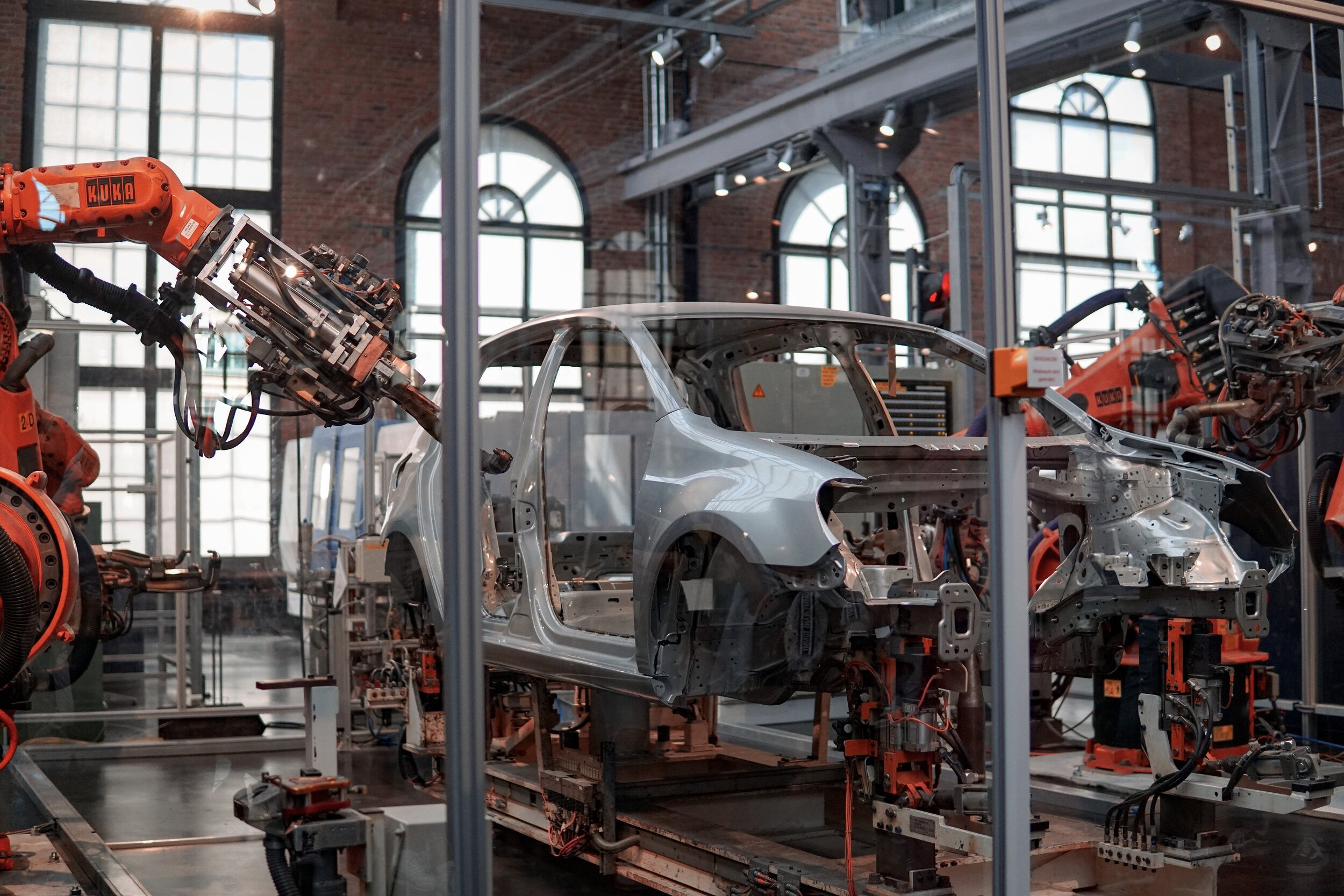
LANGUAGE OF LEAN
Ergonomic Workplace
A work place that takes into consideration most of the ergonomic aspects such as the operator’s height, range and reach.
An ergonomic workplace is a work system that considers the ergonomic aspects of an operation and the operator such as the operator’s hight, range and reach with the goal that the operator does not need to bend or turn.
The ergonomic workplace goes hand in hand with the work improvement.
Definition and purpose
Reveal waste increasing cost and not adding value.
Find waste in the movement of workers, eliminate/improve, pursue net work adding value.
Worker Movement
Lean Manufacturing and Ergonomics may have different roots and directions but together they can complement each other and define a more efficient and safer workplace.
One of the best person known for focusing on productivity and efficiency in manufacturing processes was Henry Ford with the invention of the modern assembly line. Ford really was focusing on eliminating waste and to cut down unnecessary costs in relation to the manufacturing of his cars.
Toyota is one of the best known companies that has stretched to the maximum the idea of Lean Manufacturing and is now holding the pole position when it comes to the reputation according the elimination of “waste”.
By looking at the Lean Model as well as Work Ergonomics, you clearly see the necessity of both practices in the industrial workplace, as well as observe that both can complement each other.
The 7 types of waste to eliminate include:
Transport
Inventory
Motion/Movement
Waiting
Overproduction
Overprocessing
Defects
The list of TIMWOOD is what Toyota has defined as the seven major types of wastes or non-value-adding activities. The seven wastes do not add any value to the product and the customer in the end is not willing to pay for it. Therefore it is essential to remove as much waste as possible which will have also an effect on the ergonomic workplace and furthermore on the health of the operators.
Some of these things like transport, waiting or unnecessary movement can be reduced to a limit what the operator still needs because as human being the operator is limited by his body.
The Lean Manufacturing initiatives and workplace ergonomics stepped into the manufacturing world at different times and therefore are not fully integrated. But you are perfectly advised by combining the principles of Workplace Ergonomics with Lean Manufacturing initiatives. Through a cooperative assessment and teamwork you have the chance to complement each other in making the workplace more efficient and a safer place.
OTED
One touch exchange of a die.
Depending on your field of industry the defined times to perform a changeovers varies between 1.5 and 1 minute.
To run OTED successfully following actions are required upfront:
Reduction of adjustments needed down to zero
No fastening with screws needed
100% positive locking between die and tool carrier
Proper fitting methods
Separation between tooling and function
The target is simply explained: The exchange of a die is done with one single motion.
When having a look at the development of improving changeovers the first step is to implement the single-minute exchange of a die (SMED). SMED helps you in the beginning to figure out how to perform the changeover with less motion. OTED is then the high level of changeovers. As mentioned as SMED can be also understood as single digit exchange of a die, yes this means everything under 10 minutes is SMED, OTED stands for the ultimate target. Through continuous improvement actions on SMED you are striving to reach the state of being able to exchange tooling in the takt of your line with one single motion.
In the end with OTED you have to deal like with all the other Lean Tools, don’t just apply it to be cool and “lean”. If it doesn’t make sense for your operation or process don’t do it. But when you decide to strive for OTED and you and your team are convinced by the promised improvements , make sure to understand the process flow first then take action.
Stay Connected
Ad
We want information fast and in a nutshell. We from OI recommend Blinkist* - because it’s simply the best.
* = Affiliate Link