement.
Put the new philosophy into practice. We are in a new phase of economic development, and (western) management must adapt to new circumstances.
Stop relying on quality assurance. Quality is not checked at the completion of the process but is built in from the initial stage.
Stop giving out contracts based on the lowest price. Instead, analyze a product's or service's entire cost. For each product, use only one supplier with whom you can develop a long-term and trusting connection.
Consistently and constantly improve the framework for manufacturing things.
Introduce "Training on the Job."
Introduce a fresh leadership style. The focus of leadership should be on assisting people and equipment in doing their tasks effectively.
Take away the system's fear. A culture that freely acknowledges mistakes aids in the identification of root causes, long-term solutions, and hence continuous improvement.
Remove the barriers that exist between departments. Purchasing, development, production, and sales must all work together to identify and address problems in production and service at the earliest possible time.
Employees who want zero errors or increased levels of productivity should avoid slogans and goals. Recognize that many of these goals are impacted by the system rather than by the individuals and that this incompetence demotivates employees.
Employees are no longer held to fixed quotas or performance targets. To make it clear to employees why tasks are important and should be completed, replace them with effective leadership.
Remove any barriers preventing employees from becoming proud of their work.
Introduce a holistic sublimed program that challenges and motivates each person's personal growth.
To enhance transformation, take the services of everyone in the organization.
Getting Demings principles IN THE LEAN MANAGEMENT SYSTEM
According to Deming, the 14 points of excellent management have evolved over time. While in the first point, he discusses relatively small-scale measures that facilitate a company's success, in the second point, he discusses large-scale measures that aid a company's success, the final principles are more basic statements about good business management.
In a lean workplace, we can apply any or all of the principles. Starting with a business vision that explains why the company exists and how it intends to improve over time. Continue with a new perspective on quality. Rather than employing a large number of quality control personnel to inspect the product at the end of the manufacturing process and, if needed, rework the product, the goal should be to incorporate quality into the product, this means that the manufacturing process should be built in such a way that manufacturing errors are avoided from the start (Poka-Yoke) or recognized quickly, allowing for a fast reaction rather than allowing the product to flow to the end of the line. This, of course, necessitates highly qualified staff who can best learn these abilities of immediate quality control directly at the process, as well as a culture that allows for the detection of errors without having to face negative consequences.
The style of thinking in value streams is another aspect of the Deming principles that becomes obvious. It explains how departments must coordinate to predict future difficulties in product manufacturing and services at an early stage. This demands strong cooperation among purchasing, development, sales, and production departments. He also states in principle four that decisions (such as purchasing) should not be made solely on the basis of the lowest offer but should always examine the whole expenses of a decision. What use is a 5 cent purchase price reduction if I have to budget for a 6-month replacement cycle in my warehouse? I have over 5 cents in expenses for storage, transportation, and stalled capital.
Another significant point is the shift in leadership perceptions. Deming is given the following quote:
It is the process, not the people.
Giving employees targets or piecework rates, in his opinion, makes no sense because they have no control over the results, which are decided by the system. Many people would now believe that if there are no goals, nothing will function. The distinction, in my opinion, is in the type of goals. If a corporation has a goal to grow by 10%, you might consider how to improve the system to meet this goal. You don't just hinder all of your employees' goals by 10%; you think about how you might reform the system.
Deming probably assumes that an employee is always prepared to give his all and that management is only demotivating him because it sets expectations for him that are unachievable in the current system. He goes on to say that staff wants to learn more and are always looking for ways to improve. This is a viewpoint that I can understand. When I consider the many employees I've met, I'm struck by how willing the young employees are to give their all and go hungry. Employees who have been disrupted for a long time by "the system" now only do what is necessary and seek challenges outside of work because they are not challenged or motivated at work.
I can only advise everyone to review the 14 Deming management principles again and again and to ask themselves which of the concepts are continuously followed and which are not.
6R
6R - The right product at, the right time, at the right place, in the right quantity, in the right quality and for the right price.
Let’s have a look on the logistics in operation. Everybody crossing the way with logistics will hear about the famous 6Rs the “six right ones” they say.
The right components
in the right amount
at the right place
in the right quality
at the right costs
at the right time
To summarize logistics this is it. The 6 Rs show that the main task of logistics is to make material/goods/components available.
You might have heard about the 7th R > the right customer.
So we think 6R are perfectly known as they got taught for decades. But with the lean transformation all over the 7th R becomes key on hitting lean mindset in logistics. It is all about customer centric orientation of the complete supply chain. It doesn’t matter where, how and why in the end you have to start with your customer and build along the upstream your logistics set up.
And here is the most valuable point, your customers are not only outside your organization, they are among your complete organization. If everyone along the process chain sees the next step as a customer, they also have to meet the customer expectations. This gives you a great pull effect throughout the complete process chain and in addition every employee is responsible as supplier and customer, two roles in one person. With this continuous focus on the customers demand or needs, all signs from the market result in a kind of resonance throughout your complete organization and causes an effect.
Logistics made up his way from simple material supply over optimizing material flow to become a crucial part of operations. Nowadays logistics are the arteries of manufacturing industries.
The traditional way to see logistics is seen in the 6R’s as shown in the beginning. For most of the business cases the 6R’s are enough and suitable in practice. But for real operational excellence and an impact on your lean journey keep always your customers in mind.
Following the 6(7)R’s will affect 4 main areas of your production system
Smoothed production
Warehouse organization
Production synchronous material flow
Cell production
Stay Connected
Ad
We want information fast and in a nutshell. We from OI recommend Blinkist* - because it’s simply the best.
* = Affiliate Link