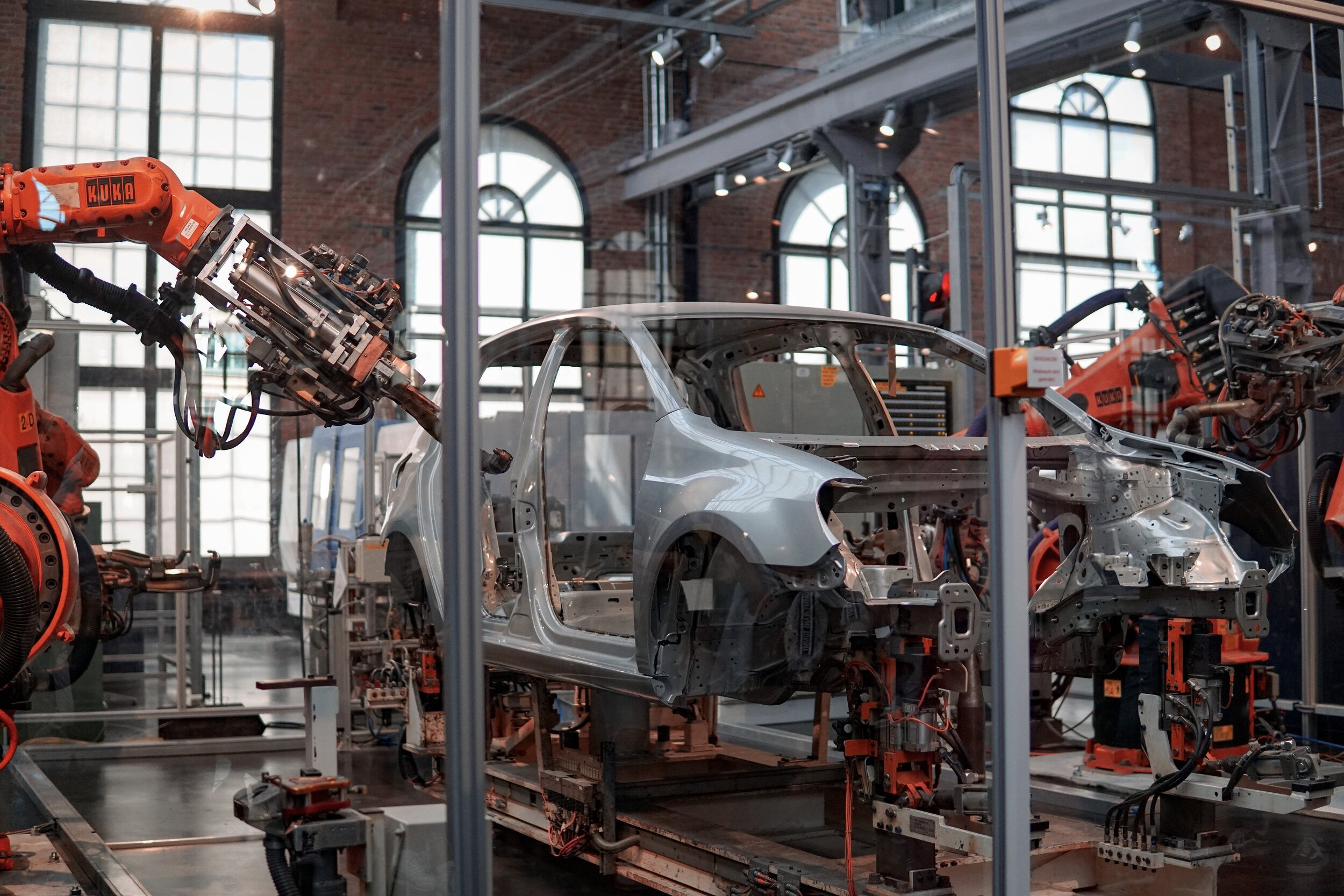
LANGUAGE OF LEAN
Genchi Genbutsu
Genchi Genbutsu encourages managers and employees to leave their desks and offices and go to the place where work is being done to see firsthand how things are working.
Genchi Gembutsu is a fundamental principle in the Lean Management system that emphasizes the importance of going to the source to observe and understand problems and opportunities. This concept was developed by Taiichi Ohno, one of the pioneers of the Toyota Production System (TPS), which is widely recognized as the precursor to Lean Management. Genchi Gembutsu is a Japanese term that translates to "go and see for yourself."
In the manufacturing industry, Genchi Gembutsu is best utilized to identify problems and opportunities in the production process. It involves visiting the production line to observe how work is being done, asking questions, and getting feedback from the workers. By going to the source, managers and leaders can see firsthand the challenges and issues that workers face on the job, and gain a deeper understanding of how the production process works.
The use of Genchi Gembutsu in the manufacturing industry is important because it allows managers to gain a comprehensive understanding of the production process, from start to finish. This includes understanding the inputs and outputs of each stage of the process, as well as the equipment and tools used. By doing so, managers can identify inefficiencies and areas where waste is being produced, and take action to eliminate these issues.
Genchi Gembutsu can also be used to identify opportunities for improvement in the production process. By observing how work is being done, managers can identify areas where work can be streamlined, and where productivity can be increased. This may involve rearranging the production line, investing in new equipment, or improving worker training and education.
One of the key benefits of Genchi Gembutsu is that it fosters a culture of continuous improvement within the organization. By encouraging managers to go to the source and observe how work is being done, organizations can identify and eliminate problems in real-time. This helps to create a more efficient and effective production process, which can lead to increased productivity and profitability.
In a nutshell, Genchi Gembutsu is a critical concept in the Lean Management system, particularly in the manufacturing industry. By going to the source to observe and understand the production process, managers can identify and eliminate inefficiencies and waste, and identify opportunities for improvement. By fostering a culture of continuous improvement, organizations can create a more efficient and effective production process, which can ultimately lead to increased productivity and profitability.
Break Through Objectives
Operational Excellence experts know the importance of establishing clear, measurable, and achievable goals in any organization.
Operational Excellence experts know the importance of establishing clear, measurable, and achievable goals in any organization. This is particularly true in the realm of Lean Management, where continuous improvement is key to success. In this context, Breakthrough Objectives play a vital role in driving progress and achieving sustainable change.
But what are Breakthrough Objectives and why are they so important? Simply put, Breakthrough Objectives are ambitious, long-term goals that aim to transform an organization and its processes. They go beyond the traditional incremental improvements that Lean Management focuses on, and aim for truly radical change. By establishing Breakthrough Objectives, organizations can focus their efforts on the most important improvements and create a clear vision for their future.
So, how can a Lean organization successfully implement and adopt Breakthrough Objectives? There are several key steps to follow:
Clarify the vision: Before setting Breakthrough Objectives, it is important to have a clear understanding of the organization’s vision and direction. This vision should align with the values and principles of Lean Management, and should be communicated clearly to all stakeholders.
Define the objectives: Once the vision is clear, it is time to define the Breakthrough Objectives. These should be specific, measurable, and achievable, and should align with the organization’s vision. It is also important to prioritize the objectives based on their importance and impact.
Engage all stakeholders: Implementing Breakthrough Objectives is a team effort, and it is crucial to engage all stakeholders in the process. This includes employees, customers, suppliers, and other key partners. By involving these stakeholders, organizations can ensure that their Breakthrough Objectives align with their needs and expectations.
Establish a clear strategy: To achieve the Breakthrough Objectives, a clear strategy must be established. This strategy should include the steps required to achieve the objectives, the resources needed, and the timeline for implementation. The strategy should also include measures for monitoring and evaluating progress.
Provide training and support: To ensure that the Breakthrough Objectives are successfully implemented, employees must be trained and supported. This may include training on Lean Management principles and practices, as well as training on new systems and processes. Employees must also be provided with the resources they need to succeed, including the right tools and equipment.
Monitor and evaluate progress: It is important to regularly monitor and evaluate progress against the Breakthrough Objectives. This helps organizations to identify areas for improvement and make adjustments as needed. By continuously monitoring and evaluating progress, organizations can ensure that they stay on track and make the necessary changes to achieve their goals.
Celebrate success: Finally, it is important to celebrate success when the Breakthrough Objectives are achieved. This helps to reinforce the importance of Lean Management principles and practices, and encourages employees to continue working towards further improvements.
In a nutshell, Breakthrough Objectives are an important tool for driving change in a Lean organization. By following these steps, organizations can successfully implement and adopt Breakthrough Objectives, and achieve truly transformative results. With a clear vision, a solid strategy, and a commitment to continuous improvement, organizations can achieve their goals and achieve Operational Excellence.
Blue Sky Workshop
A Blue Sky Workshop is a process that is often used in organizational change management and is designed to promote creative thinking and help organizations to think beyond the boundaries of their current systems and practices.
A Blue Sky Workshop is a process that is often used in organizational change management and is designed to promote creative thinking and help organizations to think beyond the boundaries of their current systems and practices. The origin of Blue Sky Workshops can be traced back to Japan, where they were first developed by a group of industrial engineers as a way to encourage free thinking and help organizations to achieve their full potential.
The purpose of a Blue Sky Workshop is to provide a structured process that allows an organization to step outside of its normal routines and think creatively about the future. This process involves bringing together a group of stakeholders, including senior executives, managers, and employees, to brainstorm and imagine new and innovative ways of working. The workshop is designed to provide a safe and supportive environment where people can let their imaginations run wild and come up with ideas that may not be possible within the constraints of the current organizational structure.
To conduct a Blue Sky Workshop, it is essential to create an atmosphere of openness and collaboration. The facilitator should encourage participants to think outside the box and challenge their existing assumptions about what is possible. It is also important to provide participants with the necessary tools and resources to help them come up with innovative ideas, such as whiteboards, sticky notes, and brainstorming software.
The first step in conducting a Blue Sky Workshop is to establish the objective of the workshop. This should be a specific, measurable, and achievable goal that the participants are trying to achieve. For example, the objective might be to develop a new product, improve customer satisfaction, or reduce costs.
Once the objective has been established, the facilitator should begin by encouraging participants to think about their ideal future. They should ask participants to imagine what their organization would look like if they could achieve their goal, and what challenges they might face along the way. This exercise helps participants to think creatively and generate new ideas that they may not have considered before.
After the initial brainstorming session, the facilitator should then encourage participants to refine their ideas and develop them further. This may involve breaking down the ideas into smaller sub-goals, or exploring the feasibility of different approaches.
Once the ideas have been refined, the facilitator should then help participants to prioritize their ideas based on their potential impact, feasibility, and potential risks. Participants should then be encouraged to develop action plans that outline the steps they will take to achieve their goals.
The final step in the Blue Sky Workshop process is to review and evaluate the progress made. This may involve regular check-ins, progress reports, or other methods of monitoring progress.
In conclusion, the Blue Sky Workshop is a powerful tool for organizations that want to think creatively about the future and develop new and innovative solutions to their problems. By encouraging participants to think beyond their current systems and practices, organizations can achieve their full potential and create a brighter future for themselves and their stakeholders.
SMART - OBJECTIVES
SMART - Objectives drive us forward and continually remind us of what we want to achieve. They help us to set priorities more clearly, to focus better and give us the strength to continue, even if our motivation is low.
Goals are helpful both in our daily work and in our personal lives, as they give us something to work for.
SMART - Objectives drive us forward and continually remind us of what we want to achieve. They help us to set priorities more clearly, to focus better and give us the strength to continue.
HOW TO DEFINE GOALS
Objectives can be manifold, but one of the best known methods to describe goals is the S.M.A.R.T. methodology. The 5 steps can be used to clearly describe a goal and make it "tangible".
The acronym SMART stands for the following 5 steps:
S - specific | Clearly defined goals
M - measurable | The target should be measurable (has a KPI)
A - accepted | The accessibility of the goal should be accepted by all stakeholders (alternative: ambitious/attractive)
R - realistic | The attainability of the goal within the set framework should be realistic,
T - terminated | The time of target achievement is clearly defined.
FURTHER DEVELOPMENT, SMART BECOMES SMARTER
Some of the terms have changed over time. So the A at the beginning stood for agreed upon. This is from the thinking that the term is used within a company. In this respect, it was important that a goal was accepted by all involved. Over time "agreed upon" often became "achievable" or "attainable".
Not only the terms themselves have changed. The acronym itself has often changed recently. Many authors have switched to making SMART - SMARTER.
The E stands for "evaluated".
The R stands for "reviewed."
More than 200 pages about OKR may seem like a stretch – and there is a bit of extraneous material – but those who must lead an OKR initiative, especially novices, will value this substantive guidance.
Read the pick here.
In my opinion, the popularity of SMART goals stems from the simplicity of the method and the higher probability of success. Why should it be higher? Now the SMART method requires from the person or department that set the goals a certain time and focus on those goals. When one is so intensively involved with defining goals, one inevitably thinks of ways in which the goal could be achieved. Furthermore, one has already taken the first step and is now more motivated to take the next necessary steps.
Of course these steps must not be missing. Action plans must be derived from the goals, whose degree of goal achievement should be regularly reviewed. Regular monitoring of progress enables me to adjust my next actions to the achievement of my goals.
Stay Connected
Ad
We want information fast and in a nutshell. We from OI recommend Blinkist* - because it’s simply the best.
* = Affiliate Link