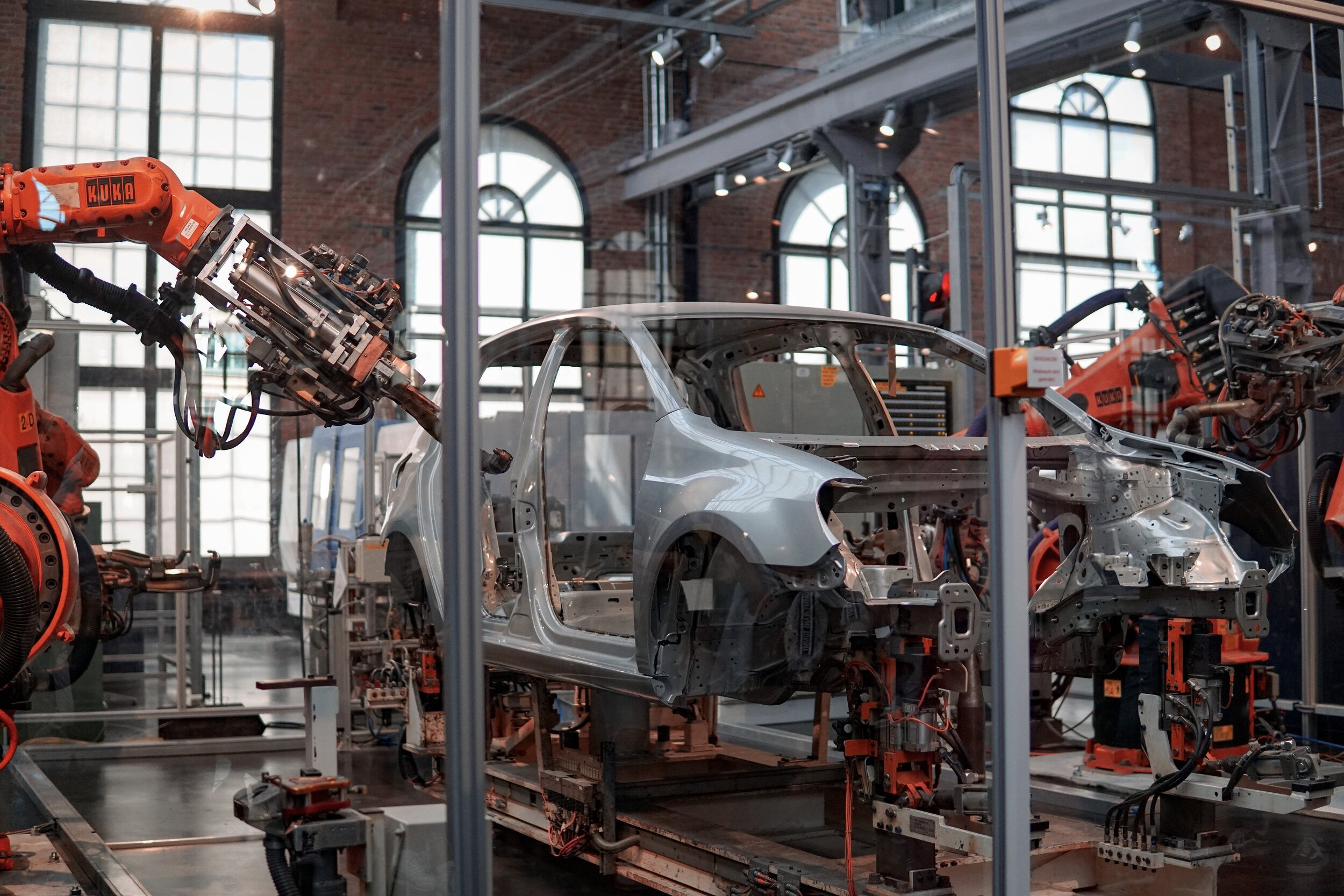
LANGUAGE OF LEAN
Pareto Principle
The 80/20 rule demonstrates that things have an unequal distribution. Out of 5 one will fly and have the most impact. With 20 percent of action 80 percent of your target state is already reached.
The Pareto Principle describes that 80% of problems can be closed with 20% of the causes. This principle is named after Vilfredo Pareto who found out that 80% of Italy’s wealth belonged to 20% of the population.
With this in mind it is worth to have a look at it.
Let us start with an assumption, according to the Pareto Principle it allows us to assume that
20% of input creates 80% of the output
20% of customers create 80% of your revenue
20% of causes create 80% of failures
20% of your employees create 80% of sales
and so on…
But before you run away now and think you have the answer hold a second. With the 80/20 rule you might tend to say that it always have to be 100 - it’s not. Make a deep analysis before making such statements! 20% of your employees can also make only 20% of sales or 60%. So before you fire 80% of your employees keep in mind that the Pareto Principle only gives you an idea on the distribution.
The whole idea behind it is that most things in life are not distributed evenly!
When we talk about value adding activities and the final product is 100% What is with all the necessary tasks, that are not adding any value to the final product but have to be done to run the company.
Or think about failures and finding the root cause, where to start to take actions? This is great when you think about a Failure Pareto and you want to satisfy your customer as quick as possible. Of course you are focusing first on the most failures and most of the time - not always - the other failures will disappear as well.
But most important of all, your customer gains trust in you that you have the competencies to do the job.
The key point is that most things are not in a 1/1 actio = reactio relationship.
So what can we use it for this 80/20 rule?
The Pareto Principle in first place supports you on realizing that most of the outcome are based on a minority of inputs. This means:
20% of input creates 80% of the output > try to reduce those non value adding activities
20% of customers create 80% of your revenue > install a key account manager that the customers knows he/she is important to your company > your customers success is your companies success
20% of causes create 80% of failures > Focus on fixing those failures first
20% of your employees create 80% of sales > get those employees a reward
We could continue on and on. To bring it to the point > focus on the 20% and not on everything at the same time.
Some examples that might help you for a better understanding:
Instead of spending a whole night to prepare a presentation and thinking about where to start > focus on one topic and do it. You will get a feedback anyway during the pitch. This feedback gives you the chance to take it and improve it.
Instead of focusing on one solution that might be the best and go through all the details. Make a list of three and go through the pros and cons with your colleagues that probably know the topic better anyway and based on their opinion make a decision with what to go on.
Maybe this examples are nuts for you but we want to emphasize that you should focus only on the important 20% and forget - for the moment - the other 80.
Last but not least - the Pareto Principle is not a law of nature it is a guideline to steer your focus and to save time on problem solving or simply getting your job done faster.
5 Why
The 5 Why methodology is a well known part of the root cause analysis. Key is to ask five times in the row – why?
The 5 Why methodology is a well known part of the root cause analysis. Key is to ask five times in the row – why? It is not the only way to determine the root cause(s) of problems. Just to mention that it usually comes together with an ISHIKAWA analysis. If you want to get deeper into problem solving including ISHIKAWA and 5Why we recommend you the article taking on the 7Steps approach.
The practice of asking why five times in a row whenever a problem occurs supports you on identifying root cause(s) and to determine effective counter measures that are developed through the process of 5Why. Then it is a simple part of PDCA to develop and implement effective measures.
To be able to steer a wide product portfolio, survive the competitive pressure and at the same time satisfying your customers with a high quality product at a reasonable price can be a tough game. Most of the time you don’t have enough time to run the complete product development cycle, do your validation and verification… The end of the story is that you start production because you need to deliver – which automatically leads to mistakes in running daily business. Therefore, the simple method of 5Why can be used to support, not only, your quality department to get faster to the bottom of problems.
The solution for a problem is not always easy, sometimes the root cause is hidden. Therefore the method is an important element of the root cause analysis. One tries to get to the root of the problem step by step with why questions, because one assumes that several causal connections interlock. The system is easy to explain, but there is a lot behind it. If you really take the time to ask the questions carefully and discuss them, the results are extremely profitable.
You should go through these steps of the 5-Why method. Describe your problem as detailed as possible. As more facts you have, you are faster on getting to the bottom of the problem.
What is the difficulty?
When did it first occur?
How often does it occur?
Is this failure randomly coming or reoccurring in a pattern?
Can you repeat the failure?
What is the effect of this failure?
and so on….
It is very important to get a fast idea of the situation on site. Take the Gemba Walk as great opportunity to talk to the people who are actually involved and to see it with your own eyes instead of guessing from your office.
Avoid making assumptions at this stage - you may draw the wrong conclusions.
Keep calm and try to understand the complete context first.
Understanding the context is where the 5-Why method comes in. Gradually ask why questions in order to get a feeling for the interrelationship of effects. This works for many areas of the company, in production, but also in your private life.
Example:
Problem: I miss all the fun part with my kids…
Why do I miss so much? - Because I’m not often at home.
Why am I not often at home? - Because of my position at work I have long working hours and business trips.
Why do I have long working hours and business trips? Because I can’t get my work done in 8 hours and bad in delegating work.
Why can I get my shit done in 8 hours and miss to delegate things? Because I’m sloppy in prioritizing and time management and don’t trust others.
Why can’t I prioritize my activities and don’t trust others? Because I don’t have the information needed to do so.
Reverse conclusion: If I’m not getting the necessary information in a certain amount of time in an acceptable quality I’m not able to steer my employees but also miss the time with my kids.
Sometimes 2 questions are necessary, sometimes 8 or even more to bring you to the “right” conclusion. But don’t give up half way.
Develop appropriate counter measures:
What contributes to solve the problem and who can implement which measures? How long will this take and what consequences will the implementation have?
First: I should try to have set timeframes with my kids which are holy and untouchable.
Second: I should define what information for me is necessary to run my company.
Third: According to the defined Information I train my employees what I need.
Fourth: I implement a clear systematic approach that I have all information latest at 11:00.
(DING DONG - Sounds familiar? BINGO — Shop Floor Management with a functioning meeting cascade.)
Keep the wheel spinning!
No matter what – before start implementing ad-hoc whatever you find best – take your time to identify what actions contribute to a real long term effect, what effects it will have on other areas, etc. Nothing worse than if you think you are doing something great but in reality you make it even worse.
The cycle of questions is often interrupted too early. The real cause is then not really eliminated and after some time there are repeated difficulties.
You can test it: If the reverse of your assumptions works, you are probably at the end of the causal chain.
As mentioned in the beginning another way is the ISHIKAWA diagram
Just keep in mind that not like with the ISHIKAWA the 5 Why only leads you to one cause for a problem. But as always in life there can be more than just one that leads to an effect. Therefore, the combination of 5Why and ISHIKAWA gives you the best approach to determine causes. It will allow you to represent several major and minor causes that can contribute to the solution.
Get the big picture with an ISHIKAWA drill it down with the 5Why.
Stay Connected
Ad
We want information fast and in a nutshell. We from OI recommend Blinkist* - because it’s simply the best.
* = Affiliate Link